Table of Contents
How To Correctly Choose The CNC Router Spindle?
- 11-17 Min Read
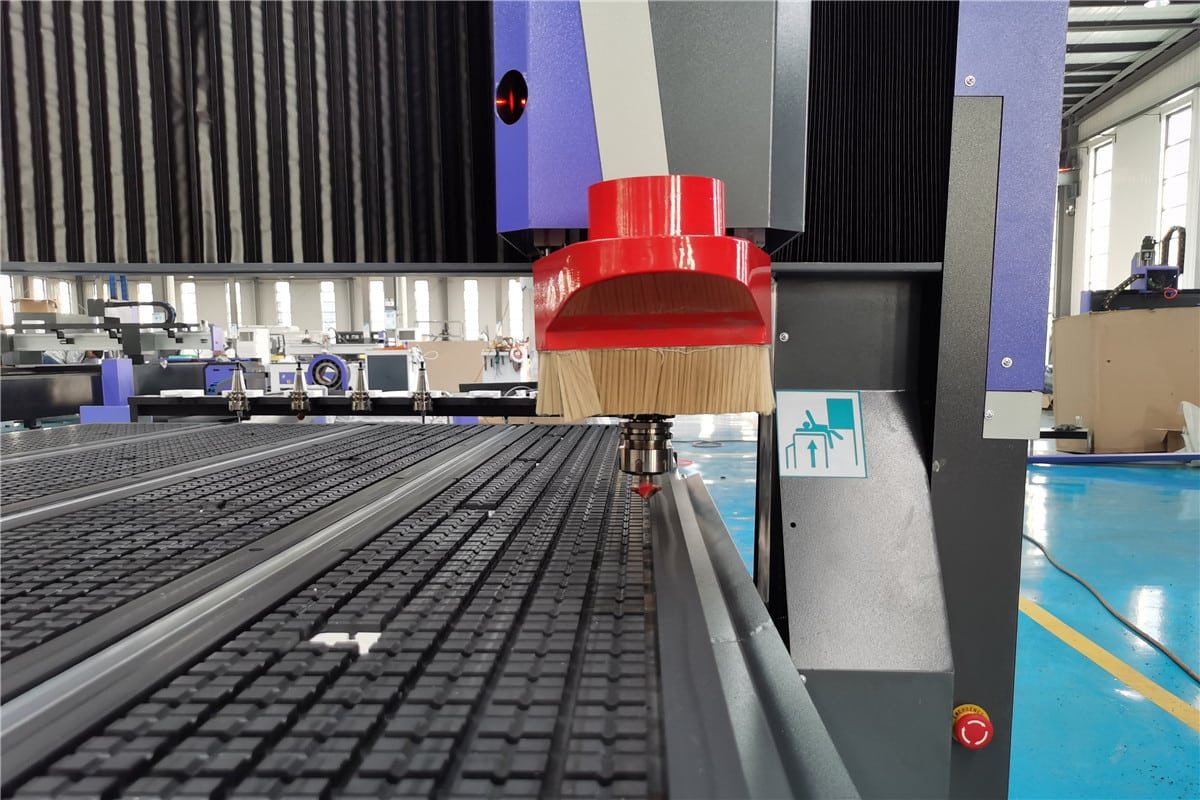
The spindle serves as the powerhouse of the CNC router, determining factors such as speed, precision, and tool compatibility. Selecting the right CNC router spindle is a critical decision that significantly influences the performance and capabilities of your machining operations. To embark on the journey of selecting the ideal CNC router spindle, it is essential to consider various factors that align with your specific needs and project requirements. From understanding different types of spindles to evaluating power and speed considerations, a well-informed decision at this stage lays the foundation for successful and efficient CNC machining. Let’s delve into the key considerations and guidelines to help you navigate the process of choosing the CNC router spindle that best suits your applications.
