- 13-18 Min Read
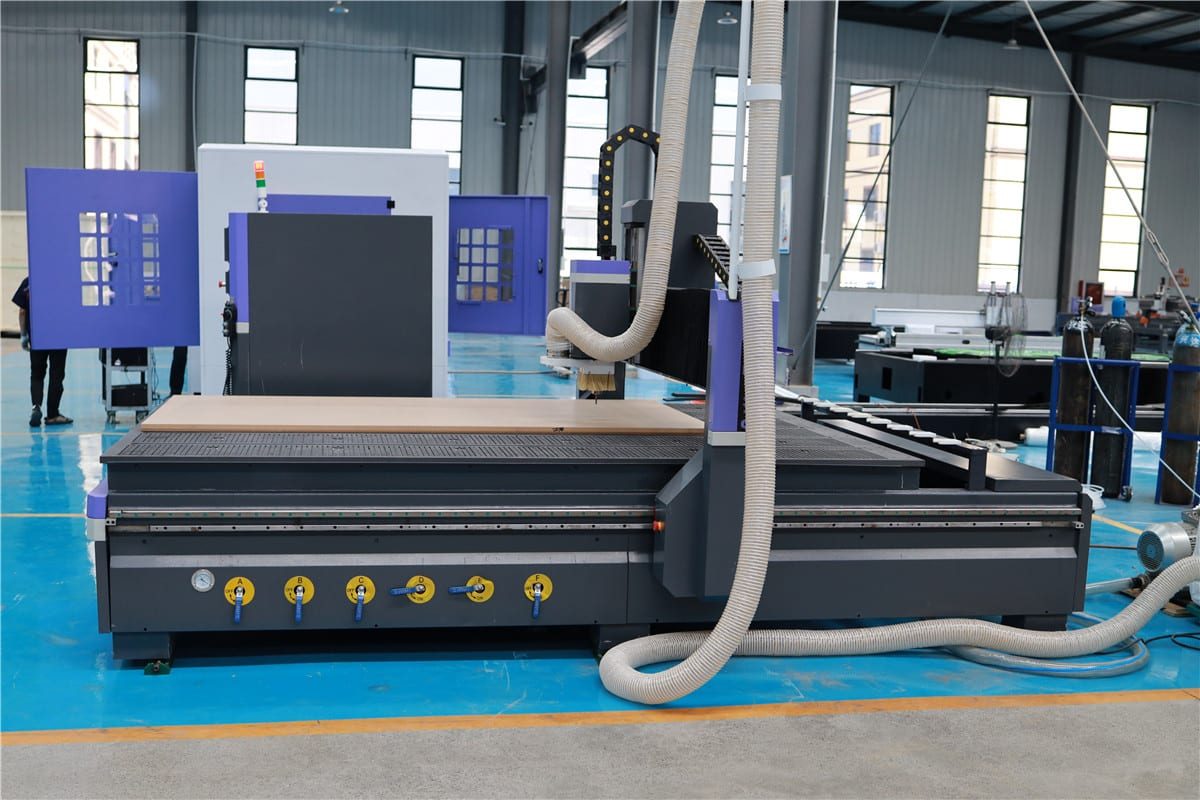
Leveling a CNC router is a crucial step in ensuring precise cuts, smooth operation, and long-term machine stability. Even minor misalignments in the machine’s frame or work surface can lead to uneven engraving, inaccurate cuts, and excessive tool wear. Whether you’re setting up a new CNC router or maintaining an existing one, ensuring that the machine is perfectly level will help maximize efficiency and extend its lifespan.
This article will explore the importance of leveling a CNC router, different methods and techniques used for the process, and a step-by-step guide to achieving a perfectly level machine. Additionally, we will cover calibration and testing to ensure accuracy, along with common challenges and solutions to help you troubleshoot potential issues. By following these guidelines, you can optimize your CNC router’s performance and achieve high-quality results with every project.
