- 12-16 Min Read
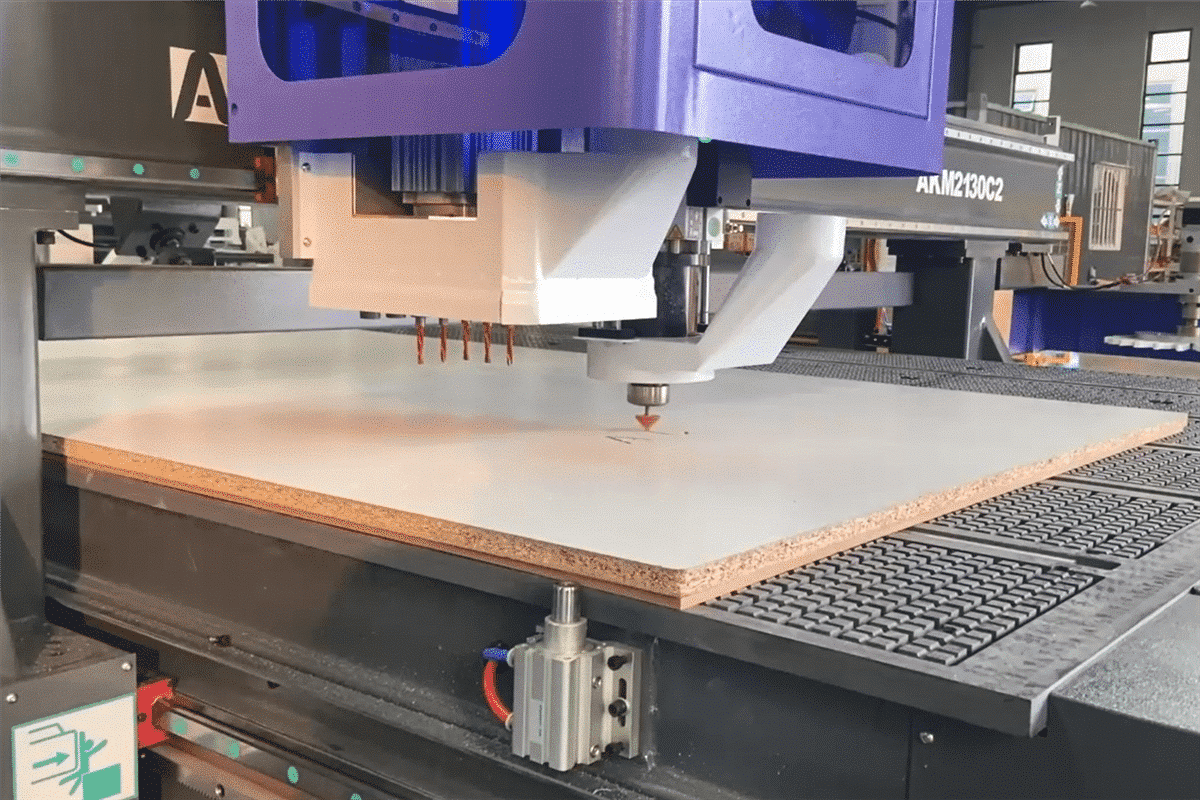
In the realm of precision engineering, the CNC router stands as a versatile tool, capable of sculpting raw materials with unparalleled accuracy. Yet, achieving optimal results across diverse materials demands a nuanced understanding of how to optimize its parameters. This article serves as a comprehensive guide to fine-tuning your CNC router settings to achieve optimal results across a wide range of materials.
From the robustness of hardwood to the delicacy of acrylic, each material demands specific adjustments in speed, feed rate, spindle speed, and tool selection. Whether you are an experienced machinist or a novice eager to explore the capabilities of your CNC router, this guide will provide you with practical insights and step-by-step instructions. Learn how to navigate the complexities of different materials, avoid common pitfalls, and enhance your cutting precision and efficiency. Our goal is to equip you with the knowledge and techniques necessary to make these adjustments with confidence.
Basic knowledge of CNC router parameters
When working with a CNC router, achieving the best results requires a thorough understanding of the key parameters that influence the cutting process. Each factor plays a role in determining the quality, efficiency, and precision of your cuts. Here, we break down the basics of these parameters to help you optimize your CNC router settings.
