- 7-11 Min Read
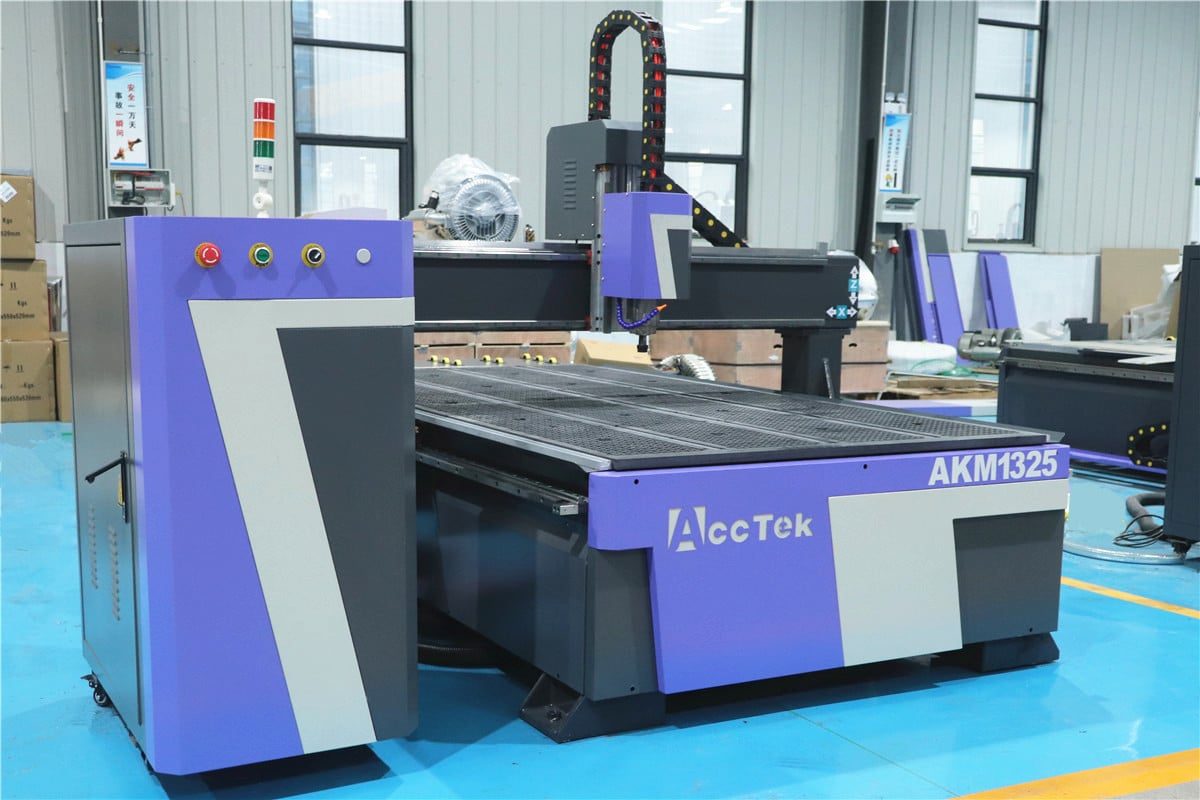
CNC routers are indispensable tools in modern manufacturing and woodworking, revolutionizing the way intricate designs are crafted with precision and efficiency. However, amidst their myriad benefits, they come with one significant downside: noise. The cacophony generated by CNC routers can be disruptive and even harmful if not properly managed. Fortunately, there are several strategies and techniques you can employ to block the noise of your CNC router effectively. In this guide, we will explore various strategies and technologies aimed at mitigating the noise generated by CNC routers. From simple and cost-effective measures to sophisticated soundproofing solutions, we will delve into the principles behind noise reduction and provide practical advice for implementing effective noise shielding strategies. Whether you’re a hobbyist seeking a quieter workshop environment or a professional machinist aiming to improve productivity and operator comfort, this guide will equip you with the knowledge and tools necessary to shield the noise of your CNC router effectively.
