- 11-16 Min Read
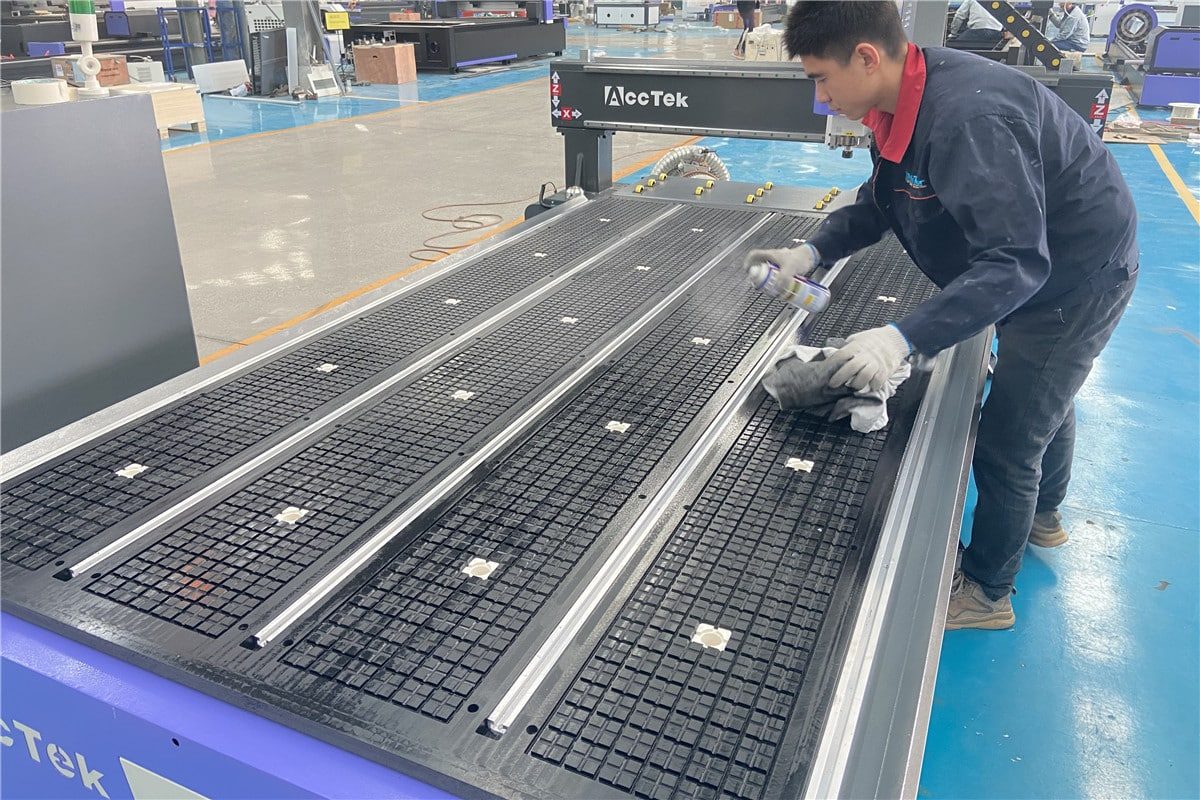
Why should CNC router be maintained regularly?
Regular maintenance of your CNC router is not just a routine task but a strategic investment in the reliability, efficiency, and longevity of the machine. It is a proactive measure that pays dividends in terms of precision, cost savings, and a seamless production process. By prioritizing maintenance, manufacturers can unlock the full potential of their CNC routers and maintain a competitive edge in today’s demanding and dynamic manufacturing landscape. The following are the main reasons why regular maintenance of CNC routers is necessary.
- Precision and Accuracy: CNC routers are renowned for their ability to execute intricate designs with exceptional precision. Regular maintenance ensures that critical components such as guide rails, ball screws, and bearings remain in optimal condition, preserving the machine’s accuracy in cutting, carving, and shaping materials.
- Extended Lifespan: Like any mechanical system, a CNC router experiences wear and tear during operation. Routine maintenance helps identify and address potential issues before they escalate, contributing to the extended lifespan of the machine. This proactive approach minimizes the risk of unexpected breakdowns and the need for major repairs.
- Reduced Downtime: Unplanned downtime due to equipment failure can have severe consequences for production schedules and project timelines. Regular maintenance minimizes the risk of sudden breakdowns, allowing for a more predictable and streamlined workflow.
- Cost Savings: Investing time and resources in preventive maintenance is a cost-effective strategy. Addressing minor issues before they become major problems can significantly reduce repair costs and prevent the need for costly replacements of critical components.
- Optimized Performance: A well-maintained CNC router operates at peak performance. This not only enhances the quality of finished products but also improves the overall efficiency of the machining process. Properly calibrated tools, well-lubricated components, and a clean working environment contribute to optimal performance.
