Table of Contents
How To Choose Auto Tool Changer Method For CNC Router?
- 11-17 Min Read
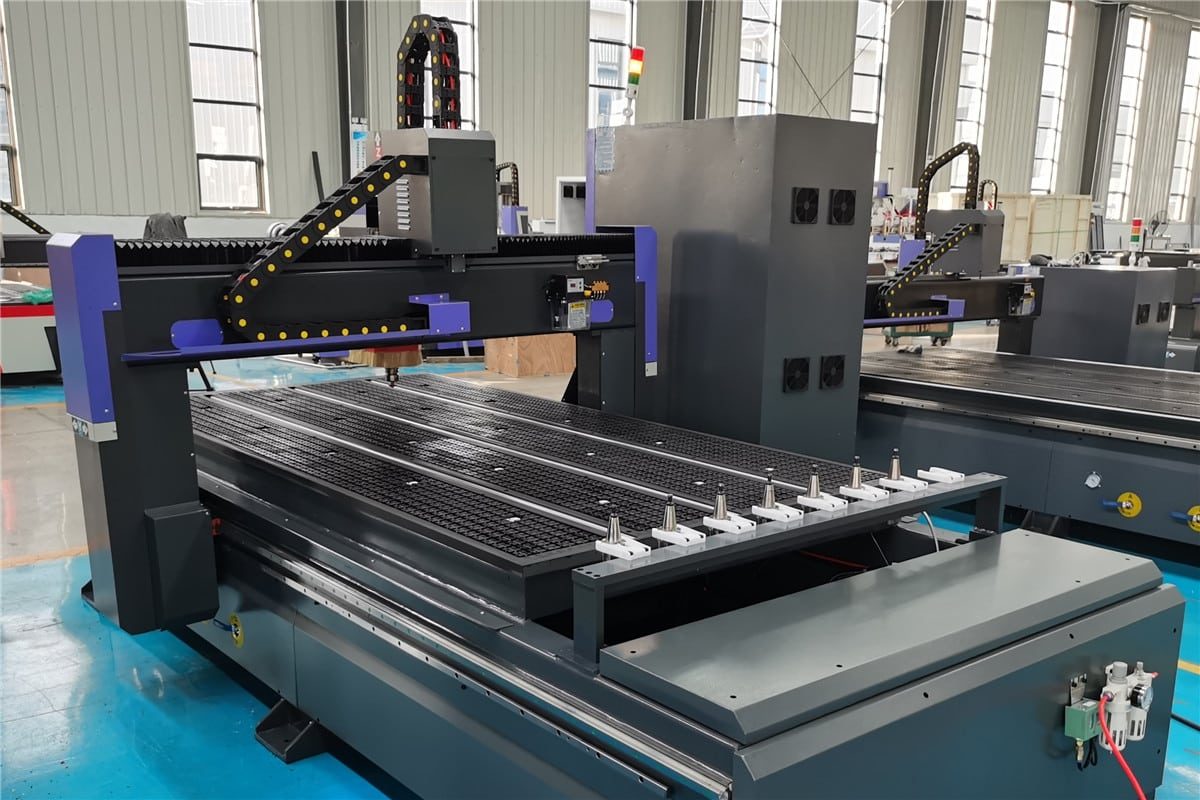
An ATC CNC router, or Automatic Tool Changer CNC router, is a type of computer numerical control (CNC) machine specifically designed to automate the process of tool changes during machining operations. CNC routers are used for cutting, carving, and shaping various materials such as wood, plastic, metal, and composites with a high degree of precision. The key feature that sets an ATC CNC router apart from a standard CNC router is its ability to automatically change cutting tools without requiring manual intervention. They are particularly useful in situations where a variety of cutting tools are required for different aspects of a machining project, as they streamline the production process and improve overall efficiency. Many factors affect the selection of automatic tool changers. In this article, we analyze the characteristics of different types of automatic tool changers from many aspects so that you can make the right choice based on actual needs.
Understanding Auto Tool Changer
An Automatic Tool Changing (ATC) device on a CNC router is a critical component that enhances the machine’s capabilities by allowing it to automatically switch between different cutting tools during a machining operation. This capability significantly improves efficiency, reduces downtime, and expands the range of applications the CNC router can handle. Here’s an introduction to the key aspects of a CNC router auto tool changer device.
