- 7-11 Min Read
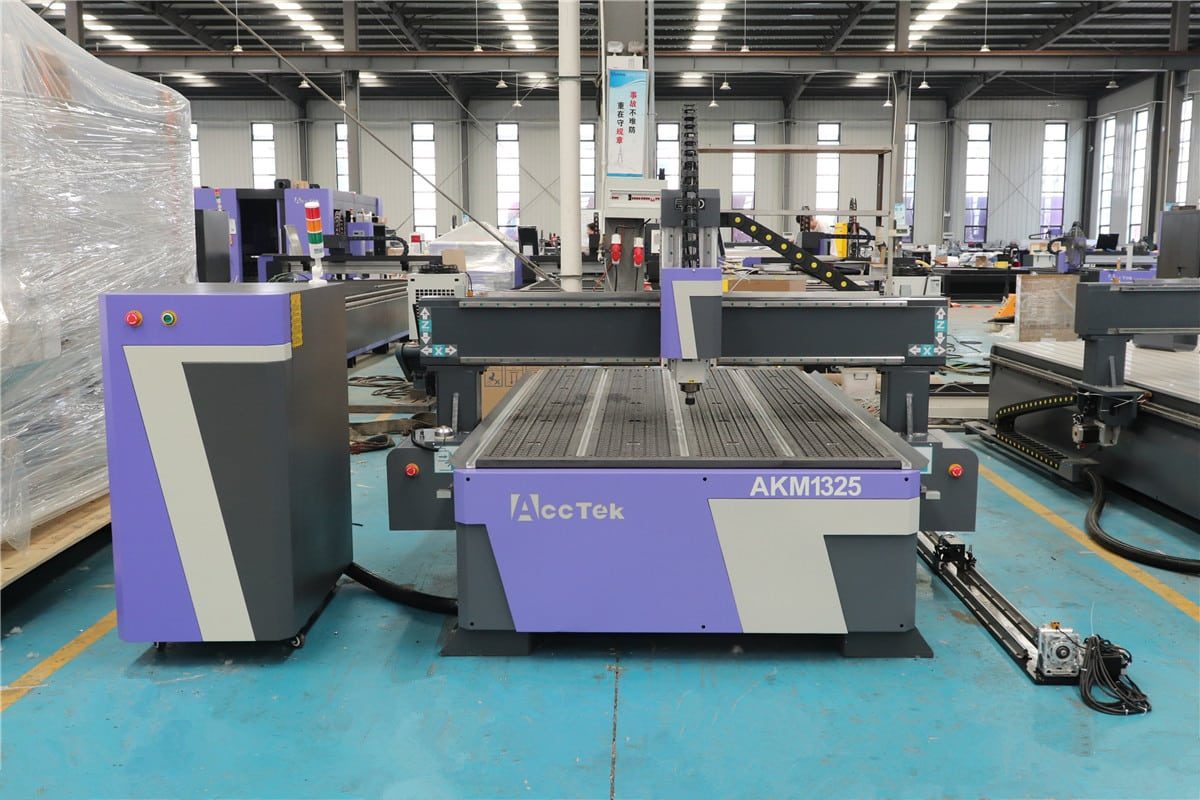
CNC routers are versatile machines capable of cutting and shaping a wide variety of materials with precision and efficiency. They are widely used in industries ranging from woodworking to metalworking and beyond. These machines are capable of executing complex designs with high accuracy, catering to both hobbyists and professionals alike. However, while CNC routers are incredibly adaptable, they are not without their limitations. There are certain materials that these machines cannot cut effectively, either due to the material’s inherent properties or the limitations of the CNC router’s design and capabilities.
In this article, we will explore the types of materials that pose challenges for CNC routers, the reasons behind these limitations, and alternative methods for working with such materials. For anyone using a CNC router, knowing these limitations can help prevent potential damage to the machine and ensure operator safety. Whether you are a seasoned machinist or just beginning your journey with CNC technology, this guide provides valuable insights into the boundaries of CNC router capabilities.
Understanding CNC Router
A CNC router is a computer-controlled cutting machine used to carve, cut, and shape various materials. “CNC” stands for “Computer Numerical Control,” which refers to the automation of machine tools by means of computers executing pre-programmed sequences of machine control commands. CNC routers are versatile tools that can work with a wide range of materials, here we learn the basics of it.
Working Principle of CNC Routers
A CNC router operates by automating the movement and control of cutting tools using a computer. The process begins with a digital design, typically created using CAD (Computer-Aided Design) software. This design is then translated into G-code, a programming language that instructs the CNC router on how to execute the cuts. The machine’s control system interprets the G-code and directs the movement of the machine’s components, including the gantry, spindle, and work table.
