- 15-20 Min Read
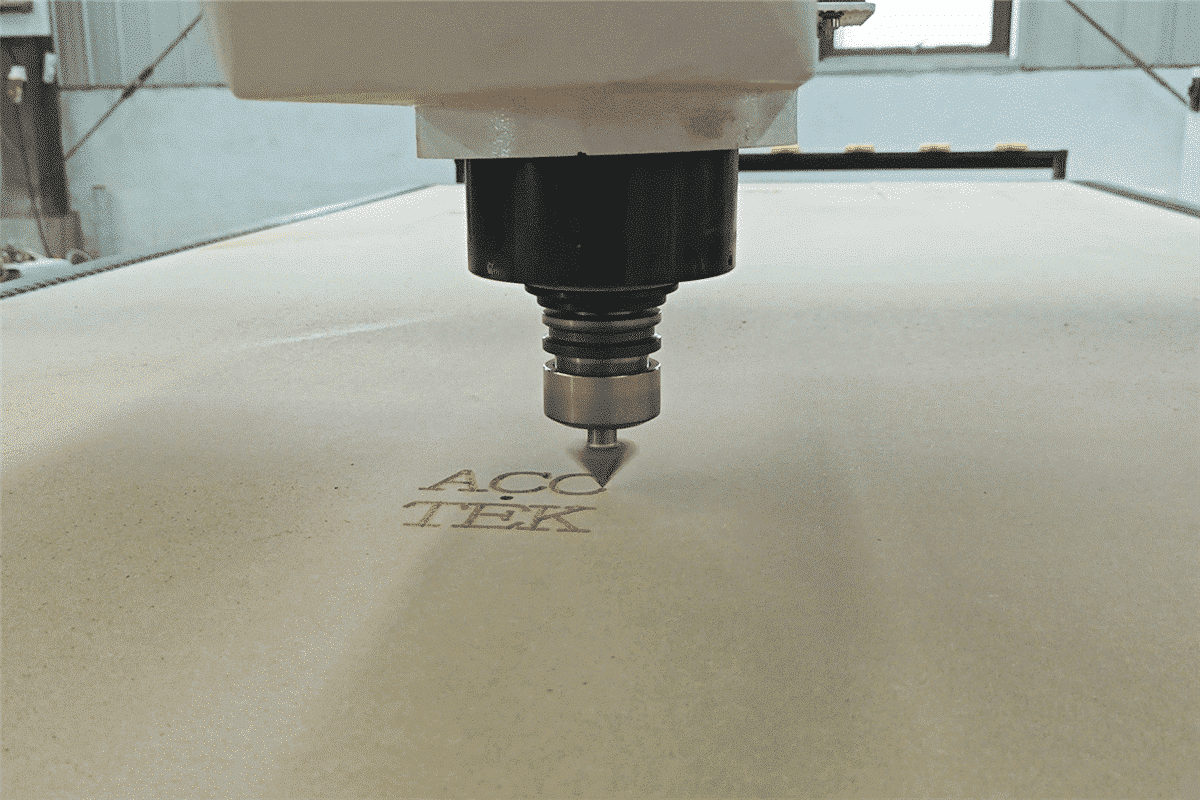
Router bits are the workhorses of CNC routing, responsible for shaping, cutting, and finishing a variety of materials with precision. However, router bit corruption, be it dulling, chipping, or breakage, can lead to inefficiencies, compromised precision, and costly downtimes. Understanding how to prevent router bit corruption not only extends the life of the tool but also ensures optimal performance, high-quality results, and cost savings over time.
In this article, we explore effective strategies and best practices to maintain your router bits in peak condition. Additionally, we provide insights into troubleshooting common router bit issues to help you identify signs of wear or damage early and take corrective action promptly, ensuring smooth and efficient CNC router operations. By preventing router bit damage, you can enhance the performance of your CNC routing system and extend the lifespan of this critical tooling component.
