- 5-8 Min Read
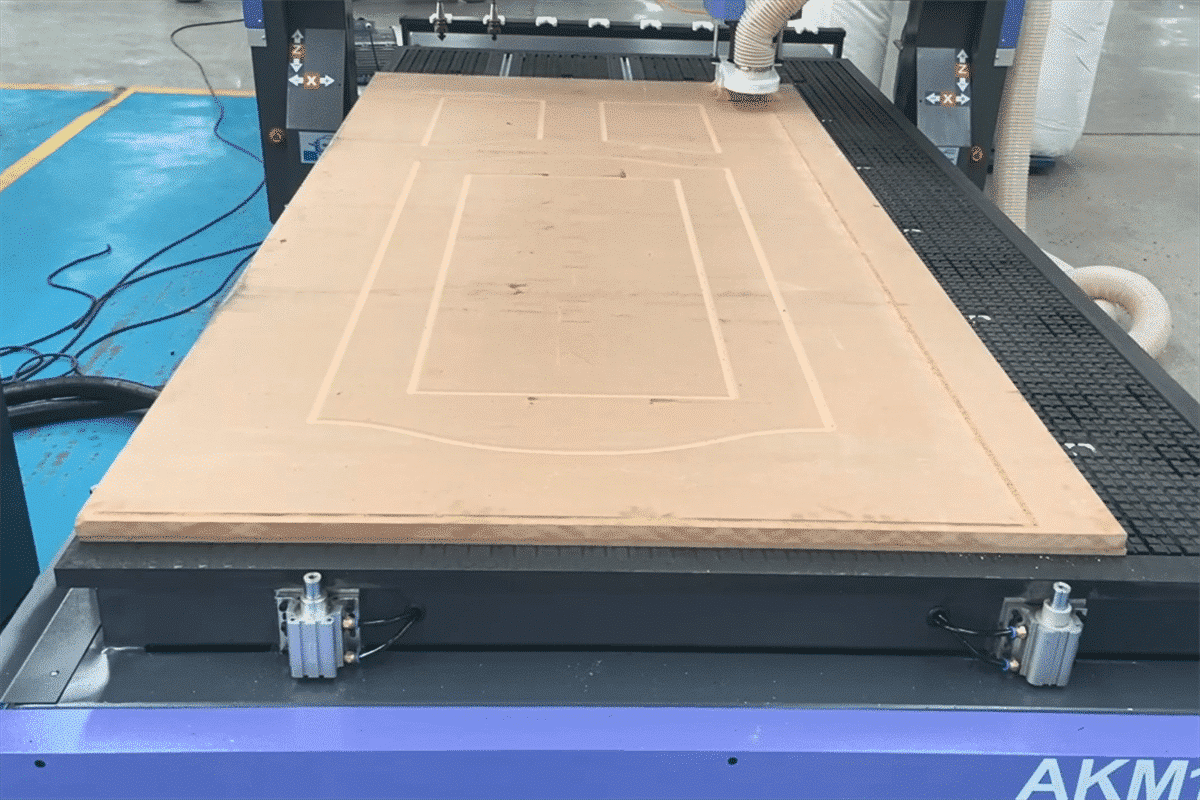
In the ever-evolving landscape of manufacturing and woodworking, efficiency is key to success. Among the many technologies driving this efficiency forward, CNC (Computer Numerical Control) routing stands out for its precision, versatility, and automation capabilities. From crafting intricate designs to mass-producing components, CNC routing has become indispensable in modern production facilities. However, with these advantages come costs, both in terms of time and resources. In today’s competitive market, manufacturers and woodworkers alike are constantly seeking ways to trim expenses without sacrificing quality or productivity.
From material selection to toolpath optimization, there exists a plethora of strategies that can be employed to minimize expenses without sacrificing quality. In this comprehensive guide, we delve into the realm of cost reduction in CNC routing, exploring strategies and best practices to optimize processes, minimize waste, and maximize efficiency. By implementing these tactics, businesses can navigate the challenges of cost management while harnessing the full potential of CNC routing technology.
