- 12-17 Min Read
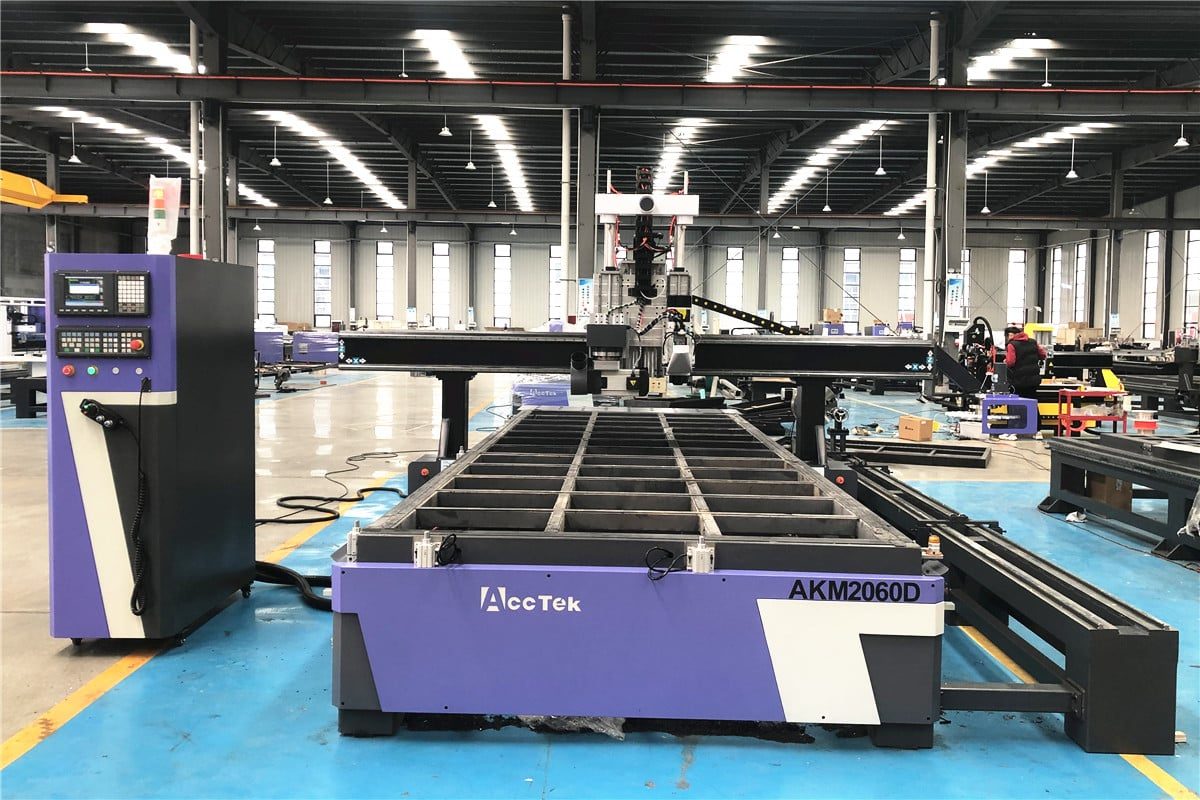
In the world of computer numerical control (CNC) routers, precision and efficiency reign supreme. These machines, with their ability to precisely cut, carve, and shape various materials, every component play a pivotal role in determining the quality of the final output. Among these components, the frame of the CNC router stands as the backbone, dictating its overall stability and accuracy. However, one often overlooked aspect of the CNC router’s frame is its rigidity—a factor that significantly influences its performance.
So, how exactly does the rigidity of the CNC router frame affect its performance? To answer this question comprehensively, we delve into the significance of frame rigidity in CNC routers, exploring how it influences various aspects of performance and why it should be a primary consideration when selecting or designing a machine. From minimizing vibration-induced errors to maximizing cutting speeds, we unravel the implications of frame rigidity on CNC router functionality and the tangible benefits it brings to the table. At the end of the article, we provide you with precautions for maintaining the CNC router frame. By practicing this guide, you can maintain the performance of the machine frame to the maximum extent.
The Importance of Frame Rigidity in CNC Routing
CNC router rigidity refers to the ability of a CNC (Computer Numerical Control) router’s frame and components to maintain their structural integrity and resist deformation or flexing during machining operations. It’s a crucial aspect of CNC routing as it directly influences the precision, accuracy, and quality of the machined parts. A more rigid frame typically translates to better cutting results, reduced vibrations, and increased longevity of the machine. The importance of frame rigidity in CNC routing is reflected in several key aspects:
- Accuracy: A rigid frame minimizes flexing and distortion during cutting operations, ensuring that the tool follows the programmed path accurately. Any deviation in the frame’s geometry can result in inaccuracies in the final workpiece dimensions and shape.
