- 10-15 Min Read
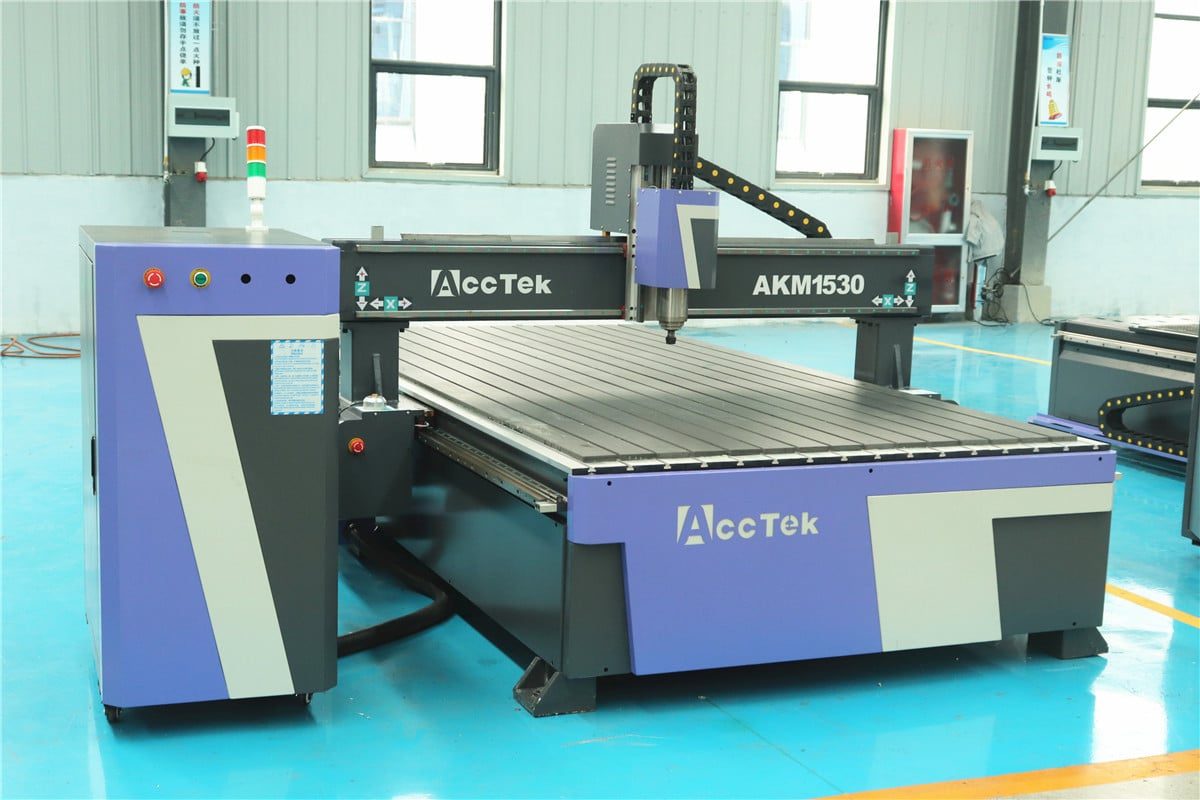
Securing wood on a CNC router is a fundamental aspect of woodworking that ensures precision, stability, and safety during the machining process. While vacuum hold-down systems are widely regarded for their efficiency and effectiveness, they are not always accessible or necessary for every workshop. Whether due to budget constraints, specific project requirements, or the nature of the workpiece, there are numerous scenarios where alternative fixing methods are required. This article aims to explore the various techniques and tools available to fix wood on a CNC router without relying on a vacuum system, offering practical solutions for woodworkers of all levels.
From traditional mechanical clamps to innovative jig designs, there are multiple ways to achieve a secure hold on your workpiece. Each offers unique advantages depending on the type of material and the complexity of the task. By understanding and utilizing these alternative methods, woodworkers can enhance their CNC routing projects’ accuracy and efficiency, ensuring that every cut is precise and every piece remains securely in place throughout the machining process.
