- 8-12 Min Read
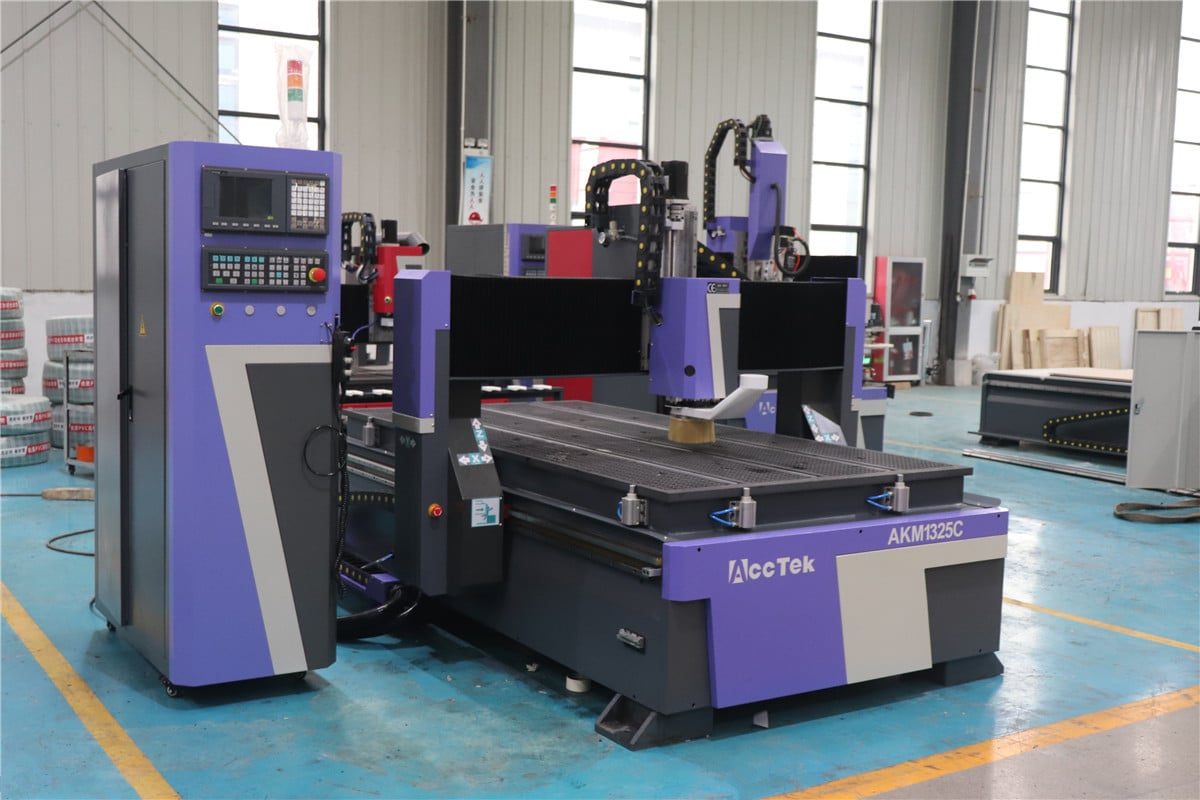
Operating a CNC router is a precise and powerful process, but it requires care, knowledge, and attention to detail to achieve the best results. While CNC routers are designed to streamline complex cutting, carving, and milling tasks, improper use or overlooking essential precautions can lead to suboptimal performance, damaged materials, or costly repairs. More critically, neglecting safety protocols can pose significant risks to operators. Understanding what to avoid when operating a CNC router is just as important as mastering its functions, ensuring both efficiency and safety in your workflow.
This article explores the most common mistakes and bad practices that can arise during CNC router operation. From neglecting maintenance schedules and incorrect tool setups to pushing the machine beyond its capabilities, these oversights can lead to inconsistent output, reduced machine lifespan, and potential workplace hazards. By identifying and avoiding these pitfalls, you can ensure your CNC router delivers the precision and reliability it’s known for, making your projects smoother, safer, and more successful.
