- 12-17 Min Read
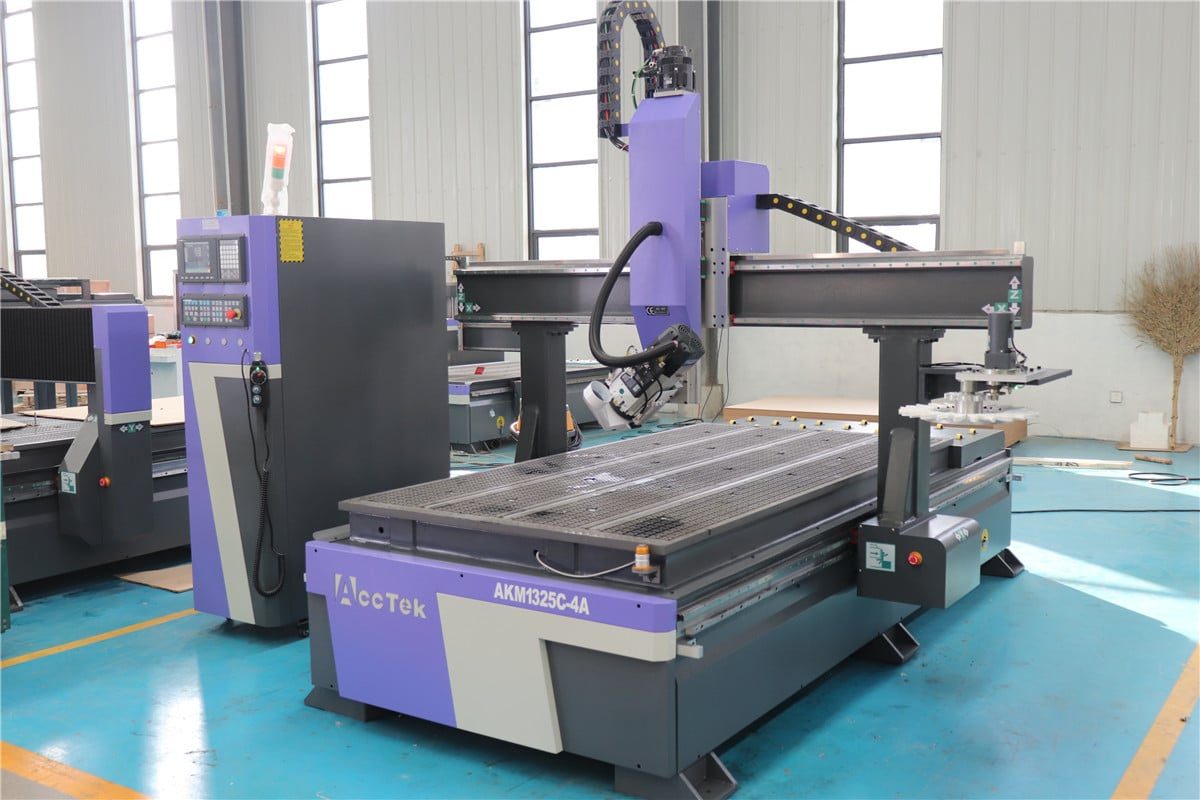
When selecting a CNC router, evaluating its energy consumption and operating costs is beneficial for maintaining cost efficiency in the long run. These machines can vary significantly in their energy demands based on factors such as spindle power, motor systems, and usage duration. Understanding how these elements contribute to overall energy consumption helps businesses avoid unexpected expenses and allows them to budget for operating costs more effectively. A well-informed evaluation of energy usage can also support efforts toward sustainability by reducing unnecessary power consumption.
In addition to energy usage, the operating costs of a CNC router include maintenance, tooling replacements, and potential downtime. These costs are influenced by the machine’s design, quality of components, and how frequently it is used. By carefully analyzing these factors, companies can make strategic decisions about which CNC router best suits their production needs while balancing upfront investment with ongoing operating expenses. This article will guide you through the key elements to consider when evaluating both the energy consumption and the overall operating costs of a CNC router, providing you with usability strategies to optimize efficiency and reduce operating costs.
