- 6-10 Min Read
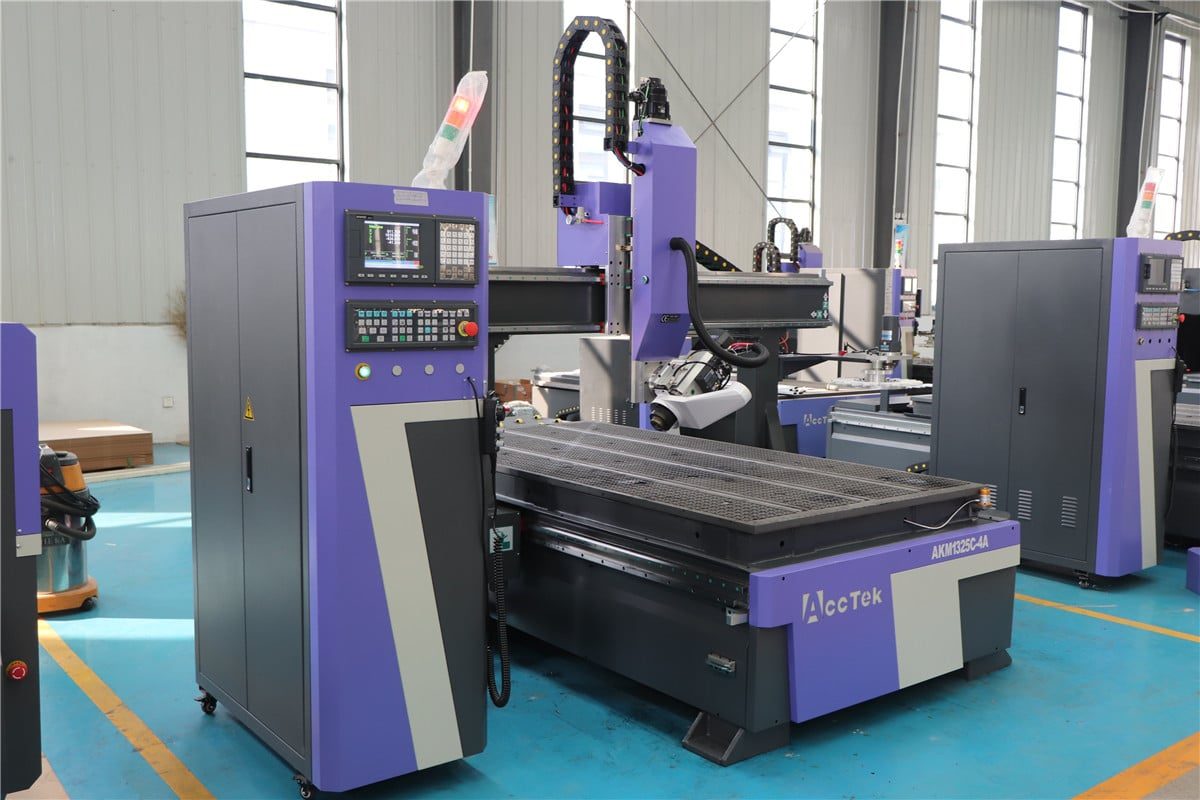
Computer Numerical Control (CNC) routers have revolutionized the manufacturing and woodworking industries by offering precise, automated cutting and shaping of various materials. These versatile machines, capable of transforming digital designs into physical products, have become indispensable in a wide range of applications, from custom furniture creation to intricate sign making. However, to achieve optimal performance and longevity from a CNC router, it is crucial to operate it in an environment tailored to its specific requirements.
This article delves into the key environmental factors necessary for running a CNC router effectively. From temperature and humidity control to workspace layout and dust management, we will explore how each aspect influences the operation and maintenance of CNC routers. Whether you are a hobbyist, a small business owner, or part of a large manufacturing operation, understanding these environmental requirements is beneficiall to maximize the benefits of your CNC router investment. Read on to learn how to create an ideal environment for increased precision, productivity, and safety in CNC routing.
The Importance of Environment to Running CNC Router
Precision and Accuracy
- Temperature Stability: Fluctuations in temperature can cause materials to expand or contract, affecting the dimensions and tolerances of machined parts. Maintaining a stable temperature ensures consistent results and high precision.
- Humidity Control: High humidity can lead to rust and corrosion of machine components, while low humidity can cause static electricity issues. Controlling humidity levels helps protect the CNC router and ensures reliable operation.