- Tool Magazine: The heart of the ATC system is the tool magazine. This is a storage unit that holds various cutting tools, such as end mills, drills, and other tool types. The tool magazine can be in the form of a carousel or a linear rack, and it’s designed to store tools securely in designated slots. The number of tools a magazine can hold depends on the design and size of the CNC router, with some machines capable of holding dozens or even hundreds of tools.
- Tool Changing Mechanism: The tool changing mechanism is responsible for retrieving tools from the tool magazine and inserting them into the spindle. This mechanism is often equipped with a gripper or a similar device to securely hold and position the tools. The mechanism must be precise and reliable to ensure accurate tool changes and minimize the risk of tool damage or misalignment. The tool-changing mechanism operates based on commands from the CNC controller, which determines when a tool change is necessary during the machining process.
The importance of auto tool changer in CNC routing
The Auto Tool Changer is a critical feature that significantly improves the overall performance and capabilities of CNC routers. Its ability to automate tool changes enhances the efficiency of the machining process, allowing CNC routers to handle a broader range of tasks and contributing to increased productivity in various industries. Here are some key reasons highlighting the importance of an Auto Tool Changer in CNC routing.
- Time Efficiency: One of the primary advantages of an Auto Tool Changer is the significant reduction in downtime during machining. Manual tool changes can be time-consuming, and they interrupt the machining process. With an ATC, tool changes can occur automatically between different operations without the need for operator intervention, leading to a more continuous and time-efficient workflow.
- Increased Productivity: CNC routers equipped with an ATC can handle complex jobs with multiple tool requirements, enabling the machine to work continuously on a variety of tasks. This leads to increased overall productivity, as the machine can complete more jobs in a given timeframe. This capability is particularly valuable in high-volume production environments.
- Versatility and Flexibility: An ATC allows for the use of multiple tools in a single machining job. This versatility enables CNC routers to perform a wide range of operations, from roughing to finishing, without requiring manual adjustments. The ability to switch between different tools makes the CNC router suitable for various materials and applications.
- Improve Operator Efficiency: Manual tool changes not only consume time but also require operator attention. An ATC minimizes the need for operators to be present during the entire machining process. This reduction in manual intervention allows operators to focus on programming, job setup, and monitoring the overall machining process, rather than spending time manually changing tools, leading to more efficient use of manpower. This allows skilled operators to optimize and fine-tune the machining parameters for better results.
- Consistency and Accuracy: Automated tool changes contribute to consistent and accurate machining results. The ATC ensures that each tool is accurately positioned and securely held in the spindle, reducing the likelihood of errors associated with manual tool changes.
- Handling Complex Designs: CNC routing often involves intricate designs and complex shapes that require different tools for various aspects of the job. An ATC makes it feasible to execute these complex designs seamlessly by automatically selecting and changing tools as needed.
- Cost Savings: While the initial investment in a CNC router with an Auto Tool Changer may be higher, the long-term benefits include cost savings in terms of increased efficiency, reduced labor costs, and minimized material waste due to improved accuracy. These help make the manufacturing process more cost-effective.
- Optimized Machining Programs: CAM software, used to generate toolpaths for CNC routers, can take full advantage of an ATC. The software can optimize tool changes, speeds, and feeds, resulting in more efficient and precise machining programs.
- Reduced Risk of Accidents: Automated tool changes minimize the need for manual handling of sharp cutting tools, reducing the risk of accidents or injuries associated with manual tool changes.
What types of auto tool changers are there?
Several types of Auto Tool Changers (ATCs) are utilized in CNC routers, each with its own design and mechanism for automatically changing cutting tools during the machining process. The choice of an ATC type depends on factors such as the specific application, the size of the CNC router, the number of tools required, and the desired level of automation. Here are some common types of ATCs in CNC routers.
Disc Auto Tool Changer
A Disc Auto Tool Changer (ATC) is a specific type of automatic tool-changing system used in CNC machines, including CNC routers. The disc ATC is characterized by a tool magazine in the form of a rotating disc, often resembling a carousel or a circular disk with tool holders arranged around its perimeter. Each tool holder on the disc is equipped to securely hold a specific cutting tool. This design allows for quick and efficient tool changes during machining operations.