Importance of Workpiece Fixtures
The importance of workpiece fixtures in CNC routing cannot be overstated. Effective fixtures ensure that the wood remains stationary, allowing the CNC router to perform intricate and precise operations with consistent results. Here is a detailed introduction to the importance of workpiece fixtures:
Stability and Accuracy
- Consistent Positioning: CNC router workpiece fixtures ensure that the material remains in a fixed position throughout the machining process. This stability is beneficiall for maintaining precision and achieving the desired dimensions and shapes.
- Vibration Reduction: Proper fixtures minimize vibrations that can occur during cutting. Reduced vibrations lead to smoother finishes and more accurate cuts, enhancing the overall quality of the workpiece.
- Repeatability: High-quality fixtures allow for consistent repeatability in production. Each workpiece can be positioned in exactly the same way, ensuring uniformity across multiple pieces and reducing the chances of errors.
Efficiency and Productivity
- Faster Setup Times: Using fixtures designed for specific tasks can significantly reduce setup times. Operators can quickly and easily secure workpieces, leading to faster production cycles.
- Enhanced Throughput: Efficient workpiece fixtures streamline the machining process. By holding the material securely, fixtures enable the CNC router to operate at optimal speeds without the risk of displacements or errors, thus increasing throughput.
- Reduced Downtime: Well-designed fixtures decrease the likelihood of workpiece movement or shifting, which can cause interruptions. This reliability minimizes downtime associated with readjustments or rework, thereby boosting overall productivity.
- Complex Machining: Fixtures enable the machining of complex shapes and intricate designs by securely holding the workpiece in the required orientation. This capability expands the range of possible projects and enhances the versatility of the CNC router.
CNC router workpiece fixtures are integral to achieving high stability and accuracy in machining operations. They play a key role in enhancing efficiency and productivity by ensuring precise, repeatable, and stable positioning of the workpiece, ultimately leading to superior quality and increased output.
Common Workpiece Clamping Methods Without Vacuum
Mechanical Clamps
Mechanical clamping involves using various types of clamps to hold the workpiece securely on the CNC router table. This method is versatile and widely used due to its reliability and strength.
- T-Slot Clamps: These fit into T-slots on the CNC router table and can be tightened to hold the workpiece in place. They are adjustable and can accommodate different sizes of workpieces.
- Toggle Clamps: Quick to set up and release, toggle clamps are ideal for repetitive tasks where efficiency is key. They provide strong holding power with minimal setup time.
- Bar Clamps: These are adjustable and can be used to secure larger workpieces. They offer flexibility and strong clamping force.
- Side Clamps: These clamps apply pressure from the sides of the workpiece, allowing the top surface to remain free for machining.
- C-Clamps and G-Clamps: Traditional and effective, these clamps can hold the workpiece from the sides or edges, though they might obstruct some areas of the surface.
Screw Fixing
Screwing the workpiece directly into the CNC router table or into sacrificial boards is a method that provides a very secure hold, though it may leave holes in the material.
- Direct Screwing: This involves driving screws through the workpiece and into the table or an underlying sacrificial layer. It’s highly secure but may require patching or filling holes after machining.
- Hold-Down Clamps with Screws: These clamps are secured to the table with screws, providing a strong and adjustable clamping solution. They are ideal for holding down larger or irregularly shaped workpieces.
Tape and Double-Sided Tape
Using tape, especially double-sided tape, is a simple and effective way to secure lightweight or thin workpieces without the need for mechanical fixtures.
- Double-Sided Tape: Heavy-duty double-sided tape provides a strong bond between the workpiece and the CNC router table. It’s particularly useful for smaller pieces or delicate materials that could be damaged by mechanical clamps.
- Carpet Tape: A type of double-sided tape that offers a strong hold. It’s often used in woodworking for its robust adhesive properties and ease of removal.
Dowel Pins and Alignment Systems
Dowel pins and alignment systems are used to position and hold the workpiece accurately. These methods are excellent for ensuring precise alignment and repeatability in CNC routing operations.