Understanding CNC Router Noise
How noise is generated in CNC router?
Noise and vibration are inherent aspects of CNC router operation, stemming from various mechanical and operational factors. Before delving into the solutions, it’s essential to understand the nature of the noise produced by CNC routers. The primary sources of noise include:
- Spindle Motor: The spindle motor is responsible for rotating the cutting tool at high speeds, generating considerable noise, especially during heavy-duty cutting operations.
- Cutting Tool: The interaction between the cutting tool and the material being cut can produce noise. This noise can vary depending on factors such as the material’s hardness, the depth of cut, and the feed rate.
- Motion Systems: CNC routers use various motion systems, such as stepper motors or servo motors, to move the cutting tool along different axes (X, Y, and Z). The movement of these motors and associated mechanical components, such as lead screws, belts, and bearings, can generate noise, especially if there is friction or wear.
- Vibration: Vibration is often a byproduct of the motion of the cutting tool and other mechanical components. Vibrations can cause additional noise, and if left unchecked, they can also affect the cut’s quality and the machine’s longevity.
- Vacuum System: Many CNC routers use vacuum systems to hold down the workpiece during cutting. The operation of these vacuum pumps can contribute to the overall noise level in the workspace.
- Cooling Systems:Cooling systems used to regulate the temperature of the spindle motor and other machine components can contribute to noise levels. Fans and pumps used for cooling may produce additional noise, particularly if they are not properly maintained or if airflow is restricted.
What are the factors that affect noise levels?
Several factors can influence the noise and vibration levels of a CNC router during operation. Understanding these factors can help identify noise and vibration sources and implement effective mitigation strategies. Here are some key factors that can affect noise and vibration levels:
- Machine Design: The design of the CNC router itself can have a significant impact on noise and vibration levels. Factors such as the rigidity of the machine frame, the quality of components (such as bearings and spindle motors), and the overall construction play a role in determining noise and vibration characteristics.
- Cutting Parameters: The cutting parameters used during machining operations, including spindle speed, feed rate, depth of cut, and cutting tool selection, can influence noise and vibration levels. Higher cutting speeds and deeper cuts generally result in increased noise and vibration.
- Material Being Processed: The type and properties of the material being processed can affect noise and vibration levels. Harder materials may require more aggressive cutting actions, leading to higher levels of noise and vibration. Additionally, the density and composition of the material can influence how vibrations propagate through the workpiece and machine.
- Tool Condition: The condition of the cutting tool, including its sharpness, wear, and alignment, can impact noise and vibration levels. Dull or damaged tools may produce more noise and vibration as they struggle to cut through the material effectively.
- Workpiece Fixturing: The method used to secure the workpiece during machining can affect noise and vibration levels. Poorly secured workpieces may vibrate excessively during cutting operations, leading to increased noise and potentially affecting the quality of the finished part.
- Enclosure and Workspace Design: The design of the workspace and any enclosures surrounding the CNC router can influence noise and vibration levels. Enclosures made from sound-absorbing materials can help dampen noise, while proper ventilation can prevent heat buildup and reduce the need for noisy cooling systems.
Effects of Noise and Vibration
During CNC router operation, both noise and vibration levels can vary based on numerous factors such as machine design, cutting parameters, material being processed, and environmental conditions. The following is an introduction to noise levels, vibration levels, and their effects during CNC router operation.
Noise Levels
CNC routers typically produce noise levels ranging from moderate to high, particularly during cutting operations. In a typical workshop environment, the noise level during CNC router operation can be anywhere from 70 to 100 decibels (dB) or more. Additionally, the noise level can vary depending on the specific operation being performed by the CNC router. For example, the noise level may increase during heavy cutting operations or when using certain cutting tools or materials that generate more noise.
Prolonged exposure to high noise levels can pose risks to occupational health, including hearing damage, tinnitus, and other auditory issues. High noise levels can also contribute to operator discomfort and fatigue, affecting concentration, productivity, and overall job satisfaction.