The working principle involves three main axes: X, Y, and Z. The X and Y axes control the horizontal and vertical movement across the work surface, while the Z-axis manages the depth of the cut. The spindle, which holds the cutting tool, rotates at high speeds to carve, cut, or engrave the material according to the programmed design. Precision motors and sensors ensure that the machine operates accurately and consistently, allowing for complex and detailed cuts.
Materials That Can Be Cut by CNC Routers
CNC routers are highly versatile and capable of cutting a wide range of materials. The choice of material depends on the specific capabilities of the CNC router and the intended application. Common materials include:
- Wood: One of the most frequently used materials, wood can be easily cut, carved, and shaped by CNC routers. This includes various types of hardwood, softwood, plywood, and MDF (medium-density fiberboard).
- Plastics: CNC routers can work with various plastics, such as acrylic, polycarbonate, PVC, and ABS. These materials are commonly used in sign-making, product prototypes, and custom parts.
- Metals: While CNC routers are not typically as powerful as CNC mills, they can still carve softer metals like aluminum, brass, and copper. With appropriate tooling and settings, more advanced CNC routers can handle harder metals, though this requires careful consideration of feed rates and tool selection.
- Composites: Composite materials, such as carbon fiber and certain types of laminates, can also be cut with CNC routers. These materials are often used in the automotive and sporting goods industries.
- Foam: Lightweight and easy to machine, foam materials like expanded polystyrene (EPS) and polyurethane foam are used for creating models, prototypes, and packaging.
The versatility of CNC routers in handling these diverse materials makes them valuable tools across various industries, from furniture manufacturing to sign-making. However, the machine’s configuration, spindle power, and tooling options must be considered to ensure optimal performance and quality when working with different materials.
Limitations of CNC Router Cutting
While CNC routers are versatile and capable machines, they do have certain limitations, especially when it comes to specific types of materials. Here are the key limitations of CNC router cutting, focusing on materials that pose challenges or are unsuitable for CNC routing:
- Hardened Metals: CNC routers are generally not equipped to cut hardened metals like hardened steel or titanium. These metals require significant cutting force, high rigidity, and specialized cutting tools, which most CNC routers lack. The high hardness of these materials leads to rapid tool wear and difficulty in achieving precision cuts.
- Glass and Ceramics: Glass and ceramics are brittle materials that can easily crack or shatter under the mechanical stresses applied by CNC routers. The vibrations and cutting forces generated during the CNC routing process are often too harsh, causing material failure.
- Stone and Granite: Stone and granite are extremely hard and dense materials that pose significant challenges for CNC routers. These materials require diamond-tipped tools and significant cutting force, which can exceed the capabilities of standard CNC routers. Additionally, the abrasive nature of stone and granite can cause rapid tool wear, making the process inefficient and costly.
- Rubber and Soft Materials: Cutting rubber and other soft materials with a CNC router can be problematic due to their flexibility and lack of resistance. These materials tend to deform under the cutting tool, leading to uneven cuts and poor-quality edges. Moreover, securing soft materials on the work table can be challenging, as they may not stay in place during the cutting process.
- Fragile and Thin Materials: Such as delicate plastics, thin metals, and certain foils, can be easily damaged by the forces exerted by a CNC router. The CNC router’s cutting tool can cause tearing, bending, or warping of these materials, especially if they are not properly supported.
- Highly Wear-Resistant Materials: Such as certain ceramics, composite materials with hard fillers, or abrasion-resistant metals, pose a challenge for CNC routers due to their ability to rapidly wear down cutting tools. The high abrasiveness of these materials leads to frequent tool changes, increased operational costs, and reduced cutting efficiency. CNC routers, which typically use high-speed rotary tools, are not ideal for such applications, where more durable cutting methods and tools are necessary.
While CNC routers are highly capable machines, they are not suitable for all materials. The limitations of CNC router cutting are largely influenced by the material’s hardness, brittleness, flexibility, and abrasiveness. Understanding these constraints helps in choosing the right tool for the job and ensures the quality and safety of the cutting process.
Factors that Affect CNC Router Limitations
The cutting material limit of a CNC router is influenced by several key factors that determine the machine’s ability to process various materials. These factors include:
- Spindle Power and Speed: The power and speed of the spindle are critical factors. The spindle must generate sufficient torque and rotational speed to cut through different materials. Higher spindle power allows the machine to handle tougher and denser materials, such as metals. Conversely, materials like wood and plastics can be processed with lower power levels. The spindle speed (RPM) also needs to be adjusted according to the material to avoid issues like burning, melting, or poor finish.
- Tooling and Bit Selection: The type of cutting tool or bit used greatly affects the material that can be cut. Different materials require specific tools, such as carbide, diamond, or high-speed steel bits, each with unique properties suited to certain materials. For instance, diamond-coated bits are necessary for cutting extremely hard or abrasive materials, while specialized bits are needed for cutting soft or brittle materials.