- Cutting Speed: Cutting speed refers to the speed at which the cutting tool moves through the material. It is typically measured in meters per minute (m/min) or feet per minute (ft/min). The appropriate cutting speed depends on the type of material being cut. For instance, softer materials like plastic or wood can be cut at higher speeds, while harder materials like metals require slower speeds to avoid tool damage and ensure a smooth finish. Adjusting the cutting speed correctly helps in prolonging tool life and achieve the desired surface quality.
- Feed Amount: Feed amount, or feed rate, is the distance the cutting tool advances into the material per revolution of the spindle. It is usually measured in millimeters per revolution (mm/rev) or inches per revolution (in/rev). A higher feed rate can increase productivity but may also increase the load on the tool and reduce precision. Conversely, a lower feed rate may improve accuracy but at the cost of longer machining times. Balancing the feed rate is beneficialfor efficient and precise cutting.
- Cutting Depth: Cutting depth refers to the vertical distance the cutting tool penetrates into the material in a single pass. It is a critical parameter because too deep a cut can overload the tool and the CNC router, leading to tool breakage or poor surface finish. Shallow cuts, while safer, may require multiple passes and increase machining time. Optimal cutting depth depends on the material’s hardness and the tool’s capabilities. Generally, harder materials require shallower cuts.
- Spindle Speed: Spindle speed is the rotational speed of the cutting tool, measured in revolutions per minute (RPM). The correct spindle speed depends on the material and the tool being used. Higher spindle speeds are suitable for softer materials and small-diameter tools, while lower speeds are better for harder materials and larger-diameter tools. Properly adjusting spindle speed helps in achieving a clean cut and extends the lifespan of the tool.
- Tool Selection: Choosing the right cutting tool is fundamental to the success of any CNC routing project. Tools vary in material, coating, size, and geometry, and each type is suited for specific materials and cutting conditions. For example, carbide tools are excellent for cutting hard materials like metals, while high-speed steel (HSS) tools are preferred for softer materials like wood and plastic. The shape and size of the tool, including the number of flutes, also affect cutting performance. Selecting the appropriate tool ensures efficient material removal, superior surface finish, and longer tool life.
Mastering the basic parameters of CNC routing is beneficial for optimizing your machining processes. By understanding and adjusting these parameters according to the material and specific project requirements, you can achieve precise, high-quality cuts while maximizing efficiency and extending tool life. Whether you are a seasoned machinist or a newcomer to CNC routing, these foundational concepts are the key to successful and proficient CNC machining.
Material considerations in CNC routing
CNC routing, like any manufacturing process, presents unique challenges depending on the material being used. Here’s an overview of the challenges and considerations for metals, plastics, composite materials, wood, and ceramics, and how these factors influence the optimization of CNC routing parameters.
Metals
- Challenge and Considerations: Metals are typically harder and more prone to heat buildup during machining. They can also produce a lot of vibration and noise, leading to tool wear and potential part inaccuracies.
- Impact on Parameter Optimization: Parameters such as cutting speed, feed rate, and tool material/coating need careful consideration to balance between efficient material removal and tool longevity. Cooling and lubrication strategies are also beneficial to manage heat buildup and extend tool life.
Plastics
- Challenge and Considerations: Plastics have a tendency to melt rather than chip away during machining, leading to issues like burrs, built-up edges on cutting tools, and poor surface finish.
- Impact on Parameter Optimization: Parameters such as cutting speed and feed rate need to be adjusted to prevent excessive heat buildup. Tool geometry and material selection are beneficial to minimize burr formation and ensure a smooth surface finish.
Composite Materials
- Challenge and Considerations: Composite materials consist of multiple layers with different properties, which can lead to delamination, fiber pullout, and uneven material removal during machining.
- Impact on Parameter Optimization: Parameters must be optimized to prevent delamination while ensuring efficient material removal. Tool selection, cutting speeds, and feed rates should be carefully adjusted to accommodate the varying properties of different layers within the composite material.
Wood
- Challenge and Considerations: Wood is prone to tearing, splintering, and grain direction issues during machining, which can result in poor surface finish and dimensional inaccuracies.
- Impact on Parameter Optimization: Parameters such as cutting direction, tool geometry, and feed rate need to be optimized to minimize tearing and splintering. Understanding the grain direction and adjusting cutting strategies accordingly helps achieve high-quality finishes and precise dimensions.