Machine Longevity and Reliability
- Cleanliness: Dust and debris can accumulate on sensitive machine components, leading to premature wear and reduced lifespan. Proper dust management and regular cleaning extend the longevity of the CNC router.
- Power Supply Stability: CNC routers require a stable power supply to operate correctly. Voltage fluctuations or power surges can damage electronic components and disrupt operations. A stable power supply, complemented by surge protectors, ensures reliable performance and protects the machine from electrical damage.
Operator Safety and Efficiency
- Workspace Layout: An organized workspace with sufficient clearance around the CNC router allows for safe operation, easy maintenance, and efficient material handling. A cluttered or poorly laid out workspace can lead to accidents and inefficiencies.
- Ventilation: Good ventilation helps dissipate heat generated during operation and maintains a comfortable working environment for operators. Proper airflow also contributes to the longevity of electronic components by preventing overheating.
Quality of Outputs and Productivity
- Environmental Control: Controlling factors like temperature, humidity, and cleanliness directly impact the quality of machined parts. Consistent environmental conditions ensure consistent results and minimize rework, enhancing productivity.
- Safety Measures: Implementing safety protocols and providing adequate personal protective equipment (PPE) protects operators from hazards associated with CNC router operation. A safe working environment boosts morale and productivity.
Cost Efficiency
- Maintenance Costs: An optimal operating environment reduces the frequency of maintenance and repairs, lowering overall operating costs. Preventive measures like proper cleaning and maintenance prolong the life of the CNC router and its components.
- Downtime Reduction: Minimizing environmental risks such as dust contamination or power fluctuations reduces unplanned downtime. Maximizing uptime improves production schedules and overall efficiency.
Key environmental factors for running CNC routers
Workspace Considerations
- Space and Layout Requirements: Ensure that there is sufficient space around the CNC router to allow for easy movement of operators and materials. A common guideline is to have at least 3-4 feet of clearance around all sides of the machine. Moreover, allocates space for storing raw materials and finished products. Organized storage helps maintain workflow efficiency and prevent clutter.
- Ventilation and Airflow: CNC routers, especially when working with materials that produce dust or fumes, require a well-ventilated environment. Proper ventilation helps in dispersing fumes and maintaining air quality.
- Temperature Regulation: CNC routers function best within a stable temperature range, typically between 60°F and 80°F (15°C to 27°C). Extreme temperatures can affect the precision of the machine and the properties of the materials being worked on.
- Humidity Control: Ideal humidity levels are between 35% and 60%. High humidity can lead to rust and corrosion of machine parts, while very low humidity can cause static electricity issues.
Structural Considerations for Stability
- Floor and Foundation Stability: The floor must be level to ensure the machine operates accurately. Uneven floors can cause misalignment and affect the precision of the cuts. The floor should have adequate load-bearing capacity to support the weight of the CNC router and any auxiliary equipment. Check the specifications of the machine and ensure the flooring can handle the load without settling or shifting.
- Machine Placement and Anchoring: Position the CNC router in a location that facilitates smooth workflow and easy access for maintenance. Avoid placing it near sources of excessive heat, cold, or moisture. Securely anchor the CNC router to the floor if required by the manufacturer. This anchoring helps in reducing vibrations and ensuring the machine remains stable during operation.
Dust and Chip Management
- Dust Collection System: Implement a dust collection system to manage the significant amount of dust and debris generated. This system should be efficient enough to capture dust at the source and prevent it from settling on machine components or becoming airborne.
- Chip Removal Strategies: Integrate automated chip removal systems, such as conveyors or vacuum systems, that can continuously remove chips from the cutting area during operation. This helps prevent chip buildup that can interfere with machining precision. For smaller operations or specific tasks, have manual tools such as brushes, vacuums, or air blowers available for periodic chip removal.
Lighting and Visibility
- Adequate Lighting: Ensure the workshop has sufficient overall lighting to maintain a safe and efficient working environment. This typically involves bright, even lighting that reduces shadows and glare. Install focused task lighting around the CNC router to illuminate critical areas such as the cutting zone, control panel, and tool holders.
- Visual Inspection and Maintenance: Implement a routine visual inspection schedule to check the CNC router for wear and tear, misalignments, or damage. This includes inspecting the cutting tools, spindles, belts, and other moving parts. Establish a preventive maintenance schedule that includes lubrication, cleaning, calibration, and replacement of worn parts.
By carefully managing these environmental factors, you can enhance the performance, safety, and lifespan of your CNC router, ensuring high-quality outputs and a safe working environment for operators.
