- 12-17 Min Read
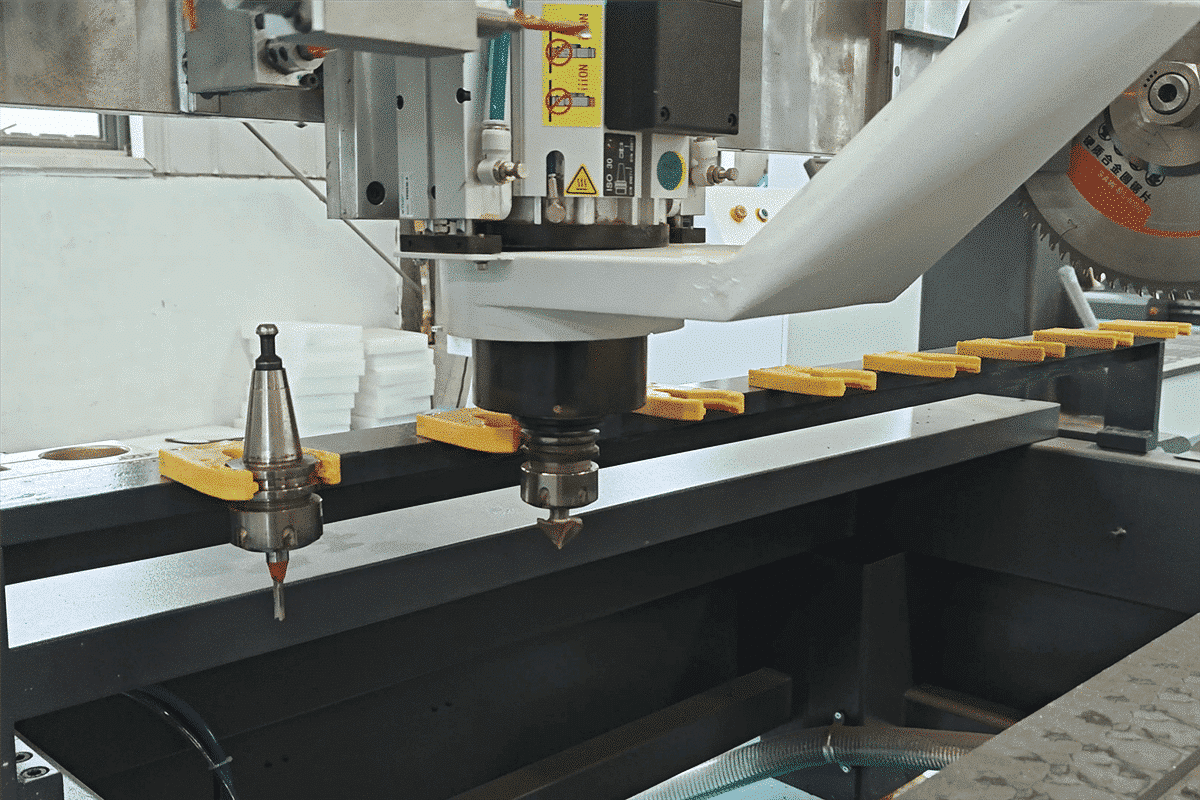
An Automatic Tool Changer (ATC) CNC router is a game-changer in precision machining, designed to perform intricate tasks efficiently and seamlessly. Unlike conventional CNC routers that require manual intervention to change tools, an ATC CNC router comes equipped with an automated tool-changing system. This feature eliminates downtime between tool changes, boosts productivity, and enables seamless multi-step operations, making ATC CNC routers a cornerstone of advanced manufacturing.
At its core, an ATC CNC router works by integrating a spindle, a tool magazine, and a tool-changing mechanism that communicates with the machine’s control system. They come with different types of tool-changing systems, each suited to specific tasks and operational demands. Selecting the right ATC system requires considering factors such as initial investment, maintenance and tool change time. In this article, we will delve into the core principles of ATC CNC routers, their different types, and explore its applications and benefits in modern manufacturing.