The Significance of Reduce Costs in CNC Routing
In the CNC routing process, cost reduction stands as a pivotal pursuit for businesses seeking to enhance profitability, competitiveness, and operational efficiency. Understanding the multifaceted significance of cost reduction in CNC routing unveils a spectrum of benefits that extend beyond mere financial gains. Below we clarify the significance of reduction cost in CNC routing.
- Improve Profitability: CNC routing involves various expenses, including machine operation, labor, tooling, and material costs. By reducing these costs, businesses can improve their profit margins and overall profitability.
- Competitive Pricing: Lowering CNC routing costs allows businesses to offer more competitive pricing for their products or services. This can be a key factor in attracting customers and winning contracts in a competitive market.
- Resource Optimization: By minimizing unnecessary expenditures, businesses can optimize the use of their resources, including machinery, manpower, and materials. This ensures that resources are utilized effectively, maximizing output while minimizing waste.
- Increased Efficiency: Streamlining operations, optimizing tool paths, and minimizing material waste all contribute to improved efficiency. This means faster turnaround times for orders and improved productivity.
- Risk Mitigation: High CNC routing costs can pose a risk to a business’s financial health, especially during economic downturns or fluctuations in demand. By reducing costs, businesses can better withstand market volatility and mitigate financial risks.
- Investment in Innovation: Cost reduction frees up capital that can be reinvested in innovation and technology upgrades. This allows businesses to stay ahead of the curve, adopt new technologies, and remain competitive in the long term.
Factors Affecting CNC Routing Costs
From the choice of materials and tooling to machine operation, labor, and beyond, the landscape of CNC routing costs is vast and multifaceted. Recognizing the intricate interplay of these factors is beneficial for businesses to optimize their processes, enhance competitiveness, and maximize profitability. The following is an analysis of the specific factors that affect CNC routing costs:
- Material Costs: The choice of material directly impacts CNC routing costs. Specialized or high-quality materials may come with a higher price tag, increasing overall project expenses. Additionally, inefficient nesting, improper stock utilization, or suboptimal cutting paths can lead to increased waste, thereby adding to project costs.
- Router Bit Cost: The choice of CNC router bit impacts routing costs. High-quality or specialized bits may have a higher upfront cost but can offer better performance and longer tool life. In addition, worn CNC router bits need to be replaced regularly, which increases routing costs.
- Machine Running Time: Machine running time directly affects CNC routing costs. Longer running times result in increased energy consumption, machine wear, and labor expenses.
- Labor Cost: Labor costs encompass wages for machine operators, programmers, and other personnel involved in CNC routing operations. Skilled labor often commands higher wages, impacting overall routing costs.
- Programming Cost: Programming costs include the time and expertise required to develop CNC routing programs. The complexity of the CNC routing program influences programming costs. More intricate designs or customizations may require additional programming time and expertise.
- Maintenance and Upkeep: Regular maintenance and upkeep of CNC routers are beneficial for optimal performance and longevity. Neglecting maintenance can lead to downtime, repairs, and increased costs.
- Energy Consumption: CNC routers consume energy during operation, contributing to operational costs.
- Material Handling and Setup Costs: Time spent on material handling, loading and unloading, and fixture setup directly impacts production efficiency and labor expenses.
- Waste Management Costs: Waste generated during CNC routing, including material scraps and swarf, requires proper disposal or recycling, adding to production costs.
- Software and Technology Costs: CNC routing operations rely heavily on software and technology for design, programming, and control. Initial investments in CAD/CAM software, simulation tools, and CNC machining software contribute to upfront costs. Ongoing expenses may include software updates, licenses, and maintenance fees to ensure compatibility and functionality.
- Quality Assurance Costs: Quality assurance processes are beneficial to ensure that CNC routing outputs meet specifications and standards. Costs associated with quality assurance include inspection equipment, testing procedures, and personnel training.
- Regulatory Compliance Costs: Compliance with regulatory requirements, such as safety standards and environmental regulations, adds to CNC routing costs. Costs may include implementing safety features, conducting audits, and obtaining certifications or permits. Non-compliance can result in fines, legal liabilities, and reputational damage, making regulatory compliance a necessary investment for businesses.