Understanding CNC Router Bit
Choosing the right router bit for your specific application is not simply a matter of preference, it requires an informed approach to the type, material, and construction of the bit. Understanding these factors is the first step in ensuring the lifespan and effectiveness of your tools, maximizing productivity, and enhancing the quality of your work.
Types of CNC Router Bit
CNC router bits come in a wide variety of types, each designed to perform specific tasks and achieve different cutting results. Here’s a look at some of the most common types:
- End Mill Bits: Often used in CNC milling applications, end mill bits are designed to remove material efficiently. They are available in various sizes and configurations, including two-flute, four-flute, and more. Fewer flutes offer better chip clearance and are often used for soft materials, while more flutes provide a smoother finish and are suited for harder materials. End mill bits are commonly used in metalworking, woodworking, and plastic machining to make smooth side cuts and flat-bottom cuts.
- Ball Nose Bits: These bits have a rounded tip, making them ideal for 3D contouring, carving, and creating smooth finishes on curved surfaces. These bits are widely used for mold-making, sign-making, and detailed projects. The smooth, rounded tip of ball nose bits also helps reduce chipping and improves the finish quality on curved surfaces.
- V-Groove Bits: V-groove bits are designed to cut V-shaped grooves in materials and are a popular choice for decorative applications such as engraving, sign-making, and creating decorative lines and designs. They come in various angles, such as 60°, or 90°, allowing for fine control over the groove depth and appearance. V-groove bits excel in creating clean, precise lines for lettering and intricate designs. They are also often used in chamfering to create decorative edges.
- Spiral Bits (Up-Cut and Down-Cut): Spiral bits are distinguished by their helical design, there are two main types: up-cut and down-cut. Up-cut bits pull chips upward, making them ideal for evacuating material quickly, but they may leave rough edges on the top surface. Down-cut bits push chips downward, resulting in cleaner top surfaces but may not clear chips as efficiently. Choosing between these depends on the desired finish and the material being cut.
Material of CNC Router Bit
The material of a CNC router bit plays a significant role in its performance, durability, and suitability for various applications. Here are the common materials used in manufacturing CNC router bits:
- High-Speed Steel (HSS): High-speed steel is one of the most affordable materials used for CNC router bits. It offers reasonable toughness and heat resistance, making it suitable for cutting softer materials like wood, soft plastics, and aluminum. However, HSS bits wear out more quickly compared to other options, especially when used for high-speed or abrasive cutting. They are ideal for less demanding tasks and are often used in applications where cost is a primary consideration.
- Carbide-Tipped Router Bits: Carbide-tipped bits have a steel body with cutting edges made of carbide. Carbide is much harder and more heat-resistant than HSS, allowing for a longer tool life and better performance on harder materials like hardwood, MDF, and some metals. Carbide-tipped bits maintain their sharpness longer and can operate at higher speeds without significant wear. These bits are widely used in woodworking and are known for providing smooth cuts and excellent durability.
- Diamond-Tipped Router Bits (PCD): Polycrystalline diamond (PCD) router bits are among the most durable and long-lasting options available. They are specifically designed for cutting highly abrasive materials, such as composites, laminates, glass-reinforced plastics (GRP), and other demanding substrates. Diamond-tipped bits offer exceptional wear resistance, precision, and durability, but they are also the most expensive option. Their long lifespan makes them ideal for high-volume or specialized industrial applications where minimal tool wear and maximum cutting efficiency are required.
Anatomy of CNC Router Bit
Understanding the anatomy of a CNC router bit is key to making informed choices about bit selection and optimizing cutting performance. Here is a breakdown of the key components of a CNC router bit:
- Shank: The shank is the part of the router bit that is inserted into the CNC router’s collet. It provides a stable and secure connection between the bit and the router or spindle. The diameter of the shank typically matches the collet size and comes in standard sizes like 1/4 inch, 1/2 inch, 6mm, and 12mm. The choice of shank size affects stability and vibration, larger shank diameters generally provide greater stability during cutting operations, reducing vibration and improving cut quality.
