- 8-12 Min Read
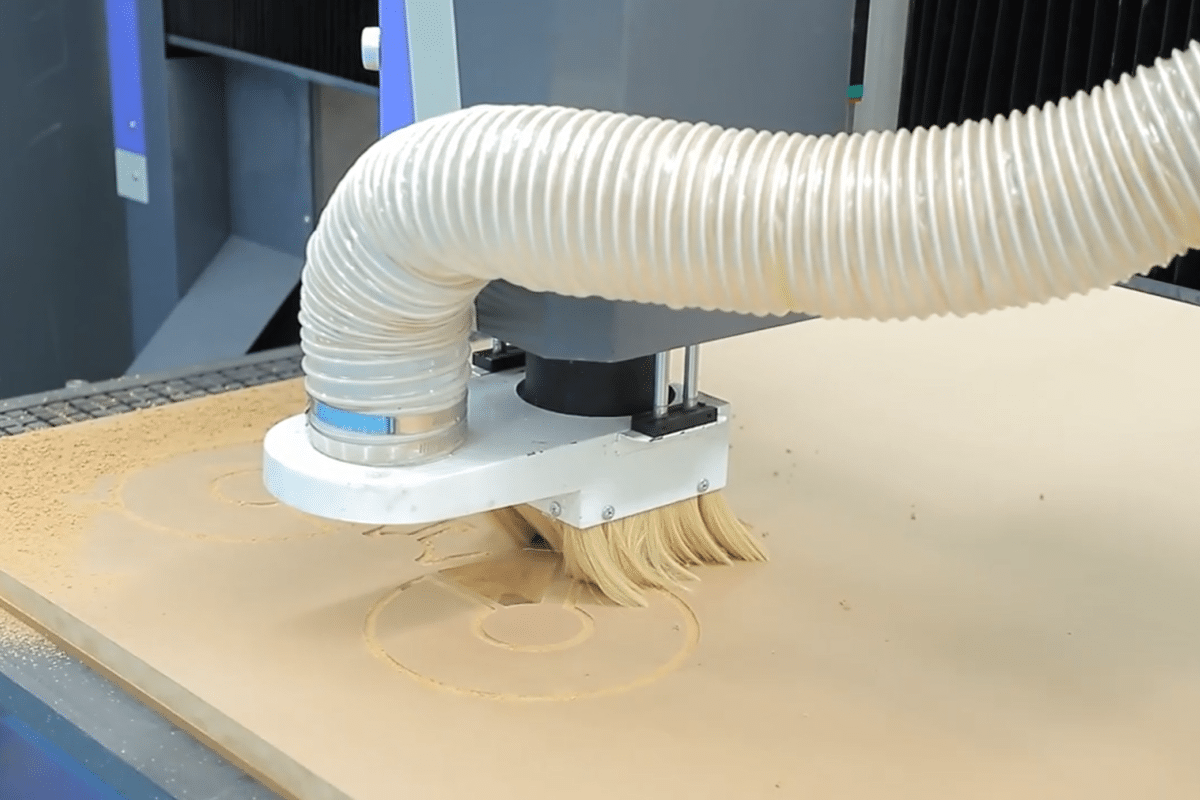
In CNC machining, stepover is a crucial parameter that determines the amount of overlap between adjacent tool passes during cutting, carving, or engraving. Stepover is typically expressed as a percentage of the tool diameter and plays a key role in balancing cutting speed and surface quality. A larger stepover increases machining speed but may leave visible tool marks, while a smaller stepover results in a smoother finish but extends processing time.
CNC routers use specific calculations to determine the optimal stepover based on factors such as tool diameter, material properties, and surface finish requirements. This article explores how CNC routers calculate stepover, the factors that affect it, and strategies for fine-tuning stepover. By understanding stepover settings, CNC users can enhance both productivity and the quality of their machined parts.
Understanding Stepover
Stepover is a critical parameter in CNC routing that directly affects both the surface finish and machining efficiency of a workpiece. It refers to the lateral distance between adjacent passes of the cutting tool during a machining operation. A well-chosen stepover ensures efficient material removal while maintaining the desired surface smoothness.
Importance of Stepover
Stepover directly influences the machining time, surface smoothness, and tool wear.