Strategies to Reduce CNC Routing Costs
Reducing CNC routing costs requires a comprehensive approach addressing various manufacturing process aspects. In this section, we explore strategic approaches to reducing CNC routing costs. By adopting these strategic approaches, businesses can effectively reduce CNC routing costs, enhance operational efficiency, and position themselves for success in the competitive manufacturing landscape.
- Efficient Material Selection: Opt for cost-effective materials that meet project requirements without compromising quality. Consider factors such as material availability, price stability, and suitability for CNC routing.
- Optimize Material Usage: Minimize material waste by optimizing nesting layouts, using efficient cutting strategies, and selecting appropriate stock sizes. Consider recycling or repurposing scrap material to reduce waste and lower material costs.
- Invest in High-Quality Tooling: Use high-quality router bits and cutting tools that offer durability and precision. While they may have a higher upfront cost, they can increase efficiency, reduce downtime, and lower long-term tooling expenses by lasting longer and maintaining cutting accuracy.
- Router Bit Path Optimization: Optimize router bit paths to minimize machining time and improve efficiency. Utilize software tools to analyze and optimize tool paths, reducing unnecessary movements and minimizing air cutting.
- Optimize Material Handling and Setup: Minimize setup times and material handling costs by standardizing setups, using quick-change tooling systems, and implementing efficient workflow processes. Invest in ergonomic equipment and tools to improve operator efficiency and safety during material handling.
- Streamline Programming Processes: Invest in advanced CAD/CAM software and automation tools to streamline programming processes and optimize tool paths. Reduce programming time by leveraging pre-built templates, libraries, and macros. Simplify designs where possible to minimize programming complexity and costs.
- Optimizing Machine Energy Consumption: Implement energy-saving measures to reduce machine energy consumption and lower operating costs. Adjust spindle speeds, feed rates, and other machining parameters to optimize energy efficiency. Schedule machining jobs during off-peak hours to take advantage of lower energy rates and reduce overall energy costs.
- Implement Preventive Maintenance: Regularly maintain CNC routers to prevent breakdowns and minimize downtime. Conduct routine inspections, lubrication, and calibration to ensure optimal machine performance and longevity. Addressing minor issues promptly can prevent costly repairs and production delays.
- Train and Empower Operators: Provide comprehensive training to CNC operators and programmers to enhance their skills and efficiency. Empower them to troubleshoot minor issues, optimize tooling setups, and implement efficient machining strategies to improve productivity and reduce errors.
- Focus on Quality Assurance: Implement robust quality control measures to reduce scrap, rework, and defects. Conduct regular inspections and quality checks throughout the production process to ensure compliance with specifications and standards. Investing in quality assurance upfront can prevent costly mistakes and enhance customer satisfaction.
- Monitor and Analyze Costs: Continuously monitor and analyze CNC routing costs to identify areas for improvement and cost-saving opportunities. Track key performance indicators such as material usage, machine uptime, scrap rates, and labor productivity to make data-driven decisions and optimize processes.
- Stay Informed and Innovate: Keep abreast of advancements in CNC technology, materials, and manufacturing techniques. Explore innovative solutions such as additive manufacturing or hybrid machining processes that may offer cost-saving benefits. Continuously seek opportunities to innovate and improve processes to stay competitive in the evolving manufacturing landscape.
Summarize
Mastering the strategy of reducing CNC routing costs is not just about cutting expenses—it’s about optimizing efficiency and maximizing value throughout the manufacturing process. From the initial stages of design optimization to the selection of cost-effective materials and the utilization of advanced machining techniques, every aspect of CNC routing presents opportunities for cost reduction. By implementing the strategies outlined in this article and remaining vigilant in monitoring and optimizing costs, businesses can position themselves for sustained success and profitability in the dynamic world of CNC routing.
AccTek CNC is a well-known CNC router manufacturer in China. With a commitment to delivering high-quality machines and comprehensive technical support, we aim to empower businesses to minimize expenses associated with downtime and inefficiencies. With AccTek CNC as your partner, you can count on efficient equipment and expert technical support to help you achieve your production goals while minimizing costs.