- Dowel Pins: These are inserted into pre-drilled holes in the workpiece and the CNC router table, aligning the piece precisely. They are particularly useful for projects requiring high precision and repeatability.
- Alignment Systems: These systems use a combination of pins, stops, and guides to position the workpiece accurately. They ensure that the workpiece is consistently placed in the same position, which is beneficiall for tasks requiring multiple passes or intricate detail work.
These clamping methods, while distinct in their applications and advantages, collectively contribute to ensuring the stability, accuracy, and efficiency of CNC machining operations. Each method is selected based on the specific requirements of the workpiece and the machining process. By employing these clamping methods, woodworkers can ensure that their workpieces remain stable and secure during CNC routing operations, leading to more precise cuts and higher-quality finished products.
Workpiece Clamping Challenges in Wood Machining
Wood machining, a critical process in woodworking and furniture manufacturing, demands precision, stability, and efficiency. Wood machining presents unique challenges due to the material’s inherent properties. In this section, we explore common workholding challenges in wood machining.
Porosity and Variability
Wood is a porous and variable material, which presents unique challenges for effective clamping. The natural porosity of wood means that it can compress under clamping pressure, leading to potential movement during the machining process. Additionally, the variability in wood density and grain structure can cause inconsistencies in how the material reacts to clamping forces. Different species of wood, moisture content, and inherent defects such as knots can all influence the stability of the workpiece. Ensuring a firm yet gentle hold that accommodates these natural variations without damaging the wood is necessary for precise machining.
Contour Complexity
The complexity of a workpiece’s contour can significantly impact the clamping strategy. Irregular shapes, curved surfaces, and intricate designs require customized clamping solutions that can adapt to the specific geometry of the wood piece. Standard clamping methods may not provide adequate support for non-uniform shapes, leading to potential shifting or vibration during machining. Custom jigs, fixtures, and flexible clamping systems are often necessary to secure complex contours without obstructing the machining area. This complexity requires careful planning and adaptation to ensure the workpiece remains stable throughout the process.
Material Thickness Variation
Wood often varies in thickness, which can complicate the clamping process. Uneven thickness can cause differential clamping pressure, leading to potential warping or movement during machining. Thin sections of the wood are particularly prone to bending or flexing under pressure, which can result in inaccurate cuts and damaged workpieces. Effective clamping must distribute pressure evenly across the entire surface, regardless of thickness variations, to maintain stability and precision. Using sacrificial layers, adjustable clamps, and pressure distribution aids can help manage these variations and ensure a secure hold.
By understanding and addressing these challenges related to porosity and variability, contour complexity, and material thickness variation, woodworkers can optimize their clamping strategies. This, in turn, enhances the stability, precision, and overall quality of their CNC machining operations.
Best Practices for Effective Workholding
Proper material preparation, balanced clamping pressure, and minimizing interference with the cutting path are crucial steps in achieving optimal machining results and high-quality finished products. By adhering to these best practices, wood machinists can enhance the stability, accuracy, and efficiency of their workholding methods.
Proper Material Preparation
- Moisture Content: Ensure the wood is properly dried and acclimated to the workshop environment to prevent movement during machining. Wood with inconsistent moisture content can warp or shift.
- Surface Cleaning: Clean the surface of the workpiece to remove any dust, debris, or residues that could interfere with clamping or machining. A clean surface ensures better adhesion for tape and more effective clamping.
- Flatness and Stability: Check that the workpiece is flat and stable. If necessary, plane or sand the surface to ensure it sits evenly on the CNC router table, reducing the risk of movement.
- Marking and Alignment: Accurately mark the workpiece for alignment with the machine bed or fixture. Proper alignment is beneficiall for maintaining precision and avoiding errors during machining.
Balanced Clamping Pressure
- Even Distribution: Apply clamping pressure evenly across the workpiece to prevent warping or bending. Use multiple clamps if needed to distribute pressure uniformly.