Vibration Levels
CNC routers generate mechanical vibrations during operation, primarily due to the motion of the cutting tool, spindle motor, and other machine components. These vibrations can propagate through the machine structure and into the surrounding environment.
Excessive vibration can adversely affect machine performance, leading to decreased accuracy, surface finish quality, and tool life. Additionally, vibrations transmitted to the operator can cause discomfort, fatigue, and even musculoskeletal disorders over time.
How to measure and assess noise and vibration levels?
Measuring and evaluating the noise and vibration levels of CNC routers can help identify potential hazards, and implement effective mitigation strategies. Here’s a step-by-step guide on how to measure and evaluate noise and vibration levels. By following these steps, operators can effectively measure and evaluate the noise and vibration levels of CNC routers, identify areas for improvement, and implement targeted interventions to create a safer and more comfortable working environment.
Determine Measurement Locations
- Identify key areas where noise and vibration measurements need to be taken, including near the CNC router, operator workstations, and surrounding areas.
- Consider factors such as distance from the machine, potential sources of noise and vibration, and areas where operators are likely to be exposed.
Select Measurement Instruments
- Choose appropriate instruments for measuring noise and vibration levels. Common instruments include sound level meters for noise measurement and vibration meters or accelerometers for vibration measurement.
- Ensure that the selected instruments are calibrated and suitable for the intended measurement environment and frequency range.
Establish Measurement Protocols
- Develop standardized measurement protocols to ensure consistency and accuracy in data collection.
- Determine factors such as measurement duration, sampling rate, and measurement locations to capture representative data.
Conduct Noise Measurements
- Place the sound level meter at the designated measurement locations, ensuring that it is positioned according to relevant standards and guidelines.
- Record noise levels in decibels (dB) at various frequencies, taking into account both continuous noise and peak noise levels during CNC router operation.
- Measure noise levels during different operating conditions, such as idle, cutting, and tool change operations, to capture variations in noise emissions.
Perform Vibration Measurements
- Position the vibration meter or accelerometer at key locations on the CNC router and surrounding structures to capture vibration levels.
- Record vibration levels in units such as acceleration (m/s²), velocity (mm/s), or displacement (mm) across different frequency ranges.
- Measure vibrations in multiple axes (X, Y, and Z) to assess the overall vibration characteristics of the machine.
Analyze Measurement Data
- Analyze the collected data to identify patterns, trends, and potential sources of noise and vibration.
- Compare measured noise and vibration levels with relevant standards, regulations, and recommended exposure limits to assess compliance and identify areas of concern.
- Consider factors such as frequency spectra, octave bands, and weighting filters to gain insights into the frequency distribution and characteristics of noise and vibration emissions.
Interpret Results and Take Action
- Interpret the measurement results in the context of the CNC router’s operation, workspace environment, and potential health and safety implications.
- Take appropriate action based on the findings, such as implementing noise control measures, optimizing machine settings, or providing personal protective equipment (PPE) for operators.
- Monitor noise and vibration levels over time to track changes, evaluate the effectiveness of mitigation measures, and ensure ongoing compliance with regulatory requirements.
Strategies for Blocking CNC Router Noise
Blocking the noise of CNC routers requires a multifaceted approach that addresses the various sources and characteristics of noise generation. Now that we’ve identified the primary sources and influencing factors of CNC router noise, let’s explore a range of strategies and techniques to effectively block and mitigate this noise:
Spindle Enclosure
Since the spindle motor is a significant source of noise, enclosing it separately can help mitigate noise effectively. Here’s how to create a spindle enclosure:
- Compact Design: Design a compact enclosure specifically for the spindle motor, ensuring it fits snugly around the motor housing.
- Soundproofing Materials: Line the interior walls of the spindle enclosure with sound-absorbing materials such as acoustic foam or soundproofing blankets to dampen the noise.
- Ventilation: Incorporate ventilation openings with soundproof baffles to ensure adequate cooling while minimizing noise leakage.