- Optimizing machining efficiency: A larger stepover increases the speed of material removal, reducing overall machining time.
- Achieving desired surface finish: A smaller stepover produces a finer surface finish, minimizing the need for post-processing.
- Extending tool life: Proper stepover selection helps distribute cutting forces evenly, reducing tool wear and heat buildup.
Impact on Tool Path and Surface Finish
Stepover significantly affects both the tool path strategy and the surface quality of the final workpiece.
- Impact on Tool Path: Different toolpath strategies use varying stepovers to balance material removal and finishing precision. Choosing the correct stepover prevents overloading the tool and ensures even cutting across the surface.
- Impact on Surface Finish: A large stepover speeds up machining but creates visible tool marks, commonly known as scallops or ridges. A small stepover results in a smoother surface but increases machining time due to more passes.
By understanding the importance and impact of stepover, CNC operators can make informed decisions when programming their toolpaths. The next sections will cover the factors affecting stepover calculation and the calculation principles behind it to ensure optimal CNC machining performance.
Factors Affecting Stepover
Selecting the right stepover size is beneficial for achieving a balance between machining speed, surface finish, and tool longevity. Here, we explore the four key factors that influence the optimal stepover setting:
Tool Diameter
The size of the cutting tool directly impacts the stepover value:
- Larger tools allow for larger stepovers, improving efficiency by covering more area per pass.
- Smaller tools require smaller stepovers to maintain precision and avoid excessive scalloping.
- Standard industry practice suggests 50% of the tool diameter for roughing and 10-20% for finishing.
- Example: A 10mm end mill with a 50% stepover moves 5mm per pass, whereas a 20% stepover moves only 2mm per pass for a finer finish.
Material Hardness
The hardness of the material affects how much material can be effectively removed per pass:
- Softer materials (wood, plastic): Can accommodate larger stepovers without compromising quality.
- Harder materials (metals, composites): Require smaller stepovers to prevent excessive tool wear and ensure smooth cutting.
- Brittle materials (glass, acrylic, ceramics): Demand fine stepovers to avoid cracking or chipping.
- Example: Cutting aluminum with a 6mm ball nose end mill may require a 10-20% stepover, whereas softwood could allow 40-50% without significant surface defects.
Machine Rigidity
The structural stability and accuracy of the CNC router play a role in determining the ideal stepover:
- High-rigidity machines: Can handle larger stepovers without excessive vibration or tool deflection.
- Less rigid or smaller CNC machines: May require smaller stepovers to maintain precision and avoid cutting inaccuracies.
- Backlash or flex in the machine: This can lead to uneven cuts, making finer stepovers necessary.
- Example: A high-end industrial CNC router can use 50% stepover on aluminum, while a desktop CNC router may need 25% or less to maintain accuracy.
Tool Path Strategy
The type of tool path used in CNC programming affects the ideal stepover:
- Raster Toolpath (Parallel Passes): Requires smaller stepovers for a smooth surface, commonly used in finishing.
- Offset Toolpath (Contour Following): Can use larger stepovers, ideal for roughing operations.
- Spiral Toolpath: Provides smoother transitions and can allow for adaptive stepovers.
- Adaptive Clearing: Dynamically adjusts stepover to optimize cutting forces and efficiency.
- Example: A raster toolpath with a ball nose end mill for 3D carving may require a 10% stepover, whereas an offset toolpath for roughing can use 50% or more.
By carefully considering these factors, CNC router operators can optimize stepover settings to achieve the best balance of speed, efficiency, and surface finish for any given project.
Stepover Calculation
The stepover value is typically calculated based on tool diameter, material properties, and surface quality requirements. Here are three common approaches to calculating the optimal stepover:
Empirical Method (Rule of Thumb Approach)
This method relies on industry best practices and pre-established guidelines to determine the stepover based on experience.
How It Works
Use pa ercentage of tool diameter as a general guide:
- Roughing operations: 40-60% of the tool diameter
- Finishing operations: 10-20% of the tool diameter
- High-precision work (e.g., engraving): 5-10% of the tool diameter
Adjust based on material hardness and required surface finish.