The importance of choosing the right spindle
Choosing the right spindle for a CNC router is a critical decision that significantly influences the performance, precision, and efficiency of the machining process. The spindle is the motorized component responsible for rotating the cutting tool or bit, and its selection has several important implications:
- Optimized Performance: The right spindle ensures optimal performance by matching the speed, power, and capabilities of the spindle to the specific requirements of the materials and cutting tools used. This results in efficient material removal and precise machining.
- Improved Precision And Accuracy: A well-matched spindle helps reduce runout, providing greater precision and accuracy for machined parts. It consistently achieves tight tolerances, resulting in a better-finished product.
- Improved Surface Finish: Correct spindle selection combined with appropriate cutting tools can help improve the surface finish of machined parts.
- Extended Tool And Spindle Life: Applying a correctly matched spindle reduces the risk of tool breakage and wear, thereby extending the life of the spindle and cutting tools and reducing maintenance costs and downtime.
- Reduce Material Waste: Using the right spindle for efficient machining minimizes material waste. CNC routers can achieve higher throughput and reduce the need for rework or scrap by optimizing cutting parameters and minimizing errors.
- Energy Efficiency: Choosing a spindle that aligns with the specific power requirements of the application contributes to energy efficiency. Running the CNC router with the right spindle can help minimize power consumption and reduce overall operating costs.
- Versatility and Adaptability: Some spindles are designed to be versatile and adaptable to various materials and applications. Choosing such a spindle allows for flexibility in machining tasks, enabling the CNC router to handle a diverse range of projects without compromising efficiency.
- Cost-Effective Operation: The right spindle can lead to cost savings in the long run by reducing the need for frequent tool changes, minimizing downtime, and lowering maintenance costs. A well-maintained and efficient spindle contributes to a more cost-effective machining process.
- Consistent Quality Across Production Runs: Matching the spindle to the specific requirements of the job ensures consistent quality across multiple production runs.
- Increased Productivity: Optimized spindle performance directly translates to increased productivity. The CNC router can operate more efficiently, allowing for faster cutting speeds and reduced machining time per part.
Understanding Spindle Specifications
A CNC router spindle is a crucial component that plays a pivotal role in the performance and precision of computer numerical control (CNC) routing machines. The spindle is essentially the motorized part responsible for rotating cutting tools, such as end mills or router bits, to carve, cut, or shape materials like wood, metal, or plastic. Understanding the key aspects of a CNC router spindle can help optimize the machining process. Here is an overview of the spindle specifications:
- RPM (Revolutions Per Minute): RPM indicates how fast the spindle rotates. It determines the cutting speed and surface finish. Higher RPM values are suitable for smaller tools and softer materials, while lower RPM is preferred for larger tools and harder materials. The right RPM depends on the material and the type of cutting tool being used.
- Torque: Torque is the rotational force or the spindle’s ability to maintain speed under load. Higher torque can cut dense or hard materials without significantly reducing speed. It influences the spindle’s ability to handle challenging cutting tasks.
- Horsepower (HP): Horsepower measures the overall power of the spindle motor. Higher horsepower generally allows the spindle to handle more demanding tasks and larger cutting tools. It allows for efficient material removal, especially in heavy-duty applications.
- Runout Tolerance: Runout tolerance refers to the deviation in the spindle’s axial or radial movement during rotation, impacting the precision of the machined parts. Lower runout tolerance ensures minimal tool deflection, resulting in more accurate and precise cuts. It minimizes wobbling, ensuring that the tool follows the intended cutting path accurately.
- Noise Level: Noise level measures the sound produced by the spindle during operation. Lower noise levels are desirable for a quieter working environment and improved operator comfort. However, noise may vary based on the spindle type (air-cooled vs. water-cooled) and design.
- Working Period: The working period or duty cycle is the amount of time the spindle can operate continuously before requiring a cooling or rest period. Understanding the working period can help prevent overheating and ensure the longevity of the spindle. The higher duty cycle reflects the spindle’s ability to handle extended periods of use without requiring frequent breaks for cooling.
What are the types of CNC router spindles?