Vibration Damping
In addition to blocking airborne noise, addressing mechanical vibrations can further reduce overall noise levels. Here are some techniques for damping vibrations:
- Isolation Mounts: Install vibration isolation mounts or pads beneath the CNC router and other equipment to decouple them from the floor and reduce the transmission of vibrations.
- Damping Materials: Apply vibration-damping materials, such as rubber pads or neoprene sheets, to the base of the CNC router and other vibrating components to absorb and dissipate vibrations.
- Structural Reinforcement: Reinforce the structure of the CNC router and surrounding work surfaces to minimize resonance and dampen vibrations. Stiffen weak or flexible components using braces or additional support.
Soundproofing Techniques
Incorporating soundproofing materials and techniques can further enhance noise reduction efforts. Here are some soundproofing strategies to consider:
- Acoustic Curtains: Hang acoustic curtains around the CNC router area to absorb sound and prevent it from spreading to other parts of the workspace.
- Noise Barrier Walls: Install noise barrier walls or partitions made of sound-absorbing materials to create a dedicated quiet zone for the CNC router.
- Double Glazing: If the workspace has windows, consider installing double-glazed windows with laminated glass to improve sound insulation.
- Soundproof Curtains: Hang soundproof curtains or drapes over doors, windows, and openings to provide additional noise absorption and blockage.
Cutting Tool Selection
Choosing the right cutting tools can also make a significant difference in reducing CNC router noise. Here are some tips:
- Router Bit Selection: Opt for high-quality router bits with carbide cutting edges, as they produce less noise compared to inferior-quality bits.
- Cutting Speed: Adjust the cutting speed and feed rate parameters in your CNC router’s software to minimize noise while maintaining cutting efficiency.
- Tool Maintenance: Regularly inspect and maintain your cutting tools to ensure they remain sharp and properly balanced, as dull or unbalanced tools can produce excessive noise.
Machine Maintenance and Optimization
Regular maintenance and optimization of the CNC router can also contribute to noise reduction. Here are some maintenance tips to keep noise levels in check:
- Lubrication: Ensure that all moving parts, such as bearings, lead screws, and guide rails, are adequately lubricated to minimize friction and noise.
- Tooling: Use sharp and properly maintained cutting tools to reduce vibrations and noise during cutting operations. Replace worn or damaged tools promptly.
- Optimized Parameters: Adjust cutting parameters, such as spindle speed, feed rate, and depth of cut, to minimize noise while maintaining cutting efficiency and quality.
- Balance and Alignment: Regularly check and adjust the balance and alignment of spindle motors, cutting tools, and motion system components to minimize vibrations and noise.
Operator Awareness and Protection
Lastly, fostering operator awareness and providing appropriate personal protective equipment (PPE) can help mitigate the impact of CNC router noise on human health and safety:
- Training: Provide comprehensive training to operators on the risks associated with noise exposure and the importance of using hearing protection.
- Hearing Protection: Supply operators with suitable hearing protection devices, such as earplugs or earmuffs, to reduce their exposure to high noise levels during CNC router operation.
- Noise Monitoring: Implement noise monitoring programs to assess and track noise levels in the workspace, ensuring compliance with occupational health and safety regulations.
Summarize
By implementing the strategies outlined in this guide, you can effectively block the noise of your CNC router and create a quieter, more comfortable working environment. It’s important to recognize that noise reduction is an ongoing process that may require experimentation, refinement, and continuous monitoring. Through proactive measures and collaborative efforts, we can operate efficiently without compromising the comfort and safety of those who operate them.
At AccTek CNC, we produce many types of CNC routers to meet the needs of various industries, including woodworking, signage, metalworking, and more. In addition to providing high-quality machines, we understand the importance of ongoing technical support to ensure optimal performance and customer satisfaction. Our team of experienced technicians is dedicated to offering comprehensive technical assistance, troubleshooting, and guidance every step of the way. Whether you’re a seasoned professional or new to CNC machining, we’re here to support you in achieving your manufacturing goals.