Example Calculation
- If using a 12mm end mill, a 50% stepover would be: Stepover=12×50=6mm
- For a high-precision finish with a 15% stepover: Stepover=12×15=1.8mm
This stepover calculation method is quick, widely used, and effective for standard machining operations. However, it suffers from the inability to take into account real-time machine behavior or specific material-tool interactions.
Tool Path Simulation (CAM Software Analysis)
Modern CNC machining relies on CAM (Computer-Aided Manufacturing) software to simulate toolpaths and optimize stepover before actual machining.
How It Works
- Enter tool size, material type, and surface finish requirements into CAM software.
- The software calculates and suggests optimal stepover values based on toolpath strategy and scallop height equations.
- Simulations show the surface quality, allowing for adjustments before actual machining.
Example Calculation
- If a 6mm ball nose end mill is used for 3D contouring, the software might recommend a stepover of 1mm to maintain a scallop height of 0.02mm.
This stepover calculation method is highly accurate and avoids over-machining or poor surface quality. It also saves time and material by reducing errors before machining. However, the simulation accuracy of this method depends on the correct machine setup, so the CNC router operator needs expertise in CAM software.
Test Piece Processing (Trial-and-Error Method)
This method involves machining a test piece and adjusting the stepover based on real-world results.
How It Works
- Select an initial stepover based on empirical rules.
- Machine a small test area using different stepover values.
- Measure the surface roughness or inspect the scallop marks.
- Adjust the stepover accordingly and finalize the optimal setting.
Example Scenario
- A CNC operator machining aluminum might start with a 30% stepover (3mm for a 10mm tool).
- After testing, they found that reducing to 20% (2mm) eliminates visible tool marks, improving finish quality.
This stepover calculation method is most accurate for specific machine-material combinations and can help fine-tune setups for custom workpieces, but it is not always practical for large-scale production because it is a one-off job, so it is time-consuming and wastes material.
Each method has its advantages depending on machining complexity, precision requirements, and available resources. The empirical method is best for quick, standard calculations. Toolpath simulation is ideal for precision machining and automatic optimization. Test piece processing is most accurate but requires additional time and material. For optimal CNC machining, combining these methods ensures efficient, high-quality results with minimal waste.
Fine-Tuning Stepover for Optimal Performance
Once the initial stepover of the CNC router is calculated, further adjustments are often necessary to achieve the best balance between machining speed, surface finish, and tool life. Fine-tuning the stepover involves making small modifications based on real-world machining conditions and specific project requirements.
Surface Finish Considerations
Stepover directly impacts the smoothness and texture of the machined surface.
- Larger stepover results in visible tool marks (scallop lines), requiring post-processing.
- Smaller stepover produces a smoother finish but increases machining time.
- Ball nose end mills require smaller stepovers (10-15% of tool diameter) for fine 3D contours, while flat end mills can use larger stepovers for roughing.
- Optimization Tip: If a highly polished or detailed surface is required, start with a 15-20% stepover and reduce as needed to eliminate noticeable marks.
Tool Wear and Life
The stepover setting affects how much load is applied to the tool, influencing wear rate and cutting efficiency.
- Excessive stepover increases cutting resistance, causing faster tool wear.
- Too small of a stepover can lead to inefficient cutting, increasing the risk of burn marks and heat buildup.
- Harder materials like stainless steel require a smaller stepover to avoid overloading the tool and extending tool life.
- Optimization Tip: Monitor tool wear during machining. If wear accelerates, try reducing stepover slightly or adjusting spindle speed and feed rate for better heat dissipation.
Processing Time Optimization
Stepover affects cycle time, impacting overall machining efficiency.
- Larger stepovers (40-60% of tool diameter) are ideal for roughing, maximizing material removal per pass.
- Smaller stepovers (10-20%) are best for finishing, improving precision but increasing machining time.
- Adaptive toolpaths in CAM software adjust stepover dynamically to maintain consistent cutting forces, improving efficiency.
- Optimization Tip: For large batch production, balance speed and finish quality by setting a moderate stepover (~30% of tool diameter) and refining only critical surface areas with a finer pass.
Fine-tuning stepover requires balancing surface quality, tool longevity, and processing efficiency. By adjusting stepover based on surface finish needs, tool wear rates, and machining time constraints, CNC router operators can optimize performance for faster, higher-quality, and cost-effective machining operations.