- Safety Considerations: Ensuring the safety of operators and other personnel is a primary concern in any manufacturing environment. Regular maintenance helps identify and rectify potential safety hazards, such as loose components, worn-out parts, or malfunctioning electrical systems.
- Consistent Product Quality: Maintaining a CNC router at its optimal state contributes to the consistent quality of the manufactured products. Whether it’s creating prototypes, producing intricate components, or executing large-scale production runs, a well-maintained machine delivers reliable and repeatable results.
- Compliance with Manufacturer Recommendations: Following the manufacturer’s recommended maintenance schedule is essential. It helps preserve warranty coverage, ensures that the machine operates within specified parameters, and aligns with the manufacturer’s guidelines for optimal performance.
How to maintain a CNC router?
Daily Maintenance
- Clean the Workspace: Remove debris, dust, and chips from the work area, especially around the spindle and guide rails. Use compressed air or a vacuum system to clean hard-to-reach areas. This prevents contamination and ensures accurate cnc router machine movements.
- Check Emergency Stop Function: Verify that the emergency stop button is functioning correctly. This is a safety feature that should be regularly tested.
- Inspect Tooling: Check the condition of the cutting tool or router bit. Replace or sharpen tools as needed.
- Check Tool Changer: If your CNC router has an automatic tool changer, inspect it daily for any issues. Ensure that tools are properly secured, and the tool-changing mechanism is functioning correctly.
Weekly Maintenance
- Lubrication: Lubricate all moving parts according to the manufacturer’s recommendations. This includes guide rails, ball screws, bearings, and any other components specified in the manual. Use the recommended lubricants and follow the specified intervals for application. Proper lubrication prevents wear and ensures smooth operation.
- Inspect Belts and Chains: Check belts and chains for signs of wear, damage, or misalignment. Replace any worn-out components and ensure proper tension as per the manufacturer’s specifications.
- Inspect Vacuum System: If your CNC router has a vacuum system for dust collection, check and empty the collection bins. Ensure that the vacuum system is functioning properly.
- Backup Parameters: Periodically backup the CNC router’s parameters and settings. This ensures that you can quickly restore the machine to its optimal configuration in case of a malfunction or after maintenance.
Monthly Maintenance
- Check Electrical Connections: Inspect electrical connections for signs of wear or loose connections. Tighten any loose terminals and replace damaged wiring. Ensure that all wiring is secure and in good condition.
- Check Tightness: Periodically check and tighten all bolts, nuts, and screws. Vibration and movement during operation can cause them to loosen over time.
- Inspect Coolant Systems: If your CNC router uses a coolant system, check coolant levels and ensure that the system is working correctly. Clean or replace filters as needed. Address any leaks or malfunctions promptly to prevent damage to the spindle or other components.
- Calibration: Verify the machine’s calibration by running test programs. This helps ensure accuracy in the cutting and machining processes.
Quarterly Maintenance
- Inspect Spindle: Check the spindle for any signs of wear, unusual noises, or vibrations. If necessary, replace bearings or other worn components.
- Check Ball Screws and Lead Nuts: Inspect ball screws and lead nuts for wear and backlash. Adjust or replace components as needed.
- Air and Dust System Check: Inspect air and dust extraction systems for efficiency. Clean or replace filters as needed.
Yearly Maintenance
- Review Software and Firmware Updates: Check for updates to the CNC router’s control software and firmware. Keeping software up-to-date can provide performance improvements and additional features.
- Replace Worn Parts: Replace any worn-out components, such as limit switches, sensors, or belts, to maintain the overall reliability of the CNC router.
- Re-Calibration: Perform a thorough recalibration of the CNC router. Ensure all axes are parallel and perpendicular as required. Ensure all settings are aligned with the manufacturer’s specifications.
- Perform Preventive Maintenance: Consider a comprehensive preventive maintenance check, which may include more in-depth inspections and adjustments. Consult the machine’s manual for specific recommendations.
General Tips
- Create a CNC router Maintenance Plan: Develop a short-term and long-term maintenance plan suitable for your CNC router model according to the manufacturer’s guidelines. And follow a maintenance schedule for routine maintenance to prevent problems from occurring. Additionally, having a well-documented maintenance plan helps in budgeting and managing costs effectively.
- Operator Training and Skills Development: Provide ongoing training for machine operators. Educate them on the importance of routine maintenance, and encourage them to report any unusual observations or issues promptly.
- Keep a Maintenance Log: Maintain a log documenting each maintenance task, including the date, the tasks performed, and any observations or repairs made. This log can be invaluable for tracking the machine’s health over time.
The impact of environmental factors on CNC router maintenance
Temperature
- Impact: Extreme temperatures can affect the accuracy and efficiency of CNC routers. High temperatures may cause thermal expansion and affect the dimensional accuracy of machined parts, while low temperatures may affect lubrication and affect mechanical stiffness.
