- 8-12 Min Read
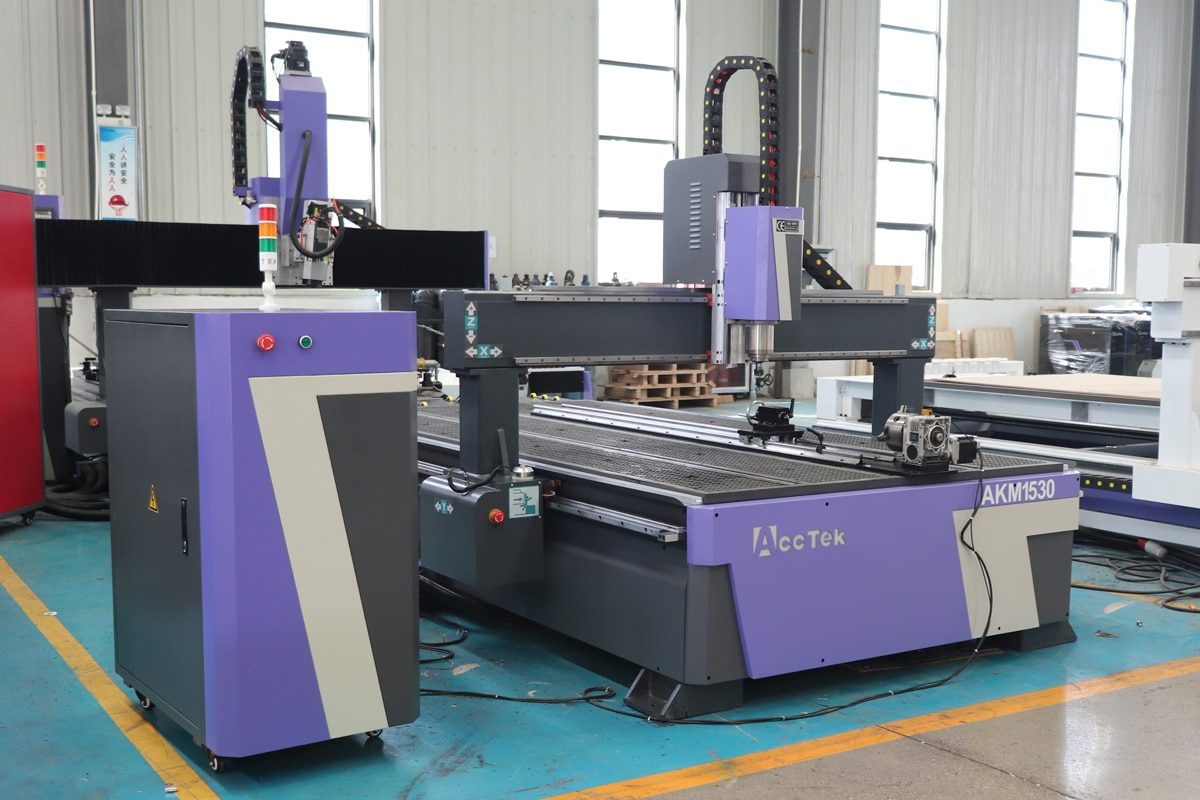
CNC routers are powerful tools used to cut, shape, and carve materials such as wood, plastic, and metal with high precision. While these machines offer great efficiency and accuracy, they also present several safety hazards. Flying debris, loud noise, fine dust particles, and moving mechanical parts can pose risks to the operator if proper precautions are not taken. That’s why wearing the right personal protective equipment (PPE) is necessary when operating a CNC router.
PPE serves as the first line of defense against potential injuries and health issues. Whether you’re a professional working in a production facility or a hobbyist in a small workshop, the right gear can protect your eyes, ears, lungs, hands, and feet from harm. In this article, we’ll go over the essential PPE recommended for CNC router use and explain how each item contributes to a safer and more comfortable working environment.
Understanding CNC Router Hazards
Operating a CNC router involves several potential hazards that, if not properly managed, can pose significant risks to both the operator and the equipment. Recognizing these dangers is the first step toward creating a safer working environment and ensuring proper protective measures are in place. By understanding what can go wrong, operators can better prepare to prevent accidents before they happen.