How to create a safe running environment
Operating a CNC router involves various safety issues that need to be addressed to ensure a safe working environment for operators. Here are some essential steps and considerations to establish a safe CNC router environment:
Electrical Considerations
- Power Requirements: Ensure that the CNC router is connected to a stable power source with the correct voltage and amperage as specified by the manufacturer. Unstable power can cause malfunctions or damage to the machine. Install surge protectors to safeguard the machine’s electronic components from power surges and spikes.
- Electrical Safety Measures: Ensure the machine is properly grounded to prevent electrical shocks and reduce the risk of electrical fires. Conduct regular inspections of all electrical components, including wires, connectors, and control panels, to identify and address any signs of wear, damage, or overheating.
Noise Reduction Strategy
- Impact of Noise on the Workspace: Provide hearing protection such as earplugs or earmuffs to operators and other personnel working near the CNC router to protect against hearing damage from prolonged exposure to high noise levels.
- Housing and Sound Insulation: Enclose the CNC router within a dedicated housing unit to contain noise and dust. This enclosure should be made from sound-absorbing materials to reduce noise levels. Install anti-vibration pads or mounts under the CNC router to reduce vibration transmission to the floor, which can contribute to noise.
Climate Control for Material Stability
- Material Expansion and Contraction: Store materials in a controlled environment to acclimate them to the workshop conditions before machining. This helps in maintaining consistent dimensions. Implement procedures for handling materials, including acclimatization periods and pre-machining inspections to ensure they are dimensionally stable.
- Electronics Cooling Systems: Equip the CNC router with adequate cooling systems to prevent overheating of electronics. This can include fans, heat sinks, and air conditioning units. Use temperature sensors to monitor the electronics and machine components. Set up alerts for any temperature anomalies that could indicate a cooling system failure.
Safety and Ergonomics
- Operator Safety: Ensure that all operators are properly trained and certified to use the CNC router. Training should cover machine operation, emergency procedures, and safety protocols. Provide personal protective equipment (PPE) such as safety glasses, hearing protection, dust masks, and gloves to protect operators from potential hazards.
- Ergonomics: Design workstations with ergonomic principles in mind. Ensure that work surfaces, control panels, and material handling areas are at comfortable heights and within easy reach. Use adjustable chairs, stands, and monitors to accommodate operators of different heights and preferences.
Comply with Regulations and Standards
- OSHA Guidelines: Ensure that all safety measures comply with OSHA regulations. This includes proper machine guarding, lockout/tagout procedures, and electrical safety. Conduct regular safety inspections to identify and address potential hazards. Use OSHA’s guidelines and checklists to ensure all aspects of workplace safety are covered.
- Environmental Compliance: Implement dust collection and filtration systems to minimize the release of dust and other particulates into the environment. Ensure these systems are compliant with local environmental regulations. Develop procedures for the proper disposal of waste materials, including recycling and disposal of hazardous materials in accordance with environmental laws.
Maintenance and Cleaning
- Daily Maintenance Practices: Perform daily inspections of the CNC router to check for signs of wear, damage, or misalignment. This includes checking the condition of cutting tools, belts, and other moving parts. Regularly calibrate the CNC router to maintain precision and accuracy. Follow the manufacturer’s guidelines for calibration frequency and procedures.
- Cleaning: Use a vacuum system or compressed air to remove dust and debris from the CNC router and surrounding area. Regular cleaning prevents buildup that can interfere with machine operation. Keep the workspace clean and free of obstructions. This includes cleaning floors, workbenches, and storage areas to reduce the risk of accidents and improve overall efficiency.
By following these guidelines, you can create a safer environment for operating a CNC router, reducing the risk of accidents and ensuring the well-being of the operator and others in the vicinity.
Summarize
The environment in which a CNC router operates plays a key role in its performance, efficiency, and longevity. Factors such as temperature, humidity levels, cleanliness, and stability of power supply are paramount. Maintaining a controlled environment not only ensures consistent and accurate machining but also enhances the durability of machine components. By adhering to recommended environmental conditions and implementing proper maintenance practices, manufacturers can maximize the productivity and reliability of their CNC routers, ultimately leading to improved overall operational success.
AccTek CNC is a well-known manufacturer of CNC routers, consistently delivering high-quality machines that meet the diverse needs of users across various industries. Our commitment to excellence is evident in the precision and durability of their CNC routers, making them an ideal choice for both novice and experienced operators. For anyone seeking a reliable CNC router solution backed by industry expertise and exceptional service, AccTek CNC stands as a trusted partner.