- 12-18 Min Read
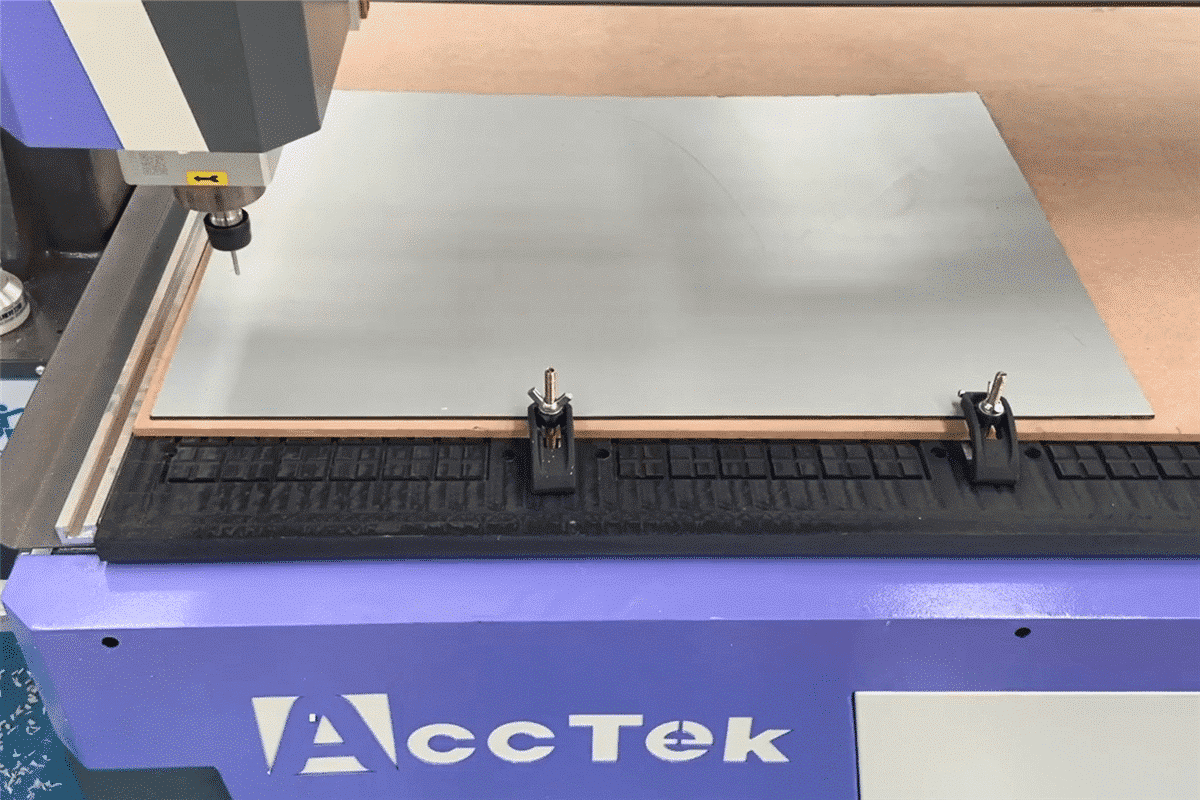
In the realm of Computer Numerical Control (CNC) machining, the efficacy of clamping methods plays a pivotal role in determining the accuracy, reliability, and efficiency of the manufacturing process. As CNC routers become increasingly ubiquitous in various industries, understanding the diverse array of clamping techniques available is imperative for optimizing productivity and ensuring high-quality outcomes. Whether it’s securing delicate workpieces with precision or maximizing throughput in mass production environments, the choice of clamping method significantly influences the overall machining process.
This article delves into the intricate world of clamping methods for CNC routers, shedding light on their functionality, advantages, and applications. From traditional techniques like manual clamping to advanced solutions such as vacuum and magnetic clamping, each method brings its own set of benefits and considerations. Through comprehensive analysis and practical insights, this article aims to empower CNC operators, engineers, and enthusiasts with the knowledge needed to optimize clamping setups, thereby unlocking the full potential of CNC routers in modern manufacturing.
