- 5-8 Min Read
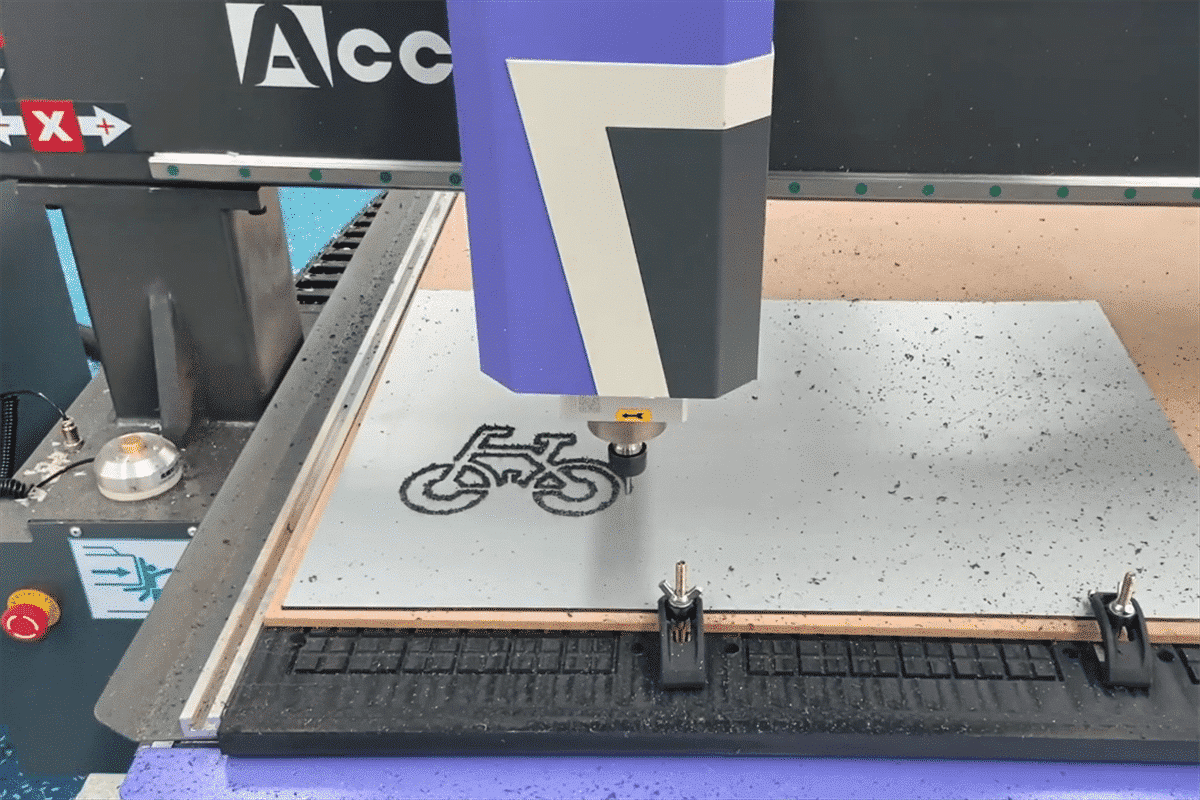
Computer Numerical Control (CNC) routers have revolutionized manufacturing processes across industries, offering unparalleled precision, efficiency, and versatility. These machines, capable of executing intricate designs quickly and accurately, are indispensable tools in modern production facilities. However, their optimal performance is contingent upon several factors, one of the most critical being environmental conditions. In recent years, the impact of extreme environments, particularly temperature and humidity fluctuations, on CNC router performance has garnered increasing attention from researchers and industry professionals alike. The interplay between these environmental variables and machine functionality presents a complex challenge.
This article comprehensively explores how extreme temperatures and humidity levels affect the operation and output of CNC routers. By understanding and addressing the impact of extreme environments on CNC routers, we aim to optimize machine performance, improve product quality, and maximize machine operating efficiency under different environmental conditions. Read on and you can get actionable advice for mitigating the adverse effects of extreme environments on your CNC router’s performance.
