- 8-12 Min Read
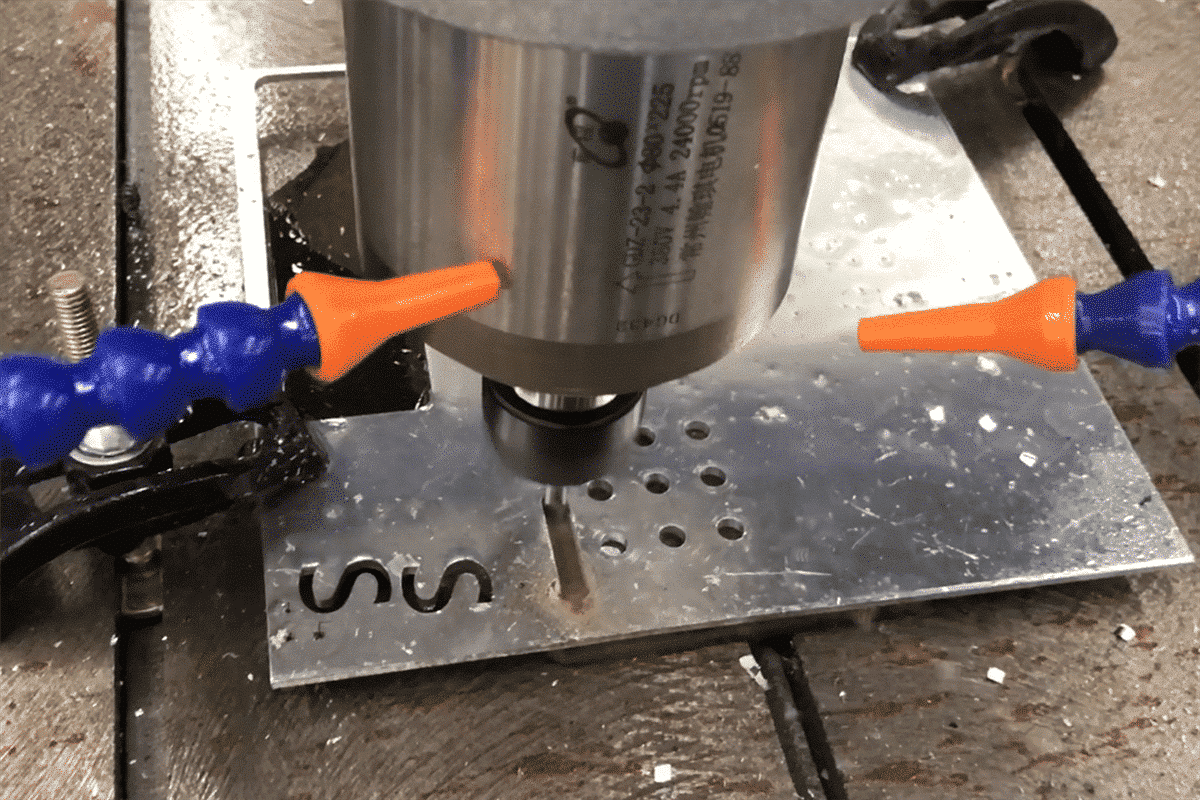
CNC routers have become essential tools in manufacturing, known for their ability to accurately and efficiently carve, cut, and shape a wide range of materials. While these machines are often associated with wood, plastics, and composites, they can also handle a wide range of metals. However, understanding which metals are best suited for CNC routing is key to achieving optimal results, as each metal’s properties influence cutting speed, tool wear, and final product quality.
Not all metals are equally compatible with CNC routers, and factors like hardness, density, and thermal conductivity must be carefully considered. Softer metals are often favored for their machinability and versatility, while harder metals present unique challenges and opportunities. In this article, we’ll explore the types of metals that CNC routers can cut and analyze the factors that influence CNC router metal processing. Whether you’re a seasoned machinist or new to metalworking with CNC routers, this guide will help you make informed decisions tailored to your specific needs and goals.