CNC router spindles are essential components in CNC machines that perform various cutting, carving, and milling tasks. There are different types of CNC router spindles, and their selection depends on the application’s specific requirements. Here are some common spindle types and their characteristics.
Fixed Spindle and ATC Spindle
- Fixed Spindle: Fixed spindle power ratings range from a few kilowatts to tens of thousands of watts, depending on the size and purpose of the CNC router. Smaller hobbyist CNC routers may have 1.5 kW to 2 kW spindles. Fixed spindle for industrial CNC routers in the power range from 3 kW to 13.5 kW or higher. Fixed spindles typically have a fixed speed range, usually measured in revolutions per minute (RPM). A common speed range for a fixed spindle might be around 6,000 RPM to 24,000 RPM. Actual speed range may vary based on specific design and intended application.
- ATC Spindles: ATC spindles are available in a wide range of power ratings, similar to fixed spindles. The rated power for ATC spindles can start from around 2.2 kW for smaller machines and go up to 12 kW or more for industrial-grade CNC routers. The speed range of ATC spindles varies widely and can range from a few hundred RPM to tens of thousands of RPM. Its advantage is that it can automatically adjust the spindle speed to optimize cutting conditions for different tools and materials. In some high-speed machining applications, ATC spindle speeds can exceed 30,000 RPM or even higher. One of the key features of ATC spindles is their ability to automatically change cutting tools during a CNC router operation.
Water-Cooled Spindle and Air-Cooled Spindle
- Water-Cooled Spindle: Water-cooled spindles typically have a rated power ranging from around 1.5 kW to 7.5 kW. The power rating depends on the specific requirements of the application. Water-cooled spindles typically offer a wider speed range compared to air-cooled spindles. The maximum speed of a water-cooled spindle can range from a few thousand RPM (e.g., 6,000 RPM) to tens of thousands of RPM (e.g., 24,000 RPM or higher). These spindles use a water circulation system to dissipate heat generated during operation, allowing them to maintain stable performance even at high speeds.
- Air-Cooled Spindle: Air-cooled spindles often have a higher power rating compared to water-cooled spindles. The rated power can range from 1.5 kW to 13.5 kW or more, depending on the application and machining requirements. Air-cooled spindles generally have a more limited speed range compared to water-cooled spindles. The maximum speed of an air-cooled spindle can vary depending on the model but typically ranges from a few thousand RPM to around 18,000 RPM. Air-cooled spindles rely on a built-in fan or airflow to dissipate heat generated during operation, which can constrain the spindle’s maximum speed and its ability to maintain stability at higher speeds than water-cooled counterparts.
High-Frequency Spindle and Low-Frequency Spindle
- High-Frequency Spindle: High-frequency spindles often have a higher rated power compared to low-frequency spindles. The power can range from a few hundred watts to several kilowatts, depending on the application. High-frequency spindles are designed to operate at significantly higher speeds than low-frequency spindles. The speed range can vary, but it often extends from several thousand RPM (revolutions per minute) up to tens of thousands of RPM.
- Low-Frequency Spindle: Low-frequency spindles generally have a lower rated power compared to high-frequency spindles. The power can range from a few hundred watts to several kilowatts, but it tends to be lower on average. Low-frequency spindles operate at lower speeds compared to high-frequency spindles. The speed range typically extends from a few hundred RPM to several thousand RPM.
It’s important to note that these are general guidelines, and the specifications can vary based on the CNC router model and manufacturer. When selecting a spindle for a specific CNC router, it’s essential to consider factors such as the material being machined, the required cutting speeds, and the complexity of the machining tasks. Additionally, always refer to the manufacturer’s specifications and guidelines for the particular spindle model you are considering, as they will provide accurate and detailed information on rated power, speed ranges, cooling requirements, and other important parameters.
What should you consider when choosing a CNC router spindle?
Choosing the right CNC router spindle is a critical decision that can significantly impact the performance and capabilities of your CNC machine. Here are some factors to consider when choosing a spindle. By carefully considering these factors, you can select a CNC router spindle that aligns with your specific needs and ensures optimal performance for your machining applications.