The Importance of Leveling a CNC Router
CNC router leveling directly affects the machine’s ability to produce accurate cuts, maintain consistent processing quality, and extend lifespan. Below, we explore the importance of leveling a CNC router from three key aspects:
Understanding the Impact of Bed Levelness
The foundation of a CNC router’s accuracy lies in the level of its machine bed. If the bed is not perfectly level, the gantry and spindle will not move evenly across the workpiece, leading to inconsistent cutting depths. This misalignment can cause one side of the machine to cut deeper than the other, resulting in errors in dimensions and poor fitment of machined parts. Over time, an unlevel machine bed can also cause excessive wear on linear guides, lead screws, and other mechanical components, reducing the machine’s operational efficiency and lifespan.
The Impact of Surface Unevenness on Processing Quality
Even if the machine bed is level, an uneven work surface—such as a warped spoil board or improperly secured material—can still compromise processing quality. Surface irregularities lead to variations in cutting depth, causing problems such as incomplete cuts, uneven engraving, and poor surface finishes. Properly leveling the machine and surfacing the spoil board ensure the tool maintains a consistent distance from the material, improving overall machining accuracy.
The Benefits of Proper Machine Leveling
A well-leveled CNC router offers several advantages:
- Improved Cutting Accuracy: Ensures consistent cutting depths, reducing errors and material waste.
- Extended Tool and Machine Lifespan: Minimizes unnecessary strain on the spindle, gantry, and cutting tools, preventing premature wear and mechanical failures.
- Better Surface Finish: Eliminates variations in engraving depth and rough edges, producing cleaner and smoother cuts.
- Increased Operational Efficiency: Reduces the need for rework and adjustments, allowing for higher productivity and cost savings.
By understanding the importance of leveling, CNC router operators can take proactive steps to maintain accuracy, improve efficiency, and extend the lifespan of their equipment. In the following sections, we’ll explore the various methods, techniques, and best practices for achieving an effective level CNC router.
Preparation Before Leveling the CNC Router
Before you level your CNC router, proper preparation is required to ensure the accuracy and efficiency of the leveling process. This involves selecting an appropriate installation location, inspecting the machine’s structural integrity, and cleaning the work surface. Here are the key steps to take before leveling your CNC router.
Machine Inspection and Maintenance
Before proceeding with leveling, check the CNC router’s overall condition to ensure that all components are in proper working order:
- Frame and Bed Stability: Check for any signs of warping, bending, or loosened fasteners in the frame and machine bed. Any misalignment can affect the leveling process.
- Gantry Alignment: Ensure the gantry moves smoothly along the rails and is not skewed or tilted. Misalignment at this stage can lead to errors in leveling.
- Spindle and Cutting Head Check: Inspect the spindle for any irregular movement or looseness that might affect precision.
- Legs and Support Structure: If the CNC router has adjustable feet, confirm that they are intact and capable of fine adjustments.
- Cleaning and Lubrication: Remove dust and debris from guide rails, lead screws, and linear bearings. Lubricate moving parts as needed to ensure smooth operation.
Workspace Preparation
A stable and well-organized workspace helps maintain the CNC router’s accuracy over time:
- Stable and Even Surface: Place the machine on a solid, vibration-free surface. Avoid uneven or flexible flooring that could shift over time.
- Controlled Temperature and Humidity: Drastic temperature or humidity changes can cause material expansion or contraction, affecting the machine’s stability.
- Vibration-Free Environment: Keep the machine away from heavy machinery, moving vehicles, or other equipment that may cause vibrations.
Gathering Necessary Tools and Equipment
Having the right tools on hand will make the leveling process more efficient and precise:
- Spirit Level or Digital Level: Necessary for checking and adjusting the level of the machine bed.
- Precision Straightedge and Feeler Gauges: Used to detect small gaps and irregularities in the surface.
- Machinist’s Dial Indicator: Helps check for fine-level variations.