The importance of clamping in CNC routing
The importance of clamping in CNC routing extends far beyond mere fixture holding—it serves as a cornerstone for achieving precision, safety, versatility, and efficiency in modern manufacturing operations. The importance of clamping in CNC routing is reflected in several critical aspects of the machining process:
- Precision and Accuracy: Clamping directly influences the precision and accuracy of CNC routing operations. Securely holding workpieces in place ensures that they remain stationary during cutting, drilling, or milling processes. Any movement or vibration due to inadequate clamping can result in dimensional inaccuracies, affecting the quality of the final product.
- Workpiece Stability: Effective clamping methods provide stability to the workpiece, preventing it from shifting or vibrating during machining. This stability is crucial, especially when dealing with intricate designs or tight tolerances. By minimizing workpiece movement, clamping enhances the consistency and repeatability of machining operations.
- Safety: Proper clamping not only safeguards the integrity of the workpiece but also promotes operator safety. Inadequate clamping can lead to workpiece ejection or unexpected tool contact, posing risks of injury to personnel and damage to equipment. Robust clamping solutions help mitigate these risks, creating a safer working environment for CNC operators.
- Optimized Machining Parameters: The choice of clamping method can impact the selection of machining parameters such as feed rates, cutting speeds, and tool engagement. With reliable clamping, operators can confidently apply optimal machining parameters, maximizing material removal rates while minimizing tool wear and energy consumption.
- Versatility and Flexibility: Different clamping methods offer varying degrees of versatility and flexibility, allowing manufacturers to adapt to diverse machining requirements. Whether it’s accommodating irregularly shaped workpieces, changing setups between production runs, or facilitating multi-axis machining, the right clamping solution enhances the CNC router’s adaptability to various applications.
- Production Efficiency: Efficient clamping methods streamline setup times, tool changes, and workflow processes, contributing to overall production efficiency. By reducing downtime associated with clamping adjustments or workpiece repositioning, manufacturers can maximize machine utilization and throughput, ultimately improving productivity and profitability.
Workpiece Clamping Type
Direct Workpiece Clamping
Direct workpiece clamping involves securing the workpiece directly to the machine table without the use of intermediate fixtures or holding devices. This method is commonly employed when machining flat or simple geometries where the workpiece can be easily accessed and clamped from the edges or corners.
Direct clamping offers simplicity and versatility, allowing for quick setup and minimal material obstruction during machining. It is often used for prototyping, one-off projects, or small-scale production runs where setup time is a critical factor. However, direct clamping may not be suitable for complex workpiece shapes or materials that require additional support and stability during machining.
Fixture-Based Clamping
Fixture-based clamping utilizes specialized holding devices or fixtures to secure the workpiece in a predefined position on the machine table. These fixtures are custom-designed to match the contours of the workpiece, providing optimal support and stability during machining.
Fixture-based clamping is particularly useful for batch production or repetitive machining tasks where consistent setup is required. By securely holding the workpiece in place, fixture-based clamping minimizes the risk of workpiece movement or vibration during machining, resulting in improved precision and repeatability. However, fixture-based clamping may require more time and effort for setup and may not be as flexible as direct clamping for accommodating changes in workpiece geometry or size.
Common Clamping Methods
In CNC routing, workpiece clamping is crucial for securing the material firmly in place during machining operations. Various types of clamping methods are employed to accommodate different workpiece geometries, materials, and machining requirements. Here are some common methods of workpiece clamping used in CNC routers:
Mechanical Clamping
Mechanical clamping is a versatile and widely used method in CNC routing. It involves securing the workpiece using mechanical devices such as screws, toggles, or clamps. These clamps exert force to hold the workpiece firmly against the machine table or fixture, ensuring stability during machining operations.
Mechanical clamping is suitable for a wide range of workpiece geometries and materials, making it a popular choice for CNC routing applications. It offers flexibility in adjusting clamp positions and pressures to accommodate varying workpiece sizes and shapes. Additionally, mechanical clamps provide a strong and reliable hold, minimizing the risk of workpiece movement or displacement during cutting, drilling, or milling processes.