- Power Rating: Consider the power requirements based on the materials you’ll be machining and the type of cuts you’ll be making. Higher power ratings are suitable for cutting denser or harder materials.
- Speed Range: Consider the spindle’s speed range, as different materials and cutting tools require specific RPM (revolutions per minute) for optimal performance. Ensure the spindle’s speed capabilities match your machining needs.
- Cooling Type: Choose between air-cooled and water-cooled spindles. Air-cooled spindles are generally simpler and may be suitable for light-duty applications, but may have limitations in heavy-duty or prolonged operations. Water-cooled spindles are more effective for dissipating heat during demanding tasks and heavy-duty operations.
- Tool Change Mechanism: If your application involves frequent tool changes or complex machining tasks, consider a spindle with an automatic tool change system. ATC spindles allow for automated tool changes, reducing downtime and increasing efficiency, especially for jobs with multiple tool requirements. Tool change times for ATC spindles can vary, but are usually very quick, typically within seconds.
- Collet Type and Size: Verify that the spindle is compatible with the types and sizes of cutting tools you plan to use. Check the spindle’s tool holder and collet system to ensure it accommodates your tools. This affects the variety of cutting tools you can use with the spindle.
- Precision and Accuracy: Evaluate the spindle’s precision and accuracy, especially if you require high-quality finishes or intricate details in your work. A high-quality spindle with low runout helps achieve tight tolerances and accurate cuts.
- Budget Considerations: Determine your budget constraints and find a spindle that meets your requirements while staying within your financial limits. Different spindle types and features come with varying price points. Keep in mind that quality and performance often correlate with price.
- Manufacturer Reputation: Choose spindles from reputable manufacturers with a history of producing reliable and durable products. Read reviews, seek recommendations, and check for customer feedback to assess the manufacturer’s track record.
- Compatibility with CNC Machine: Ensure that the chosen spindle is compatible with your CNC machine in terms of mounting, power requirements, and control interface. Ensure that the physical dimensions and weight of the spindle are compatible with your CNC machine’s specifications and structure.
- Ease of Maintenance: Look for spindles that are easy to maintain. Consider factors such as accessibility for cleaning, lubrication requirements, and overall maintenance procedures.
- Duty Cycle and Reliability: Consider the duty cycle and reliability of the spindle, especially if you anticipate continuous or heavy use. For heavy-duty or production-level work, choose a spindle with a higher-duty cycle.
- Application-Specific Considerations: Different applications may require specialized spindles. For instance, high-speed spindles are suitable for fine detailing and small tooling, while heavy-duty spindles are better for large-scale material removal. Choosing a spindle that aligns with your specific application ensures optimal results.
What impact does spindle type have on machine performance?
The type of CNC router spindle has a significant impact on the overall performance of the machining process. Different spindle types are designed to meet specific requirements, and their characteristics can influence factors such as speed, power, precision, and versatility. Let’s explore how fixed spindle vs. ATC (Automatic Tool Change) spindle, air-cooled spindle vs. water-cooled spindle, and high-frequency spindle vs. low-frequency spindle influence CNC router performance:
Fixed Spindle
- Simplicity and Cost: Fixed spindles are simpler in design and typically more cost-effective than ATC spindles. They have fewer moving parts, which can contribute to lower initial costs and reduced maintenance requirements.
- Tool Change Time: Fixed spindles have a longer tool change time since tools need to be manually changed. This can result in increased downtime, especially in applications requiring frequent tool changes.
- Suitability for Specific Applications: Fixed spindles are well-suited for applications where a limited number of tools are sufficient for the entire machining process. In scenarios where a variety of tools are needed, a fixed spindle may not be as efficient.
- Simplicity in Operation: The operation of a fixed spindle is straightforward, making it easier for operators, especially those new to CNC machining. There is less complexity in managing tool changes and tool offsets.
ATC Spindle
- Tool Change Speed: One of the primary advantages of ATC spindles is their ability to change tools automatically. This significantly reduces tool change time and increases overall machine efficiency, especially in applications requiring a variety of tools.
