- 8-12 Min Read
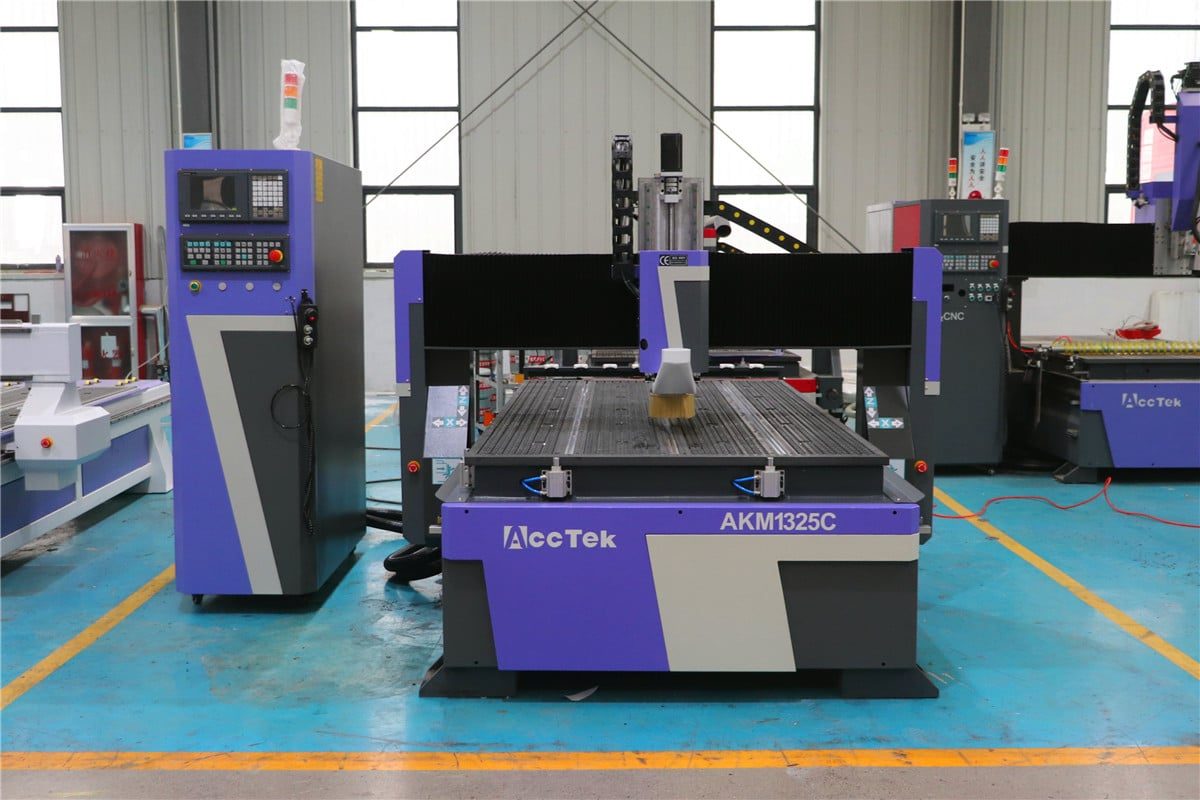
Chatter marks are a common challenge in CNC routing, often appearing as unwanted surface imperfections that compromise the quality of a finished product. These marks result from vibrations between the cutting tool and the workpiece, leading to irregular patterns that affect both aesthetics and precision. Left unchecked, chatter can reduce machining accuracy, cause excessive tool wear, and even lead to material waste.
Understanding the causes of chatter marks and implementing the right adjustments can significantly improve cutting performance. In this guide, we will explore practical methods to eliminate chatter marks, covering everything from optimizing machine settings to maintaining proper tooling and workpiece stability. By applying these strategies, CNC router operators can achieve cleaner cuts, extend tool life, and enhance overall machining efficiency.
Understanding Chatter Marks
Chatter marks are unwanted surface imperfections that appear as repetitive patterns, ridges, or waves on a workpiece after CNC routing. These marks occur due to excessive vibration between the cutting tool and the material, resulting in inconsistent cutting performance and poor surface finish.