Mechanical Hazards
Mechanical hazards are among the most immediate and serious risks when operating a CNC router.
- Moving Parts: CNC routers have several moving components, including the gantry, Z-axis assembly, and tool carriage. These parts move rapidly and with significant force during operation to execute precise cuts. If an operator’s hand or clothing comes into contact with these moving parts, it can lead to serious injuries such as crushing, pinching, or entanglement.
- Spindle Speed: The spindle is the heart of the CNC router and rotates often between 8,000 to 24,000 RPM, depending on the material and cutting tool used. Even a minor misalignment or imbalance can create dangerous conditions at such high speeds. A loose tool or unsecured workpiece can be thrown from the machine with great force, potentially striking the operator or causing damage.
- Cutting Tools: CNC routers use various sharp cutting tools to perform material removal. These tools are designed to slice through dense materials with precision, making them inherently dangerous if mishandled. Worn or damaged tools can fracture under stress, sending sharp fragments flying. Improper tool installation or use of incorrect tool types can also lead to breakage or poor cutting performance, increasing the risk of accidents.
Noise Hazards
CNC routers can generate significant noise levels, often exceeding 85 decibels, especially when cutting dense or hard materials. Prolonged exposure to this level of noise without protection can lead to noise-induced hearing loss (NIHL). The noise is typically produced by the CNC router’s motor, spindle, vacuum system, and the cutting process itself. In a busy workshop environment with multiple machines running, the cumulative effect of noise can also cause stress, fatigue, and decreased concentration, which further increases the risk of accidents.
Airborne Hazards
During the cutting, engraving, or milling process, CNC routers produce fine dust and airborne particles, especially when working with materials like wood, MDF, plastics, or composites. These particles can linger in the air and be inhaled by the operator, potentially leading to respiratory issues such as bronchitis, asthma, or long-term lung damage. Some materials, like MDF, contain formaldehyde-based resins, which can be harmful or carcinogenic when inhaled in large amounts. In addition, certain plastics can release toxic fumes when cut at high speeds or temperatures, making proper ventilation and respiratory protection necessary.
Electrical Hazards
CNC routers are complex machines that rely on electrical systems for their motors, control panels, drives, and auxiliary components like vacuum pumps and cooling systems. Electrical hazards may arise from faulty wiring, exposed conductors, improper grounding, or moisture intrusion. Operators may suffer from electric shocks or burns if they accidentally come into contact with live parts. Overloaded circuits or short circuits can also damage the equipment or create safety risks.
Fire Risks
Although CNC routers are not typically considered fire-prone equipment, fire risks do exist, especially when cutting combustible materials like wood, acrylic, or foam. A buildup of fine dust can become highly flammable under the right conditions, particularly when exposed to sparks or high temperatures. Overheated motors, friction from dull tools, or electrical faults can also be sources of ignition. In some cases, poor dust extraction systems allow combustible dust to accumulate inside the machine or around the workshop, increasing the fire hazard.
By identifying these risks early and implementing appropriate safety practices, operators not only protect themselves but also improve workflow efficiency and equipment longevity. Ultimately, knowledge and caution are the most effective tools for staying safe while getting the most out of your CNC router.
Essential Personal Protective Equipment (PPE)
To ensure the safe operation of a CNC router, wearing the appropriate personal protective equipment (PPE) is not just recommended—it’s essential. This section outlines the key types of PPE that should be worn during CNC router use, explaining how each item contributes to a safer working environment.
Eye Protection: Safety glasses or face shields
- Purpose: CNC routers generate flying debris such as wood chips, plastic shavings, and broken tool fragments. Eye protection prevents these particles from causing eye injuries, which can be severe and irreversible. For added coverage, especially in high-speed operations, a full face shield may be used over safety glasses.
- Recommendation: For tasks involving particularly high speeds or materials that produce more debris, a face shield worn over safety glasses offers additional protection. It is important to use equipment that meets ANSI Z87.1 standards to ensure impact resistance and optical clarity.
Hearing Protection: Earplugs or earmuffs
- Purpose: CNC routers can produce high noise levels, particularly when cutting dense materials or running multiple machines. Prolonged exposure to noise over 85 dB can cause permanent hearing damage.