Understanding CNC Router Functions
CNC routers are dynamic tools capable of performing a wide range of functions that extend far beyond basic cutting. At their core, these computer-controlled machines excel at precision cutting and shaping, allowing users to create complex patterns, intricate designs, and precise cuts with minimal manual effort. Here is a detailed introduction to its functions:
Precision Cutting and Shaping
CNC routers excel in precision cutting, offering unmatched accuracy and repeatability in shaping a wide range of materials. By relying on computer-guided commands, these machines produce complex patterns, tight tolerances, and intricate cuts that would be challenging to achieve manually. Precision cutting enables users to create highly detailed designs, components, and products while minimizing errors and material waste. In addition, CNC routers offer remarkable plasticity in their application, as they can handle diverse materials such as wood, plastics, metals, and composites. This adaptability allows users to transition seamlessly between different projects and industries.
Milling, Engraving, and Carving
Beyond simple cuts, CNC routers excel at milling, engraving, and carving. Milling involves removing layers of material from a workpiece to create three-dimensional objects, complex geometries, and custom shapes. CNC routers’ high-speed rotating tools can handle both rough and fine milling, enabling precise material removal and detailed designs. Engraving and carving further highlight the CNC router’s capabilities, as it can add intricate surface designs, text, or patterns to materials. This makes CNC routers popular for applications such as sign-making, decorative panels, and custom parts where artistic detailing or branding elements are essential. With the ability to adjust cutting depths and angles, users can achieve stunning visual and tactile details, enriching the value of their projects.
Drilling and Hole-Making
CNC routers also offer exceptional drilling and hole-making capabilities, making them suitable for creating holes with precise diameters and depths. Whether creating holes for assembly, fasteners, or wiring channels, these machines ensure exact positioning and uniform depth. Automated drilling eliminates the need for manual measurements and adjustments, increasing production speed and minimizing errors. CNC routers are widely used in furniture manufacturing, cabinetry, and more, where precise hole-making is necessary for reliable assembly and performance. This function, combined with the machine’s ability to punch holes through various materials, expands its utility and streamlines workflows for industrial and artisanal tasks alike.
By understanding these functions, users can maximize the potential of CNC routers, leveraging their capabilities to create detailed, high-quality, and innovative products. Whether for industrial manufacturing, artistic creations, or complex engineering projects, CNC routers serve as powerful tools that enhance productivity, accuracy, and creativity in modern machining.
Common metals suitable for CNC routing
CNC routers are capable of machining a variety of metals, each with distinct properties and applications. Here are some of the most common metals suitable for CNC routing:
- Aluminum: Aluminum is a popular choice for CNC routing due to its lightweight properties, excellent machinability, and versatility. It is relatively soft compared to other metals, allowing for faster cutting speeds and less wear on tools.
- Mild Steel: Mild steel offers a balance of strength, affordability, and ease of machining, making it a common material in structural components and industrial parts. CNC routing of mild steel requires tools and settings designed to handle its hardness and durability, but it can yield accurate and robust parts when done correctly.
- Stainless Steel: Stainless steel is prized for its strength, corrosion resistance, and aesthetic appeal. While it is harder to machine than softer metals, CNC routers equipped with high-speed cutting tools and proper cooling can produce precise and high-quality cuts in stainless steel.
- Brass: Brass is another metal well-suited for CNC routing because of its machinability, strength, and corrosion resistance. It is often used for applications requiring decorative elements and fittings. Brass’s smooth finish and ease of cutting make it a popular choice for intricate designs and detailed engravings.
- Copper: Copper is known for its excellent electrical and thermal conductivity. CNC routers can machine copper effectively, although care must be taken due to its tendency to generate heat during cutting. Proper cooling and tool selection are beneficial when routing copper to achieve clean cuts and precise results.
- Iron: Iron is a widely used metal in CNC routing due to its strength, durability, and versatility. Although iron can be more challenging to machine than softer metals due to its hardness and potential brittleness, CNC routers equipped with the right tools and settings can produce accurate and robust parts.
- Titanium: Titanium is a strong, lightweight metal. CNC routing of titanium requires specialized tools and techniques due to its toughness and tendency to retain heat during cutting. However, when properly machined, titanium offers exceptional strength-to-weight ratios and durability.