- Surface Finish: A stable frame reduces vibrations transmitted to the cutting tool, leading to smoother cuts and improved surface finish on the workpiece. Vibrations caused by inadequate frame rigidity can manifest as visible marks or imperfections on the routed surface.
- Cutting Quality: Frame rigidity directly affects the quality of cuts, particularly when machining materials that require high precision, such as metals or hardwoods. A rigid frame enables the CNC router to maintain consistent cutting forces, resulting in cleaner edges and tighter tolerances.
- Tool Life: Excessive vibrations due to a lack of frame rigidity can accelerate tool wear and compromise cutting tool life. A stable frame minimizes tool deflection and chatter, prolonging the lifespan of cutting tools and reducing the frequency of tool replacements.
- Productivity and Efficiency: With a rigid frame, CNC routers can operate at higher speeds and feeds without sacrificing cutting quality. This increased efficiency translates to shorter machining times, higher throughput, and ultimately, improved productivity for the operator or manufacturer.
- Machining of Hard Materials: When machining hard materials like metals or composites, maintaining rigidity is beneficial to prevent tool deflection and ensure precise cuts. A rigid frame provides the necessary support for the cutting tool to penetrate the material effectively without compromising dimensional accuracy.
- Long-Term Reliability: A well-built, rigid frame contributes to the overall durability and reliability of the CNC router. Machines with inadequate frame rigidity may experience premature wear and mechanical failures, leading to costly repairs and downtime.
In essence, frame rigidity is fundamental to achieving consistent, high-quality results in CNC routing across various materials and applications. It underpins the machine’s performance, reliability, and ability to meet the demands of modern manufacturing and fabrication processes.
The Role of Rigidity in CNC Router Performance
The role of rigidity in CNC router performance encompasses a wide array of critical factors that directly influence the machining process. It directly impacts machining tolerances, surface quality, tool longevity, and overall efficiency, making it a critical consideration in the design and operation of CNC routing systems. Here’s a breakdown of how rigidity affects CNC router performance in various aspects:
Precision and Accuracy
- Machining Tolerances: A rigid frame ensures stability during cutting operations, minimizing deflection and maintaining the intended dimensions and geometries specified in the machining program. By providing a solid foundation, rigidity helps achieve tighter tolerances and ensures the accuracy of the finished workpieces.
- Reduction of Vibration and Deformation: A rigidity frame plays a key role in reducing vibration and structural deformation during machining. When subjected to cutting forces, a rigid frame remains stable, preventing unwanted oscillations and ensuring that the tool follows the programmed toolpath accurately. By minimizing vibration and deformation, rigidity helps eliminate deviations from the desired machining outcomes and enhances the overall quality of the machined parts.
Surface Finish
- Reducing Tool Chatter and Vibration Traces: A rigid frame provides a stable foundation, effectively dampening tool vibrations and mitigating chatter. By reducing chatter and vibration traces, rigidity ensures that the cutting tool follows a smooth and consistent path, resulting in eliminating undesirable marks or surface imperfections on the workpiece.
- Improving Surface Smoothness: The stability afforded by rigidity translates directly into the quality of the machined surface. A rigid frame minimizes vibrations, resulting in smoother cuts and finer surface finishes. By promoting stability and precision, rigidity contributes to achieving the desired surface smoothness, enhancing the aesthetics and functionality of the machined parts.
Tool Life
- Reducing Cutting Tool Wear: A rigid frame effectively dampens vibrations and maintains precise tool positioning, reducing the likelihood of tool deflection and ensuring that the cutting tool maintains its intended path and engagement with the workpiece. By minimizing cutting tool wear, rigidity contributes to cost savings by reducing the frequency of tool replacements and enhancing overall machining efficiency.
- Consistent Cutting Force and Tool Engagement: A rigid frame enables the CNC router to apply consistent cutting forces and maintain optimal tool engagement throughout the machining process, resulting in uniform material removal and improved machining efficiency.
Effects on High-Speed Machining
- Rigidity is particularly crucial for high-speed machining operations, where dynamic forces are more pronounced. A rigid frame allows the CNC router to operate at higher speeds with greater stability, maximizing productivity without compromising cutting quality.
Workpiece Support
- Rigidity directly influences the ability of a CNC router to provide robust support for the workpiece during machining. A rigid frame ensures that the workpiece remains securely positioned and stable throughout the cutting process, preventing unwanted vibrations or deflections that could compromise machining accuracy. Additionally, effective workpiece support facilitates consistent material removal and prevents errors such as chatter or surface irregularities. Whether machining large components or delicate parts, a CNC router with adequate rigidity can deliver superior results by maintaining precise workpiece alignment and minimizing the risk of dimensional inaccuracies.