Common Causes of Chatter Marks
Chatter marks can arise from several factors, including incorrect machine settings, improper tooling, or mechanical issues. Below are the most common causes:
- Improper Spindle Speed and Feed Rate: One of the most common causes of chatter marks in CNC routing is an incorrect combination of spindle speed and feed rate. When the spindle speed is too high or the feed rate is too low, the cutting tool may rub against the material instead of making clean cuts, leading to vibrations that produce chatter. Conversely, an excessively high feed rate with a low spindle speed can force the tool to cut too aggressively, causing instability and inconsistent cutting forces.
- Tool Deflection and Wear: Using an improperly sized or worn-out cutting tool can contribute to chatter by reducing cutting stability. A tool that is too long or has a small diameter is more prone to flexing under cutting forces, which results in inconsistent contact with the material. Additionally, dull or damaged cutting edges increase cutting resistance, leading to vibrations that manifest as chatter marks on the workpiece.
- Workpiece Rigidity and Fixture Setup: Insufficient support or improper clamping of the workpiece can cause it to vibrate during cutting, leading to chatter marks. When a material is not firmly secured, cutting forces can induce movement or flexing, preventing the tool from making stable and even cuts. This is especially problematic when working with thin sheets, large workpieces, or materials with high flexibility.
- Mechanical Issues with the CNC Router: Chatter marks can also result from mechanical problems within the CNC router itself, such as worn-out bearings, loose belts, or backlash in the motion system. Any instability in the spindle, linear guides, or drive system can create vibrations that transfer to the cutting tool, leading to surface imperfections.
The Influence of Chatter Marks on Machined Parts
- Reduced Surface Quality and Aesthetic Defects: Chatter marks create unwanted ridges and patterns on the machined surface, leading to a rough and uneven finish. Poor surface quality may necessitate additional post-processing, such as sanding or polishing, increasing production time and costs.
- Dimensional Inaccuracy and Poor Fit: Excessive vibrations during CNC routing can lead to deviations from the intended design, affecting the accuracy of machined parts. Inaccurate cuts can result in poor part fit, leading to functional issues in assembled products, wasted material, and the need for rework.
- Increased Tool Wear and Shortened Tool Life: Chatter marks indicate unstable cutting conditions, which generate excessive tool vibration and uneven loading. This results in increased tool wear, premature dulling, and potential tool breakage. Frequent tool replacements not only raise operating costs but also reduce productivity due to increased downtime.
- Compromised Structural Integrity of the Workpiece: In cases where chatter is severe, the excessive vibrations can weaken the structural integrity of the workpiece, especially in delicate or thin materials. Unstable cutting forces may introduce micro-cracks, fractures, or material fatigue, making the final product more susceptible to failure.
By understanding the causes and negative effects of chatter marks, CNC router operators can prioritize effective machining practices to prevent them, ensuring higher quality output, increased efficiency, and reduced operating costs. The next sections will explore specific techniques to eliminate chatter and optimize CNC routing performance.
Preventive measures to avoid chatter marks
Avoiding chatter requires a combination of proper tool selection, optimized machining parameters, machine stability, and secure workpiece clamping. The following sections explore preventive measures for chatter in CNC routing processes:
Tool and Tool Path Optimization
The proper tool selection and toolpath strategy can help reduce chatter during CNC routing.
- Tool Geometry Considerations: Using a rigid tool with a larger diameter and shorter length minimizes deflection and vibrations. Selecting the appropriate flute count and helix angle ensures smooth cutting forces and chip evacuation, reducing the chances of chatter.
- Tool Path Strategy: Implementing climb milling instead of conventional milling helps achieve more stable cuts. Trochoidal milling and adaptive toolpaths distribute cutting forces evenly, preventing sudden tool engagement that can induce chatter.
- Tool Path Simulation and Verification: Before actual machining, using CAM software to simulate toolpaths allows operators to detect potential vibration-prone areas. Adjusting entry angles, tool engagement, and cutting direction helps achieve more stable and controlled machining.
Ensuring Machine Rigidity
A rigid and well-maintained CNC router machine minimizes external vibrations that contribute to chatter.
- Proper Machine Maintenance: Regularly inspecting and tightening spindle bearings, linear rails, and motion system components helps eliminate mechanical looseness that may cause vibrations. Ensuring proper lubrication and cleaning prevents unnecessary wear and instability.