Vacuum Clamping
Vacuum clamping utilizes suction to hold the workpiece securely onto the machine table. A vacuum pump creates negative pressure between the workpiece and the table surface, effectively sucking the workpiece into place. This method is particularly well-suited for thin or non-porous materials such as sheet goods, plastics, and composites.
Vacuum clamping offers several advantages, including uniform clamping pressure across the entire workpiece surface, accessibility for machining the entire workpiece profile without obstruction from clamps, and ease of setup for quick workpiece changes. However, vacuum clamping may not be suitable for porous or irregularly shaped workpieces, as they may not create a sufficient seal for effective clamping.
Pneumatic Clamping
Pneumatic clamping systems utilize compressed air to actuate clamps or cylinders that secure the workpiece to the machine table. This method offers fast and automated clamping, making it ideal for high-volume production environments. Pneumatic clamps can exert significant clamping force, ensuring workpiece stability during Aggressive machining operations. They are commonly used in conjunction with mechanical clamps to provide additional holding force or to automate clamping processes for improved productivity.
Pneumatic clamping systems are versatile and adaptable, allowing for easy adjustment of clamping pressures and positions to suit different workpiece requirements. However, pneumatic clamping may require additional infrastructure such as air compressors and pneumatic control systems, and careful consideration of safety protocols to prevent accidental clamp release during operation.
Hydraulic Clamping
Hydraulic clamping systems utilize hydraulic fluid to generate clamping force and secure the workpiece to the machine table or fixture. These systems typically consist of hydraulic cylinders or actuators that exert pressure on clamping elements, such as clamps or vices, to hold the workpiece in place. Hydraulic clamping offers high clamping force and uniform pressure distribution, making it suitable for heavy-duty machining applications where extreme force is required to secure large or heavy workpieces.
Hydraulic clamps are often used in conjunction with mechanical or fixture-based clamping systems to provide additional holding force and stability during machining operations. While hydraulic clamping systems offer excellent performance and reliability, they may require additional infrastructure such as hydraulic pumps, hoses, and control systems, and careful maintenance to ensure optimal operation.
Magnetic Clamping
Magnetic clamping systems utilize powerful magnets to hold ferrous workpieces securely in place on the machine table. These magnets create a strong magnetic field that attracts and holds the workpiece firmly against the table surface. Magnetic clamping offers several advantages, including quick and easy setup, minimal obstruction during machining, and the ability to hold workpieces of various shapes and sizes without the need for mechanical clamps or fixtures. It is particularly well-suited for flat or prismatic workpieces made of ferrous metals, such as steel or cast iron.
Magnetic clamping systems are versatile and adaptable, allowing for rapid workpiece changes and improved workflow efficiency. However, magnetic clamping may not be suitable for non-ferrous materials or workpieces with irregular shapes or surface profiles that do not provide sufficient contact area for effective clamping.
These clamping methods each offer unique advantages and considerations in CNC routing applications. By understanding their characteristics and capabilities, manufacturers can select the most suitable solution to meet their specific machining requirements and optimize productivity and quality in their CNC routing processes.
Considerations for selecting clamping methods
When selecting a clamping method for CNC routing, several key considerations should be taken into account to ensure optimal performance, efficiency, and safety throughout the machining process. These considerations include:
Workpiece Materials and Properties
- Material Hardness: Hard materials such as metals may require clamping methods capable of exerting high clamping forces to prevent workpiece movement during machining. Mechanical clamping or hydraulic clamping systems may be suitable for securing hard materials effectively.
- Material Conductivity: For non-ferrous materials that are not magnetic, such as aluminum or brass, magnetic clamping would not be suitable. Alternative clamping methods like mechanical clamping or vacuum clamping may be preferred.
- Material Porosity: Porous materials like wood or foam may not provide a suitable surface for vacuum clamping due to air leakage. In such cases, mechanical clamping methods may be more effective in securing the workpiece.
