- 10-15 Min Read
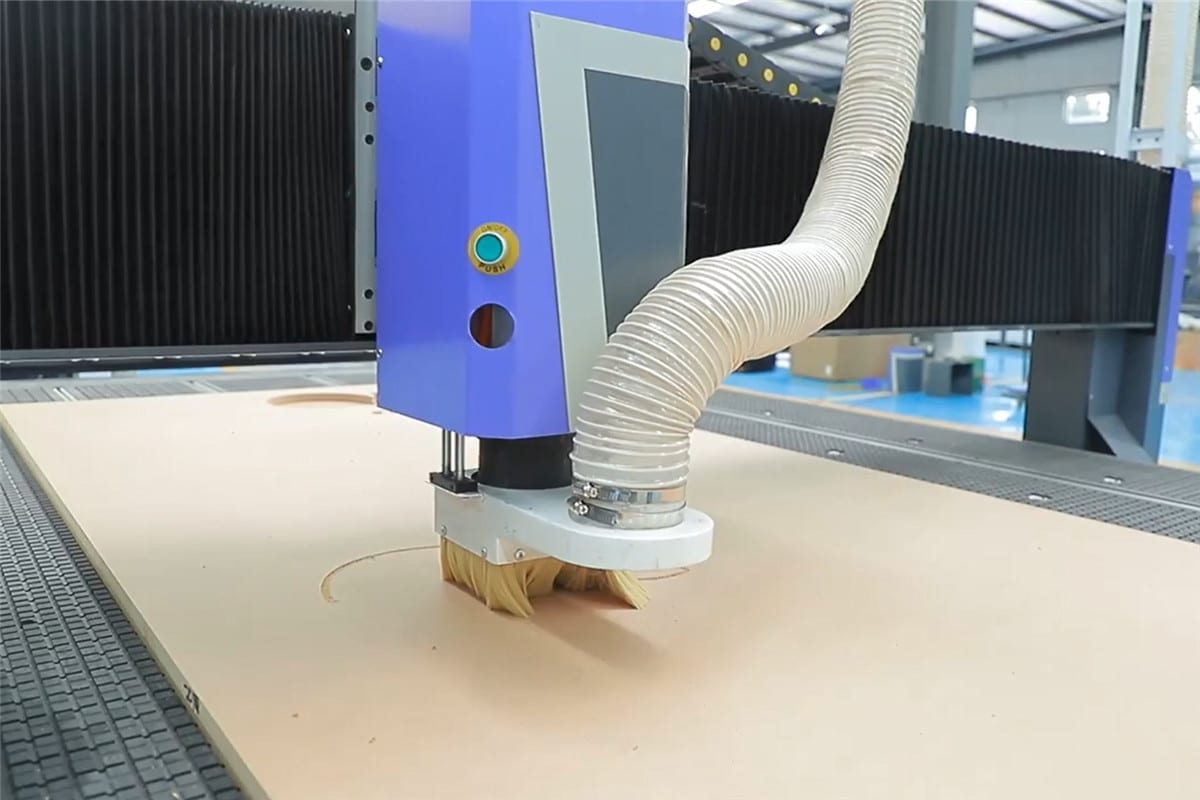
Understanding CNC Router Cutting Depth
Factors Influencing Cutting Depth
Achieving the desired cutting depth with a CNC router involves considering various factors that influence the performance of the machine and the quality of the cut. Understanding and optimizing these factors based on the material and cutting task requirements helps unlock the CNC router’s full potential and achieve accurate and efficient cutting depths. Here are the key factors that play a crucial role in determining CNC router cutting depth:
- Z-Axis Travel: The cutting depth is directly influenced by the Z-axis travel of the CNC router. The Z-axis, representing the vertical movement of the cutting tool, is a primary factor in determining cutting depth. Different CNC router models have varying Z-axis travel distances, establishing the maximum depth the tool can cut.
- Cutting Tool Length: The length of the cutting tool, often referred to as the end mill or router bit, is a critical factor in determining the maximum cutting depth. Longer tools allow for greater cutting depth, but considerations of stability and accuracy must be addressed to avoid compromising the machining process.