Understanding the energy consumption of CNC routers
Understanding the energy consumption of CNC routers is a critical step in evaluating their long-term operational efficiency. The power consumption of a CNC router is typically influenced by power supply requirements, idling power and cutting power, and auxiliary systems. Each of these factors plays a role in determining the overall energy efficiency and cost of operating the machine.
Power Supply Requirements
CNC routers typically require a stable power supply to ensure consistent performance. The power rating of the spindle motor and the machine’s electrical components, such as the motion control systems, determine the voltage and current needed. Machines with higher spindle power ratings will demand more energy from the power supply, which can directly impact overall energy consumption during operation.
Idling Power and Cutting Power
CNC routers consume energy even when they are not actively cutting material. Idling power refers to the energy used to keep the machine ready for operation, including maintaining the spindle motor and motion systems in a standby state. In contrast, cutting power represents the energy consumed while the CNC router is actively engaged in cutting or shaping materials. Cutting power consumption is influenced by the type of material being processed, cutting speeds, and the complexity of the design. Optimizing cutting parameters can significantly reduce energy consumption during active operation.
Auxiliary Systems
In addition to the CNC router’s primary functions, auxiliary systems such as cooling systems, dust collection units, and lighting also contribute to overall energy consumption. Cooling systems are used to maintain the optimum operating temperature of the machine, especially in high-powered CNC routers. Dust extraction and filtration systems, necessary for maintaining a clean workspace and protecting machine components, also consume energy and should be factored into the total energy assessment. Managing these auxiliary systems efficiently can help reduce unnecessary energy waste and lower operating costs.
Factors affecting operating costs
Several factors influence the operating costs of a CNC router, making it essential for businesses to understand these variables to optimize their investment. These costs can be broken down into four main aspects: energy prices and tariffs, machine utilization, maintenance and servicing, and tool and material costs. Evaluating these areas can help identify opportunities for cost savings and improve the overall efficiency of the machine.
Energy Prices and Tariffs
Energy consumption is a key operating cost, and fluctuating energy prices or tariffs can affect the overall cost of running a CNC router. The location of the facility, local energy rates, and peak usage hours all contribute to how much businesses spend on electricity. Machines that operate during peak energy hours or in regions with higher electricity costs will face steeper operating expenses. To minimize these costs, businesses can explore energy-efficient CNC routers or schedule operations during off-peak hours to take advantage of lower tariffs.
Machine Utilization
Machine utilization directly affects operating costs by influencing how efficiently a CNC router is used. High machine utilization means that the machine is actively working for most of its available hours, thereby justifying its energy consumption and maximizing productivity. However, underutilization can lead to inefficiencies, as the machine still consumes idle power when not in use, adding to energy bills without producing valuable output. On the other hand, overutilization can result in excessive wear and tear, leading to frequent maintenance and reduced machine lifespan. So the optimal balance should be found—ensuring the machine is running at full capacity during peak production periods without overburdening it.
Maintenance and Servicing
CNC routers require regular maintenance to operate efficiently and to prevent costly breakdowns. Maintenance costs encompass a range of activities such as lubricating mechanical parts, recalibrating systems, replacing worn-out components, and conducting routine inspections. The quality and complexity of the machine largely determine the frequency and type of maintenance required. High-end machines with advanced components may require specialized technicians and costly replacement parts, which can drive up service expenses. Predictive maintenance strategies can help businesses plan for these expenses, reduce downtime, and extend the lifespan of the machine, all of which contribute to cost savings in the long term.
Tool and Material Costs
Tooling and material expenses significantly affect the operating costs of a CNC router. Cutting tools such as end mills, router bits, and drill bits wear out over time, particularly when processing hard materials like metals or composites. The frequency with which tools need to be replaced depends on the material being cut, the cutting parameters used, and the quality of the tooling itself. High-quality tools are often more expensive but offer better durability, reducing the frequency of replacements and downtime for tool changes.
In addition to tooling, material costs also play a role in determining operating expenses. Some materials may require slower cutting speeds or higher spindle power, increasing both energy consumption and tool wear. Investing in durable tools and adopting efficient material usage practices can lead to significant savings over the long term.
By carefully considering these factors, businesses can gain a comprehensive understanding of the factors that influence the operating costs of a CNC router. Effective management of these factors can lead to optimized operations, reduced expenses, and ultimately, a better return on investment.