- Material Fragility: Delicate materials prone to damage or deformation, such as ceramics or glass, require gentle clamping methods to avoid workpiece breakage. Vacuum clamping may be preferred for securing fragile materials without applying excessive force.
- Material Size and Shape: Consider the size, shape, and surface characteristics of the workpiece when selecting a clamping method. Irregularly shaped or oversized workpieces may require custom fixtures or mechanical clamps to provide adequate support and stability during machining.
Machining Operations and Tool Paths
- Cutting Forces: Machining operations involving high cutting forces, such as heavy milling or roughing, require clamping methods capable of withstanding these forces without workpiece movement. Hydraulic clamping or mechanical clamping systems with robust holding capacity may be suitable for such applications.
- Tool Access: The clamping method should allow unobstructed access for the cutting tool to reach all areas of the workpiece without interference. Vacuum clamping or magnetic clamping systems that do not require physical clamps or fixtures may provide greater accessibility for machining operations.
- Tool Path Complexity: Complex tool paths involving intricate cuts or multi-axis machining require stable workpiece fixation to maintain dimensional accuracy and surface finish. Fixture-based clamping methods can offer comprehensive support and stability for complex machining operations.
- Tool Change Frequency: Clamping methods that facilitate quick tool changes and workpiece setup are advantageous for applications with frequent tool changes or batch production. Pneumatic clamping or quick-change fixture systems can streamline setup times and maximize productivity.
CNC Router Configuration
- Table Design and Size: The design and size of the CNC router table influence the choice of clamping method. For example, a large, flat table may be suitable for vacuum clamping, while a smaller table with T-slots may be better suited for mechanical clamping with clamps or vises.
- Compatibility with CNC Router Components: Consider the compatibility of the clamping system with other CNC router components such as the spindle, tool changer, and automated systems. Certain clamping methods may interfere with toolpaths or limit the range of motion of the spindle, affecting machining capabilities and efficiency.
- Integration with Automation: If the CNC router is integrated with automation systems for material handling or tool changing, the clamping method should facilitate seamless integration and operation. Automated clamping systems, such as pneumatic or vacuum clamps, may be preferred for streamlined workflow and reduced operator intervention.
Operator Safety and Ergonomics
- Workpiece Securement: The clamping method should ensure the securement of the workpiece throughout the machining process to prevent workpiece ejection or movement. Proper clamping reduces the risk of accidents, tool interference, and potential injury to the operator.
- Accessibility and Visibility: The selected clamping method should provide clear visibility and easy access to the workpiece for loading, unloading, and inspection. This facilitates safe operation and allows operators to monitor machining processes without obstruction.
- Emergency Stop and Override: CNC routers should be equipped with emergency stop features and manual override capabilities to quickly halt operations in case of emergencies or unexpected events related to clamping failure or workpiece misalignment.
- Ergonomic Considerations: Consider ergonomic factors such as operator comfort, fatigue, and ease of operation when selecting clamping methods. Choose systems that minimize repetitive tasks and physical strain to enhance operator productivity and well-being.
Clamping accessories and enhanced functions
Clamping accessories and enhanced functions can help optimize the efficiency, versatility, and precision of CNC routers. Here are some common clamping accessories and enhanced functions used in CNC router setups:
T-Slot Worktable and Fixtures
T-slot worktables are foundational components of CNC routers, providing a versatile platform for securing workpieces and fixtures during machining operations. These tables feature a grid of T-shaped slots or channels along the surface, allowing for the attachment of various clamping accessories, fixtures, and workholding devices. T-slot worktables offer flexibility in workpiece positioning and securement, enabling operators to quickly and precisely clamp down materials of different shapes and sizes. Fixtures, which are specialized holding devices or setups, can be securely mounted to the T-slot worktable to provide additional support and stability for workpieces during machining. Common types of fixtures include vices, clamps, and custom-designed fixtures tailored to specific machining requirements. T-slot worktables and fixtures are essential elements of CNC router setups, facilitating efficient workflow and ensuring accurate machining results.