- Adjustable Wrenches and Screwdrivers: Needed for making adjustments to the machine’s leveling feet and structural components.
- Shims or Leveling Feet: Used to compensate for uneven flooring or minor misalignments.
Ensuring Safety Protocols
Safety is a crucial aspect of CNC router machine maintenance and leveling:
- Power Off the Machine: Disconnect the CNC router from power before making any adjustments.
- Wear Protective Gear: Use safety gloves and protective eyewear to prevent injuries from sharp machine edges or moving parts.
- Check Electrical and Mechanical Components: Inspect wiring and moving parts to ensure there are no loose connections or potential hazards.
- Follow Manufacturer Guidelines: Always refer to the machine’s manual for specific safety recommendations and adjustment procedures.
By thoroughly preparing the CNC router before leveling, you can achieve more accurate adjustments and maintain long-term machine stability. In the next section, we will discuss methods and techniques for leveling your CNC router.
Leveling Methods and Technology for CNC Routers
Leveling a CNC router requires the use of a variety of methods and techniques. The operator needs to use different leveling methods depending on the design and structure of the machine. Below, we explore the key leveling methods and technologies commonly used in CNC router setups.
Three-Point Leveling System
The three-point leveling method is commonly used for CNC routers with a triangular support structure or smaller footprint machines.
Principle
- This system relies on three adjustable points (typically leveling feet or screws) to establish a stable plane.
- Two adjustment points are placed at the front corners, while the third is positioned at the back center, forming a triangular support.
- Adjustments are made until all three points are in contact with the reference plane, ensuring a level and stable machine base.
Advantages
- Quick and Easy Adjustment: Fewer points make it easier to level.
- More Stable Support: A three-point system prevents the machine from rocking or developing uneven stress.
- Ideal for Small and Medium-Sized CNC Routers: Works well for compact machines that do not require extensive structural support.
Disadvantages
- Limited Control Over Larger Beds: Larger CNC routers may need more support to prevent sagging.
- Not Suitable for Heavy-Duty Machines: Industrial CNC routers require additional support points for structural integrity.
Four-Point Leveling System
A four-point leveling system is the most common method for medium to large CNC routers, providing better control over the leveling process.
Principle
- The machine is supported by four adjustable leveling feet or screws at each corner.
- Each corner is individually adjusted to align the machine bed evenly across the X and Y axes.
- A spirit level or digital level is used to ensure balance from front to back and side to side.
Advantages
- Better Stability for Large Machines: Prevents frame flexing and ensures uniform contact with the floor.
- More Control Over Leveling Adjustments: Allows for precise corrections in multiple directions.
- Prevents Material or Bed Warping: Distributes weight evenly across all four points.
Disadvantages
- More Complex Adjustment Process: Requires careful fine-tuning at each point to avoid tilting.
- Possibility of Introducing Stress Points: If one corner is significantly higher or lower, it can create tension in the machine’s structure.
Alternative Leveling Technologies
For higher precision and automation, advanced leveling technologies can be used alongside traditional methods.
- Laser Leveling System: A laser level projects a straight reference beam across the CNC bed, ensuring precise alignment. Useful for industrial CNC routers requiring micron-level accuracy.
- Auto-Bed Leveling with Touch Probes: The CNC router scans the work surface using a touch probe to generate a digital height map. The control software compensates for minor inconsistencies in real time.
- G-Code Compensation Adjustments: Some CNC software allows G-code modifications to adjust for small leveling errors dynamically. This method works well when processing slightly uneven workpieces.
By selecting the appropriate leveling technology, CNC router operators can achieve optimal machine performance, ensuring precise, high-quality machining results. In the next section, we will cover a step-by-step guide to performing the leveling process effectively.
Step-by-Step Leveling Process for CNC Routers
When leveling the CNC router, a structured leveling method is required. This section provides a detailed, step-by-step guide to the CNC router leveling process. By following these steps, operators can maintain a stable and reliable CNC system for high-quality machining.