Evaluate energy efficiency and operating costs
Evaluating the energy efficiency and operating costs of a CNC router requires a holistic approach that incorporates both energy consumption and the broader economic impact over the machine’s life span. This can be effectively assessed from four key perspectives: energy monitoring systems, energy efficiency indicators, total cost of ownership (TCO) analysis, and life cycle assessment (LCA). Each of these aspects provides valuable insights into optimizing energy efficiency and managing operating costs.
Energy Monitoring System
An energy monitoring system is beneficial for accurately tracking a CNC router’s real-time energy consumption. These systems allow businesses to measure power usage during various operational states, such as idle, cutting, and tool changes, offering detailed insights into how much energy is consumed at each stage of the process. By identifying periods of high consumption or inefficiencies, businesses can take steps to optimize machine operation.
The system can also track energy peaks during intensive tasks, enabling the adjustment of cutting parameters to reduce power usage. With this information, businesses can proactively manage energy consumption. Advanced energy monitoring systems often come with reporting tools that allow managers to evaluate trends, set energy consumption benchmarks, and optimize machine scheduling to reduce power use.
Energy Efficiency Indicators
Energy efficiency indicators are measurable metrics used to assess how effectively a CNC router uses energy. These indicators include metrics like the power consumption per unit of output (kWh per workpiece) or the power efficiency ratio (kW of power consumed versus machine productivity). Tracking these indicators over time helps businesses compare the energy performance of different machines or production processes and identify areas for improvement.
An efficient CNC router should demonstrate a high ratio of output relative to energy input. Machines with lower energy efficiency will have higher operational costs because they require more power to perform the same tasks. Additionally, tracking energy efficiency indicators enables businesses to benchmark their performance against industry standards, which can guide decisions on machine upgrades or changes in operational practices to reduce energy consumption.
Total Cost of Ownership (TCO) Analysis
Total cost of ownership (TCO) analysis provides a comprehensive view of the costs associated with owning and operating a CNC router over its entire lifespan. Beyond the initial purchase price, TCO considers ongoing expenses such as energy consumption, maintenance, tooling, and potential downtime. Energy efficiency directly influences TCO, as more energy-efficient machines will incur lower electricity costs over time, contributing to a lower overall TCO.
In evaluating the TCO, businesses should account for the long-term financial impact of energy consumption, including the effects of fluctuating energy prices and potential energy-saving initiatives. A machine with a higher upfront cost but superior energy efficiency may offer a more favorable TCO in the long run compared to a cheaper, less efficient machine that consumes more energy and requires frequent repairs. TCO analysis helps businesses make informed decisions about which CNC router offers the best balance of initial investment and long-term operating expenses, factoring in the total lifecycle costs of energy, maintenance, and tool replacements.
Life Cycle Assessment (LCA)
Life cycle assessment (LCA) evaluates the environmental and economic impact of a CNC router throughout its entire life cycle, from production to disposal. This comprehensive approach includes assessing the energy consumed during the machine’s manufacturing process, its operational lifespan, and the energy required for maintenance, repairs, and eventual recycling or disposal. LCA also evaluates the environmental footprint, including carbon emissions associated with the machine’s energy use.
In terms of operating costs, LCA allows businesses to understand how energy efficiency contributes to the machine’s overall environmental and financial impact. Machines that consume less energy over their operational life are more environmentally friendly and cost-effective. Furthermore, LCA provides insight into how long a machine can effectively operate before becoming obsolete or requiring costly repairs, allowing businesses to plan for replacement or upgrades at the right time. By conducting a life cycle assessment, companies can prioritize CNC routers that not only minimize energy consumption during operation but also have a reduced environmental footprint throughout their lifecycle.
Evaluating the energy efficiency and operating costs of CNC routers from the above four perspectives offers a comprehensive approach. The goal is to balance upfront investment in energy-efficient machines with ongoing operational savings, ensuring that the CNC router remains a cost-effective solution for production needs.
Strategies to optimize efficiency and reduce operating costs
Optimizing efficiency and reducing operating costs for CNC routers require a strategic approach that integrates thoughtful machine selection, material and tooling management, process improvements, and energy-saving practices. Below are four key aspects to consider when developing strategies to achieve these goals.