- Nickel Alloys: Nickel alloys offer resistance to heat, corrosion, and wear, making them suitable for high-performance applications in harsh environments. CNC routing of nickel alloys can be challenging due to their hardness, but with the right tooling and cutting strategies, precise and durable parts can be manufactured.
- Tungsten: Tungsten is one of the hardest and densest metals available, known for its extraordinary strength, wear resistance, and high melting point. Machining tungsten with a CNC router can be challenging due to its hardness and brittleness, requiring specialized carbide tools and careful control of cutting parameters.
By selecting the appropriate metal for CNC routing and considering the material’s properties, users can achieve accurate, efficient, and high-quality machining results across various projects. Whether for intricate artistic work or demanding industrial components, CNC routers offer the flexibility and precision needed to meet diverse machining requirements.
Factors affecting CNC router metal cutting
When cutting metal with a CNC router, several key factors influence the overall quality, precision, and efficiency of the process. Understanding and managing these factors can significantly impact the outcome, ensuring a smooth operation and consistent results. Here are the primary factors that affect metal CNC router cutting:
Material Hardness and Composition
Different metals exhibit distinct properties that can affect cutting performance. Softer metals, such as aluminum and brass, are generally easier to cut and produce less tool wear, while harder metals like stainless steel, titanium, and tungsten present greater challenges. Metals with high hardness require specialized cutting tools with robust materials, such as carbide or diamond coatings, to maintain precision and tool longevity.
The composition of the metal, including its alloying elements, can influence machinability, brittleness, and heat resistance, further affecting the cutting performance. Materials that generate a lot of heat or have high thermal conductivity may require cooling systems to prevent tool wear and ensure consistent cutting quality. Understanding the specific properties of the material is beneficial to selecting appropriate tools, speeds, and feeds for optimal results.
Cutting Parameters
Cutting parameters, including cutting speed, feed rate, and depth of cut, significantly affect CNC router performance when machining metal. To cut metal effectively, these parameters must be carefully balanced. Higher cutting speeds can lead to faster material removal but may generate more heat and wear out tools quickly. Conversely, lower speeds can reduce heat but may slow down the process.
The feed rate must also be adjusted based on the metal’s hardness to prevent tool damage, while the depth of cut should be optimized to manage tool stress and avoid excessive vibrations. Taking a deep cut can lead to tool stress, excessive vibrations, and uneven cuts, while taking shallow passes can help maintain tool integrity and achieve a better finish. Fine-tuning these parameters is beneficial to achieve precision and consistent surface finishes.
Machine Rigidity and Stability
The rigidity and stability of a CNC router directly influence its ability to cut metals accurately. A machine with a rigid frame, sturdy construction, and stable motion systems can better resist deflection, vibrations, and tool chatter during metal cutting. Insufficient rigidity or instability can lead to inaccuracies, uneven cuts, and tool wear.
For optimal metal cutting performance, CNC routers designed for metalworking often feature reinforced frames, high-torque spindles, and precision linear guides. Ensuring machine stability also improves surface finish quality and helps maintain consistent dimensional accuracy.
Heat Generation
Cutting metal with a CNC router generates significant heat. This is caused by the friction between the cutting tool and the metal surface and the accumulation of chips around the cutting area. Excessive heat can lead to thermal expansion of the workpiece, tool wear, and poor surface finishes. Managing heat generation is beneficial to maintaining cutting precision and prolonging tool life.
Coolants, air blasts, and lubricants are commonly used to reduce heat buildup, improve chip evacuation, and enhance tool performance. Effective heat management is particularly important for metals with high thermal conductivity, such as copper, and for operations involving deep cuts or prolonged cutting times. By minimizing heat accumulation, users can achieve clean cuts and avoid damage to the material and tools.
By considering and optimizing these factors, users can enhance the performance and precision of CNC routers when cutting metal, leading to consistent, high-quality results and prolonged tool and machine life.
Safety precautions for CNC router metal cutting
When using a CNC router for metal cutting, it is essential to adhere to safety precautions to protect operators and ensure a smooth and hazard-free operation. Metal cutting involves high speeds, heat generation, and the potential for flying debris, making safety a top priority. Here are key safety measures to consider:
Wear Appropriate Personal Protective Equipment (PPE)
- Eye Protection: Always wear safety goggles or a face shield to protect your eyes from flying metal chips, dust, and sparks.