Initial Assessment and Adjustment
- Verifying Machine Placement and Stability: Before leveling, ensure the CNC router is placed on a stable and vibration-free surface. The floor should be solid and even to prevent shifts over time. Secure the machine frame properly and check that it is not subject to excessive movement or external vibrations.
- Checking the Machine Level Indicator: Most CNC routers have built-in level indicators or reference points to assess initial levelness. Place a spirit level or digital level on the machine bed and gantry to check for any tilt in both the X and Y directions. This initial check provides a baseline for adjustments and helps identify whether the machine is significantly out of alignment.
- Identifying Areas of Deviation or Misalignment: With the measurements from the precision tools, identify high and low spots on the machine bed. If the gantry is not parallel to the machine bed, it may cause inconsistent cutting depths. Mark the points where adjustments are needed, focusing on any misalignment in the machine frame, bed, or gantry.
Performing the Leveling Process
- Adjusting Machine Feet or Mounting Points: If the CNC router is equipped with adjustable leveling feet, raise or lower them incrementally to correct the tilt. For machines bolted to a surface, loosen the mounting points slightly and insert shims where necessary to bring the machine to an even position. Always adjust in small increments to avoid overcompensating and creating new misalignments.
- Using a Precision Level: After rough adjustments, place a precision level along the length and width of the machine bed. Ensure that readings are consistent in all directions. The level should be checked at multiple points on the bed to confirm that there are no unexpected variances in different sections of the machine.
- Fine-Tuning the Bed Level: Once the overall machine level is set, fine-tune the machine bed by adjusting the spoilboard or support structures. If the spoilboard is warped, a resurfacing pass using a large-diameter cutter can help create a perfectly flat work surface. Any remaining minor deviations can be corrected by using shims under specific sections of the machine bed.
- Verify Gantry Alignment: Move the spindle across the entire X and Y axes, ensuring the gantry stays at a consistent height. Mount the dial indicator on the spindle and move it across the bed to detect height variations. If needed, loosen and realign the gantry rails to ensure even movement.
Calibration and Testing
- Verifying Machine Calibration Parameters: Before running test cuts, ensure that all machine calibration settings align with manufacturer specifications. This includes checking the spindle alignment, axis movement accuracy, and stepper motor or servo motor settings. Use a dial indicator to measure movement precision along the X, Y, and Z axes, ensuring they travel the correct distances per input command. Additionally, verify that the machine’s software compensates correctly for backlash and other mechanical variances.
- Performing Test Cuts and Surface Inspections: Once the machine parameters are verified, perform a test cut on a flat material surface. Use a large surfacing bit to skim a thin layer off the spoilboard, revealing any remaining high or low spots. Inspect the cut pattern for inconsistencies such as uneven depths, tool marks, or variations in cut width. If the cutting depth is not uniform across the surface, it may indicate that further leveling adjustments are needed.
- Adjusting Tool Paths for Compensation: If minor variations remain after leveling, software compensation can help refine cutting accuracy. Many CNC control software options allow for Z-height adjustments to correct for slight inconsistencies. A touch probe or auto-bed leveling feature can map surface irregularities and adjust tool paths accordingly. Additionally, fine-tuning feed rates and spindle speeds can improve cut quality when working with materials that exhibit slight variations.
- Recording Leveling Procedures and Results: Documenting measurements from precision tools, any adjustments made to the machine frame or bed, and changes in software compensation settings will help streamline future realignments. Regularly scheduled checks using these recorded benchmarks ensure that the CNC router maintains optimal performance over time.
A properly leveled CNC router lays the foundation for precise and efficient machining. Through careful assessment, adjustment, and calibration, operators can eliminate inconsistencies and ensure that the machine performs at its best. Testing and verification further confirm that the leveling process was successful, minimizing the need for rework and prolonging the machine’s lifespan.