The basic principles of CNC routing
The basic principles of CNC routing serve as the foundation for modern automated manufacturing processes. Understanding its fundamental principles highlights how this transformative technology drives innovation and productivity, shaping the future of modern manufacturing. Here are its details:
Operation Overview
CNC routing is a transformative manufacturing process that automates the precise cutting, shaping, and engraving of various materials using computer-driven commands. From an operational standpoint, CNC routers follow pre-programmed paths to execute intricate designs and repeatable tasks with remarkable accuracy. This automated process involves inputting a digital design into specialized software, which then generates a set of precise instructions (known as G-code) that guides the machine’s movements. The CNC router’s spindle, guided by stepper or servo motors, maneuvers the cutting tool along multiple axes, enabling the creation of complex parts with minimal human intervention.
Tools in CNC Routing
Tools are the defining elements in CNC routing, enabling the transformation of raw materials into precise, high-quality components and products. The choice and performance of these tools dictate the range of tasks a CNC router can perform and the quality of the finished work. Here are the common tool types used in CNC routing:
- End Mills: End mills are versatile cutting tools used for creating smooth edges, precise contours, and intricate shapes. Available in flat, ball-nose, and specialty profiles, they are suitable for machining both ferrous and non-ferrous materials.
- Straight Router Bits: These bits are used for general-purpose cutting and shaping of materials, making straight cuts and grooves.
- Ball Nose Bits: These tools are designed for creating contoured or rounded surfaces. They are often used in applications that require smooth 3D cuts and sculpted surfaces.
- V-Bits: Ideal for engraving, beveling edges, and creating intricate details, V-bits produce sharp, clean cuts with angular shapes, making them popular for decorative work.
- Drilling Tools: CNC routers use a variety of drilling bits to create holes of different diameters and depths. These tools are precision-oriented and capable of boring holes in materials like wood, metal, and plastic.
From cutting and drilling to engraving and shaping, the proper selection and use of these tools enable CNC routers to deliver consistent, intricate, and high-quality work across a wide range of applications and industries. To learn how to choose the right CNC router tools, read “CNC Router Bits: Complete Buyer’s Guide.”
Automatic Tool Changer (ATC) System Introduction
An Automatic Tool Changing (ATC) system is a critical feature in modern CNC routers, designed to automate the process of switching between different cutting, milling, or drilling tools during a machining operation. The primary purpose of an ATC system is to enhance productivity by minimizing downtime and eliminating the need for manual tool changes. This results in faster production cycles, greater precision, and improved operational efficiency, enabling manufacturers to perform complex, multi-tool operations seamlessly. ATC systems are widely used in applications where different tools are needed in quick succession, making them essential in industries like woodworking, metal fabrication, plastics, and more.
Working Principle of the ATC System
- Tool Selection: The ATC system operates based on instructions programmed into the CNC router’s control system. When a specific machining task requires a change of tools, the control system sends a signal to the ATC mechanism to retrieve the required tool from the tool magazine. The tool selection process is determined by pre-programmed commands that dictate the tool’s order, position in the magazine, and specific function.
- Tool Changing Process: The tool-changing process involves several steps that are carried out with precision and speed. First, the spindle releases the currently used tool and returns it to its designated slot in the tool magazine. Next, the ATC mechanism retrieves the new tool from the magazine and secures it into the spindle. This process can be completed in seconds, ensuring that the CNC router resumes its operation with minimal interruption. By automating these steps, the ATC system eliminates manual intervention, reduces errors, and significantly enhances the speed of multi-tool machining processes.
Key Components of the ATC CNC Router
- Tool Magazine: The tool magazine serves as the storage unit for all the tools required during a machining operation. It can come in different configurations, such as linear magazines or disk magazines, depending on the machine’s design and operational needs. The magazine’s capacity and design affect the flexibility and number of tools available for switching, making it a critical component of the ATC system.
- Tool Changing Device: The tool-changing device is responsible for physically swapping the tools between the spindle and the magazine. It typically consists of mechanical arms, grippers, or robotic mechanisms that engage and release tools with precision. The speed and accuracy of this component are key to maintaining productivity and ensuring accurate tool placement.
- Control System: The control system acts as the “brain” of the ATC CNC router, managing the tool-changing process based on the programmed instructions. It coordinates all movements of the spindle, tool-changing device, and tool magazine, ensuring that each tool change is executed smoothly and accurately. Advanced control systems allow for seamless integration of the ATC system with the CNC router’s overall operations, optimizing tool paths, reducing cycle times, and minimizing human intervention.
Together, these aspects make the ATC system a powerful and efficient tool in modern CNC routing, transforming the way complex machining operations are performed and contributing to increased productivity, precision, and adaptability in manufacturing processes.