Advanced Technology for Stepover Calculation
The development of CNC machining technology has introduced more intelligent and automated methods for calculating and optimizing stepover. Two key advancements in this area are adaptive processing and tool path optimization software, which enhance machining efficiency, precision, and surface quality.
Adaptive Processing
Adaptive processing is an advanced technology that dynamically adjusts stepover based on real-time machining conditions. Instead of using a fixed stepover value throughout the process, CNC systems continuously analyze factors such as tool wear, cutting forces, and surface conditions, making automatic adjustments to optimize efficiency and quality.
Key Features
- Real-Time Stepover Adjustment: CNC controllers adapt the stepover dynamically, reducing it in high-detail areas and increasing it in less critical regions.
- Tool Wear Compensation: The system detects tool deflection or wear and modifies the stepover accordingly to maintain consistent cutting performance.
- Material Variation Handling: Some materials (such as composites or cast metals) have inconsistent hardness, and adaptive processing ensures the stepover changes accordingly to prevent excessive force or uneven cuts.
Example
- In wood engraving, adaptive processing reduces stepover for intricate details while increasing it for larger areas, balancing speed and surface finish.
- In metal routing, sensors detect tool wear and automatically decrease stepover to reduce stress on the cutter, prolonging tool life.
Benefits
- Increases machining precision by adjusting stepover in critical areas.
- Reduces tool wear and heat buildup, extending tool life.
- Improves efficiency by using variable stepovers instead of a fixed value.
Tool Path Optimization Software
Advanced CAM software integrates intelligent tool path optimization to automatically calculate the best stepover for different toolpaths. These programs analyze geometry, material properties, and machining goals to generate an optimized stepover for both roughing and finishing passes.
Key Features
- Automatic Stepover Calculation: The software determines the best stepover based on tool type, material, and desired surface finish.
- Adaptive Toolpath Strategies: Instead of using fixed raster paths, modern CAM software adjusts the stepover dynamically based on surface curvature and cutting load.
- Minimization of Scallop Height: In 3D machining, the software ensures that the stepover value is optimized to reduce tool marks and scallops, improving surface finish.
- Multi-Axis Machining Support: For 5-axis CNC routers, tool path optimization ensures that the stepover is adjusted across complex curved surfaces to prevent overcutting or gouging.
Example
- Fusion 360 and Mastercam use adaptive clearing strategies to adjust stepover dynamically during roughing, ensuring efficient material removal.
- PowerMill and SolidCAM calculate the minimum necessary stepover in 3D surface machining to reduce machining time while maintaining accuracy.
Benefits
- Enhances machining efficiency by optimizing stepover across different toolpaths.
- Reduces manual programming effort by automatically setting the best stepover.
- Ensures better surface quality by adjusting the stepover based on geometry and cutting forces.
By integrating adaptive processing and intelligent tool path optimization software, modern CNC routers achieve greater accuracy, efficiency, and automation in stepover calculation. These advancements allow CNC machines to dynamically adjust stepover based on real-time conditions while automatically optimizing toolpaths for the best machining results. This not only improves surface finish and tool life but also reduces machining time and operational costs.
Summarize
Stepover calculation is a critical aspect of CNC routing that directly influences machining efficiency, surface finish, and tool longevity. By understanding the fundamentals of stepover, considering key factors such as tool diameter, material hardness, machine rigidity, and toolpath strategy, and utilizing advanced technologies, CNC router operators can optimize their machining processes for the best results. Whether using empirical methods, CAM software simulations, or test piece processing, fine-tuning stepover ensures a balance between speed, accuracy, and cost-effectiveness.
When it comes to high-precision and efficient CNC routing, AccTek CNC stands out as a professional CNC router manufacturer that integrates advanced machining technologies to deliver superior performance. Our CNC routers provide consistent performance, smooth cutting transitions, and reliable precision. For manufacturers seeking efficiency, quality, and innovation, AccTek CNC is the trusted choice for advanced CNC routing solutions.
The stepover value is typically calculated based on tool diameter, material properties, and surface quality requirements. Here are three common approaches to calculating the optimal stepover: