- 10-15 Min Read
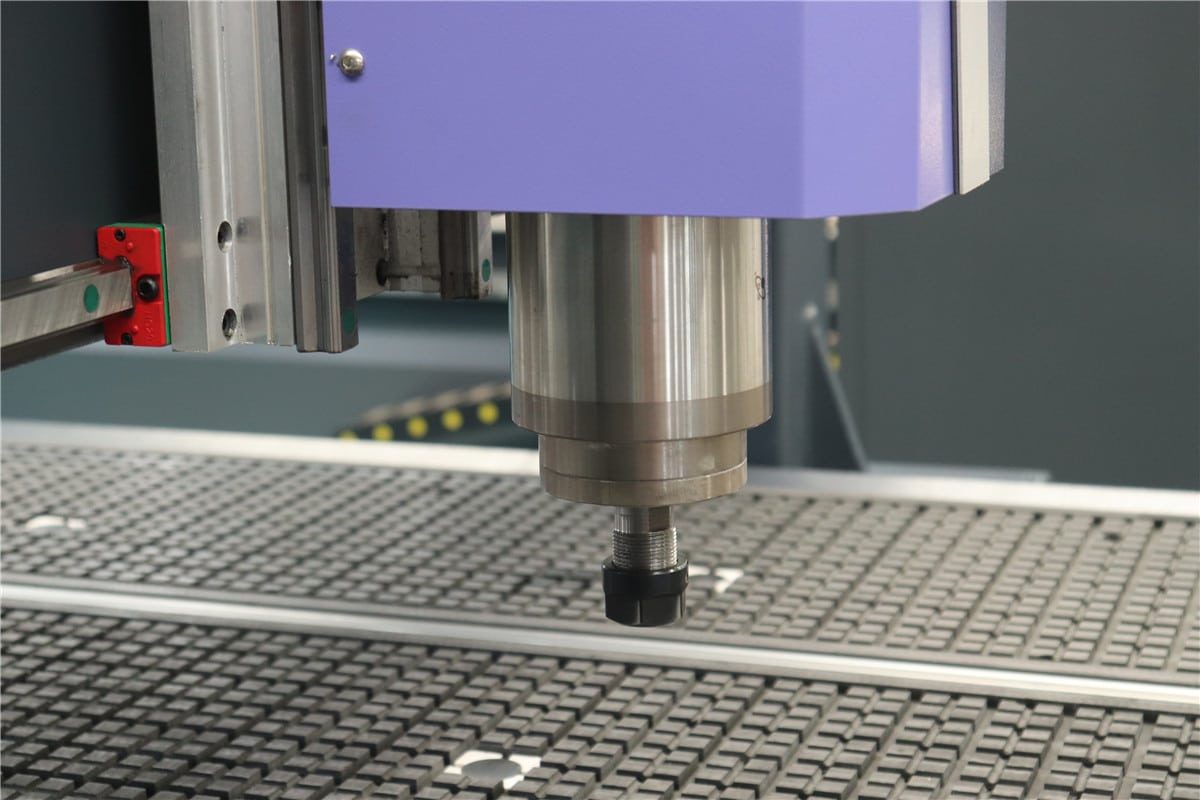
The spindle is one of the most critical components of a CNC router, as it powers the cutting tools that shape and create precise designs. Its performance and longevity directly impact the efficiency and reliability of the entire machine. For businesses and hobbyists alike, understanding the typical lifespan of a CNC router spindle can help users optimize their machine’s performance, reduce unexpected downtime, and plan for replacements effectively.
But how long does a spindle typically last? The answer depends on several factors, including the type of spindle, its usage intensity, and how well it is maintained. On average, CNC router spindles last between 5,000 and 10,000 operating hours. This article explores the key elements that affect spindle lifespan, provides insights into extending its service life, and helps you identify when it might be time for a replacement. By the end, you’ll have a clear understanding of how to get the most out of your CNC router’s spindle.
Understanding CNC Router Spindle
The spindle of a CNC router is the core mechanical component that drives the cutting tool by rotating at high speeds. The spindle’s design and performance directly influence the machine’s cutting precision, speed, and efficiency. As the heart of the CNC router, it plays a pivotal role in the machine’s ability to execute complex operations accurately. Here are its details:
Spindle Function
The primary function of the CNC router spindle is to hold and rotate the cutting tool at a consistent speed, ensuring precise material removal. It provides the power and stability needed to perform tasks such as drilling, carving, engraving, and milling across a wide range of materials, including wood, plastic, metal, and composites. Additionally, the spindle ensures smooth operations by minimizing vibrations and maintaining control during high-speed machining, which is beneficial for achieving high-quality finishes and intricate details.
Spindle Characteristics
Key characteristics of a CNC router spindle include its power rating, rotational speed (measured in RPM), and compatibility with tooling systems. High-performance spindles are typically designed for continuous use and can handle demanding tasks such as cutting metals or intricate engraving. On the other hand, lower-powered spindles are better suited for lighter materials like wood, plastic, or soft composites.
Spindle Types
CNC router spindles are available in different types, each designed for specific applications and operating conditions. The two main categories are:
- Air-Cooled Spindles: These spindles use fans to dissipate heat generated during operation. They are simpler to install and maintain, making them a popular choice for lighter workloads or environments where water cooling is impractical.
- Water-Cooled Spindles: These spindles use a water circulation system to manage heat, allowing for better thermal regulation during extended operations. They are ideal for high-performance applications that require consistent cooling to prevent overheating and maintain precision.
Understanding these CNC router basics helps operators choose the right spindle for their needs and optimize machine performance for various tasks.
Factors Affecting the Service Life of a CNC Router Spindle
The service life of a CNC router spindle depends on various factors that influence its performance and durability. Proper understanding of these factors can help maximize spindle longevity and prevent premature wear or failure. Below are the key factors that affect a spindle’s service life:
Usage Pattern
- Frequency of Use: Spindles subjected to continuous, high-intensity operations wear out faster than those used intermittently. Overloading or exceeding operational limits can significantly shorten the spindle’s lifespan.
- Cutting Applications: Tasks involving dense or abrasive materials, such as metals, generate more stress on the spindle compared to lighter materials like wood or plastic.
- Speed and Feed Rates: Operating the spindle at excessive speeds or improper feed rates can cause overheating, increased vibrations, and early component failure.
Maintenance Practices
- Regular Cleaning: Dust and debris accumulation can obstruct airflow or damage internal components. Cleaning the spindle regularly ensures smooth operation.
- Lubrication: Proper lubrication of bearings and moving parts reduces friction and prevents overheating, prolonging service life.
- Timely Repairs and Replacements: Replacing worn-out bearings, seals, or other components promptly can prevent more severe damage to the spindle.
Environmental Conditions
- Temperature and Humidity: Extreme heat or cold can affect spindle performance. High humidity may lead to rust and corrosion in metal components.
- Dust and Debris: Operating in a dusty or dirty environment increases the risk of clogging and internal damage, especially if the spindle lacks proper seals.
- Vibration Isolation: Spindles installed in unstable setups or vibrating environments are prone to misalignment and accelerated wear.
Material Compatibility
- Tool Material and Balance: Using unbalanced or incompatible tools can increase stress and cause vibrations that damage the spindle.
- Workpiece Material: Cutting abrasive or dense materials requires more power, generating heat and wear on the spindle over time.
Spindle Design and Construction
- Material Quality: High-quality materials and precise engineering ensure better durability. Premium-grade spindles are less prone to wear and tear, offering extended service life.
- Cooling System: Water-cooled spindles generally last longer due to superior heat dissipation, whereas air-cooled spindles may experience higher thermal stress during prolonged use.
- Bearings: High-quality bearings are beneficial for smooth operation and longevity. Precision-engineered bearings reduce friction and wear under heavy loads.
- Sealing and Protection: Spindles with effective seals prevent dust and debris from entering, enhancing durability in harsh working conditions.
By paying attention to these factors and implementing best practices, operators can ensure the CNC router spindle delivers reliable performance over its expected lifespan.
Average Service Life of a CNC Router Spindle
The service life of a CNC router spindle varies depending on several factors, including its type, quality, usage, and maintenance. On average, CNC router spindles last between 5,000 and 10,000 operating hours, but this can vary widely based on the following considerations:
Spindle Types
- Air-Cooled Spindles: Typically last 5,000 to 7,000 hours. Air-cooled spindles are more prone to overheating in continuous or demanding operations, which can reduce their longevity. They are better suited for lighter workloads or environments where water cooling is impractical.
- Water-Cooled Spindles: These spindles generally offer a longer lifespan of 7,000 to 10,000 hours, thanks to their efficient cooling systems. Water-cooled spindles are ideal for high-performance applications and extended periods of use, as they effectively manage thermal stress.
- High-Speed Spindles: These spindles are often used in precision machining, and may have a slightly shorter lifespan of 4,000 to 6,000 hours due to the added stress from operating at higher RPMs.
Benchmarks for Industrial-Grade and Entry-Level Spindles
- Industrial-Grade Spindles: These spindles are built using high-quality materials and precision-engineered components, such as premium bearings and advanced cooling systems. Designed for durability and continuous operation, industrial-grade spindles can last 8,000 to 10,000+ hours with proper care.
- Entry-Level Spindles: These spindles often found in hobbyist or budget CNC routers, have a shorter lifespan of 3,000 to 5,000 hours. They are typically constructed with lower-cost materials and simpler designs, making them more affordable but less durable for intensive or continuous operations.
Manufacturer Recommendations and Warranties
Manufacturers often provide recommended operating parameters, such as RPM ranges, duty cycles, and load limits. Following these guidelines ensures optimal performance and extends the spindle lifespan. Spindles typically come with warranties ranging from 6 months to 2 years, depending on the manufacturer and spindle quality. Longer warranty periods are often indicative of higher durability and confidence in the product.
The lifespan of CNC router spindles varies based on type, with water-cooled and industrial-grade spindles generally offering longer service lives. By understanding these lifespans, users can select the right spindle type for their specific needs and plan maintenance or replacements effectively.
Signs That a Spindle Needs Replacement
Identifying when a CNC router spindle requires replacement involves observing common signs of wear and using diagnostic tools and techniques to confirm issues. Early detection helps prevent machine downtime, maintain precision, and avoid costly damage.
Common Indicators of Spindle Wear
- Unusual Noise: Grinding, whining, or rattling sounds during operation can indicate worn-out bearings or internal damage.
- Vibrations: Excessive or irregular vibrations may suggest imbalance, misalignment, or degraded components within the spindle.
- Overheating: A spindle that becomes excessively hot during normal operation could signal issues with the cooling system, lubrication, or internal motor components.
- Decline in Cutting Precision: Poor cutting accuracy, rough edges, or inconsistent depths in workpieces may indicate that the spindle is losing its stability or rotational precision.
- Tool Holding Problems: Difficulty securing tools, slipping tools, or loose tool holders may indicate wear in the spindle’s collet, chuck, or tool holder system.
- Frequent Overload or Shutdowns: Spindles that frequently trip overload protection systems or shut down unexpectedly may have internal electrical or mechanical issues.
- Reduced RPM or Inconsistent Speed: A noticeable drop in maximum RPM or fluctuating spindle speeds during operation may signal internal motor failure or bearing degradation.
- Visible Wear or Damage: Cracks, dents, or other visible damage to the spindle housing or related components are clear signs that the spindle may need replacement. Leaks in water-cooled spindles or damaged air vents in air-cooled spindles also indicate serious problems.
Tools and Techniques for Diagnosing Spindle Problems
- Vibration Analysis: Specialized vibration monitoring tools can detect imbalances or excessive vibrations, identifying issues with bearings or alignment.
- Temperature Monitoring: Using infrared thermometers or thermal imaging cameras to monitor spindle temperature can reveal cooling inefficiencies or overheating.
- Noise Analysis: Acoustic sensors or listening devices can detect abnormal sounds that indicate bearing wear or internal damage.
- Runout Measurement: Runout testers measure the deviation of the spindle’s rotation from a true center. High runout values indicate wear or misalignment.
- Load Monitoring: Monitoring spindle motor load with a diagnostic tool can identify increased resistance, which often signals internal wear.
- Tool Retention Force Testing: Specialized gauges measure the clamping force of the spindle’s tool holder system. Insufficient force may indicate collet or chuck wear.
- Visual Inspections: Regular visual checks for cracks, wear, leaks, or other damage to the spindle housing or components can reveal issues before they escalate.
Recognizing the signs of spindle wear, combined with diagnostic tools and techniques, helps operators address problems before they lead to costly failures. When signs of wear persist despite maintenance or diagnostic results confirming serious issues, spindle replacement is the best solution to restore CNC router performance and reliability.
Best Practices to Extend Spindle Service Life
The service life of a CNC router spindle can be significantly prolonged with proper care, consistent maintenance, and adherence to recommended operating conditions. Implementing the following best practices helps prevent wear and tear, reduces the risk of unexpected failures, and optimizes spindle performance.
Regular Maintenance
- Cleaning: Keep the spindle and surrounding area free from dust, debris, and residue. Regular cleaning prevents blockages and protects internal components.
- Lubrication: Apply the appropriate lubricant to bearings and other moving parts as recommended by the manufacturer. Proper lubrication minimizes friction and overheating.
- Inspection: Perform routine inspections to check for wear, loose components, or misalignment. Replace worn-out bearings or seals promptly to prevent further damage.
Optimize Operating Conditions
- Speed and Feed Rates: Operate the spindle within the manufacturer’s recommended speed and feed rate limits to avoid unnecessary stress on the motor and bearings.
- Tool Selection: Use well-balanced and properly installed tools to minimize vibration and reduce stress on the spindle.
- Cooling System Management: Ensure water-cooled spindles have a functional cooling system with clean, adequate water flow. For air-cooled spindles, maintain proper ventilation.
Proper Usage Practices
- Warm-Up Routine: Before full operation, warm up the spindle by running it at a moderate speed. This helps evenly distribute lubrication and reduces thermal shock.
- Avoid Overloading: Do not exceed the spindle’s maximum load capacity or run it at continuous full power for extended periods.
- Frequent Tool Changes: Inspect and replace cutting tools regularly to ensure sharpness, which reduces cutting resistance and spindle strain.
- Follow Manufacturer Guidelines: Adhere to the manufacturer’s recommendations for operating limits, maintenance schedules, and replacement intervals for consumable parts like bearings and seals. Use only approved accessories and spare parts to maintain compatibility and performance.
- Train Operators: Provide adequate training to machine operators to ensure proper handling and minimize human errors that can lead to spindle damage.
Maintain a Clean and Controlled Environment
- Temperature and Humidity: Operate the CNC router in a temperature-controlled environment to prevent thermal stress and condensation in the spindle.
- Dust Management: Use dust extraction systems to reduce airborne particles that can infiltrate and damage the spindle.
- Stable Installation: Ensure the CNC router is installed on a stable surface to avoid unnecessary vibrations that can impact the spindle.
Ensure Proper Installation and Alignment
- Align the spindle correctly with the tool and machine axis to prevent uneven wear and vibration.
- Securely mount the spindle to avoid instability during operation.
Monitor Performance and Use Diagnostics
- Vibration Monitoring: Check for unusual vibrations using diagnostic tools to identify early signs of imbalance or wear.
- Temperature Monitoring: Regularly monitor spindle temperature to detect overheating issues and address cooling system faults.
- Runout Testing: Test for excessive runout periodically to ensure the spindle is maintaining precision.
By implementing these best practices, CNC router users can significantly extend the service life of their spindles, maintain consistent performance, and reduce operational costs associated with repairs or replacements. Regular attention to maintenance and operational guidelines is the key to ensuring long-term reliability and productivity.
Precautions for Spindle Replacement
Replacing a CNC router spindle is a delicate process that requires proper preparation, careful handling, and adherence to safety protocols. Following these precautions ensures a successful replacement and avoids damage to the machine or spindle.
Preparation Before Replacement
- Gather the Required Tools: Ensure you have all necessary tools, such as wrenches, screwdrivers, alignment tools, and a runout tester, before starting the replacement.
- Review Manufacturer Guidelines: Refer to the CNC router and spindle manufacturer’s manuals for specific instructions and recommendations on removal and installation.
- Power Off and Disconnect: Turn off the CNC router, disconnect it from the power supply, and release any residual power to prevent accidental activation during the process.
- Clean the Machine Area: Remove dust, debris, and material residue around the spindle and machine area to avoid contamination during installation.
Removal of the Old Spindle
- Secure the Machine: Ensure the CNC router is stable and properly supported to avoid movement during the replacement process.
- Disconnect Wiring and Connections: Carefully detach the spindle’s electrical connections, cooling lines (for water-cooled spindles), and any pneumatic connections, labeling them for correct reassembly.
- Remove Mounting Hardware: Loosen and remove bolts or clamps holding the spindle in place. Support the spindle securely while detaching it to prevent damage or injury.
- Inspect Related Components: Check for wear or damage to spindle mounts, bearings, and alignment components. Replace or repair these parts if necessary before installing the new spindle.
Installation of the New Spindle
- Check the New Spindle: Inspect the new spindle for any visible damage or defects. Ensure it matches the specifications required for your CNC router.
- Align the Spindle Properly: Use alignment tools to ensure the spindle is mounted correctly and centered with the machine axis. Misalignment can cause vibrations, imprecision, and accelerated wear.
- Secure the Spindle: Tighten the mounting bolts or clamps evenly to avoid uneven pressure. Ensure the spindle is firmly attached and stable.
- Reconnect Wiring and Cooling Lines: Reattach all electrical, cooling, and pneumatic connections, following the labels from the removal process. Double-check connections for proper sealing and contact.
Testing After Replacement
- Check for Proper Functioning: Power on the CNC router and run the spindle at low speed to check for smooth operation, unusual noises, or vibrations.
- Monitor Cooling System: Ensure water-cooled spindles have proper water flow and air-cooled spindles have unobstructed airflow.
- Run a Test Job: Perform a test run with a light workload to verify the spindle’s performance and accuracy before returning to full operation.
Safety Precautions
- Wear Safety Gear: Use gloves and eye protection while handling the spindle and tools to avoid injury.
- Avoid Over-Tightening: Do not overtighten bolts or clamps, as this can damage the spindle or its mounts.
- Ensure Proper Grounding: Verify that the spindle’s electrical connections are properly grounded to prevent electrical hazards.
By following these precautions during spindle replacement, users can ensure the new spindle is installed correctly, operates smoothly, and delivers optimal performance. Taking the time to carefully prepare, install, and test the spindle will prevent costly mistakes and downtime.
Summarize
The service life of a CNC router spindle is influenced by multiple factors, including the type of spindle, operating conditions, maintenance practices, and the quality of its construction. While the average lifespan can range from 5,000 to 10,000 hours, careful operation, regular maintenance, and adherence to manufacturer guidelines can significantly extend its durability and performance. Recognizing the signs of spindle wear and addressing issues promptly ensures reliable operation and minimizes costly downtime. For more information, please continue reading “How to correctly choose the CNC router spindle?”.
When it comes to ensuring a long-lasting and reliable CNC router spindle, choosing the right manufacturer is just as important as proper maintenance and operation. AccTek CNC, a professional CNC router manufacturer, stands out as a trusted provider of high-quality machines designed for durability and performance. Our CNC routers are built with premium components, including robust spindles designed to handle a wide range of applications, from woodworking to precision metal cutting. By investing in a machine from AccTek, you’re ensuring a reliable partner for your production goals.