Importance of CNC Router Runtime Security
CNC router runtime security is a cornerstone of efficient and safe manufacturing. This aspect of CNC operation involves taking precautions and implementing safeguards to protect both the machine and its operators from potential hazards or failures. Here’s why runtime security is importance:
- Ensuring Operator Safety: Improper handling, unexpected tool breakages, or machine malfunctions can lead to serious accidents. Runtime security measures help minimize these risks.
- Maintaining Machine Integrity: CNC routers are precision machines with complex components that require protection during operation. Runtime security ensures that parts like spindles, tool holders, and linear guides are not damaged due to overloading, tool collisions, or overheating.
- Enhancing Cutting Precision and Quality: Proper runtime security ensures that software settings and toolpaths are error-free, reducing the likelihood of inaccurate cuts or scrapped materials. Security measures also help maintain uninterrupted operations, ensuring high-quality results for intricate designs and detailed machining tasks.
- Reducing Downtime and Maintenance Costs: Unexpected breakdowns or equipment failures during runtime can result in significant downtime and costly repairs. Security measures help prevent these disruptions. By proactively addressing potential issues, runtime security reduces maintenance expenses and maximizes productivity.
- Ensuring Compliance with Safety Standards: Industries that rely on CNC routers often operate under strict safety and regulatory requirements. Implementing runtime security measures ensures compliance with workplace safety standards and reduces the risk of non-compliance penalties. It also mitigates legal and financial liabilities arising from workplace incidents, creating a safer environment for all.
Incorporating robust runtime security measures not only ensures smooth CNC router operations but also provides peace of mind for operators and businesses alike. By prioritizing these practices, users can achieve safer, more efficient, and cost-effective manufacturing.
Common Mistakes in CNC Router Operation
CNC router operation demands attention to detail and adherence to best practices. Mistakes during runtime or setup not only compromise the quality of work but can also damage the machine and create safety hazards. Here’s a deeper exploration of some frequently overlooked mistakes:
Overloading the Machine
Overloading occurs when the machine is pushed beyond its design limits, whether by using oversized tools, cutting excessively hard materials, or setting an aggressive feed rate. Here are the consequences:
- Excessive strain on the spindle and motors, leading to overheating or mechanical failure.
- Increased tool wear and poor cutting accuracy.
- Potential damage to the workpiece, wasting materials.
Ignoring Warning Signals
Machines are equipped with sensors and alarms to signal issues like overheating, low lubrication, or tool wear. Ignoring these signals can escalate minor problems into major breakdowns. Here are the consequences:
- Irreversible damage to machine components.
- Reduced machine lifespan and unexpected downtime.
- Safety hazards for operators.
Improper Chip Management
CNC routers generate chips and debris during operation, especially when cutting wood, plastic, or metal. Poor chip management clogs the workspace and impacts machine performance. Here are the consequences:
- Overheating due to accumulated debris around the tool or spindle.
- Reduced cutting accuracy and tool efficiency.
- Fire hazards in extreme cases.
Incorrect Settings
Errors in settings like spindle speed, feed rate, and cutting depth often stem from a lack of understanding or oversight during programming. Here are the consequences:
- Burn marks, rough edges, or tool breakage due to incorrect spindle speeds.
- Material waste from poorly cut or ruined workpieces.
- Increased wear on machine components.
Using Inappropriate Tools or Materials
Mismatching tools or materials, such as using a dull bit for hardwood or the wrong tool diameter for a specific cut, can compromise performance. Here are the consequences:
- Uneven cuts and wasted material.
- Excessive wear and tear on tools and spindles.
- Increased risk of machine damage.
Skipping Regular Maintenance
Neglecting routine maintenance, such as lubrication, calibration, or cleaning, allows minor issues to escalate unnoticed. Here are the consequences:
- Poor performance and accuracy over time.
- Higher repair costs and longer downtimes.
- Increased likelihood of machine failure during operation.
Failing to Secure Workpieces Properly
Unsecured workpieces can shift during operation due to vibration or cutting forces, leading to inaccuracies and potential machine damage. Here are the consequences:
- Misaligned cuts or ruined workpieces.
- Tool damage from unexpected resistance.
- Safety risks from flying parts.
The above content introduces the common errors that need to be avoided in CNC router operation. By recognizing these pitfalls, operators can take the first step toward safer, more efficient, and higher-quality machining. Next, we will delve into practical strategies to avoid these mistakes, helping you maximize your CNC router’s performance and ensure long-term reliability.
Preventive Measures to Avoid Common Errors in CNC Routers
Implementing preventive measures is key to ensuring the safe, efficient, and reliable operation of CNC routers. Here are actionable strategies to avoid common errors and maintain optimal performance:
Safety Precautions
Safety is paramount in CNC router operations. Following these precautions minimizes risks to operators and equipment.
- Personal Protective Equipment (PPE): Always require operators to wear PPE such as safety goggles, gloves, and ear protection. It is recommended to wear a dust mask when processing materials that produce fine particles.
- Clear Work Environment: Maintain a clean and organized workspace to reduce trip hazards and ensure smooth machine operations. Remove unnecessary tools or materials from the CNC router area.
- Safety Barriers and Guards: Use machine enclosures or protective shields to reduce exposure to high-speed moving parts and cutting debris.
Emergency Protocols
Effective emergency protocols are beneficial to mitigate risks and ensure the safety of operators and equipment during unforeseen situations.
- Emergency Stop Button: Ensure the emergency stop button is easily accessible and functional. Test it regularly to confirm its effectiveness.
- Alarms and Sensors: Use machines equipped with alarms for overheating, tool wear, or misalignment. Address warnings immediately to prevent damage or injury.
- Fire Safety: CNC routers can generate significant heat and sparks, especially when cutting metals or working with flammable materials. Therefore, it is necessary to equip the workplace with fire extinguishers and ensure that operators know how to use them.
- Evacuation Plans: In the event of a major emergency, a clear evacuation plan ensures personnel safety. Emergency exits must be well-marked, unobstructed, and easily accessible, with assembly points designated at a safe distance from the machine area.
Operator Training and Capabilities
A comprehensive training program is the foundation for equipping operators with the knowledge and skills to use CNC routers effectively and safely.
- Initial Training: Provide comprehensive training for new operators, covering machine controls, software operation, tool setup, and safety measures.
- Regular Skill Updates: Conduct periodic training sessions to keep operators updated on new technologies, software features, and best practices.
- Software Proficiency: Ensure operators are proficient in CAD/CAM software to minimize programming errors such as incorrect toolpaths or scaling issues.
- Tool Knowledge: Train operators to select appropriate tools for the material and operation, and to recognize signs of tool wear or damage.
- Problem-Solving Skills: Encourage operators to develop troubleshooting skills to address issues such as tool chatter, poor surface finishes, or alignment problems efficiently.
Maintenance Tips
Routine maintenance is beneficial to prevent downtime and maintain the longevity of the CNC router.
- Daily Cleaning: Remove dust, chips, and debris from the CNC router and surrounding area at the end of each shift. Pay special attention to toolholders, linear guides, and spindle areas.
- Lubrication: Regularly lubricate moving parts, such as rails and ball screws, as per the manufacturer’s guidelines to ensure smooth operation and prevent wear.
- Tool Inspection: Check tools for sharpness and damage before each use. Replace or resharpen tools that are dull to maintain cutting quality and reduce machine strain.
- Cooling System Maintenance: Monitor coolant levels and clean the cooling system periodically to prevent overheating of the spindle and other components.
- Alignment Checks: Periodically calibrate the machine to ensure that all axes are aligned and functioning accurately.
- Software and Firmware Updates: Keep the CNC router’s software and firmware updated to benefit from improved features and bug fixes.
By implementing these detailed preventive measures, you can significantly reduce the likelihood of common CNC router errors. A strong focus on safety precautions, readiness for emergencies, operator competency, and regular maintenance ensures not only smooth operations but also long-term efficiency and machine reliability. These practices collectively enhance productivity and create a safer working environment.
Operational Practices to Avoid Common Errors in CNC Routers
Implementing best practices during CNC router operations can prevent common errors and ensure efficient, safe, and accurate machining. Here are key operational practices to consider:
Best Practices in Operation Process
Effective operating procedures are beneficial to ensuring the safe, accurate, and efficient performance of a CNC router. By adopting systematic approaches to operation, businesses can improve machine reliability, enhance product quality, and ensure a safer working environment for operators.
- Tooling Inspection and Maintenance: Before each operation, check tools for signs of dullness, wear, or damage, as using compromised tools can lead to inaccurate cuts and increase strain on the machine. Use the right tool for the material and application, ensuring it is sharp and clean for optimal performance. After use, clean and store tools properly in a designated area to avoid damage and ensure quick accessibility for future projects.
- Material Preparation: Effective material preparation minimizes errors and ensures smooth operations. Please start by selecting high-quality materials for the intended machining process and ensuring their dimensions match the machine’s capacity. Inspect the material for defects such as warping, cracks, or inconsistencies affecting cutting accuracy. Cleaning the material to remove dust or oils further improves adhesion and ensures better precision.
- Programming and Setup: Double-check CAD/CAM software settings to confirm the correct toolpaths, scaling, and cutting parameters. Simulate the machining process in the software to identify and correct potential errors before running the program on the actual material. Set appropriate spindle speeds, feed rates, and cutting depths that align with the material properties and tool capabilities. Ensure all machine settings and alignments, such as axis calibration and spindle alignment, are verified before starting the operation.
- Monitoring and Supervision: Operators should observe the cutting process closely to identify unusual noises, vibrations, or deviations in performance, which may indicate problems such as tool wear or material inconsistencies. Monitor spindle load, cutting speed, and coolant systems to prevent overheating and ensure smooth operations. Use sensors and alarms to assist in identifying issues in real time. In the event of any anomalies, halt operations immediately, assess the situation, and resolve the issue before proceeding.
Best Practices in Material Handling and Setup
Proper material handling and setup are foundational to achieving consistent and high-quality results with a CNC router. By focusing on these practices, operators can optimize workflow, reduce material waste, and create a safer, cleaner workspace.
- Securing Workpieces: Use appropriate clamping methods, such as mechanical clamps, vacuum tables, or adhesive fixtures, depending on the material and operation. Ensure the workpiece is firmly held in place without obstruction to the cutting path or potential tool collisions. For irregularly shaped materials, custom jigs or fixtures may be necessary to provide stability. Double-check the security of the workpiece before starting the operation, as any movement during cutting can result in inaccuracies or damage to the tooling.
- Material Loading and Unloading: Align the material correctly on the machine’s worktable or fixtures to ensure proper positioning relative to the programmed toolpath. Use alignment tools, stops, or markings to facilitate accurate placement. When handling heavy or large materials, use lifting equipment or work with additional personnel to avoid accidents. After machining, carefully remove the finished workpiece to prevent damage. Establish a workflow that minimizes idle time between loading and unloading to maximize productivity while maintaining safety.
- Dust and Chip Management: Install a dust collection system to capture debris generated during cutting, which reduces the risk of overheating and prevents chips from interfering with the cutting process. Regularly clean the worktable and surrounding area to remove any remaining dust or debris. Use compressed air or a vacuum to clear chips from the cutting zone, but ensure the machine is turned off before cleaning. Effective dust and chip management also protects operators from health hazards associated with inhaling fine particles and keeps the workspace organized for efficient operations.
By adopting these operational practices, CNC router users can significantly reduce errors, improve efficiency, and extend the lifespan of both the machine and its components. These habits not only enhance the quality of work but also create a safer and more productive machining environment.
Summarize
Operating a CNC router effectively requires attention to detail, adherence to best practices, and a commitment to safety. By understanding and avoiding common mistakes, operators can ensure consistent performance and extend the life of their equipment. Implementing proper training, thorough inspections, and robust operational and material handling procedures minimizes errors and creates a safer work environment. Taking the time to prioritize these best practices empowers users to get the most out of their CNC routers and maximize their investment in this versatile technology. You can get more effective methods by reading “CNC Router Safety Operation Guide“.
AccTek CNC, a well-known CNC router manufacturer in China, stands out as a trusted provider for those seeking high-performance and reliable machines. Our machines are designed to minimize maintenance efforts and maximize efficiency, making them a good choice for both beginners and experienced users. AccTek also provides comprehensive training resources and exceptional customer support, enabling users to confidently implement best practices in CNC router operation. Whether for woodworking, metalworking, or intricate design applications, AccTek CNC delivers the tools and expertise to help users optimize their workflows and elevate their productivity.