- Flutes: Flutes are grooves or channels that run along the cutting edge and body of the router bit. They play a critical role in chip removal, directing the debris away from the cutting area. Flutes also affect the surface finish of the cut and heat dissipation. Up-cut flutes pull chips upward, providing efficient material removal but potentially causing tear-out on the top surface. Down-cut flutes push chips downward, resulting in cleaner top surfaces.
- Cutting Edge: The cutting edge is the most critical component of the router bit, as it directly interacts with the material being cut. Cutting edges are responsible for removing material and determining the shape and finish of the cut. They can have different geometries, such as flat, angled, rounded, or spiral, depending on the type of cut required. The number of cutting edges or flutes can vary, more flutes generally mean a smoother finish but less efficient chip evacuation.
- Helix Angle: The helix angle refers to the angle at which the flutes spiral around the body of the bit. A steeper helix angle generally provides a smoother cut and better surface finish but may reduce chip clearance. A lower helix angle improves chip removal but may lead to rougher finishes.
CNC router bits come in a wide range of shapes, materials, and configurations, each tailored to specific tasks and cutting requirements. By gaining a solid understanding of their design, function, and application, you can optimize your CNC routing process, reduce tool wear, and achieve superior cut quality.
Factors that Cause CNC Router Bit Damage
CNC router bit damage can occur due to a variety of factors, many of which stem from improper use, machine settings, or material characteristics. Understanding these factors is beneficial for preventing damage, extending the lifespan of your bits, and ensuring high-quality cuts. Here are some of the common causes of CNC router bit damage:
Improper Feed Rates and Speeds
- Understanding Speeds and Feeds: In CNC machining, speeds refer to the rotational speed of the router bit (measured in RPM), while feeds denote the rate at which material moves into the cutting tool (measured in IPM or mm/min). Properly balancing speeds and feeds ensures efficient material removal, minimal heat buildup, and a high-quality cut. If the feed rate is too fast, it can put excessive stress on the bit, causing chipping or breakage. Conversely, a feed rate that is too slow can lead to heat buildup, dulling, and even burning of the bit.
- Calculating the Proper RPM (Revolutions Per Minute): The correct RPM depends on the bit diameter and material being cut. Smaller bits require higher RPMs, while larger bits need lower speeds to avoid stress on the cutting edge. Calculating RPM involves considering the surface speed of the material, using formulas or manufacturer recommendations as guidelines.
- Determining Feed Rates: The feed rate dictates how fast the material is fed into the bit and is influenced by the RPM, bit type, number of flutes, and desired finish. Calculating feed rates involves multiplying the RPM by the number of flutes and the chip load (amount of material removed per cutting edge per revolution).
Improper Tool Selection
- Matching Tool with Material: Selecting the correct tool for the material you are cutting is a prerequisite for efficient and precise machining. Different materials require specific types of cutting tools. For example, softer materials like wood may work well with high-speed steel (HSS) bits, but harder or abrasive materials like metals or composites often need carbide or diamond-tipped tools. Using an improper tool for a specific material can lead to rapid wear, dulling, breakage, or poor-quality cuts.
- Considering Tool Geometry: Tool geometry, including the shape of the cutting edge, angle, and tip configuration, affects the cutting performance and quality of the final product. For instance, using a straight bit for contouring complex 3D shapes may lead to poor results, while a ball nose bit would provide smoother finishes. Ensuring that the tool geometry matches the intended cutting application and design requirements is beneficial for achieving precise and efficient results.
- Chip Groove Configuration: Chip groove or flute configuration impacts how effectively chips are removed from the cutting area. An improper configuration can lead to poor chip evacuation, resulting in heat buildup, clogging, and tool wear. Selecting a tool with the right chip groove configuration for the material and application prevents clogging, reduces heat, and enhances tool life and machining performance.