Machine Selection and Configuration
Choosing the right CNC router and configuring it appropriately is one of the most impactful ways to optimize efficiency and minimize operating costs.
- Select the Right Machine for the Job: When choosing a CNC router, you need to select a machine that matches the specific needs of your production process. For instance, a high-power machine may be more efficient for cutting hard materials like metals, but it would be overkill for softer materials such as wood or plastics. Selecting a machine with the appropriate spindle power, motor type (stepper or servo), and axis configuration can significantly affect efficiency and costs.
- Customizable Features: Opt for machines with customizable features that allow you to adapt the machine for specific tasks. For example, machines with automatic tool changers, multiple spindles, or rotary attachments enable faster transitions between tasks, improving productivity and reducing downtime.
- High-Quality Components: Invest in machines with high-quality components, such as precision linear guides and advanced control systems, which contribute to better performance and durability. While these machines may have a higher initial cost, their long-term benefits—such as fewer repairs, reduced maintenance, and better accuracy—translate into lower operating costs.
Material and Tooling Optimization
Efficient use of materials and tools can lead to significant cost savings and improve the overall productivity of a CNC router.
- Material Selection and Utilization: Optimizing material use by selecting the appropriate type and thickness for each job can lower waste and reduce overall costs. Using nesting software can help arrange parts more efficiently on the material sheet, minimizing waste. Additionally, choosing durable materials that require fewer adjustments or slower cutting speeds can help maintain a smooth workflow.
- Invest in High-Quality Tooling: High-quality cutting tools may have a higher upfront cost but offer greater durability, resulting in longer tool life and less frequent replacements. Tools with specialized coatings or materials, such as carbide or diamond-coated bits, can extend their lifespan when cutting tougher materials. Longer-lasting tools reduce downtime for tool changes and help maintain consistent cutting quality.
- Optimize Tooling Parameters: Fine-tuning cutting parameters such as spindle speed, feed rate, and depth of cut ensures that tools operate at peak efficiency, reducing wear and tear. Properly adjusted cutting parameters can also reduce material waste and improve the speed and quality of cuts.
Process Optimization
Process optimization focuses on improving the workflow, reducing idle time, and ensuring that the CNC router operates at its highest potential.
- Batch Processing: Grouping similar jobs together into batches reduces the need for tool changes and machine setup time. For example, cutting multiple parts from the same material in a single setup minimizes the machine’s downtime and maximizes throughput, helping reduce operating costs.
- Automated Workflow Solutions: Implementing automated systems, such as automatic tool changers, can improve process efficiency by reducing manual intervention. Automation reduces the time required to switch between tasks, leading to faster production cycles and lower labor costs.
- Minimize Downtime: Unplanned downtime can significantly increase operating costs. Implement a preventive maintenance schedule to address potential issues before they lead to breakdowns. In addition, having an efficient material handling system that reduces machine setup and material loading time can minimize idle time, allowing the machine to stay productive.
- Continuous Process Improvement: Regularly reviewing and refining machining processes can lead to ongoing improvements in efficiency. Analyze cutting parameters, material flow, and tool usage to identify areas for optimization. Implementing lean manufacturing practices can help eliminate waste, increase production speed, and reduce costs.
Energy Management Practices
Effective energy management is beneficial for reducing the overall operating costs of a CNC router. By implementing energy-saving practices, businesses can lower electricity bills while maintaining high production levels.
- Monitor Energy Consumption: Using energy monitoring systems helps track the real-time power usage of the CNC router. With this data, businesses can identify high-energy usage periods and adjust processes to operate more efficiently. For example, scheduling high-energy tasks during off-peak electricity hours can reduce energy costs.
- Energy-Saving Features: Many modern CNC routers come with energy-saving features such as power-down modes when the machine is idle or standby settings that reduce energy consumption during breaks between tasks. Ensuring these features are enabled can save energy over time without affecting productivity.
- Optimize Cooling Systems: Cooling systems, which prevent overheating of the machine’s spindle and motors, consume a significant amount of energy. Regular maintenance ensures that these systems operate efficiently, and adjusting the cooling power to the required levels based on machine workload can minimize energy waste.