Factors Affecting Frame Rigidity
Several factors contribute to the rigidity of a CNC router frame, each playing a role in determining the overall stability and performance of the machine. By addressing potential sources of flex or instability, manufacturers can ensure that the CNC router delivers consistent and precise performance in various machining applications. Some of the key factors include:
- Material Selection: The material from which the frame is constructed plays a pivotal role in determining its rigidity. Common materials for CNC router frames include aluminum, steel, cast iron, and composite materials like granite or epoxy granite. Each material possesses unique stiffness properties, with steel and cast iron often favored for their superior rigidity compared to aluminum or composites. The selection of frame material must consider factors such as weight, cost, and the specific requirements of the machining application.
- Frame Design: The structural design of the frame significantly influences its rigidity and performance. Various frame configurations, such as welded steel tubing, box-sections, or truss structures, offer different levels of stiffness and stability. Additionally, features like ribbing, gussets, and cross-bracing can be incorporated into the design to enhance rigidity and minimize deflection under load. The optimized frame geometry, including dimensions and shapes, further contributes to overall stiffness and ensures efficient load distribution.
- Frame Geometry: The geometry of the frame, including its dimensions and shape, affects its rigidity. Frames with larger cross-sectional areas and shorter spans tend to be stiffer than those with smaller dimensions or longer spans. Moreover, frames with geometrically optimized shapes can distribute loads more efficiently, reducing stress concentrations and improving overall rigidity.
- Welding Technology: The welding technology employed in fabricating the CNC router frame directly impacts its rigidity and structural integrity. High-quality welding techniques, such as TIG (Tungsten Inert Gas) welding or MIG (Metal Inert Gas) welding, ensure strong and durable connections between frame components. Proper welding practices, including pre-weld preparation, joint fit-up, and welding parameters, are beneficial for achieving consistent weld quality and minimizing distortion. By employing advanced welding technologies and skilled craftsmanship, manufacturers can produce CNC router frames with superior rigidity and stability, ensuring optimal performance in demanding machining environments.
- Base Material: The surface on which the CNC router frame is mounted also influences its rigidity. A sturdy and level base, such as a concrete foundation or heavy-duty workstation, provides better support and stability, reducing the risk of frame deflection or vibration.
- Machine Components and Accessories: The addition of components such as linear guides, ball screws, motors, and tool holders can affect the overall rigidity of the CNC router system. Mounting these components securely and aligning them properly with the frame minimizes any potential sources of flex or misalignment.
- Environmental Factors: Environmental conditions such as temperature fluctuations, humidity, and exposure to vibrations can affect frame rigidity over time. Proper maintenance and storage practices can help mitigate the impact of these factors and preserve the structural integrity of the CNC router frame.
Frame Stiffness and Dynamic Loads
Dynamic loads in the context of CNC routing refer to the varying forces and stresses exerted on the machine frame during machining operations. These loads are dynamic in nature, meaning they fluctuate over time as the CNC router moves, accelerates, decelerates, and engages with the workpiece. By providing robust support and resistance to deformation, frame stiffness ensures that the CNC router responds accurately to dynamic load changes, preserving machining precision and preventing dimensional errors in the workpiece. The following are the sources of dynamic loads and the role of machine rigidity in the CNC routing process.
- Acceleration and Deceleration: When the CNC router accelerates or decelerates, dynamic loads are generated due to changes in velocity. These dynamic loads can induce inertial forces that stress the machine frame, particularly during rapid movements or changes in cutting direction. A stiff frame resists deformation and maintains stability, ensuring that the machine responds promptly to changes in velocity without introducing inaccuracies in tool positioning or workpiece dimensions.
- Cutting Forces: Cutting forces exerted by the tool as it interacts with the workpiece also contribute to dynamic loads. These forces vary depending on factors such as cutting depth, feed rate, material properties, and tool geometry. Dynamic loads from cutting forces can cause the machine frame to flex or deflect, affecting machining accuracy and surface finish. A rigid frame effectively absorbs and distributes these forces, minimizing deflection and ensuring that the tool maintains its intended path. By providing a stable cutting environment, frame stiffness enhances cutting accuracy and prevents dimensional errors in the machined parts.
- Directional Changes: Dynamic loads are also encountered when the CNC router changes direction during machining operations. Rapid changes in cutting direction can induce sudden changes in load distribution across the machine frame, leading to transient dynamic responses and potential instability. A rigid frame maintains structural integrity under fluctuating loads, ensuring consistent machining performance and minimizing the risk of dimensional inaccuracies or workpiece distortion.