- Padded Clamps: Use clamps with protective pads to distribute pressure and avoid leaving marks or dents on the wood surface.
- Adjustable Clamps: Utilize adjustable clamps like T-slot clamps, toggle clamps, or bar clamps to fine-tune the pressure and ensure a secure hold without over-tightening.
- Test Clamping: Perform a test clamping to check for any movement or slipping. Adjust the clamps as necessary to ensure a secure and stable hold before beginning the machining process.
Minimize Interference with the Cutting Path
- Strategic Clamp Placement: Position clamps away from the cutting path to avoid interference with the CNC router bit. Ensure that the clamps do not obstruct the tool’s movement or the workpiece’s surface that needs machining.
- Custom Jigs and Fixtures: Design custom jigs and fixtures that hold irregularly shaped workpieces securely while keeping the machining area clear. These can be particularly useful for complex or repetitive tasks.
- Repositioning Clamps: For complex cuts that require multiple passes or angles, plan the clamping strategy to allow for repositioning as needed. Ensure that the workpiece remains secure even when clamps are moved or adjusted.
Safety Considerations in Workpiece Clamping
Operator and equipment safety is important during workholding. Proper clamping techniques and practices can help prevent accidents, injuries, and damage to tools and machines. Here are some ways to protect operators and optimize tool life and performance. By adhering to these safety principles, workplaces can achieve enhanced productivity and reduced risk.
Operator Safety
- Secure Workpiece Placement: Ensuring the workpiece is firmly secured is paramount to prevent any unexpected movement during machining. A loose workpiece can become a projectile, posing serious risks to the operator.
- Personal Protective Equipment (PPE): Operators should always wear appropriate PPE, including safety glasses to protect against flying debris, hearing protection to guard against noise, and dust masks to avoid inhaling harmful particles. Avoid loose clothing, jewelry, or anything that could get caught in the machinery.
- Emergency Procedures: Operators should be well-versed in emergency stop procedures and ensure that these controls are easily accessible. Quick action can prevent accidents if the workpiece becomes unstable.
- Workspace Organization: A tidy workspace reduces the risk of tripping and accidental contact with the machine. All tools and materials should be stored properly to ensure a safe working environment. Ensure the work area is well-lit to clearly see the clamping setup and the machining process, reducing the risk of errors and accidents.
- Training and Awareness: Ensure all operators are properly trained in the use of the CNC router and the clamping methods. Operators should understand the risks and be aware of safe practices to minimize hazards.
Tool and Machine Safety
- Clamp Integrity: Regularly inspect clamps and fixtures for wear or damage. Using compromised equipment can lead to failures that may damage the workpiece and the CNC router.
- Balanced Pressure: Even clamping pressure prevents workpiece movement and reduces the strain on the CNC router, ensuring that the machine operates smoothly without unnecessary stress on its components.
- Clear Machining Path: Proper clamp placement avoids collisions with the CNC router bit, which can damage both the tool and the machine. This precaution helps maintain the longevity of the equipment.
- Regular Maintenance: Routine checks and maintenance of the CNC router and its accessories are beneficiall to keep the machine in optimal working condition. This includes ensuring all clamps, bolts, and fixtures are functioning correctly.
- Proper Tool Use: Ensuring that the correct tools and bits are used for the specific material and job can prevent undue stress on the machine, reducing wear and tear and extending the life of the equipment.
- Preventing Overloading: Avoiding excessive clamping pressure not only protects the workpiece but also prevents overloading the machine, which can cause mechanical failures or damage.
By focusing on these safety considerations, operators can ensure a secure and efficient workholding process, minimizing risks to themselves and protecting the tools and machines they work with. This dual approach to safety not only enhances productivity but also fosters a safer working environment.
Troubleshooting and Problem Solving
Effective workpiece clamping is key for achieving precision and quality in machining operations. However, challenges such as workpiece movement and material tearing can arise, disrupting the workflow and compromising the end product. Addressing these issues promptly and effectively helps maintain productivity and ensure high standards. Here we provide practical solutions and best practices to address these challenges.