Ceramics
- Challenge and Considerations: Ceramics are extremely hard and brittle materials, making them prone to chipping, cracking, and tool wear during machining.
- Impact on Parameter Optimization: Parameters need to be carefully optimized to minimize tool wear and prevent cracking or chipping of the ceramic workpiece. Cutting speeds, feed rates, and tool materials/coatings must be selected to balance between material removal efficiency and tool longevity.
Each material presents its own set of challenges in CNC routing, ranging from heat buildup and tool wear to surface finish and dimensional accuracy issues. Parameter optimization plays a critical role in addressing these challenges and achieving efficient and high-quality machining results for various materials.
Optimize cutting speeds and feed rates
Cutting speed, feed rate, and cutting depth are fundamental parameters in CNC machining that significantly influence the processing process, including material removal rate, surface finish, tool life, and overall machining efficiency. Here’s an introduction to these parameters and their effects, followed by optimal values for different materials:
Cutting Speed
- Impact: Cutting speed directly affects the material removal rate, tool life, surface finish, and heat generation. High cutting speeds can reduce machining time but may lead to increased heat generation, which can cause tool wear and workpiece deformation. Low cutting speeds can improve tool life and surface finish but may increase machining time.
- Optimal Values: For metals, slower cutting speeds are typically used to reduce heat build-up. However, with materials such as plastics and composites, higher cutting speeds can be used to achieve a clean cut without generating excessive heat. Due to the brittle nature of ceramics, it may be necessary to use very slow cutting speeds to prevent cracking and control tool wear.
Feed Rate
- Impact: Feed rate influences chip thickness, cutting forces, surface finish, and tool life. High feed rates can reduce machining time but may cause poor surface finish and dimensional inaccuracies due to increased cutting forces. Low feed rates can improve surface finish and dimensional accuracy but may lead to longer machining times and potential tool wear due to insufficient material removal rates.
- Optimal Values: Optimal feed rates depend on the material being machined and the specific machining operation. For metals, a moderate feed rate is usually chosen to balance efficient material removal with tool life. Plastics and composites may require moderate to high feed rates to reduce heat build-up and prevent melting. Wood machining often benefits from moderate feed rates to balance between chip evacuation and surface finish. Ceramics may require slow feed rates to minimize stress and avoid cracking.
Cutting Depth
- Impact: Cutting depth affects chip thickness, cutting forces, tool deflection, and surface finish. High cutting depths can increase material removal rates and efficiency but may lead to excessive tool wear, increased cutting forces, and potential workpiece deformation. Low cutting depths can improve tool life and surface finish but may result in longer machining times due to reduced material removal per pass.
- Optimal Values: Optimal cutting depths depend on factors such as material hardness, tool geometry, and machine rigidity. For metals, shallower depths of cut are often utilized to prevent overloading the tool and ensure a smooth surface finish. Plastics and composites can be deeper than metal, but should be balanced to avoid chipping. The wood can be worked relatively deep but will need to be adjusted to avoid tearing. Ceramics generally require shallow cuts to minimize the risk of chipping and tool breakage.
It’s important to note that optimal cutting parameters may vary based on specific machining conditions, such as machine rigidity, tool geometry, coolant/lubrication, and workpiece geometry. Experimentation and adjustment may be necessary to achieve the best results for a particular material and machining operation. Additionally, consulting tool manufacturers’ recommendations and machining guidelines can provide valuable insights into optimal cutting parameters for different materials.
Spindle speed optimization
Spindle speed optimization is a critical aspect of CNC machining that involves understanding the fundamental principles of spindle speed, balancing spindle speed with tool material characteristics, and implementing adaptive control techniques to optimize cutting performance Let’s delve into each of these aspects:
Understanding the Spindle Speed
- Definition and Importance: The spindle speed refers to the rotational speed of the spindle and the cutting tool attached to it, measured in revolutions per minute (RPM). It determines the rate at which the cutting tool engages with the workpiece material. The spindle speed directly impacts cutting parameters such as cutting forces, chip formation, tool wear, and surface finish.
- Material Considerations: Different materials require different spindle speeds based on their properties, such as hardness, thermal conductivity, and machinability. Metals, plastics, wood, and composites each have optimal speed ranges.