- Upgrading Machine Components: Replacing worn-out ball screws, linear guides, and drive motors with high-precision components enhances machine stability. A high-rigidity frame, along with a vibration-resistant spindle, improves cutting accuracy and surface finish.
- Damping Technology: Adding vibration-damping solutions such as tuned mass dampers, advanced tool holders with integrated damping, or filling machine cavities with damping materials helps absorb excess vibrations, reducing chatter during machining.
Optimizing Feed and Speed
Fine-tuning spindle speed and feed rate is beneficial to achieving smooth, chatter-free cuts.
- Feed and Speed Calculation: Using manufacturer recommendations, chip load calculations, and CNC cutting calculators helps set an optimal starting point for spindle speed and feed rate. Ensuring the cutting parameters match the material and tool type reduces excessive vibrations.
- Trial Cutting and Optimization: Performing test cuts and making small adjustments to spindle speed (increasing or decreasing by 5-10%) helps find the ideal cutting condition that minimizes chatter. Observing tool engagement and sound feedback allows for real-time optimizations.
- Dynamic Tool Path Adjustment: Leveraging CNC software to dynamically adjust feed rates and speeds based on cutting forces ensures consistent material removal. Features like adaptive feed control and high-speed machining strategies help prevent excessive vibrations.
Workpiece Clamping
Properly securing the workpiece is beneficial for preventing material movement and ensuring smooth cutting.
- Safe Workpiece Clamping Solutions: Using vacuum tables, mechanical clamps, or hybrid clamping solutions ensures that the material remains securely fixed during machining. Adjusting clamping force based on material type prevents unwanted shifting that may induce chatter.
- Minimizing Workpiece Flexibility: Supporting thin or flexible materials with sacrificial backers, additional fixtures, or reinforcement structures reduces vibrations. Ensuring uniform support across the workpiece prevents resonance effects that contribute to chatter marks.
- Balancing Material Removal Rate: Adjusting cutting depth and step-over ensures a stable material removal rate, reducing sudden load changes that can induce chatter. Using multiple shallow passes instead of a deep single cut improves cutting stability and finish quality.
By optimizing cutting parameters, maintaining machine rigidity, and implementing proper toolpath strategies, CNC operators can significantly reduce vibrations and achieve high-quality surface finishes. Regular monitoring, testing, and fine-tuning of machining processes will further enhance precision and efficiency, ensuring smooth and consistent CNC routing operations.
How to Troubleshoot Chatter Marks
Effective troubleshooting is the next step when chatter marks appear during the CNC routing process. This involves systematically analyzing these potential causes and implementing corrective actions. The following are four key areas to consider when diagnosing and troubleshooting chatter-related issues.
Identifying Chatter Patterns
Before applying solutions, the chatter pattern needs to be accurately identified to determine its root cause.
- Frequency Analysis: Using vibration analysis tools or listening to machine noise can help detect resonance frequencies contributing to chatter. High-pitched, periodic vibrations often indicate instability in tool engagement, while irregular sounds may suggest inconsistent feed rates or material inconsistencies.
- Visual Inspection of Machined Surfaces: Examining the surface finish of the workpiece can reveal important clues. Parallel wave-like patterns indicate excessive vibration, while irregular marks suggest tool deflection or poor chip evacuation. Identifying these patterns allows operators to make targeted adjustments to machining parameters and tool configurations.
Solving Tool Problems
Chatter often originates from issues related to the cutting tool itself, such as tool wear, imbalance, or improper selection.
- Tool Wear and Dullness: A worn or dull cutting tool increases cutting resistance, leading to inconsistent engagement with the workpiece and higher vibration levels. Replacing or re-sharpening tools regularly ensures clean, stable cuts and minimizes chatter.
- Tool Runout and Imbalance: If a tool is not properly seated in the collet or has excessive runout, it can cause uneven material removal, leading to chatter. Checking tool concentricity with a dial indicator and using high-quality, balanced tool holders can reduce runout and improve stability.
Machine-Related Solutions
Mechanical issues in the CNC router itself can contribute to chatter, requiring adjustments and maintenance.