- Material Type: The nature of the material being cut significantly influences cutting depth. Softer materials may allow for deeper cuts, while harder materials may require shallower cuts to avoid excessive tool wear, heat generation, and potential damage to the material.
- Cutting Tool Diameter: The diameter of the cutting tool also influences cutting depth. Smaller-diameter tools may need more passes to achieve the same depth as larger-diameter tools. The tool diameter choice depends on the cutting task’s specific requirements.
- Spindle Speed: The spindle speed, measured in revolutions per minute (RPM), affects the cutting performance. Higher spindle speeds are often associated with finer cuts, while lower speeds may be suitable for roughing passes. Optimizing spindle speed helps achieve the desired cutting depth efficiently.
- Feed Rate: The feed rate, representing the speed at which the cutting tool moves along the material, impacts cutting depth. Adjusting the feed rate allows for control over the material removal rate and helps prevent issues like tool breakage and excessive heat generation.
- Stepover Distance: In CNC machining, the stepover distance refers to the lateral distance between two passes of the cutting tool. It influences the surface finish and the time it takes to complete a machining operation. Adjusting the stepover distance can impact the cutting depth and the overall efficiency of the process.
- Material Support and Fixturing: Proper support and fixturing of materials help maintain stability during machining. Inadequate support can lead to vibrations, affecting the precision of the cut and potentially limiting the achievable cutting depth.
- Tool Geometry and Coating: The geometry of the cutting tool, including the number of flutes and their shape, as well as the presence of coatings, can impact cutting performance. Proper tool selection based on material and application can help achieve the desired cutting depth.
Cutting Depth for Different Materials
- Softwoods (e.g., pine, cedar): CNC routers can achieve relatively deep cuts in softwoods, often allowing for efficient material removal.
- Hardwoods (e.g., oak, maple): Cutting depth in hardwoods may be shallower due to their higher density and hardness. Multiple passes may be needed to achieve the desired depth.
- MDF (Medium-Density Fiberboard): MDF is a common material in woodworking. CNC routers can achieve substantial cutting depths in MDF, but considerations of tool wear and dust extraction are important.
- Acrylic, PVC, and polycarbonate: These materials are often well-suited for CNC routing, and cutting depths can vary based on the specific type of plastic. Care should be taken to avoid melting or chipping.
- Fiberglass, carbon fiber: CNC routers are often used for precision cutting of composite materials. Cutting depths may be influenced by the type and arrangement of fibers in the composite.
- HDPE (High-Density Polyethylene): Generally, HDPE is machinable with CNC routers, and cutting depths can be adjusted based on the material thickness.
- Polyurethane foam, expanded polystyrene (EPS): CNC routers can achieve significant cutting depths in foam materials. Care should be taken to avoid excessive heat generation.
- Aluminum: CNC routers can cut aluminum, but the cutting depth may be limited compared to softer materials. The use of specialized cutting tools and lubrication can enhance performance.
- Soft metals (e.g., brass, copper): Similar considerations as aluminum apply, and cutting depths may vary based on the specific metal.
- Soft stones: CNC routers can be used for engraving and light cutting of soft stones, but cutting depth may be limited.
- Hard stones (e.g., granite, marble): CNC routers are not typically used for deep cutting in hard stones due to the high hardness and abrasive nature of these materials.
- Glass: CNC routers are generally not suitable for cutting glass due to its brittle nature. CNC engraving or etching is more common for glass applications.
Strategies for Achieving Greater Cutting Depth
- Tool Selection: Choose a router bit with a larger diameter, as larger bits can handle deeper cuts. Consider using end mills specifically designed for deep cutting with features like long flutes and sturdy construction.
- Spindle Power and Speed: Ensure that your CNC router has sufficient spindle power to handle deeper cuts. Adjust the spindle speed to match the cutting conditions and material being used. Higher speeds may be required for certain materials.
- Machine Rigidity: Check for any play or flex in the machine structure, as this can negatively impact cutting depth. Ensure that your machine is properly calibrated and well-maintained. A rigid and stable CNC router is more helpful in completing deep cutting.