- Recommendation: Earplugs are lightweight and convenient, while earmuffs provide consistent protection and are easier to wear for extended periods. In particularly loud settings, both can be used together for enhanced protection. Selecting products with a sufficient noise reduction rating (NRR) ensures effective sound attenuation.
Respiratory Protection: Dust masks or respirators
- Purpose: Fine dust particles, especially from materials like MDF or composites, can cause respiratory problems over time. Some materials may release toxic fumes when machined, which requires proper filtration.
- Recommendation: A basic N95 mask filters out 95% of airborne particles, while a P100 respirator offers higher filtration efficiency. For work involving fumes or potentially toxic vapors, such as certain plastics, a respirator with organic vapor cartridges is recommended. It’s also important to ensure a proper fit and seal for maximum protection.
Hand Protection: Cut-resistant gloves (when appropriate)
- Purpose: Hands are at risk of cuts from sharp tools, splinters, or jagged materials during handling and setup. Cut-resistant gloves offer protection from sharp tools, splinters, and rough surfaces. However, gloves should never be worn while the CNC router is in operation if there’s any risk of them being caught in rotating or moving parts. This could lead to serious entanglement injuries.
- Recommendation: The best practice is to wear gloves during setup, maintenance, or cleanup, and to remove them when the machine is running. Gloves made with materials such as Kevlar or those with EN 388 cut resistance ratings are commonly used in industrial settings for this purpose.
Protective Clothing: Fitted workwear or long-sleeve shirts
- Purpose: Loose clothing can be dangerous around CNC routers because it can get caught in moving parts. Operators should wear fitted clothing that allows free movement without posing a risk of entanglement. Protective clothing made from durable materials shields the skin from flying debris and minor abrasions.
- Recommendation: In some cases, wearing a protective apron or sleeves can help guard the body from wood dust and sharp edges. Avoid garments with hanging strings, oversized cuffs, or external pockets near the machine. Removing jewelry such as rings, necklaces, and bracelets is also strongly advised.
Foot Protectio: Safety shoes or boots
- Purpose: CNC router work often involves lifting and positioning large or heavy material sheets. There’s a risk of dropping materials or tools, which can cause foot injuries if not properly protected. Additionally, slippery or uneven flooring in workshops can increase the chance of slips, trips, and falls.
- Recommendation: To prevent these injuries, operators should wear steel-toe or composite-toe with slip-resistant shoes that protect the feet from impact and compression. Slip-resistant soles help maintain stability on workshop floors that may be dusty or coated with lubricants.
Using the correct PPE significantly reduces the risks associated with CNC router operation. Each piece—from eye and hearing protection to proper footwear—serves a specific purpose in safeguarding the operator from injury or illness. While PPE cannot eliminate all dangers, it forms a vital part of a comprehensive safety strategy. By consistently wearing the required equipment and maintaining it in good condition, operators can work with greater confidence, efficiency, and peace of mind.
Additional PPE Considerations
While basic PPE like eye, ear, respiratory, hand, and foot protection covers the most common safety needs, there are several additional considerations that can further enhance operator safety when working with CNC routers.
- Hair and Accessory Safety: Long hair can be a serious entanglement hazard around rotating tools and moving parts. Operators with long hair should always tie it back securely or use a cap or hairnet to prevent it from being pulled into the machine. It’s also important to avoid wearing accessories like scarves, dangling earrings, or necklaces, which can pose similar entanglement risks.
- Hearing Protection Regulations: According to occupational safety standards in many countries, hearing protection is required when noise levels reach or exceed 85 decibels (dB) averaged over an 8-hour shift. Employers are often required to conduct noise assessments, provide hearing protection, and implement a hearing conservation program when necessary. Operators should understand these regulations and use properly rated hearing protection to stay within safe exposure limits and avoid long-term hearing loss.
- PPE for Maintenance and Cleaning: Different tasks require different protection levels. For example, during maintenance or tool changes, operators may need to wear thicker gloves, safety aprons, or even protective sleeves. Respirators may also be necessary when blowing out dust from enclosures or emptying dust collection units.
- PPE in Enclosed or Poorly Ventilated Spaces: If the CNC router is used in a small or enclosed area, the accumulation of dust or fumes can pose a serious health risk. In such cases, operators may need to use powered air-purifying respirators (PAPRs) or work in conjunction with a properly installed dust extraction and ventilation system.
- Task-Specific Enhancements: Some CNC operations involve materials that release harmful chemicals, such as cutting certain plastics or composite panels. Operators should consult material safety data sheets (MSDS) and wear chemical-resistant gloves or specialized respirators when needed.
- Training and Fit Testing: PPE is only effective when it fits properly and is used correctly. Operators should be trained on how to wear and adjust their equipment, and respirators should undergo regular fit testing to ensure a proper seal.
These additional considerations help address a wider range of safety scenarios, ensuring that operators are well-protected no matter the task or work environment.
Best Practices for PPE Use
Following best practices for personal protective equipment (PPE) use is beneficial to ensure maximum safety and effectiveness in CNC router operations. PPE alone cannot eliminate hazards, but when used properly, it significantly reduces the risk of injury and long-term health issues. Below are key guidelines for getting the most out of your protective equipment:
- Wear PPE Consistently and Correctly: PPE must be worn at all times when operating or working near the CNC router. Skipping PPE for quick tasks or minor adjustments can still lead to serious accidents. Operators should be trained on how to properly wear each item- for example, ensuring goggles fit snugly, respirators form a proper seal, and gloves are appropriate for the task and machine status.
- Inspect PPE Before Each Use: Before every shift or session, all PPE should be inspected for damage, wear, or contamination. Look for cracks in safety glasses, clogged respirator filters, worn-out gloves, or flattened earmuffs. Damaged PPE should be replaced immediately, as compromised equipment may provide little to no protection.
- Maintain and Store PPE Properly: After use, PPE should be cleaned (if applicable) and stored in a designated, clean, and dry area away from dust, chemicals, or direct sunlight. This helps prolong its lifespan and ensures it’s ready for the next use. For example, respirators should be stored in sealed containers to prevent dust buildup, and hearing protection should be kept in clean cases to maintain hygiene.
- Choose the Right PPE for the Task: Not all PPE is suitable for every situation. Operators must select PPE based on the materials being processed, the type of tooling used, and the environment. For example, more advanced respiratory protection may be needed when cutting plastics that release fumes, while thicker gloves may be needed during cleanup rather than active machine operation.
- Receive Proper Training: All CNC router operators should receive training not only on machine safety but also on PPE usage. This includes understanding the purpose of each type of PPE, how to wear it correctly, how to inspect it, and when it is required. Training should also cover the limitations of PPE and when to replace it.
- PPE Compliance Policy: In addition to technical instructions, workshops should have a clearly defined PPE compliance policy outlining mandatory usage rules, consequences of non-compliance, and procedures for reporting damaged or missing gear.
- Encourage a Safety-First Culture: Beyond individual responsibility, employers and workshop managers should promote a culture where safety and PPE use are a priority. Posting reminders, offering refresher training, and ensuring easy access to replacement PPE are good ways to support consistent and proper use.
Implementing these best practices helps ensure that PPE fulfills its intended role in protecting operators and contributes to a safer, more productive work environment.
Summarize
Operating a CNC router involves exposure to various hazards, ranging from flying debris and loud noise to fine dust and moving mechanical parts. Wearing the appropriate personal protective equipment (PPE) is beneficial for minimizing these risks and ensuring a safe. However, safety doesn’t stop at simply wearing gear—regular equipment maintenance, proper machine setup, and a clear understanding of safe operating procedures are equally important. By making PPE a standard part of every CNC router task, operators can work confidently, protect their health, and maintain a productive workspace. Continue reading the “CNC Router Safety Operation Guide” for more helpful suggestions.
AccTek CNC is a professional CNC router manufacturer known for providing high-quality machines in a wide range of models to suit different production needs. Whether you’re handling wood, plastic, or metal, AccTek offers reliable, precision-engineered routers designed for efficiency and long-term performance. For businesses seeking dependable CNC routing solutions backed by strong technical service, AccTek CNC is a trusted choice.