Insufficient Tool Lubrication
- The Importance of Lubrication: Proper lubrication ensures smoother cuts, reduces tool wear, and maintains consistent machining performance by dissipating heat and minimizing friction. Without sufficient lubrication, excessive friction and heat are generated, leading to rapid dulling, wear, and even damage to the cutting edge. High heat buildup can cause thermal expansion of the bit and material, resulting in imprecise cuts, reduced tool lifespan, and potential breakage.
- Selection of Appropriate Lubricants: The effectiveness of lubrication depends on choosing the appropriate lubricant for the specific material being machined. Different materials—such as wood, plastics, or metals—require different types of lubricants. The right lubricant must also be compatible with the tool and workpiece, providing optimal cooling, minimal residue, and ease of cleaning. Using an unsuitable lubricant can lead to poor cooling, excessive residue buildup, and ineffective lubrication, causing damage to the router bit.
- Correct Lubrication Technology: The right lubrication technology is in place to help maintain consistent tool temperatures, reduce friction, and prevent router bit damage. Lubrication technology involves using methods such as flood cooling, mist cooling, or air blasts to ensure even distribution of the lubricant to the cutting area. Incorrect application methods can lead to uneven cooling or inadequate coverage, resulting in localized heat buildup, increased wear, and reduced effectiveness of the router bit.
Improper Machine Settings
- Inspection and Calibration of CNC Router: Improper machine settings often stem from a lack of thorough inspection and calibration of the CNC router. When the CNC router is not properly calibrated, axes may be misaligned, causing uneven or inaccurate cuts that put excessive stress on the router bit. Unchecked mechanical wear or misadjusted components can lead to vibration, tool deflection, and inconsistent cutting forces, all of which accelerate tool wear and increase the risk of bit breakage.
- Ensuring Correct Installation of Tool Holder: If the tool holder is not properly seated or tightened, the router bit may experience vibration, deflection, or even become dislodged during machining. This instability can lead to uneven cuts, excessive stress on the cutting edge, and, ultimately, bit damage. Proper installation involves cleaning the tool holder and collet to ensure a secure fit, verifying that the bit is correctly seated, and tightening it to the appropriate torque.
- Workpiece Clamping Technology: Inadequate or improper clamping of the workpiece is another factor that can lead to router bit damage. If the workpiece shifts or vibrates during machining due to insufficient clamping, the router bit can experience uneven forces, leading to chipping, breakage, or rapid dulling. Proper workpiece clamping techniques involve using secure clamps, vacuum tables, or mechanical fixtures to hold the material firmly in place.
By addressing these factors and employing proper techniques, you can significantly extend the life of your CNC router bits, maintain consistent cutting performance, and minimize costly downtime due to bit replacement.
Precautions and Best Practices
To ensure optimal performance, safety, and longevity of router bits and equipment in CNC machining, it is important to follow certain precautions and best practices. Here are some key guidelines:
Regular Maintenance
- Cleaning and Inspecting the Router Bit: During use, debris, resin, and other material residues can accumulate on the cutting edge, reducing its sharpness and cutting efficiency. It is important to clean router bits thoroughly with an appropriate cleaning solution to remove buildup without damaging the bit. Additionally, inspect the bit for signs of wear, chipping, or cracks. Early detection of issues allows you to address potential problems before they lead to tool breakage or compromised cuts.
- Sharpening and Re-sharpening Techniques: Router bits gradually dull with use, leading to reduced cutting precision, increased heat generation, and potential damage to the workpiece. Sharpening and re-sharpening are critical maintenance practices to restore the cutting edge’s sharpness and prolong the bit’s life. Proper sharpening angles and techniques must be followed to ensure the cutting edge maintains its original geometry and effectiveness.
- Storage Guidelines: Router bits should be stored in a dedicated, organized manner, such as in a storage case, rack, or foam-lined drawer, where each bit is kept separate and secure. Ensure that the storage area is dry and protected from moisture to prevent rusting, especially for bits made of high-speed steel. Taking the time to store bits correctly minimizes the risk of accidental damage and maintains their readiness for use.