- Maintenance Considerations: Ensure that the CNC router operates within the recommended temperature range. Lubrication schedules may need adjustments in extreme conditions.
Humidity
- Impact: High humidity can contribute to corrosion of metal components and electrical issues, while low humidity can lead to electrostatic discharge and affect the performance of electronic components.
- Maintenance Considerations: Maintain humidity levels within the specified range. Use dehumidifiers or humidifiers as needed, and regularly inspect components for signs of corrosion.
Dust and Particulate Matter
- Impact: Dust and particulate matter in the environment can accumulate on machine components, affecting accuracy, and causing wear and tear.
- Maintenance Considerations: Implement a robust dust collection system. Regularly clean and inspect the machine, especially sensitive components like sensors, bearings, and ball screws.
Vibration
- Impact: Excessive vibrations from the surrounding environment or the machine itself can lead to misalignment, wear on moving parts, and reduced precision.
- Maintenance Considerations: Install the CNC router on a stable foundation. Regularly check and tighten bolts, fasteners, and connection points. Use vibration-dampening materials if necessary.
Air Quality
- Impact: Poor air quality with high levels of contaminants can affect the efficiency of cooling systems and contribute to increased wear on moving parts.
- Maintenance Considerations: Maintain a clean environment, regularly replace air filters in cooling systems, and consider air filtration systems to reduce contaminants.
Chemical Exposure
- Impact: Exposure to corrosive chemicals or fumes in the environment can lead to corrosion of metal components and deterioration of electrical connections.
- Maintenance Considerations: Protect the CNC router from exposure to corrosive substances. Implement proper ventilation systems and use chemical-resistant materials when applicable.
Lighting Conditions
- Impact: Inadequate or inconsistent lighting can contribute to errors in setup, inspection, and maintenance tasks.
- Maintenance Considerations: Ensure proper lighting in the CNC router workspace to facilitate accurate setup and inspection.
Space Constraints
- Impact: Limited space around the CNC router can hinder accessibility for maintenance tasks, potentially leading to delays or incomplete inspections.
- Maintenance Considerations: Plan the layout of the workspace to allow easy access for maintenance tasks. Ensure there is sufficient clearance for tool changes, inspections, and adjustments.
Troubleshooting and Problem Resolution
Machine Not Powering On
- Check Power Supply: Ensure that the machine is properly plugged in and that the power source is functioning. Check circuit breakers and power switches.
Axis Movement Issues
- Calibration Check: Verify the calibration of each axis. Recalibrate if necessary.
- Motor and Drive Inspection: Inspect motors and drives for loose connections, damaged wires, or faulty components.
Tool Alignment and Chatter
- Tool Calibration: Check tool calibration. Recalibrate if necessary.
- Spindle Speed: Ensure that the spindle speed matches the requirements for the material and tool being used.
Irregular Cutting or Carving
- Tool Wear: Inspect the cutting tool for wear and replace it if necessary.
- Material Holding: Check if the material is securely held in place, and ensure the workpiece is properly aligned. Adjust clamps or fixtures if needed.
- Z-Axis Calibration: Check the calibration of the Z-axis to avoid incorrect material penetration.
Excessive Vibration or Noise
- Loose Components: Check for loose bolts, nuts, or screws. Tighten as needed.
- Spindle Inspection: If applicable, inspect the spindle for signs of wear or damage.
Coolant System Issues
- Coolant Levels: Verify coolant levels and ensure the system is functioning properly.
- Clogged Lines: Check for clogs in coolant lines. Clean or replace as necessary.
Inconsistent or Interrupted Tool Changes
- Tool Changer Mechanism: Inspect the tool changer for proper functioning. Clean and lubricate if needed.
- Tool Change Sequence: Ensure the correct tool change sequence is programmed.
- Tool Holder Condition: Inspect tool holders for damage or misalignment, and ensure that tool holders are aligned correctly.
Emergency Stop Activation
- Check Emergency Stop Buttons: Inspect emergency stop buttons for proper functioning.
- Reset Procedure: Follow the manufacturer’s reset procedure to clear any emergency stop conditions.
Electrical Issues
- Voltage and Wiring Check: Verify that the machine is receiving the correct voltage. Inspect all wiring for damage or loose connections.
Software Errors
- Update Software: Check for software updates and install the latest version.
- Reprogram CNC Code: If there’s an issue with the CNC code, review and reprogram as needed.
Spindle Overheating
- Cooling System: Verify the spindle cooling system’s functionality.
- Correct Speeds and Feeds: Ensure the spindle is operating within recommended speeds and feeds.
Communication Errors
- Check Cables and Connections: Inspect communication cables and connections.
- Controller Settings: Verify CNC controller settings for communication parameters.