- Hearing Protection: CNC routers can produce high noise levels during metal cutting. Use earplugs or noise-canceling earmuffs to prevent hearing damage.
- Respiratory Protection: Cutting metals may generate fine dust or fumes. Wear a suitable dust mask or respirator to protect your lungs.
- Gloves: Use cut-resistant gloves for handling metal parts but avoid wearing loose gloves while operating the machine to prevent entanglement.
Ensure Proper Machine Setup and Maintenance
- Secure Workpieces Properly: Use clamps, vacuum tables, or other workholding devices to prevent movement during cutting. A securely held workpiece reduces vibration and prevents accidents.
- Check Tooling and Bits: Ensure that cutting tools are sharp, properly installed, and suitable for the metal being cut. Dull or damaged tools can break or cause rough cuts.
- Inspect the Machine: Regularly check the CNC router for loose bolts, worn parts, and any potential mechanical issues that could lead to malfunctions during operation.
- Inspect Cords and Connections: Check power cords, connections, and grounding to prevent electrical hazards. Use properly rated outlets and avoid overloading circuits.
- Turn Off Power When Adjusting Tools: Before changing tools, adjusting the workpiece, or performing maintenance, ensure the machine is powered off and disconnected.
Follow Correct Operating Procedures
- Set Appropriate Cutting Parameters: Incorrect speeds, feeds, or depths of cut can generate excessive heat, causing tool breakage or fire hazards. Always use recommended settings for the specific metal being machined.
- Use Coolants and Lubricants: Apply coolant or lubricant to reduce heat buildup, minimize tool wear, and improve cutting performance.
- Keep the Work Area Clean: Ensure that metal chips, debris, and dust are regularly removed to prevent build-up around the machine. Clutter can cause accidents or interfere with machine operation.
- Avoid Manual Intervention During Operation: Do not attempt to manually clear chips or adjust the workpiece while the machine is in motion. Wait for the machine to stop completely before making any adjustments.
- Monitor the Cutting Process: Never leave the machine unattended while it is in operation. Monitor the cutting process to detect any signs of overheating, tool wear, or irregularities that could pose a safety risk.
Other Safety Precautions
- Use Safety Shields and Guards: Where possible, use protective guards or enclosures to contain metal chips and flying debris. This prevents projectiles from causing injury to operators and bystanders.
- Emergency Stop Protocols: Ensure that all operators are familiar with the location and use of the emergency stop button on the CNC router. This allows for immediate shutdown in case of an emergency.
- Training and Operator Awareness: Ensure that all operators are properly trained in CNC router operation, including safety protocols and emergency procedures. Encourage ongoing training to stay informed about new safety practices and machine capabilities.
By implementing these safety measures, CNC router operators can minimize risks and ensure a safe working environment when cutting metals. Proper precautions not only protect operators but also contribute to a more efficient and productive machining process.
Summarize
CNC routers offer versatile capabilities for cutting a wide range of metals, from aluminum and brass to more challenging materials. However, achieving optimal results requires a deep understanding of each metal’s properties and the appropriate cutting techniques, tools, and settings. By leveraging the capabilities of CNC routers and carefully selecting suitable metals, users can unlock new possibilities in metalworking, creating intricate designs and high-quality products. Whether for large-scale industrial applications or custom creations, CNC routers continue to expand the boundaries of modern metalworking. Continue reading “What Materials Cannot CNC Router Cut?” and you can learn the limitations of CNC router cutting.
For those seeking a reliable and versatile CNC router for metal cutting, AccTek CNC stands out as a well-known and trusted manufacturer in China. With a strong reputation for producing high-precision, durable, and innovative CNC routers, AccTek’s machines are designed to handle a wide range of metals, including aluminum, brass, stainless steel, and more. Our metal CNC routers are equipped with robust features such as high-torque spindles, advanced motion systems, and user-friendly control interfaces, ensuring superior performance and accuracy. With exceptional pre- and post-sales support, AccTek is dedicated to helping users maximize productivity and unlock the full potential of their metalworking projects.