- Versatility: ATC spindles allow for a wide range of tooling options, making them suitable for complex machining tasks that require different tools for various operations. This versatility is particularly valuable in industries with diverse machining requirements.
- Reduced Downtime: The automatic tool change capability of ATC spindles minimizes downtime associated with manual tool changes. This can effectively keep productivity high, which is especially beneficial in an efficiency-driven environment.
- Precision and Accuracy: ATC spindles often come with features like tool length sensors and automatic tool calibration, contributing to improved precision and accuracy in machining. This is beneficial for applications requiring tight tolerances.
- Complex Job Handling: ATC spindles excel in handling complex machining tasks that involve multiple tools. They are well-suited for jobs that require intricate detailing, diverse cutting tools, and precise tool changes.
Air-Cooled Spindle
- Cooling Mechanism: Air-cooled spindles use a built-in fan or airflow system to dissipate heat generated during operation. This design simplifies the cooling process and eliminates the need for an external cooling system.
- Installation and Maintenance: Air-cooled spindles are generally easier to install and require less maintenance compared to water-cooled spindles. There is no need for a separate water cooling system or regular checks for coolant levels.
- Noise Level: Air-cooled spindles can be noisier due to the fan or airflow system. This may be a consideration in environments where noise levels are a concern.
Water-Cooled Spindle
- Cooling Mechanism: Water-cooled spindles use a water circulation system to dissipate heat, offering more effective and consistent cooling. This allows for sustained high-speed machining without overheating.
- Temperature Control: Water-cooled spindles provide better temperature control, as the cooling water absorbs heat more efficiently than air. This results in a more stable temperature during prolonged machining sessions.
- Precision and Stability: The superior cooling capacity of water-cooled spindles contributes to enhanced precision and stability. This is beneficial for applications requiring high precision and tight tolerances.
- Noise Level: Water-cooled spindles are generally quieter compared to air-cooled spindles. The water circulation system produces less noise, making it suitable for environments where noise reduction is important.
- Longevity: The efficient cooling provided by water-cooled spindles can contribute to the longevity of the spindle and associated components by reducing thermal stress.
High-Frequency Spindle
- Speed and RPM Range: High-frequency spindles typically operate at faster speeds and higher RPMs compared to low-frequency spindles. This allows for quicker cutting and finer detailing, making them suitable for applications that require precision and a smooth finish.
- Precision and Fine Detailing: The higher rotational speeds of high-frequency spindles contribute to enhanced precision and the ability to achieve fine details. This makes them well-suited for tasks such as engraving, intricate milling, and other applications demanding high precision.
- Lighter Cutting Tasks: High-frequency spindles are often more suitable for lighter cutting tasks, such as those involving softer materials or fine detailing. They may not be as well-suited for heavy-duty machining tasks that require high torque.
- Reduced Heat Generation: High-frequency spindles can generate less heat during operation due to their faster cutting speeds. This can be advantageous for certain materials and applications, as it helps in minimizing the risk of material deformation or damage.
Low-Frequency Spindle
- Power and Torque: Low-frequency spindles typically provide higher torque, making them well-suited for heavy-duty cutting tasks and machining harder materials. They excel in applications where a significant amount of material needs to be removed.
- Heavy-Duty Machining: Low-frequency spindles are often preferred for tasks that involve heavy material removal, such as roughing or profiling solid wood, aluminum, or other dense materials. Their higher torque allows for more efficient cutting in these scenarios.
- Enhanced Stability: The higher torque and lower speeds of low-frequency spindles contribute to enhanced stability during heavy cutting. This stability is beneficial for maintaining consistent cutting performance and preventing tool deformation.
- Adaptability to Larger Tools: Low-frequency spindles are generally more adaptable to larger cutting tools. This makes them suitable for applications that require the use of bigger tools, which may be necessary for certain machining tasks.