The importance of CNC router environmental considerations
There are many considerations involved in using a CNC router, with environmental factors playing a role in ensuring efficiency, safety, and sustainability. Incorporating environmental considerations into CNC routing operations can minimize negative impacts, conserve resources, and promote sustainable manufacturing practices. The following are examples of the importance of environmental factors when operating a CNC router:
- Efficiency and Performance: Environmental conditions such as temperature, humidity, and air quality can directly impact the performance and efficiency of CNC routers. Operating within optimal environmental parameters ensures consistent and reliable machine operation, minimizing errors, downtime, and material wastage.
- Machine Longevity: Extreme temperatures and humidity levels can accelerate wear and tear on CNC router components, leading to premature failure and increased maintenance costs. By controlling environmental factors, businesses can extend the lifespan of their equipment and maximize return on investment.
- Accuracy and Precision: CNC routers rely on precise movements and measurements to produce high-quality parts and components. Fluctuations in temperature and humidity can cause materials to expand or contract, affecting dimensional tolerances and surface finish. Maintaining consistent environmental conditions within the machining environment helps ensure repeatability and quality in finished parts.
Ideal operating conditions for CNC router
The ideal operating environment for a CNC router typically involves maintaining stable temperature and humidity conditions within a specified range to ensure optimal performance, accuracy, and longevity of the machine. While specific recommendations may vary depending on the manufacturer and the model of the CNC router, the following general guidelines can help create an ideal operating environment:
- Temperature Range: The standard temperature range for operating CNC routers is typically between 18℃to 24℃ (64℉ to 75℉). This range helps minimize thermal expansion or contraction of machine components, ensuring dimensional stability and accuracy in machining operations.
- Humidity Range: The recommended humidity range for operating CNC routers is typically between 40% to 60% relative humidity. This range helps prevent corrosion and rust formation on metal components, maintains the dimensional stability of materials, and minimizes the risk of static electricity buildup.
- Follow Manufacturer Recommendations: It’s essential to consult the manufacturer’s recommendations and specifications for the specific CNC router model being used. Manufacturers often provide guidelines regarding the ideal operating environment, including temperature and humidity ranges, as well as any other environmental considerations or requirements.
Maintaining stable temperature and humidity conditions within recommended ranges is beneficial in achieving and maintaining high levels of accuracy and precision in CNC machining operations. Stable working conditions also contribute to the longevity of the machine and reduce the risk of premature wear or damage to components. Regularly monitoring and controlling environmental factors can optimize CNC router performance and maximize productivity.
The impact of extreme environments on CNC router performance
Extreme environments can have various impacts on CNC router performance, potentially leading to operational challenges and reduced efficiency. Dealing with the impact of extreme environments on CNC routers requires implementing various measures to mitigate potential risks and ensure optimal performance. The following are the effects of extreme environments on CNC routers and coping strategies:
Effect of extreme temperatures on CNC router performance
Extreme temperatures, whether excessively hot or cold, can affect the performance of CNC routers. Temperature fluctuations can cause thermal expansion or contraction of machine components, leading to dimensional inaccuracies in machined parts. Additionally, temperature-sensitive components such as electronics and lubricants may experience degradation or malfunction, resulting in machine downtime and decreased productivity.
Strategies for coping with extreme temperatures
- Install HVAC (heating, ventilation, and air conditioning) systems to regulate temperature within the recommended range.
- Use temperature control devices such as thermostats and heaters to maintain stable temperatures in the CNC router’s operating area.
- Insulate the workspace to minimize the effects of external temperature fluctuations.
Effect of high humidity on CNC router performance
High levels of humidity can promote corrosion and rust formation on metal components of CNC routers, especially in environments with poor ventilation or exposure to moisture. Corrosion can lead to premature wear and tear of machine parts, affecting accuracy and reliability.