Loss of Positioning Accuracy
- Calibration Check: Verify the calibration of all axes.
- Mechanical Inspection: Inspect mechanical components for wear and tear.
Machine Jerking or Lagging
- Motor and Drive Inspection: Inspect motors and drives for signs of wear or malfunction.
- Check Controller Signals: Verify that the controller is sending signals correctly.
Safety Precautions for Maintaining CNC Router
During the maintenance of the CNC router, always prioritize safety and adhere to the specific safety recommendations provided by the CNC router manufacturer. Here’s a safety guide to follow when performing maintenance tasks on a CNC router. By following these safety guidelines, you can help create a safer work environment for maintenance personnel and minimize the risk of accidents during CNC router maintenance.
- Read the Manual: Always refer to the manufacturer’s safety guidelines and maintenance procedures outlined in the CNC router’s user manual.
- Training: Ensure that maintenance personnel are adequately trained on the specific safety procedures and protocols for the CNC router.
- Emergency Procedures: Familiarize maintenance personnel with emergency stop procedures. Mark and ensure easy access to emergency stop buttons.
- Lockout/Tagout: Implement a lockout/tagout (LOTO) procedure before starting any maintenance work. Ensure all energy sources (electrical, pneumatic, hydraulic) are properly isolated.
- Personal Protective Equipment (PPE): Wear appropriate PPE, including safety glasses, hearing protection, gloves, and any other necessary gear as specified by the manufacturer.
- Workspace Preparation: Clear the work area of any unnecessary tools, materials, or debris before starting maintenance. Use a clean and organized workspace to reduce the risk of accidents.
- Disconnect Power: Disconnect the CNC router from the power source before starting any maintenance work. Ensure the machine is completely powered down.
- Secure Moving Parts: Secure or immobilize moving parts, such as the spindle or gantry, to prevent unexpected movements during maintenance.
- Chemical Handling: If using cleaning agents or lubricants, follow proper handling procedures. Use chemicals in well-ventilated areas and wear appropriate protective gear.
- Tool Inspection: Inspect and properly store all tools before beginning maintenance. Ensure that tools are in good condition to avoid accidents during use.
- Ladders and Platforms: Use stable and secure ladders or platforms when accessing elevated parts of the CNC router. Follow proper ladder safety guidelines.
- Machine Stability: Ensure that the CNC router is stable and on a level surface during maintenance to prevent tipping or shifting.
- Communication: Establish clear communication channels between maintenance personnel and others in the vicinity. Use warning signs or barriers to indicate maintenance in progress.
- First Aid Kit: Have a well-equipped first aid kit available in the maintenance area. Ensure that personnel know the location of the first aid kit and how to use its contents.
- Safety Checks: Before restarting the CNC router after maintenance, conduct safety checks to ensure all components are properly secured and functioning.
What are the costs of maintaining a CNC router?
The costs associated with CNC router maintenance can vary based on factors such as the machine’s complexity, usage, age, and the type of maintenance required. It’s important to note that investing in regular and preventive maintenance can often lead to cost savings in the long run by reducing the frequency of unexpected breakdowns, extending the lifespan of components, and maintaining consistent production efficiency. Here are some common costs associated with CNC router maintenance:
- Labor Costs: If you have in-house maintenance personnel, the cost involves labor hours spent on routine maintenance, inspections, and repairs. If you hire external technicians or service providers for specialized maintenance tasks or repairs, labor costs may include service fees and hourly rates.
- Replacement Parts: Parts that wear out over time, such as cutting tools, lubricants, filters, and belts, incur regular replacement costs. Certain components, like bearings, ball screws, and spindles, may need periodic replacement due to wear and tear.
- Software Updates: Some CNC routers may require periodic software updates, and manufacturers may charge maintenance fees for access to the latest versions.
- Training Costs: Costs associated with training machine operators on routine maintenance tasks and troubleshooting procedures.
- Downtime Costs: Unplanned downtime can lead to lost production hours, affecting overall productivity and potentially resulting in financial losses.
- Emergency Repairs: Emergency repairs due to unexpected breakdowns may incur additional costs for urgent service calls, replacement parts, and overtime labor.
- Preventive Maintenance Tools and Supplies: Costs associated with purchasing lubricants, cleaning solutions, and other preventive maintenance supplies.
- Spindle Rebuilding or Replacement: Costs for spindle rebuilding, bearing replacement, or even full spindle replacement if significant issues are identified.
- Professional Inspections: Costs associated with hiring professional technicians for scheduled inspections or annual maintenance checks.
- Documentation Costs: If using digital maintenance management systems, there may be costs associated with software licenses or subscriptions for maintaining digital maintenance logs.
- Safety and Compliance Costs: Costs associated with ensuring that the CNC router complies with safety standards, including the purchase of safety equipment or modifications to meet regulatory requirements.