- Machine Rigidity and Stability: The structural rigidity and stability of the CNC router’s frame and gantry affect the processing effect of different materials. Machines with higher rigidity can maintain accuracy and precision when cutting harder materials, as they reduce vibrations and deflections. Less rigid machines may struggle with these materials, leading to inaccuracies and potential damage.
- Feed Rate and Cutting Speed: The feed rate (the speed at which the material is fed into the cutting tool) and the cutting speed (the speed of the tool’s movement along the material) must be adjusted according to the material being processed. Incorrect feed rates and cutting speeds can lead to issues such as tool wear, material damage, or suboptimal cut quality. Softer materials typically allow for higher feed rates, while harder materials require slower, more controlled feeds.
The material limits of a CNC router are determined by a combination of machine specifications, tooling options, and parameter settings. Understanding and optimizing these elements can help expand the range of materials a CNC router can effectively process.
Alternative Cutting Methods
When CNC routers are not suitable for cutting certain materials or achieving specific results, various alternative cutting methods can be employed. Each method has unique advantages and is suited for particular applications or materials. Here are some common alternative cutting methods:
Laser Cutting
Laser cutting utilizes a concentrated laser beam to melt, burn, or vaporize material, achieving precise and clean cuts. The laser source generates a high-energy beam, which is focused through optics and directed at the material’s surface. The energy from the laser beam rapidly heats the material, causing it to melt or vaporize along the intended cut path.
Laser cutting is known for its high precision and ability to produce intricate designs with minimal material waste. It is effective for a variety of materials, with fiber laser cutters being particularly good at cutting metals, while CO2 laser cutters work well in cutting soft materials like cloth and leather. Laser cutting can handle both thin and thick materials, depending on the power of the laser.
Water Jet Cutting
Water jet cutting is a versatile cutting process that uses a high-pressure jet of water, often mixed with abrasive particles, to cut through a wide range of materials. The water is pressurized to extremely high levels and directed through a small nozzle, creating a thin, focused stream capable of cutting through materials with precision.
The addition of abrasive particles, such as garnet, enhances the cutting power, allowing water jet cutting to handle tough materials like metal, stone, glass, ceramics, and composites. One of the key advantages of water jet cutting is that it produces no heat-affected zone (HAZ), making it ideal for materials sensitive to heat or those that require a smooth, clean edge.
Plasma Cutting
Plasma cutting is a process that uses an electrically conductive gas, or plasma, to cut through electrically conductive materials. It involves creating an electrical arc between an electrode and the workpiece, ionizing the gas and forming plasma. This plasma jet is directed through a nozzle at high speeds, reaching temperatures that can exceed 20,000°C. The intense heat melts the material, while the high-velocity gas blows away the molten metal, creating a cut.
Plasma cutting is especially effective for cutting metals like steel, stainless steel, and aluminum. It offers fast cutting speeds and is capable of handling thick materials, making it ideal for industrial applications, metal fabrication, and automotive repair.
CNC Milling
CNC milling is a machining process that uses rotary cutters to remove material from a workpiece, creating a desired shape or surface. Unlike CNC routers, which are generally used for softer materials, CNC mills are more robust and capable of handling a wider range of materials, including hard metals. The process involves securing the workpiece on a movable table and using rotating cutting tools to machine the material along multiple axes.
CNC milling can perform a variety of operations, such as drilling, tapping, contouring, and slotting, with high precision and repeatability. It is suitable for creating complex shapes and intricate details and can be equipped with various tools and attachments to meet specific machining needs.
Each of these alternative cutting methods has its own set of advantages and limitations, making them suitable for different applications and materials. The choice of method depends on factors such as the type of material, thickness, precision requirements, and production volume.
Summarize
Knowing the capabilities and limits of CNC routers, along with the availability of alternative technologies, empowers users to make informed decisions and expand the range of materials and designs they can work with. This knowledge not only enhances the quality of the final products but also optimizes the cutting process, making it safer and more cost-effective. Although CNC routers have certain limitations for certain materials, they are still one of the most important tools in the field of industrial processing. Click on What Industries Are CNC Routers Used In is used to learn about its use and the range of materials it processes.
AccTek is a reputable brand specializing in the production of high-quality CNC routers tailored to meet diverse material processing needs. Whether you’re working with wood, foam, plastic, metal, or stone, AccTek offers specialized CNC routers designed to handle the unique requirements of each material. We understand that selecting the right CNC router can be challenging, especially when considering the specific characteristics of different materials. Our team of experts is available to provide professional advice and help you choose the most suitable machine for your needs. If you’re unsure which machine type is best for your project, we invite you to contact us online for personalized recommendations and guidance. Trust AccTek to deliver solutions and support for all your CNC routing requirements.