How does the disc ATC perform tool change?
The CNC controller, guided by the machining program and CAM software, determines when a tool change is required. When a tool change is commanded, the disc rotates to bring the designated tool holder containing the required cutting tool to the loading/unloading position. Once the correct tool holder is positioned, the tool-changing mechanism engages. The tool-changing mechanism retrieves the current tool from the spindle, releasing it from the tool holder. The tool is then moved to a designated location within the ATC. Simultaneously, the tool-changing mechanism retrieves the new tool from the selected tool holder on the rotating disc. The new tool is positioned and secured within the spindle’s tool holder.
Advantages of Disc ATC
- Speed and Efficiency: Disc auto tool changers are known for their quick tool changes. The rotating disc allows for rapid access to the required tool, minimizing downtime and contributing to higher machining efficiency.
- Compact Design: The space-efficient design of disc tool changers makes them suitable for CNC routers with limited space, allowing for more flexibility in machine layout.
Disadvantages of Disc ATC
- Limited Tool Capacity: Compared to some other types of ATCs, a disc ATC may have a more limited tool capacity. This limitation could be a drawback in applications requiring a large number of different tools.
- Complexity and Maintenance: The rotating disc mechanism involves moving parts, making the system relatively complex. This complexity may result in higher maintenance requirements compared to simpler tool-changing systems.
- Initial Cost: CNC routers equipped with disc ATCs may have a higher initial cost compared to machines with simpler tool-changing systems. The investment should be considered about the benefits and requirements of the specific application.
Linear Auto Tool Changer
The Linear Auto Tool Changer (ATC) is another type of tool changing mechanism used in CNC machining systems, including CNC routers. Unlike the Disc ATC, the Linear ATC features a linear arrangement of tools in a magazine. The tool magazine is typically a linear rack or tray that holds multiple tool holders in a row. Tools are securely held in individual tool holder slots along the linear track. This design is known for its straightforward and linear arrangement of tools, offering advantages in terms of tool capacity and maintenance simplicity.
How does the linear ATC perform tool change?
When a tool change is commanded in the CNC program, the CNC controller sends signals to initiate the tool changing process. The CNC router moves the spindle to the position of the selected tool along the fixed linear track. If a tool is currently in the spindle, it needs to be released. The spindle is then moved to the desired tool position for replacement. This movement is precisely controlled to align the spindle with the tool that needs to be exchanged. Once the new tool is in the spindle, a locking mechanism is activated to secure it in place. After the tool change is completed, the CNC router continues with the machining operation, utilizing the capabilities of the newly installed tool.
Advantages of Linear ATC
- Higher Tool Capacity: The linear arrangement allows for a larger number of tool slots compared to disc ATC. Well-suited for applications requiring a larger number of tools.
- Simpler Mechanical Design: The linear motion system is often simpler, leading to potentially lower maintenance.
Disadvantages of Linear ATC
- Longer Tool Change Times: Compared to disc ATC, tool changes may take slightly longer due to the linear motion.
- Space Requirements: The linear tool magazine requires more horizontal space within the CNC router.
Following Linear Auto Tool Changer
Similar to a Linear ATC, the Following Linear ATC has a linear tool magazine where cutting tools are arranged in a row. Tools are secured in individual holders within the magazine. The difference is that the Following Linear ATC has a unique design, and the tool magazine is mounted on a rigid frame attached to the CNC router. During the tool change process, the entire tool magazine moves along with the spindle.
How does the Following Linear ATC perform tool change?
The CNC controller sends signals to the Following Linear ATC to initiate the tool change process based on the instructions in the CNC program. Similar to the ordinary linear ATC, the previously used tool is released from the spindle and returned to its designated slot in the linear tool magazine. The spindle is then moved to the desired tool position for replacement. After the tool change is completed, the CNC router resumes the machining operation with the newly installed tool. The difference is that “following” implies that the linear ATC system is designed to follow the spindle and move on the gantry. This tool changing method greatly shortens the spindle movement stroke, thereby minimizing non-cutting time.
Advantages of Following Linear ATC
- Minimized Non-Cutting Time: Integration with the machine’s motion could result in minimal pauses during tool changes, leading to increased productivity. Faster tool change times compared to a traditional linear ATC. Well-suited for high-speed machining applications.