- Step-Down and Step-Over Values: Optimize step-down (vertical depth per pass) and step-over (horizontal distance between passes) values in your CAM software. Smaller step-down values can help in achieving greater depth gradually. Experiment with different settings to find the balance between efficiency and quality.
- Cutting Speeds and Feeds: Adjust the cutting speeds and feeds based on the material being machined. Consult the tool and material manufacturers’ recommendations. Running the CNC router at optimal speeds and feeds can improve the efficiency of the cutting process.
- Coolant and Chip Evacuation: Use coolant to dissipate heat during cutting, especially when working with hard materials. Ensure effective chip evacuation to prevent chips from interfering with the cutting process.
- Toolpath Optimization: Optimize your toolpaths to minimize tool engagement and reduce the load on the tool during cutting. Consider using adaptive toolpaths that dynamically adjust the cutting conditions based on the geometry of the part.
- Material Considerations: Different materials may require different cutting strategies. Adjust your parameters based on the hardness and characteristics of the material. Consider using climb milling for better chip evacuation.
- Testing and Fine-Tuning: Conduct test cuts on scrap material to fine-tune your cutting parameters and ensure optimal results. Monitor the cutting process closely during initial attempts at a greater cutting depth.
Limitations and Challenges
While CNC routers are versatile tools for cutting and engraving, they do have certain limitations and challenges when it comes to cutting depth. Understanding these limitations and addressing them through careful planning, tool selection, and machine setup can help achieve accurate and reliable cutting depth when using a CNC router.
- Tool Length and Rigidity: The length and rigidity of the cutting tool can limit the achievable cutting depth. Longer tools may experience increased deflection, affecting accuracy and potentially causing tool breakage.
- Material Hardness: Hard materials, such as metals or certain composites, may pose challenges for achieving significant cutting depths. Softer materials are generally more suitable for deeper cuts.
- Tool Diameter: The diameter of the cutting tool influences the maximum achievable cutting depth. Smaller diameter tools are often limited in how deeply they can cut without compromising stability.
- Machine Power: The power of the CNC router’s spindle motor plays a role in determining the maximum cutting depth. Higher-powered machines can handle deeper cuts more effectively.
- Cutting Speed and Feed Rate: Aggressive cutting speeds and feed rates can lead to excessive heat generation, tool wear, and decreased tool life. So the right balance needs to be found to achieve optimal cutting depth.
- Material Holding Capacity: The ability of the work holding system to securely hold the material in place becomes more critical with increased cutting depth. Inadequate workholding may result in material movement or vibrations.
- Surface Finish: Deeper cuts may result in rougher surface finishes, especially if the tool is not designed for heavy cutting. Finishing passes or additional processes may be required to achieve the desired surface quality.
- Chip Evacuation: Efficient chip evacuation becomes challenging as cutting depth increases. Proper chip removal helps prevent problems such as recutting, tool overheating, and potential damage to the workpiece.
- Tool Cooling: Deeper cuts generate more heat, and adequate cooling helps prevent tool overheating and premature wear. Insufficient cooling can lead to tool failure and poor cutting performance.
- Machining Time: Deeper cuts may increase machining time significantly. There is a need to balance cutting depth and production efficiency to meet project deadlines.
- Tool Path Optimization: Complex designs or toolpaths with sharp changes in direction may limit the achievable cutting depth. Optimizing toolpaths for smoother transitions can help overcome this challenge.
- Material Thickness: The thickness of the material being cut can influence the practical cutting depth. Cutting too deeply into thin materials may result in instability or damage.
- Tool Changes: Some CNC routers may have limitations on the tool-changing mechanism, affecting the ease with which tools can be changed during a job, especially for varying cutting depths.
Safety Considerations
Ensuring safety is paramount when working with CNC routers, especially when dealing with cutting depth. Here are important safety considerations to keep in mind. By adhering to these safety considerations, operators can significantly reduce the risk of accidents and injuries when working with CNC routers, especially when adjusting cutting depths.