Resolving Workpiece Movement Issues
The workpiece moves or shifts during machining, leading to inaccurate cuts and potential damage. The solutions are as follows:
- Check Clamp Tightness: Loose clamps are a common cause of workpiece movement. Verify that all clamps are properly tightened. Check and re-tighten clamps periodically during long machining operations to maintain a secure hold.
- Increase Clamping Points: Add more clamps to distribute pressure more evenly and secure the workpiece better. Ensure the clamps are positioned in a way that balances the hold without obstructing the machining area.
- Use Supplemental Methods: Use secondary clamping methods like double-sided tape or screws to supplement the primary clamps for added security. Heavy-duty double-sided tape can provide additional holding power, especially for smaller or lightweight workpieces.
- Enhancing Surface Grip: Use non-slip mats or rubber pads between the workpiece and the machine bed to increase friction and prevent movement. Clean both the workpiece and the clamping surfaces to remove any dust, oil, or debris that might reduce grip.
- Proper Clamp Selection: Choose the right type of clamp for the specific workpiece and operation. Different materials and shapes may require different clamping solutions, such as edge clamps, toggle clamps, or C-clamps. Create custom jigs or fixtures tailored to the specific shape and size of the workpiece to hold it securely.
- Checking Clamp Integrity: Regularly inspect clamps for wear and tear. Damaged or worn-out clamps may not provide adequate holding force.
Dealing with Material Tearout
The workpiece experiences tearout, where wood fibers are pulled out or torn, leading to rough edges and poor surface finish. The solutions are as follows:
- Sharp Cutting Tools: Ensure that CNC router bits are sharp and in good condition. Dull bits can cause tearout by tearing the fibers instead of cutting them cleanly. Regularly inspect and sharpen or replace CNC router bits to maintain optimal cutting performance.
- Appropriate Cutting Parameters: Adjust the feed rate and spindle speed to match the material and bit being used. Too fast a feed rate or too slow a spindle speed can increase the risk of tearout. Make shallower passes to reduce the stress on the wood fibers, resulting in cleaner cuts and less tearout.
- Use Padded Clamps: Apply clamps with protective pads to distribute pressure and prevent direct contact with the wood.
- Employ Sacrificial Layers: Place a thin, sacrificial piece of wood between the clamp and the workpiece to absorb any damage.
- Adjusting Clamping Force: Apply enough pressure to hold the workpiece securely without causing deformation or tearing. Fine-tuning the pressure can help strike a balance between stability and material integrity.
- Grain Direction: Plan cuts to follow the grain direction whenever possible. Cutting against the grain increases the likelihood of tearout. Be aware of changes in grain direction within the workpiece and adjust the cutting approach accordingly.
- Proper Workpiece Support: Ensure the workpiece is securely clamped and fully supported. Any movement or vibration can exacerbate tearout. Apply even clamping pressure to avoid distorting the workpiece, which can lead to uneven cuts and tearout.
By addressing workpiece movement issues and dealing with material tearout through these solutions, machinists can enhance their ability to overcome obstacles, ensuring smooth and precise machining processes. This leads to improved precision, safety, and overall efficiency in the workshop.
Summarize
Securing wood on a CNC router without a vacuum system presents unique challenges, but with the right methods and techniques, it can be effectively achieved. By implementing these strategies in the article, users can optimize their CNC routing operations, ensuring their workpieces remain stable and precise throughout the machining process. Also, if vacuum clamping methods are your best option, see our “What is a Vacuum Worktable: Comprehensive Guide” to learn about them. Or click “Exploring Clamping Methods for CNC Routers” to learn more about workpiece clamping options.
AccTek CNC’s CNC routers offer versatile workholding solutions, including both vacuum adsorption and fixture clamping methods. Whether your project requires the convenience and speed of vacuum hold-down or the precision and stability of mechanical fixtures, we’ve got you covered. Share your specific processing needs with us, and our professional sales team will provide expert advice to help you choose the most effective clamping solution for your CNC routing operations.