Strategies for coping with high humidity
- Use dehumidifiers to control humidity levels within the recommended range.
- Seal windows, doors, and other openings to prevent moisture ingress and maintain stable humidity levels.
- Implement moisture-resistant materials and coatings to protect CNC router components from corrosion and rust.
By implementing these strategies, businesses can effectively mitigate the impact of extreme environments on CNC routers, ensuring reliable performance, accuracy, and longevity of the equipment.
Measures to prevent the impact of environments on CNC routers
To prevent the impact of extreme environments on CNC routers, especially in terms of calibration, formulating a daily calibration plan and taking measures can solve the problem in a timely and effective manner. This helps minimize downtime and optimize productivity. The following are measures to prevent the impact of extreme environments on CNC routers.
- Establish Environmental Monitoring: To mitigate the impact of environmental changes on CNC router calibration, it’s essential to implement environmental controls and monitoring systems. This may include maintaining stable temperature and humidity levels within specified ranges and using sensors and data logging systems to track changes over time. Regular calibration checks and adjustments are also necessary to ensure the continued accuracy and reliability of CNC router operations despite changing environmental conditions.
- Define Acceptable Ranges: Determine acceptable ranges for environmental factors based on manufacturer specifications and industry standards. These ranges should ensure optimal performance and accuracy of the CNC router while considering the specific requirements of the machining processes.
- Regular Calibration Schedule: Develop a routine calibration schedule based on the environmental conditions and the operating frequency of the CNC router. Calibration should be performed regularly to maintain accuracy and consistency in machining operations.
- Environmental Controls: Implement environmental controls to mitigate the impact of extreme conditions on calibration. This can include climate-controlled enclosures, insulation, and humidity control systems to maintain stable operating conditions within acceptable ranges.
- Emergency Response Plan: Develop an emergency response plan to address sudden changes or incidents that may affect the CNC router’s calibration. This plan should outline steps for identifying, troubleshooting, and resolving issues promptly to minimize downtime and production delays.
- Staff Training and Awareness: Train operators and maintenance personnel on the importance of environmental factors in CNC router calibration and performance. Raise awareness about potential risks associated with extreme environments and educate staff on preventive measures and troubleshooting techniques.
- Documentation and Record-Keeping: Maintain detailed records of calibration activities, environmental conditions, and any deviations from the established norms. Documentation should include calibration schedules, procedures, results, and corrective actions taken to address issues.
- Supplier Collaboration: Collaborate with suppliers and service providers to identify potential solutions for mitigating the impact of extreme environments on CNC router calibration. Suppliers may offer specialized equipment, components, or maintenance services tailored to specific environmental conditions.
- Continuous Improvement: Regularly review and evaluate the effectiveness of calibration plans and environmental controls. Identify areas for improvement and implement changes as necessary to optimize CNC router performance and minimize the impact of environmental changes on calibration.
By implementing these measures, businesses can proactively address the challenges posed by extreme environments and ensure the reliable operation and accuracy of CNC routers over time. Effective calibration planning and environmental management can maximize the productivity, quality and profitability in CNC machining operation.
Summarize
The study on the impact of extreme environments on the performance of CNC routers shows that fluctuations in temperature and humidity can significantly affect the dimensional accuracy, service life, and overall efficiency of the machine. Armed with this understanding, manufacturers and operators can implement proactive measures to mitigate the adverse effects of extreme environments. By implementing the measures mentioned above, users can bolster the resilience of CNC routers against environmental challenges, thereby ensuring consistent performance and superior product quality.
AccTek CNC is a well-known CNC router manufacturer in China, committed to providing CNC machining solutions to meet the changing needs of various industries around the world. At AccTek, our goal is not only to provide high-quality CNC routers, we also strive to provide users with the necessary knowledge and resources to maximize the performance and efficiency of their machining operations. Welcome to choose AccTek and let us be your partner in seeking excellent processing solutions.