Common Challenges and Solution
Leveling a CNC router can be a complex process, with several challenges that may arise due to machine structure, environmental factors, or incorrect adjustments. Below are some of the most common issues encountered during the leveling process and effective solutions to address them.
Dealing with Machine Deformation and Bending
Over time, CNC router frames, beds, or gantries can experience deformation due to mechanical stress, improper handling, or heavy loads. A warped machine structure can lead to uneven cuts and inaccurate leveling. Here is the solution:
- Inspect the machine frame and bed for any visible signs of bending or warping.
- Use precision straightedge and feeler gauges to detect minor deformations.
- If the machine frame is warped, consider reinforcing the structure with additional bracing.
- For minor deformations, carefully adjust the machine’s leveling feet to compensate.
- If severe bending is present, consult the manufacturer for possible frame realignment or replacement.
Solving Structural Wear Problems
Long-term use of a CNC router can lead to wear in components such as linear guides, ball screws, and support structures, affecting the machine’s ability to maintain a level position. Here is the solution:
- Regularly inspect and maintain linear guides, bearings, and screws for signs of wear.
- Replace worn-out components to restore machine precision.
- Ensure all fasteners and structural connections are tight to prevent frame instability.
- Lubricate moving parts as recommended by the manufacturer to reduce excessive wear.
Dealing with Environmental Factors
External factors such as unstable flooring, vibrations from nearby equipment, temperature changes, and humidity can impact CNC router levelness over time. Here is the solution:
- Floor Stability: Place the CNC router on a solid, vibration-free surface. If the floor is uneven, use leveling feet or shims to stabilize the machine.
- Vibration Reduction: If the machine is near heavy industrial equipment, consider using vibration dampeners under the CNC router’s base.
- Temperature and Humidity Control: Sudden environmental changes can cause material expansion or contraction, affecting levelness. Ensure the workspace maintains a stable climate.
- Minimize Movement: Avoid unnecessary relocation of the machine, as frequent repositioning can disrupt leveling.
Eliminating Alignment Errors and Deviations
Misalignment between the CNC router bed, gantry, and spindle can result in uneven toolpaths and inaccurate cuts. Even after leveling the machine base, improper alignment of the moving components can cause precision issues. Here is the solution:
- Check Gantry Parallelism: Use a dial indicator or precision straightedge to ensure the gantry is parallel to the machine bed. Adjust gantry mounts if needed.
- Verify Spindle Perpendicularity: Ensure the spindle is perfectly perpendicular to the machine bed using a tramming gauge or dial indicator. Adjust the spindle mount if deviations are found.
- Calibrate Axis Movement: Run test cuts and measure actual movement against expected values. Adjust software compensation settings if necessary.
- Perform Regular Re-Leveling Checks: Over time, minor shifts can occur due to machine stress or vibration. Conduct periodic checks to maintain proper alignment.
By identifying and addressing these common challenges, CNC operators can ensure a properly leveled machine that delivers precise and consistent results. Regular maintenance, calibration, and monitoring will help maintain the accuracy and efficiency of the CNC router over time.
Maintenance and Periodic Inspection
Over time, factors such as vibrations, environmental changes, and normal wear can cause the machine to shift, affecting its performance. To prevent misalignment and ensure consistent machining quality, a structured maintenance and inspection plan is necessary. Below are key aspects of CNC router maintenance and periodic inspections.
Developing a Routine Maintenance Schedule
A well-planned maintenance schedule ensures that leveling issues are detected and corrected before they impact machining accuracy.
- Daily Maintenance: Clean the machine bed, check for visible misalignments, and ensure no loose fasteners.
- Weekly Maintenance: Use a spirit level to check the CNC router’s level and inspect the spoilboard for warping.
- Monthly Maintenance: Perform a more detailed check using precision measuring tools such as a dial indicator to verify machine bed flatness and gantry alignment.