Advantages of ATC CNC Routers
The advantages of an Automatic Tool Changer (ATC) CNC router make it a powerful tool for modern manufacturing processes. By automating the tool-changing process, these machines enhance productivity, ensure precision, and offer unmatched versatility in machining operations. Here are the main benefits of ATC CNC routers, highlighting their role in streamlining production and delivering high-quality results.
Increased Productivity
One of the most significant advantages of an Automatic Tool Changer (ATC) CNC router is the substantial boost in productivity it offers. Traditional CNC routers require operators to manually switch tools during a machining process, resulting in downtime and potential delays. In contrast, an ATC system automates this process, seamlessly changing tools within seconds as needed for various machining operations.
This automation minimizes idle time and allows for continuous, uninterrupted production, thereby increasing throughput. As a result, complex multi-step tasks can be completed more quickly and efficiently, reducing overall production time and enabling manufacturers to meet tight deadlines and handle higher production volumes without sacrificing quality. The increased productivity is beneficial for businesses focused on high-volume manufacturing or those requiring fast turnarounds.
Precision and Accuracy
The automation and precision of ATC CNC routers contribute to improved accuracy in machining operations. Manually changing tools introduces a risk of human error, such as incorrect tool placement or improper calibration, which can lead to deviations and inconsistencies in the final product. An ATC system eliminates this variability by ensuring that each tool change is performed with exact alignment and positioning according to the programmed instructions. This results in consistently accurate cuts, shapes, and details, even for complex and intricate designs.
Additionally, the ATC system’s ability to execute precise tool transitions reduces potential misalignments and defects, delivering superior quality and uniformity across all manufactured parts. This level of precision and repeatability is a key capability for industries where even small deviations can lead to subpar results or rejected parts.
Tool Versatility
ATC CNC routers offer unparalleled versatility by allowing for the use of multiple tools within a single machining cycle. In a typical production scenario, different tools may be required for various stages of a project, such as cutting, drilling, engraving, and shaping. The ATC system facilitates seamless transitions between these tools without manual intervention, enabling the completion of complex operations in one setup.
This versatility is ideal for manufacturers working with intricate designs or multi-process tasks, as it allows for rapid adjustments and customizations. Moreover, the system’s capacity to accommodate a wide range of tool types and sizes broadens the scope of applications that can be performed, making ATC CNC routers suitable for diverse industries such as woodworking, metal fabrication, plastics, and more. By offering a flexible and adaptive approach to tool usage, the ATC system optimizes productivity and enables manufacturers to tackle a wider variety of projects with ease.
ATC CNC routers stand out for their ability to boost productivity, maintain precise and accurate machining, and handle diverse tools seamlessly. Their advantages make them essential for industries seeking to optimize operations and produce consistent, high-quality products. By integrating automation and versatility, ATC CNC routers drive efficiency and adaptability in modern manufacturing.
Types of ATC Systems
Several types of Auto Tool Changers (ATCs) are utilized in CNC routers, each with its own design and mechanism for automatically changing cutting tools during the machining process. Among the various types, three common ATC systems are the fixed linear tool changer, disc tool changer, and follow-up linear tool changer. Each system is suited for different applications, offering unique benefits and potential drawbacks.
Disc Auto Tool Changer
The disc tool changer, also known as a carousel tool changer, stores tools in a rotating disc or turret that is often positioned near the spindle. The disc rotates to bring the required tool into position for the spindle to pick up.
Advantages
- Fast Tool Changes: The rotational movement of the disc makes tool changes rapid, significantly improving productivity in high-volume or complex machining tasks.
- Compact Design: The circular configuration allows for more tools to be stored in a smaller space compared to linear arrangements, making it efficient for machines with limited space.
- Greater Tool Capacity: Disc tool changers typically hold more tools, making them suitable for operations requiring diverse tool sets.
Disadvantages
- Complexity and Maintenance: The rotating disc mechanism involves moving parts, making the system relatively complex. This complexity may result in higher maintenance requirements compared to simpler tool-changing systems.
- Initial Cost: CNC routers equipped with disc ATCs may have a higher initial cost compared to machines with simpler tool-changing systems.