Temperature Control
- Understanding the Generation of Heat: In CNC machining, heat generation is a natural byproduct of the cutting process due to friction between the router bit and the material being machined. High-speed rotations and contact pressure cause significant energy transfer, leading to elevated temperatures at the cutting edge. Excessive heat can negatively impact machining by dulling the router bit, causing thermal expansion, and leading to poor-quality cuts or material deformation.
- Implementing a Cooling System: Cooling systems help dissipate heat and minimize thermal stress on the router bit and the workpiece. Flood cooling uses a continuous flow of coolant to keep temperatures low and lubricate the cutting area, making it ideal for metal and high-speed machining. Mist cooling applies a fine spray of coolant, offering a balance between lubrication and heat dissipation without excessive fluid use. Air cooling systems blow compressed air to clear chips and reduce heat buildup without adding liquid to the cutting environment.
Operator Training
- CNC Router Operation Education: Proper operator training is a crucial step in preventing CNC router bit damage. A comprehensive education in CNC router operation helps operators understand the intricacies of machine setup, tool selection, and programming. Training should cover key areas such as the selection of appropriate router bits for specific materials and setting optimal feed rates and speeds. Educated operators can identify signs of bit wear and adjust machine settings accordingly to prevent excessive stress or damage to the bit.
- Promoting Safety Practices: Promoting and adhering to safety practices not only protects operators but also prevents damage to router bits and other equipment. Safety training should emphasize proper tool installation, secure workpiece clamping, and regular machine inspections to minimize vibration and ensure stable cutting conditions. By fostering a culture of safety awareness, operators are more likely to handle tools and machines correctly, reducing the risk of bit damage caused by improper setup, mishandling, or unexpected machine movements.
Tool Path Optimization
- Efficient Tool Path Planning: Efficient paths reduce unnecessary tool travel, lowering the chances of overheating and wear. Tool paths should also be programmed to follow logical cutting sequences that maintain a consistent chip load and avoid cutting into previously machined areas. By optimizing the tool path, you ensure that the router bit operates with minimal friction and vibration, reducing the risk of damage and enhancing the precision and quality of cuts.
- Minimizing the Pressure on the Router Bit: Tool path optimization can also help minimize the pressure exerted on the router bit, thereby reducing the likelihood of damage. Reducing sharp turns, minimizing deep passes, and maintaining a steady, consistent feed rate all contribute to distributing the cutting forces evenly across the bit. This approach prevents localized stress that can lead to chipping, breakage, or dulling of the cutting edge.
By implementing these precautions and best practices, you can significantly reduce the risk of router bit corruption, enhance cutting performance, and extend the life of your tools, leading to consistent and high-quality machining results.
Troubleshooting of Router Bit Damage
Troubleshooting router bit damage is beneficial for maintaining high-quality cuts and prolonging tool life. Here is a structured approach to identifying and resolving issues that may cause damage to router bits:
Identifying Signs of Wear
- Visual Inspection: Conducting a thorough visual inspection of your router bit can reveal a lot about its condition. Carefully examine the cutting edges for any signs of dullness, chipping, or breakage. Any signs of rounding or wear indicate that the bit may need maintenance or replacement. Also, check for residue build-up which can hinder cutting efficiency and increase friction. Inspect the shank for any wear or signs of damage that may impact the bit’s stability during operation.
- Monitoring Cutting Sounds: The sounds produced during CNC machining can provide valuable clues about the condition of the router bit. Changes in sound during cutting can suggest that the bit is experiencing increased friction, instability, or uneven wear. Regularly listening for these auditory cues helps you identify potential issues before they escalate.
- Checking Surface Finish: The quality of the surface finish produced by the router bit is another reliable indicator of its condition. If you notice rough edges, splintering, and inconsistent cutting depths on the workpiece, it is a clear sign that the bit may be dull or damaged. Monitoring changes in surface finish over time allows you to pinpoint when a bit requires sharpening or replacement, helping to maintain consistent machining quality and prevent further tool wear.