- Personal Protective Equipment (PPE): Wear appropriate PPE, including safety glasses or goggles to protect your eyes from debris, and hearing protection if the CNC router generates significant noise. Gloves can also provide additional protection.
- Emergency Stop Button: Ensure the CNC router is equipped with an easily accessible emergency stop button. Operators should be trained on its use, and it should be tested regularly to guarantee functionality.
- Machine Isolation: Before making adjustments or changing tools, ensure the CNC router is turned off and properly isolated. This prevents accidental activation and minimizes the risk of injury during maintenance.
- Material Securing: Securely fasten the material being cut to prevent movement during the machining process. Unsecured materials can lead to accidents and damage to the CNC router.
- Tool Inspection: Regularly inspect cutting tools for signs of wear or damage. Damaged tools can break during operation, posing a safety risk. Replace tools as needed, and follow proper tool-changing procedures.
- Dust Collection and Ventilation: Implement a dust collection system to remove debris and maintain a clean work environment. Proper ventilation helps prevent the inhalation of harmful particles and fumes.
- Cooling System: Ensure that the CNC router’s cooling system is functioning correctly. Adequate cooling helps prevent overheating of the tool and reduces the risk of injuries related to hot components.
- Training and Supervision: Provide comprehensive training to operators on the safe use of the CNC router, including proper handling of cutting depths. Always have a qualified and trained individual supervising machine operation.
- Emergency Response Plan: Develop and communicate an emergency response plan that includes procedures for dealing with potential accidents, injuries, or equipment malfunctions. Ensure all operators are familiar with these procedures.
- Electrical Safety: Regularly inspect electrical components and wiring for signs of wear or damage. Follow electrical safety protocols and ensure the CNC router is properly grounded.
- Clear Workspace: Keep the workspace clear of unnecessary tools, materials, or obstructions. A clutter-free environment minimizes the risk of tripping hazards and ensures a safer working space.
Future Trends and Progress
As technology evolves, advancements in cutting depth capabilities are likely to be driven by a combination of improved hardware, software, and material science. Here, we provide insights into potential directions and advancements that could shape the future of CNC router machine technology, including cutting-depth capabilities.
- Precision and Accuracy Improvements: Future CNC routers may feature enhanced precision and accuracy in controlling cutting depths. Advancements in sensor technologies and feedback systems could contribute to more reliable depth control.
- Smart Automation: Integration of smart automation and artificial intelligence (AI) could lead to CNC routers that can automatically optimize cutting parameters, including depth, based on material properties and design requirements. This could improve efficiency and reduce the need for manual calibration.
- Real-time Monitoring and Feedback: Future CNC routers may incorporate real-time monitoring systems that provide instant feedback on cutting performance. This can include monitoring tool wear, detecting anomalies in cutting forces and adjusting parameters on the fly to maintain optimal cutting depth.
- Multi-Tool Systems: CNC routers with advanced multi-tool systems may become more prevalent. These systems could allow for seamless tool changes during a job, enabling the use of different tools for varied cutting depths and applications within a single project.
- Material Science Innovations: Advancements in materials, especially those designed for CNC machining, may influence cutting depth capabilities. New materials with improved machinability could allow for deeper cuts without compromising quality.
- Improved Cooling and Lubrication Systems: Future CNC routers may incorporate more efficient cooling and lubrication systems to handle increased cutting depths. Better heat dissipation and chip evacuation systems could contribute to longer tool life and improved cutting performance.
- Nanotechnology Applications: Nanotechnology innovations could impact the design and performance of cutting tools, potentially leading to tools that are more durable and capable of achieving greater cutting depths with precision.
- Additive Manufacturing Integration: Integration of additive manufacturing (3D printing) and subtractive manufacturing processes within the same CNC router could open up new possibilities for complex geometries and varied cutting depths within a single manufacturing workflow.
- Enhanced Software Capabilities: Future CNC router software may feature advanced algorithms for toolpath optimization, taking into account cutting-depth requirements, material characteristics, and machine capabilities. This could result in more efficient and precise machining.