Precautions for specific applications of spindle
Using a CNC router spindle for different materials, such as wood, metal, and other specific materials, requires careful consideration of various factors to ensure safety, efficiency, and optimal performance. Here are precautions and guidelines for using a CNC router spindle with different materials:
Woodworking Applications
- Spindle Characteristics: Woodworking spindles are typically high-speed spindles designed for precision cutting and detailing in wood. They may operate at higher RPMs compared to spindles used for metalworking or other materials. Woodworking applications require looking for a spindle with minimal runout. A low runout spindle ensures that the cutting tool follows an accurate path, resulting in clean and precise cuts. Some woodworking spindles come with built-in cooling systems to dissipate heat generated during high-speed machining. Efficient cooling helps maintain consistent performance and extends the lifespan of the spindle.
- Speed Requirements: Woodworking spindles typically operate at higher RPMs compared to spindles used for metal or composite materials. The optimal RPM range depends on the specific wood being machined and the type of cutting tool being used. Having variable speed control is advantageous for woodworking applications. It allows operators to adjust the spindle speed based on the material, tool size, and the type of cut required.
- Power Requirements: Woodworking spindles come in different power ratings, typically measured in kilowatts (kW) or horsepower (HP). The motor power should be suitable for the intended woodworking tasks, considering factors like material density and the depth of cut.
Metalworking Applications
- Spindle Characteristics: Metal spindles are designed with a robust construction to withstand the forces and vibrations associated with cutting metal. Typically made from materials like stainless steel or other alloys with high strength and durability. Metal spindles often utilize high-performance motors, such as brushless DC motors or AC motors, capable of delivering the power required for metal cutting. To ensure accurate dimensions and surface finish of metal parts, metal spindles are often designed with low runout.
- Torque Requirements: Metal cutting often requires higher torque, especially when dealing with harder or denser metals. Ensure that the spindle provides sufficient torque to handle the cutting forces involved. A spindle with variable torque control allows for adjustments based on the specific cutting conditions and material hardness. This feature enhances adaptability to different metalworking tasks.
- Speed Requirements: Metal spindles should have a variable speed range to accommodate different cutting tools and materials. The ability to adjust the speed is beneficial for achieving optimal results with various metal types. Metalworking spindles need to operate at relatively high RPMs to achieve efficient cutting. Ensure that the spindle can reach the necessary high speeds for the intended applications.
Other Specific Material Applications
- Tool Selection: Choose cutting tools specifically designed for the properties of plastics or composite materials. Carbide or diamond-coated tools are often suitable for these applications.
- Spindle Speed and Cooling: Adjust spindle speed based on the material type. Use coolants or air blast systems to prevent material overheating and reduce tool wear. Some plastics may require special considerations for lubrication.
- Appropriate Torque: Ensure the spindle provides the appropriate torque for cutting through plastics and composites without causing damage to the material or excessive tool wear.
- Speed Range: Spindles should have variable speed control to accommodate different tool sizes and optimize cutting parameters based on specific material properties.
These considerations should be adapted based on the specific characteristics and requirements of the materials you are working with. Always refer to the CNC router and tooling manufacturers’ guidelines and recommendations for the materials and applications you intend to process.
Summarize
Choosing the correct CNC router spindle is a pivotal decision that directly influences the outcome of your machining projects. By carefully considering factors such as material type, spindle power, speed, torque, cooling systems, and safety measures, you can tailor your choice to meet the specific demands of your applications. Always refer to manufacturers’ guidelines for the specific spindle model and application requirements. By investing time in the selection process and staying attuned to the unique requirements of your materials, you can unlock the full potential of your CNC router and achieve superior results in your machining endeavors.
At AccTek CNC, we not only provide users with high-quality CNC routers but also provide users with purchasing planning guidance. If you’re not sure what type of spindle you need, tell us about the materials you want to machine, your machining requirements, and the results you want to achieve. Our professional sales team will provide you with complete solutions according to your needs. Contact us for more professional purchasing advice.
Want To get a good machine?
Click the button, our CNC Experts will contact you and send you a solution.