Efficient Auxiliary Systems: Auxiliary systems such as dust collection, vacuum pumps, and lighting also contribute to energy usage. Installing energy-efficient equipment or using systems that activate only when needed can help reduce overall energy consumption.
Optimizing the efficiency and reducing the operating costs of a CNC router requires a comprehensive approach. By focusing on these four aspects, businesses can ensure that their CNC routers operate at peak efficiency, minimize waste, and keep operating costs under control, leading to improved profitability and a higher return on investment.
The importance of continuous improvement and monitoring
The importance of continuous improvement and monitoring lies in their ability to drive efficiency, innovation, and collaboration across operations. By fostering a culture of continuous improvement, implementing regular performance monitoring, and encouraging feedback and collaboration, businesses can achieve long-term success and adapt to evolving market demands. Here’s a detailed introduction from these three aspects:
Continuous Improvement Culture
A culture of continuous improvement emphasizes the ongoing pursuit of operational excellence and process optimization. This mindset encourages employees at all levels to seek out ways to improve workflows, reduce inefficiencies, and enhance product quality. In the context of CNC router operations, this culture promotes the regular evaluation of machining processes, energy use, and resource management to identify areas for enhancement.
The importance of such a culture lies in its ability to generate incremental improvements that lead to significant long-term gains. Instead of waiting for major disruptions to drive change, a continuous improvement culture encourages proactive, small-scale adjustments that cumulatively lead to higher productivity and lower operating costs. Additionally, businesses that embrace continuous improvement are better equipped to adapt to changing technologies, customer demands, and market conditions, ensuring sustained competitiveness.
Regular Performance Monitoring
Regular performance monitoring is beneficial to understanding the efficiency and effectiveness of a CNC router and other production systems. By tracking key performance indicators (KPIs) such as energy consumption, material use, tool wear, and machine uptime, businesses can gather valuable data that informs decision-making. Monitoring allows operators and managers to identify deviations from expected performance and take corrective actions before minor issues escalate into major problems.
The significance of regular monitoring lies in its ability to provide real-time insights into machine performance and production trends. This data-driven approach enables businesses to spot inefficiencies early, reduce downtime, and optimize resource allocation. For example, monitoring tool wear can help predict when a tool needs to be replaced, preventing costly breakdowns and extending tool life. Moreover, by tracking energy usage patterns, companies can implement strategies to reduce energy consumption during peak hours, lowering operational costs.
Feedback and Collaboration
Feedback and collaboration ensure that continuous improvement efforts and performance monitoring lead to tangible results. Encouraging feedback from operators, technicians, and other stakeholders allows businesses to gather diverse perspectives on process optimization and machine performance. Collaboration between departments—such as production, maintenance, and quality control—enables teams to work together on problem-solving and process refinement.
The importance of feedback and collaboration lies in their ability to foster a holistic approach to improvement. When employees feel that their input is valued and acted upon, they are more likely to engage with continuous improvement initiatives. Collaborative efforts across departments ensure that solutions are well-rounded and address multiple aspects of the production process, leading to more effective and sustainable improvements.
Continuous improvement and monitoring are beneficial for driving operational excellence and maintaining competitiveness. A culture of continuous improvement empowers businesses to proactively enhance processes, while regular performance monitoring provides the data needed to make informed decisions. Feedback and collaboration further amplify these efforts by fostering a team-oriented approach to problem-solving. Together, these aspects form a powerful framework for achieving sustained growth, innovation, and efficiency.
Summarize
Evaluating the energy consumption and operating costs of a CNC router is a key step in cost control for users. By understanding the factors that influence the energy consumption and operating costs of CNC routers and applying the strategies outlined in this article, businesses can effectively optimize their operations. This approach not only helps minimize unnecessary expenses but also enables continuous improvement, allowing companies to maintain better control over costs while maximizing the productivity and longevity of their CNC routers. For more information, read A Comprehensive Guide to CNC Router Power Consumption.
AccTek CNC, as a leading CNC router manufacturer in China, is an ideal choice for businesses seeking to optimize energy consumption and control operating costs. Our machines are equipped with energy-efficient components and customizable features that allow businesses to tailor the machine to their specific needs, minimizing energy usage and maintenance costs. By selecting an AccTek CNC router, you benefit from superior engineering that helps you reduce waste, improve productivity, and ensure a strong return on investment.