- Tool Vibrations and Chatter: Vibrations and tool chatter during cutting introduce additional dynamic loads on the machine frame. Tool vibrations can arise from factors such as improper tool geometry, inadequate tool rigidity, or improper machining parameters. These dynamic loads can adversely affect machining precision, surface finish, and tool life if not properly managed. A stiff frame acts as a dampening mechanism, attenuating these vibrations and reducing their impact on machining quality. By suppressing tool vibrations, frame stiffness enhances surface finish and edge quality, resulting in smoother cuts and finer detail on the machined parts.
Frame stiffness plays a key role in mitigating dynamic forces encountered during CNC routing operations. A stiff frame effectively distributes dynamic loads, minimizing deflection and maintaining stability throughout the machining process. By providing stability, resistance to deformation, and vibration damping capabilities, a stiff frame ensures consistent machining accuracy, surface finish, and part quality, enabling the CNC router to deliver reliable performance across a wide range of cutting tasks and operating conditions.
Precautions for Maintaining Frame
In the world of CNC routing, the robustness of the machine’s frame stands as a fundamental pillar for achieving precision and longevity in machining operations. However, ensuring the continuous integrity of the CNC router frame demands vigilant maintenance practices and proactive measures. Here are some precautions and best practices for maintaining the CNC router framework:
- Regular Inspection: Regularly inspect the CNC router frame for any indications of deformation, such as cracks, bends, or misalignments. Inspect welds, joints, and structural components for cracks, deformation, or corrosion. Pay close attention to critical areas where stress concentrations are likely to occur, such as connection points and load-bearing components. Early detection of deformations allows for timely interventions to prevent structural compromises and maintain machining accuracy.
- Alignment: Verify the alignment of the CNC router frame and components, including linear guides, spindle, and tool holder. Misalignment can result in poor machining accuracy, surface finish, and premature wear of cutting tools. Adjust or realign components as needed to maintain proper geometry and alignment.
- Keep it Clean: Regularly clean the CNC router frame to remove dust, debris, and buildup that can accumulate during machining operations. Use compressed air or vacuum cleaners to clean hard-to-reach areas. Keeping the frame clean helps prevent contamination and ensures smooth operation of moving parts.
- Tighten Fasteners: Periodically check and tighten bolts, nuts, screws, and other fasteners used to secure the frame and components. Vibrations from machining operations can cause fasteners to loosen over time, leading to misalignment or structural instability. Use torque wrenches to ensure proper tightening torque according to specifications.
- Avoid Overloading: Avoid overloading the CNC router frame beyond its rated capacity. Excessive loads can stress the frame, lead to deformation, and compromise machining precision. Follow manufacturer recommendations for maximum load limits and cutting parameters.
- Environmental Considerations: Maintain stable environmental conditions in the CNC router workspace, including temperature and humidity levels. Extreme temperatures or fluctuations can affect the dimensional stability of the frame and components, leading to inaccuracies in machining. Use climate control systems or enclosures to regulate environmental conditions as needed.
- Frame Reinforcement and Modification: Consider reinforcing the CNC router frame with additional bracing, gussets, or support structures to enhance its rigidity and resistance to dynamic forces. Reinforcement measures can be tailored to address specific areas of weakness identified during routine inspections. Reinforcing vulnerable sections of the frame mitigates the risk of deformation and ensures stable machining performance under varying load conditions.
- Strengthening Rigidity Modification: Implement modifications aimed at strengthening the rigidity of the CNC router frame to withstand high-speed machining and heavy cutting applications. This may involve upgrading frame materials, optimizing structural geometry, or integrating advanced damping technologies. Strengthening rigidity modifications improve the machine’s ability to maintain dimensional accuracy, minimize vibration-induced errors, and achieve superior surface finishes.
By following these precautions and maintenance practices, CNC router operators can maximize the performance, reliability, and lifespan of the machine framework, ultimately optimizing machining efficiency and quality. Regular maintenance helps prevent costly downtime, repairs, and ensures consistent performance over time.
Summarize
The rigidity of the CNC router frame stands as a cornerstone in determining the overall performance and efficacy of the machining process. As explored in this article, frame rigidity directly influences precision, accuracy, surface finish, tool life, and the ability to handle diverse machining tasks. From maintaining tight tolerances to enhancing surface finishes, frame rigidity plays a pivotal role in meeting the exacting demands of modern manufacturing. In high-speed and heavy-duty machining applications, rigid frames become indispensable, allowing manufacturers to turn their visions into reality with unparalleled precision and efficiency.
AccTek CNC routers are designed and built with a focus on robust frame construction to meet the demanding requirements of modern manufacturing. With our robust frame construction and rigorous quality control measures, AccTek CNC routers deliver unmatched reliability and performance, making them ideal for a wide range of machining applications. Experience the difference that superior frame rigidity can make in your CNC routing operations with AccTek CNC. Choose reliability, choose performance, and choose AccTek CNC for your machining needs.