Balancing Spindle Speed and Tool Material
- Tool Material Properties: The choice of tool material and coat influences the optimal spindle speed for a given machining operation. Carbide tools are preferred for their hardness and wear resistance, allowing for higher spindle speeds compared to high-speed steel (HSS) tools. Coating tools like TiN, TiAlN, or DLC can enhance tool performance at higher spindle speeds by reducing friction and wear.
- Balancing Considerations: Higher spindle speeds generate more heat, which can affect tool life and workpiece quality. Coated tools or tools made from materials with high thermal resistance can mitigate this. Finding the balance between spindle speed and tool material properties helps in maximizing tool life while maintaining productivity.
Adaptive Spindle Speed Control
- Real-Time Monitoring and Adjustment: Adaptive spindle speed control involves monitoring machining conditions in real-time and dynamically adjusting spindle speed to optimize cutting performance. Sensors can be used to measure parameters such as cutting forces, tool wear, temperature, and vibration, providing feedback for adaptive control algorithms.
- Benefits and Applications: Adaptive spindle speed control offers several benefits, including improved tool life, reduced machining time, enhanced surface finish, and energy savings. It is particularly useful in complex machining operations, variable material properties, and applications where maintaining consistent cutting conditions is challenging.
- Implementation Techniques: Modern CNC systems often come with adaptive control features that automatically adjust spindle speed and feed rate based on pre-set algorithms and real-time feedback. CAM software can simulate and optimize tool paths, suggesting optimal spindle speeds and making adjustments based on the material and tool being used.
Tool selection and toolpath optimization
When using a CNC router to cut different materials, tool selection and tool path optimization is beneficial for achieving high-quality results, minimizing tool wear, and maximizing machining efficiency. Here’s a detailed introduction on how to approach these aspects for various materials:
Choosing the right tool
- Tool Geometry: Tool geometry plays a key role in determining machining efficiency. Different geometries, such as square end mills, ball nose end mills, drills, etc., are suitable for specific machining operations. For example, ball nose end mills are ideal for 3D contouring, while drills are better for creating holes. Additionally, considerations like rake angle, helix angle, and edge preparation impact chip formation, tool life, and surface finish.
- Materials and Coatings: The choice of tool material and coatings significantly affects machining efficiency. High-speed steel (HSS), carbide, and ceramic are common tool materials, each offering specific advantages. Carbide, for instance, is known for its high hardness and wear resistance, making it suitable for high-speed machining and hard materials. Coatings like TiN (Titanium Nitride), TiCN (Titanium Carbo-Nitride), and TiAlN (Titanium Aluminum Nitride) enhance tool life, reduce friction, and improve chip evacuation.
- Strategies for Selection: When selecting the best tool for different materials, consider factors like material hardness, cutting conditions (speed, feed, depth of cut), surface finish requirements, and budget constraints. For example, for high-speed machining of aluminum, carbide tools with polished flutes and high helix angles are preferred to minimize chip adhesion and achieve an excellent surface finish.
Tool Path Optimization
- Impact on Cutting Forces, Tool Wear, and Surface Finish: Optimized tool paths play a key role in minimizing cutting forces, reducing tool wear, and improving surface finish. Strategies like constant tool engagement, smooth transitions between cutting passes, and minimizing air cutting can enhance machining efficiency. Moreover, adaptive tool paths adjust cutting parameters based on real-time feedback, optimizing tool engagement and prolonging tool life.
- Implementing Optimized Tool Paths: CAD/CAM software offers various tool path optimization features, such as high-efficiency roughing, rest machining, and trochoidal milling. High-efficiency roughing strategies, like dynamic milling or adaptive clearing, remove material quickly while maintaining consistent tool engagement, reducing cutting forces, and extending tool life. Rest machining identifies areas left by previous tool paths and removes material only from those areas, reducing machining time and tool wear. Trochoidal milling involves using circular tool paths to minimize radial cutting forces and improve surface finish, particularly in deep cavities.
Advanced Mold Technology
- Adaptive Tool Paths: Adaptive tool paths dynamically adjust cutting parameters based on real-time sensor feedback, such as cutting forces, tool wear, and temperature. These paths optimize tool engagement, minimize tool deflection, and maximize material removal rates, particularly in complex geometries and varying material properties.