Fixed Linear Auto Tool Changer
The fixed linear tool changer is another type of tool changing mechanism used in CNC routers. Unlike the Disc ATC, the Linear ATC features a linear arrangement of tools in a magazine. The tool magazine is typically a linear rack or tray that holds multiple tool holders in a row. Tools are stored in a fixed row, and the machine’s spindle moves to the designated tool position during a tool change.
Advantages
- Simplicity and Low Cost: This system is relatively simple in design, making it cost-effective compared to more complex ATC systems.
- Reliability: With fewer moving parts, fixed linear tool changers are generally more reliable and require less maintenance.
Disadvantages
- Slower Tool Changes: Since the spindle must move to the fixed rack, tool changes can take longer, potentially reducing overall productivity in high-volume operations.
- Space Requirements: The linear tool magazine requires more horizontal space within the CNC router.
Follow-Up Linear Auto Tool Changer
Similar to a fixed linear ATC, the follow-up linear ATC has a linear tool magazine where cutting tools are arranged in a row. Tools are secured in individual holders within the magazine. The difference is that the follow-up linear ATC has a unique design, and the tool magazine is mounted on a rigid frame attached to the CNC router. During the machining process, the entire tool magazine moves along with the spindle.
Advantages
- Faster Tool Changes: By keeping the tool rack closer to the spindle, the follow-up linear tool changer reduces the time it takes to switch tools compared to a fixed linear system.
Disadvantages
- Increased Mechanical Complexity: The movement of the tool rack introduces additional mechanical elements, potentially leading to increased maintenance compared to a completely fixed system.
Each of these ATC systems offers distinct advantages and disadvantages. The choice of system depends on specific operational needs, including tool capacity, speed of tool changes, budget considerations, and the complexity of machining tasks. Understanding these factors can help businesses select the best ATC system to optimize productivity and efficiency.
Considerations and Challenges in Selecting an ATC System
When selecting an Automatic Tool Changing (ATC) system for a CNC router, several important considerations and challenges must be taken into account to ensure optimal performance and efficiency. The right ATC system can significantly enhance productivity, reduce manual intervention, and enable seamless multi-tool operations, but the choice requires careful evaluation of key factors and potential obstacles.
Initial Investment
The initial cost of acquiring an Automatic Tool Changing (ATC) system can vary significantly based on the type, complexity, and capacity of the system. Fixed linear ATC systems tend to have lower upfront costs, while more advanced options such as disc or carousel systems are generally more expensive due to their increased capacity and faster tool-change capabilities.
The challenge lies in balancing cost and performance. While a higher initial investment in a sophisticated ATC system may lead to long-term productivity gains and efficiency improvements, it may not be feasible for small businesses or those with limited budgets. Decision-makers must carefully assess whether the potential return on investment (ROI) justifies the added expense and whether the chosen system aligns with their specific production needs.
Maintenance and Calibration
ATC systems require regular maintenance and calibration to ensure they function properly and maintain high levels of accuracy. Complex systems with numerous moving parts, such as disc changers, may need more frequent maintenance, while simpler linear systems often have fewer components and therefore may be easier to maintain.
High-maintenance systems can lead to increased downtime, repair costs, and potential disruptions to production schedules. Additionally, proper calibration is beneficial for maintaining precision during tool changes. Any misalignment can result in machining errors, tool damage, or quality issues. Businesses must weigh the complexity of maintenance and calibration against the performance gains offered by more sophisticated systems and ensure they have the expertise and resources required for ongoing care.
Tool Change Time
The speed at which an ATC system can change tools is a major factor influencing overall productivity. Faster tool changes improve productivity by minimizing downtime between machining operations. Systems like disc changers typically offer faster tool change times compared to fixed linear systems, which require more movement to access tools.
While faster tool-change times can significantly improve throughput and reduce downtime, they often come with higher costs and increased mechanical complexity. For operations where rapid tool changes are not a critical factor, a simpler system with longer tool-change times may be more cost-effective. However, for high-volume or complex operations, any delay in tool changes can negatively impact production efficiency. Striking the right balance between speed and cost, while considering operational demands, is key to making an informed selection.
Selecting an ATC system for a CNC router involves weighing various considerations. Each choice presents potential challenges that must be carefully evaluated to strike the right balance between productivity, cost, and operational efficiency. By addressing these considerations and challenges, businesses can ensure they select an ATC system that meets their unique requirements and optimizes their manufacturing processes.