Diagnosing Common Problems
- Chatter and Vibration: Chatter occurs when the router bit encounters inconsistent resistance during cutting, causing oscillations that produce a rough surface finish and potentially damage the bit. This problem can arise from an improperly secured bit, worn tool holders, or incorrect feed rates and speeds. To troubleshoot this issue, ensure the router bit is properly installed and securely tightened in the collet, and verify that the workpiece is firmly clamped. Adjusting the feed rate and reducing the spindle speed may also help minimize chatter and improve cutting stability.
- Burning and Smoke: The presence of burning or smoke during machining is a common sign that the router bit is experiencing excessive friction and heat buildup. Causes of burning and smoke include using a dull bit, running the router at an incorrect speed, applying too slow of a feed rate, or failing to provide adequate cooling or lubrication. To address this, check the sharpness of the bit and replace or re-sharpen it if necessary. Adjust the spindle speed and feed rate to reduce heat generation and consider using a cooling system to keep the bit and material cool during cutting.
- Chip Size and Evacuation: The size and evacuation of chips produced during cutting can reveal much about the condition and performance of the router bit. If chips are too fine or dust-like, it may indicate that the bit is dull and removing material inefficiently. Conversely, chips that are too large could be the result of an overly aggressive feed rate. Poor chip evacuation, where chips accumulate around the cutting area, can cause friction, overheating, and reduced tool life. To troubleshoot these issues, adjust the feed rate and spindle speed to produce optimal chip size and use bits with proper flute designs for effective chip removal.
Corrective Measures
- Adjusting Speed and Feed Rate: One of the most effective ways to eliminate router bit damage is to optimize the speed (RPM) and feed rate of the CNC router. If the router bit is overheating, increasing the feed rate or lowering the spindle speed can reduce friction and heat buildup. Conversely, if the bit is experiencing chipping or struggling to cut, slowing the feed rate or increasing the spindle speed may improve cutting stability and reduce tool stress. Careful adjustment of these parameters ensures that the router bit engages with the material optimally, minimizing wear and extending its lifespan.
- Changing Router Bit Geometry: Another corrective measure to prevent router bit damage involves selecting the appropriate bit geometry for the specific application. For example, switching to a spiral bit with up-cut, down-cut, or compression flutes can improve chip evacuation, reduce heat, and provide a cleaner finish, depending on the material and cut requirements. Adjusting the number of flutes, cutting angles, or tip shapes can also enhance performance for specific materials, reducing the stress on the bit and preventing damage.
- Modifying Lubrication Methods: Proper lubrication reduces friction and heat during cutting, helping to prevent router bit damage. If excessive heat buildup is a problem, modifying the lubrication method can be highly effective. For metal cutting or other high-heat applications, using a mist cooling system or flood cooling can help dissipate heat more effectively. For softer materials, air blasts may be sufficient to clear chips and maintain cooling. Ensuring that the correct type of lubricant or coolant is used for the material being machined can optimize cutting conditions, reduce wear, and prevent damage to the router bit.
By following this troubleshooting process, you can effectively identify and address the causes of router bit damage, improving cutting performance, reducing downtime, and enhancing the overall lifespan of your CNC router bits.
Summarize
The above article content provides you with preventive measures and best practices to prevent CNC router bit damage, and guides you on how to troubleshoot according to the status of the router bit. By applying these strategies and regularly monitoring your tools, you can enhance the performance and lifespan of your router bits, achieve consistent machining quality, and minimize costly interruptions. Taking a proactive approach to bit care and maintenance not only ensures optimal cutting results but also contributes to a more efficient and productive CNC machining process. Continue reading “What Are The Factors That Affect The Life of CNC Router Bit?” for more maintenance advice.
AccTek CNC is a well-known CNC router manufacturer in China, recognized for its commitment to precision, durability, and performance. When using AccTek CNC routers, you can trust that the machines are engineered to maximize tool longevity and deliver superior cutting results. AccTek’s advanced CNC routers, combined with best practices, empower users to achieve consistent, high-quality machining outcomes, making them a reliable partner for all your CNC routing needs.