Disadvantages of Following Linear ATC
- Complexity: Synchronizing the linear ATC system’s movement with the machine’s motion may introduce complexity in programming and control.
- Precision Requirements: Requires precise coordination to avoid any misalignment or collisions during tool changes.
- Tool Length Limitations: The design of the Following Linear ATC may impose limitations on the maximum tool length that can be accommodated. This limitation could affect the selection of tools for certain machining tasks.
Factors affecting the selection of ATC method
The selection of the Automatic Tool Changer (ATC) method in a CNC router is influenced by several factors. Users need to balance between performance requirements, budget constraints, and long-term operational considerations. Considering these factors and conducting a thorough analysis of the specific requirements of the CNC router application will help in making an informed decision regarding the most suitable Automatic Tool Changer method. Here are key factors that affect the selection of an ATC method.
Application Requirements
- Material Types: Consider the types of materials being processed, as certain materials may require specific tool types.
- Application Complexity: Assess the complexity of machining tasks, including multi-axis operations.
- Production Volume: Consider the size and frequency of production batches to determine the desired tool change efficiency.
Tool Variety and Capacity
- Tool Types: The diversity of cutting tools needed for a particular application. Consider the variety of cutting tools needed for your applications (e.g., end mills, drills, etc.).
- Tool Capacity: Assess the total number of tools required for your specific machining tasks. Different ATC systems have varying tool capacities.
Tool Change Speed and Tool Change Time
- Cycle Time: Evaluate the required speed for tool changes to maintain overall machining efficiency.
- High-Speed Machining: If high-speed machining is a priority, choose an ATC that minimizes tool change times.
- Cycle Time Requirements: Align the chosen ATC system with specific cycle time requirements for efficient production.
Initial Cost and Budget
- Equipment Cost: Assess the upfront investment required for implementing a specific ATC system.
- Total Cost of Ownership: Consider maintenance, repair, and operational costs over the tool changer’s lifespan.
Integration with CNC Controller
- Compatibility: Ensure that the chosen ATC system integrates seamlessly with the CNC controller software.
- Ease of Programming: Consider the ease of programming for tool changes and overall system integration.
- Degree of Automation: Determine the level of automation required for the CNC router’s tool change process.
Other Factors
- Machine Size: Evaluate the available space within the CNC router for accommodating different ATC systems.
- Maintenance Requirements: Consider the complexity of maintenance tasks associated with different ATC systems.
- Tool Change Precision: Evaluate the level of accuracy required during tool changes to maintain machining precision.
- Ease of Use: Consider the simplicity and user-friendliness of the chosen ATC system, especially for operators with varying skill levels.
- Scalability: Assess the ability of the selected ATC system to accommodate potential increases in tool variety or production volume in the future.
By carefully evaluating these factors and conducting a comprehensive analysis of your specific CNC router application, you can make an informed decision when selecting the most suitable type of Automatic Tool Changer.
Summarize
The process of choosing the Auto Tool Changer (ATC) method for a CNC router involves a thorough analysis of various factors, each playing a pivotal role in the overall efficiency and productivity of the machining process. Whether prioritizing tool variety, production volume, speed, or space considerations, a well-informed decision ensures that the CNC router operates at its optimal capacity, delivering precision, reliability, and efficiency in every machining task. In the dynamic landscape of CNC machining, the continuous evolution of ATC methods contributes to pushing the boundaries of what is achievable in terms of automation, speed, and versatility. Choosing the right ATC method today is not just about meeting current needs but also about preparing for the challenges and opportunities that the future may bring to the world of CNC routing.
AccTek CNC is a provider of advanced technology in the realm of CNC routers, specializing in Automatic Tool Changer (ATC) systems. AccTek CNC provides users with high-quality ATC CNC routers designed to meet the demands of precision machining and intricate designs. These state-of-the-art machines are equipped with automatic tool change capabilities, streamlining the manufacturing process and enhancing efficiency. AccTek CNC’s dedication to innovation ensures that their machines deliver exceptional performance, making them a preferred choice for industries requiring precision and reliability. With AccTek CNC, users can achieve intricate and accurate results in their CNC routing projects. Contact us to learn more about ATC CNC routers.
Want To get a good machine?
Click the button, our CNC Experts will contact you and send you a solution.