Soft Jaws and Fixtures
Soft jaws and fixtures are designed to securely hold delicate or irregularly shaped workpieces without causing damage or deformation. Soft jaws are typically made of materials such as aluminum or plastic and can be machined or molded to match the contours of the workpiece. These jaws provide a gentle yet firm grip, minimizing the risk of workpiece marring or surface imperfections during machining. Soft fixtures, similarly, feature non-abrasive surfaces or padded inserts to protect the workpiece while providing sufficient clamping force. Soft jaws and fixtures are particularly useful for machining materials that are prone to damage or for intricate geometries where surface finish is critical. By incorporating soft jaws and fixtures into CNC router setups, manufacturers can ensure the integrity of their workpieces while achieving precise and repeatable machining results.
By incorporating these clamping accessories and enhancements into CNC router configurations, manufacturers can achieve greater versatility, precision, and efficiency in their machining operations, ultimately leading to improved productivity and quality of finished parts.
Operator Clamping Technology Training
Operator Clamping Technology Training encompasses the education and skill development necessary for CNC router operators to effectively utilize various clamping methods and technologies. This training equips operators with the knowledge and expertise required to securely hold workpieces during machining operations, ensuring precision, safety, and productivity in CNC routing processes. Here are the key aspects typically included in such training programs:
Clamping Methods and Technologies
- Understanding different types of clamping methods used in CNC routing, such as mechanical clamps, vacuum clamping, hydraulic clamping, pneumatic clamping, magnetic clamping, and fixture-based clamping.
- Familiarization with the components, operation principles, advantages, and limitations of each clamping method.
- Selection criteria for choosing appropriate clamping methods based on workpiece characteristics, machining requirements, and safety considerations.
Clamping System Setup and Adjustment
- Hands-on training on setting up and adjusting various clamping systems, including installation of clamps, fixtures, workholding devices, and accessories.
- Techniques for aligning workpieces, securing clamps, and optimizing clamping pressures to ensure stability and precision during machining operations.
- Troubleshooting common issues related to clamping setup, such as misalignment, slippage, or inadequate holding force, and implementing corrective measures.
Safety Protocols and Best Practices
- Training on safety protocols, procedures, and best practices for handling clamping equipment, machinery, and related tools.
- Awareness of potential hazards associated with clamping operations, such as pinch points, entanglement, and flying debris, and strategies for mitigating risks.
- Importance of wearing appropriate personal protective equipment (PPE), maintaining clear work areas, and adhering to safety guidelines to prevent accidents and injuries.
Material Considerations and Workpiece Compatibility
- Knowledge of the properties, characteristics, and behaviors of common workpiece materials used in CNC routing, including metals, plastics, woods, and composites.
- Understanding the impact of workpiece material properties, such as hardness, porosity, fragility, and conductivity, on clamping requirements and selection of suitable clamping methods.
- Techniques for assessing workpiece compatibility with different clamping technologies and optimizing clamping strategies accordingly.
Clamping Optimization and Efficiency
- Strategies for optimizing clamping setups to improve machining efficiency, productivity, and accuracy.
- Minimizing setup times, reducing material wastage, and maximizing workflow efficiency through effective clamping practices.
- Utilizing advanced clamping technologies, adaptive clamping solutions, and automated workpiece positioning devices to enhance precision, repeatability, and versatility in machining operations.
Practical Application and Simulation
- Hands-on practical exercises, demonstrations, and simulation scenarios to reinforce learning objectives and develop practical skills in clamping technology.
- Opportunities for operators to apply acquired knowledge and techniques in real-world machining scenarios under supervised guidance and feedback.
Assessment and Certification
- Evaluation of operator competency through practical assessments, performance demonstrations, and knowledge assessments.
- Provision of certifications or qualifications upon successful completion of the clamping technology training program, indicating proficiency in clamping methods and technologies for CNC routing operations.
By addressing these key aspects in operator clamping technology training, CNC router operators can acquire the necessary knowledge, skills, and competencies to effectively utilize clamping methods and technologies, ensuring safe, efficient, and high-quality machining processes.