- Spindle Speed and Acceleration Optimization: Adjusting spindle speed in small increments (5-10% variations) can help break resonance frequencies that cause chatter. Additionally, fine-tuning acceleration and deceleration settings in the CNC controller ensures smoother transitions and prevents sudden tool engagement shocks.
- Cutting Tool Holder and Collet Inspection: Loose or worn-out tool holders and collets can cause instability in the cutting tool. Regularly checking and replacing worn collets, ensuring proper tool tightening, and using precision-balanced holders improve tool grip and minimize vibrations.
Material and Workpiece Considerations
Material properties and workpiece stability play a key role in preventing chatter during machining.
- Material Hardness and Grain Structure: Harder materials or those with inconsistent grain structures can lead to uneven cutting forces, increasing the risk of chatter. Using appropriate cutting speeds and tool geometries for different materials helps maintain stability.
- Workpiece Support and Fixture Adjustment: An improperly secured workpiece can move during machining, amplifying vibrations. Using additional clamps, vacuum tables, or sacrificial support layers ensures better stability. Reducing overhangs and adjusting fixture positions to maximize support also prevents unnecessary flexing that leads to chatter.
By systematically addressing these aspects, CNC router operators can effectively troubleshoot and eliminate chatter marks, improving surface finish, tool life, and overall machining efficiency.
Preventive Maintenance for Long-Term Performance
Preventing chatter marks in CNC routing is not just about adjusting machining parameters, it also requires regular maintenance to ensure long-term machine stability and cutting performance. Implementing a structured maintenance routine can help minimize vibrations, extend tool life, and maintain machining precision. Below are key preventive measures for keeping CNC routers in optimal condition.
Regular Machine Inspection and Calibration: Routine inspections help detect potential issues before they lead to excessive vibrations and chatter. Checking spindle bearings, linear guides, ball screws, and belts for wear ensures the machine remains rigid and precise. Periodic calibration of machine axes and tool offsets also helps maintain accuracy and cutting stability.
Spindle and Tool Holder Maintenance: A worn or misaligned spindle can introduce vibration, affecting cutting performance. Regularly checking spindle runout, lubricating bearings, and ensuring tool holders are clean and properly balanced can prevent instability. Replacing worn-out collets and ensuring tools are securely tightened further reduces the risk of chatter marks.
Lubrication of Moving Components: Linear rails, ball screws, and other motion components require proper lubrication to reduce friction and maintain smooth operation. Following the manufacturer’s lubrication schedule prevents mechanical wear and helps maintain consistent cutting performance.
Worktable and Fixture Maintenance: Ensuring the worktable surface is clean and free of debris improves material stability and reduces vibrations. Periodic inspection of clamps, vacuum tables, and other fixturing systems helps maintain proper workpiece support, minimizing the risk of chatter caused by shifting materials.
Environmental Control and Vibration Damping: External factors such as temperature fluctuations and ambient vibrations can also contribute to chatter. Keeping the CNC router in a stable environment with minimal external vibrations ensures better cutting conditions. Adding vibration-damping materials to the machine base or using isolation pads can further reduce resonance effects.
By following these preventive maintenance practices, CNC operators can significantly reduce the occurrence of chatter marks, ensuring smoother finishes, improved tool longevity, and more efficient machining processes. Regular maintenance not only enhances productivity but also extends the overall lifespan of the CNC router.
Summarize
Eliminating chatter marks on a CNC router requires a combination of proper tool selection, optimized cutting parameters, machine stability, and secure workpiece clamping. Ensuring machine rigidity through regular maintenance, checking spindle bearings, and using vibration-damping techniques further enhances stability. Proper fixturing and support reduce material movement, preventing unwanted chatter. By applying these best practices and continuously fine-tuning machining parameters, CNC operators can achieve smoother cuts, improved accuracy, and enhanced overall efficiency in CNC routing.
AccTek CNC, a professional CNC router manufacturer in China, provides high-performance CNC routing solutions. By choosing AccTek CNC routers, businesses can optimize their CNC machining processes, reduce material waste, enhance productivity, and achieve consistent, high-quality results. Whether for wood, acrylic, aluminum, or composite materials, AccTek CNC provides reliable, precision-driven solutions that meet the demands of modern manufacturing.