- Quarterly Maintenance: Conduct a full re-leveling process, lubricate moving parts, and check for structural wear or deformation.
- Annual Maintenance: Inspect all major components, including the frame, leveling feet, and fasteners, and make any necessary repairs or replacements.
By following a structured routine, operators can minimize performance issues and extend the lifespan of their CNC router.
Monitoring Machine Performance Over Time
Tracking the CNC router’s performance can help identify gradual leveling issues before they become critical.
- Record Cutting Quality: Regularly inspect finished workpieces for variations in cutting depth, tool marks, or misalignment.
- Monitor Tool Wear: Uneven tool wear can indicate an unlevel machine bed or misaligned gantry.
- Log Machine Movements: Check for any shifts in machine position, especially if the CNC router is installed on an unstable surface.
- Use Diagnostic Tools: Some CNC software includes monitoring features that can detect minor deviations in machine movement and cutting accuracy.
Consistently monitoring performance ensures early detection of potential leveling issues, allowing for timely adjustments.
Performing Periodic Re-Leveling Procedures
Even with regular maintenance, CNC routers require periodic re-leveling to maintain accuracy.
- Check Machine Level Regularly: Use a digital level or inclinometer to measure deviations in the X and Y axes.
- Inspect and Adjust Leveling Feet: Over time, leveling feet may loosen or shift, requiring minor height adjustments or shim replacements.
- Re-Surface the Spoilboard: If the spoilboard shows signs of wear or unevenness, run a resurfacing pass with a large cutting tool to restore flatness.
- Verify Gantry and Spindle Alignment: Ensure that the gantry is parallel to the machine bed and the spindle is perpendicular to the work surface.
Performing re-leveling procedures on a scheduled basis prevents long-term misalignment and ensures consistent machining results.
Training Personnel on Leveling Procedures
Ensuring that all operators understand the importance of CNC router leveling and know how to perform maintenance is beneficial for long-term machine performance.
- Provide Training on Leveling Techniques: Teach operators how to use spirit levels, digital inclinometers, and dial indicators to check machine levelness.
- Demonstrate Adjustment Procedures: Train staff on how to adjust leveling feet, re-surface spoilboards, and correct gantry misalignment.
- Create a Maintenance Checklist: Establish a clear maintenance and inspection checklist for operators to follow.
- Encourage Proactive Monitoring: Train personnel to recognize early signs of leveling issues, such as inconsistent cutting depths or excessive tool wear.
By equipping operators with the knowledge to properly maintain and re-level the CNC router, businesses can prevent downtime and maintain high machining accuracy.
A well-maintained and periodically inspected CNC router ensures precision, efficiency, and longevity. By following a structured checklist and addressing issues proactively, operators can prevent misalignment issues and keep their CNC router in top condition. Regular attention to leveling and maintenance not only improves machining quality but also reduces costly repairs and downtime, ensuring smooth operations in the long run.
Summarize
Leveling a CNC router is not just a one-time task—it is an ongoing process that ensures precision, efficiency, and machine longevity. By following the structured steps outlined in this guide, from initial assessment and leveling to calibration and periodic inspections, operators can maintain a stable and reliable CNC system. Proper leveling enhances cutting accuracy, reduces tool wear, and prevents costly rework, making it an essential part of CNC router maintenance. With a commitment to proper leveling and maintenance, you can achieve precision results and maximize the full potential of your CNC router.
When it comes to achieving precision and reliability in CNC machining, selecting a high-quality CNC router is just as important as properly leveling and maintaining it. AccTek CNC is a professional CNC router manufacturer, whether it is woodworking, metal engraving or industrial applications, we can provide versatile, high-performance solutions. With comprehensive support and expert guidance, AccTek CNC ensures that every machine operates at peak efficiency, making it a trusted partner for professionals in need of reliable CNC machining. Visit AccTek CNC’s website to explore their range of CNC routers and take your production capabilities to the next level.