Maintenance and inspection of clamping systems
Maintenance and inspection of clamping systems are critical aspects of ensuring the safe and reliable operation of CNC routers. Here’s a guide covering the key steps and considerations for maintaining and inspecting clamping systems:
Regular Cleaning
- Begin by cleaning the clamping system components, including clamps, fixtures, and workholding devices, to remove dirt, debris, and coolant residue.
- Use appropriate cleaning agents and tools to avoid damaging sensitive components or surfaces.
- Inspect for any signs of wear, corrosion, or buildup that may affect clamping performance.
Lubrication
- Apply lubrication to moving parts and mechanisms of the clamping system to ensure smooth operation and prevent premature wear.
- Use lubricants recommended by the manufacturer to avoid compatibility issues and maintain optimal performance.
- Pay special attention to hydraulic or pneumatic components that require proper lubrication to operate effectively.
Tightening and Adjustment
- Check for loose fasteners, bolts, or screws in the clamping system and tighten them as needed to prevent shifting or movement during machining.
- Verify that clamps, fixtures, and workholding devices are securely mounted to the machine table or fixture plates to avoid workpiece slippage or misalignment.
- Adjust clamping pressures, angles, or positions as necessary to accommodate different workpiece sizes, shapes, and materials.
Wear and Damage Inspection
- Inspect all clamping system components for signs of wear, damage, or deterioration, such as cracks, dents, or deformation.
- Pay close attention to contact surfaces, jaws, and gripping areas that may show signs of excessive wear from repeated use.
- Replace worn or damaged components promptly to maintain clamping performance and prevent safety hazards.
Fluid Levels and Pressure Checks
- If the clamping system utilizes hydraulic or pneumatic components, check fluid levels and pressure settings regularly to ensure proper operation.
- Monitor for leaks, pressure drops, or abnormal noises during hydraulic or pneumatic operation, indicating potential issues that require attention.
- Follow manufacturer recommendations for fluid maintenance, filtration, and replacement intervals to prolong component lifespan and maintain system integrity.
Alignment and Calibration
- Verify the alignment and calibration of clamping system components, particularly for fixture-based setups or multi-axis machining applications.
- Use precision measurement tools and techniques to ensure accurate positioning, alignment, and repeatability of clamping devices and workpieces.
- Perform calibration checks on automated or CNC-controlled clamping systems to verify accuracy and consistency in clamping operations.
Documentation and Record-Keeping
- Maintain comprehensive records of clamping system maintenance activities, including cleaning schedules, lubrication intervals, inspections, and repairs.
- Document any observed issues, corrective actions taken, and recommendations for future maintenance or improvements.
- Keep track of component serial numbers, part replacements, and service history to facilitate troubleshooting and traceability.
By following these maintenance and inspection practices, CNC router operators can prolong the lifespan of clamping systems, minimize downtime, and ensure the safety and reliability of machining operations. Regular maintenance and proactive inspection are beneficial for identifying and addressing potential issues before they escalate into costly repairs or production disruptions.
Summarize
The exploration of clamping methods in CNC routers underscores their fundamental importance in ensuring the success of machining operations. From traditional mechanical clamps to advanced vacuum systems, each method offers unique benefits and considerations tailored to diverse machining tasks and workpiece materials. Understanding and implementing CNC router clamping methods contribute to the seamless execution of machining tasks, empowering manufacturers to achieve superior results and meet the demands of modern manufacturing industries. As technology advances and new innovations emerge, continued exploration and adaptation of clamping methods will drive efficiency, precision, and innovation in CNC routing processes.
At AccTek CNC, we understand the diverse needs of our users in CNC routing applications. Our recommendation is to leverage the versatility of our CNC routers equipped with T-slots and vacuum combination worktables. This unique configuration offers users the flexibility to choose between fixture clamping and vacuum adsorption, depending on the specific requirements of their machining tasks. By offering the option to seamlessly switch between fixture clamping and vacuum adsorption, our CNC routers empower users to adapt to various machining scenarios and optimize their workflow efficiency. Whether tackling intricate designs or high-volume production runs, AccTek CNC routers deliver the versatility and performance needed to achieve exceptional results. Choose AccTek to start your CNC machining plan.