Applications and industries using ATC CNC router
Automatic Tool Changer (ATC) CNC routers have transformed modern manufacturing and crafting by providing seamless, automated tool changes that enhance precision, productivity, and versatility. As a result, ATC CNC routers are utilized across a broad range of applications and industries. Here are some key areas where these machines are making a significant impact:
Woodworking
ATC CNC routers have revolutionized the woodworking industry by automating and streamlining complex cutting, carving, engraving, and shaping processes. Here are some key applications of ATC CNC routers in woodworking:
- Furniture Production: ATC CNC routers are widely used in crafting various types of furniture, such as tables, chairs, cabinets, and custom-designed pieces. The ability to seamlessly switch between cutting, drilling, carving, and finishing tools allows for the rapid production of components with intricate designs, precise joinery, and consistent quality.
- Decorative Panels and Engravings: Woodworking projects often involve intricate decorative work, such as engraved panels, detailed patterns, and artistic carvings. Automated tool changes ensure seamless transitions between various cutting, shaping, and decorative processes, improving production speed and quality.
- Custom Wood Projects: ATC CNC routers empower woodworkers to create bespoke and highly detailed wood products, such as intricate inlays, artistic sculptures, and custom-built furniture pieces. The flexibility of these CNC routers enables designers and artisans to experiment with unique shapes, patterns, and textures.
Metal Processing
ATC CNC routers play a pivotal role in the metal processing industry by automating complex machining operations and providing precise, efficient, and versatile solutions. Here are some key applications of ATC CNC routers in metal processing:
- Milling and Drilling Operations: ATC CNC routers can mill and drill holes in metal quickly and accurately. This capability makes it ideal for creating metal molds, fixtures, and mechanical components.
- Engraving and Marking: ATC CNC routers equipped with engraving tools can achieve intricate, high-precision engravings on metals like steel, aluminum, brass, and more. This application is widely used in the production of nameplates, custom metalwork, and branded components.
- Die Making: ATC CNC routers are often used in die-making. The ability to automatically change between cutting, shaping, and finishing tools ensures the creation of accurate, durable, and complex dies and molds for manufacturing processes.
Plastic Manufacturing
Plastic materials often require specific machining processes to achieve clean cuts, intricate shapes, and smooth finishes, and ATC CNC routers meet these demands through automated tool changes. Here are some of the key applications of ATC CNC routers in plastic manufacturing:
- Cutting and Profiling Plastic Sheets: ATC CNC routers are frequently used to cut and profile plastic sheets into various shapes and sizes. This includes creating panels, custom parts, and intricate designs from materials such as acrylic, polycarbonate, PVC, and polyethylene.
- Engraving and Etching: Plastic products frequently require detailed engravings and markings, such as branding, serial numbers, or decorative elements. ATC CNC routers equipped with engraving tools can achieve intricate designs with high precision, providing clean, detailed results on plastic surfaces.
- Fabrication of Plastic Displays and Fixtures: ATC CNC routers are used to create high-quality displays, fixtures, and point-of-sale elements from plastic materials. The machine’s precision and ability to perform intricate cuts and detailed engravings make it possible to produce eye-catching, durable displays for trade shows.
The ATC CNC router’s ability to automate tool changes and execute complex machining operations with speed and precision makes them indispensable for high-efficiency, high-quality production. As technology continues to advance, the applications of ATC CNC routers are expected to expand even further, driving innovation and productivity across various sectors.
Summarize
ATC CNC router streamlines the machining process by automating tool changes, enhancing productivity and precision in complex operations. With its seamless integration of tool magazines, changing mechanisms, and control systems, it reduces downtime and improves accuracy, making it indispensable for diverse manufacturing applications. ATC CNC routers continue to drive innovation, providing manufacturers with the flexibility and precision they need to meet changing production demands. Continuing reading “A Guide to Selecting the Right ATC CNC Router for Your Needs” will provide you with insights to make the right decision.
AccTek CNC is a well-known CNC router manufacturer in China, recognized for its high-quality and reliable CNC solutions, including advanced Automatic Tool Changer (ATC) systems. With a focus on delivering exceptional precision, productivity, and versatility, AccTek’s ATC CNC routers automate complex tool changes, significantly reducing downtime and enhancing operational efficiency. For businesses seeking to optimize their production capabilities and achieve superior outcomes, AccTek CNC is the go-to partner, offering customized services, training support, and technical consulting.