- Tool Monitoring: Tool monitoring systems use sensors to track tool wear, cutting forces, vibration, and temperature during machining operations. Real-time data analysis enables predictive maintenance, early detection of tool wear or breakage, and optimization of cutting parameters to prevent tool failure and ensure consistent quality.
CNC router maintenance to optimize parameters
Regular maintenance practices help maintain the optimal functioning of a CNC router, which in turn ensures that machining parameters remain effective and reliable. Implementing a tool life monitoring system can significantly enhance the optimization of machining parameters by providing real-time data and predictive insights. Here’s a detailed introduction:
Regular Maintenance Practices
- Cleaning and Lubrication: Remove chips, dust, and debris from the machine surfaces, spindle, tooling, and work area to prevent accumulation that can affect machine performance and precision. Lubricate all moving parts such as linear guides, ball screws, and bearings every week or as recommended by the manufacturer to reduce friction and prevent wear.
- Calibration and Alignment: Periodically calibrate the machine’s axes, spindle alignment, and tool changer to maintain accuracy and precision. Check the squareness and parallelism of the machine’s axes and worktable. Ensuring these are correct helps maintain the integrity of cutting parameters and machining accuracy.
- Tool Inspection and Replacement: Regularly inspect cutting tools for signs of wear, damage, or dullness. Replace tools as needed to maintain cutting quality and efficiency. Ensure tool holders are clean and free of debris. Inspect for wear and ensure proper clamping to maintain tool stability and accuracy.
- Spindle and Coolant System Maintenance: Maintain the coolant system to ensure it provides adequate cooling during operations. Regularly check coolant levels and replace or clean the coolant as necessary. Monitor spindle bearings for any signs of wear or damage. Replacing worn bearings prevents spindle runout, maintaining precision and surface finish.
- Electrical and Electronic Components: Regularly inspect wiring and electrical connections for signs of wear, damage, or loose connections. Address any issues promptly to prevent electrical problems. Ensure proper cooling of electronic components to prevent overheating and premature failure.
Tool Life Monitoring System
- Real-Time Monitoring: Equip the CNC router with sensors to monitor critical parameters such as cutting forces, vibrations, temperature, and tool wear in real-time. Continuously collect data from these sensors during machining operations to monitor the condition and performance of the cutting tools and the machine.
- Data Analysis and Parameter Optimization: Analyze the collected data to identify trends and patterns in tool wear and machine performance. Use this information to understand how different parameters affect tool life and machining efficiency. Based on the analysis, adjust cutting parameters such as spindle speed, feed rate, and depth of cut to optimize tool life and improve machining performance. For example, reducing spindle speed or feed rate when excessive tool wear is detected can prolong tool life and prevent unexpected tool failures.
- Predictive Maintenance: Set predefined thresholds for tool wear or other critical parameters. When these thresholds are reached, the system can trigger alerts or alarms, prompting maintenance actions before tool failure occurs. Use predictive analytics to forecast tool life and schedule maintenance or tool replacements proactively. This approach minimizes unplanned downtime and ensures continuous, efficient operation.
- Closed-Loop Control and Automation: Implement closed-loop control systems that automatically adjust machining parameters in real-time based on feedback from the tool life monitoring system. This ensures optimal cutting conditions are maintained throughout the machining process. Integrate tool life monitoring data with Computer-Aided Manufacturing (CAM) software to dynamically adjust tool paths and cutting strategies. This integration helps in optimizing the entire machining process for better efficiency and tool longevity.
Summarize
Optimizing the parameters of a CNC router when cutting different materials is a multifaceted process that requires careful consideration of material properties, tool selection, cutting conditions, and maintenance practices. By integrating these practices and leveraging modern CNC technologies, manufacturers can achieve higher productivity, lower production costs, and superior machining quality across a wide range of materials and applications. With a systematic approach to parameter optimization, CNC router operators can unlock the full potential of their machines and stay competitive in today’s manufacturing landscape.
At AccTek CNC, we provide our users with high-quality CNC routers and exceptional customer service. Whether you’re a small business owner, a hobbyist, or a large-scale manufacturer, we’re here to ensure that you have the tools and support you need to succeed. Our commitment to excellence extends beyond delivering the right CNC machinery, we strive to empower our customers with valuable knowledge and resources to optimize their CNC router operations. Thank you for choosing AccTek CNC. We look forward to helping you unlock the full potential of your CNC router and achieve your machining goals with precision and efficiency.