- 8-12 Min Read
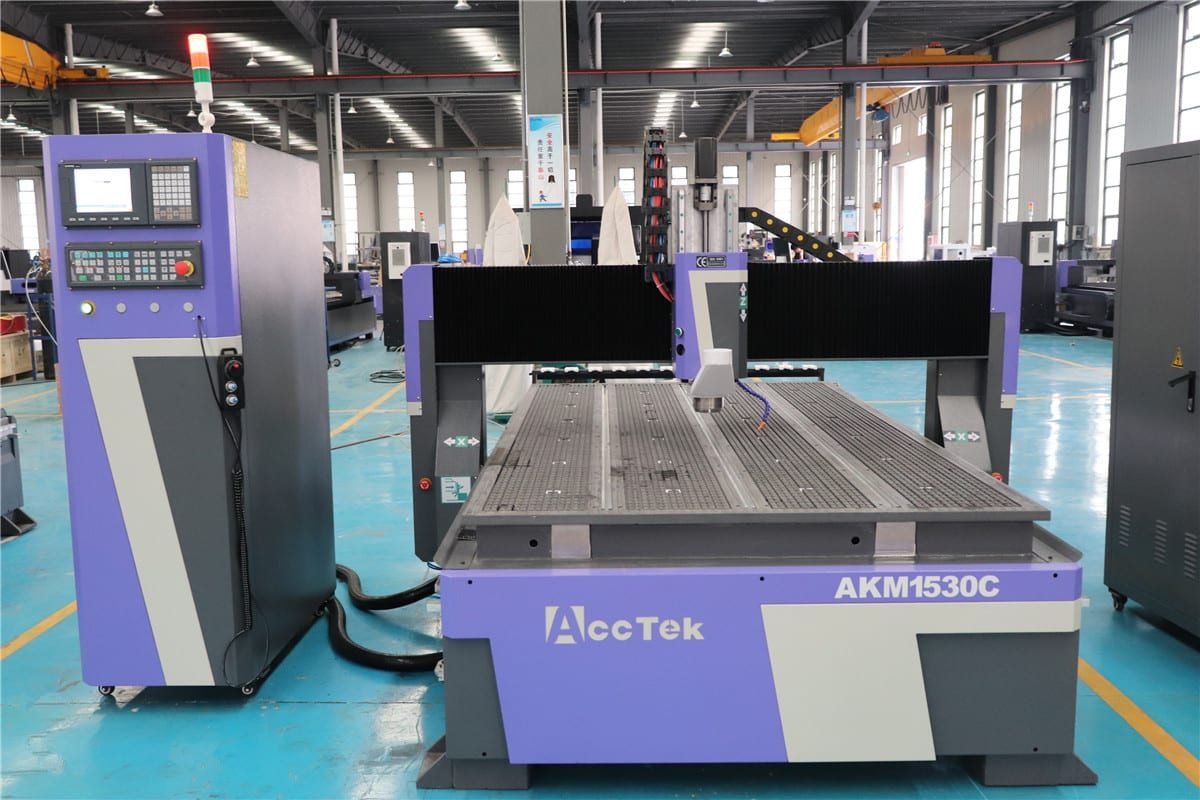
In the realm of modern manufacturing, Computer Numerical Control (CNC) routers stand as indispensable tools, driving precision, efficiency, and versatility in the production process. These machines have revolutionized various industries, from woodworking to metal fabrication, by automating intricate cutting, carving, and shaping tasks with remarkable accuracy. Yet, amidst the acclaim for their capabilities, one pertinent question looms large: what exactly is the service life of a CNC router?
The service life of a CNC router is a multifaceted concept, influenced by an array of factors spanning from machine design and construction to operational practices and maintenance routines. In this exploration, we delve into the intricacies of CNC router service life, dissecting the key factors that shape it and elucidating the expectations and maintenance practices necessary to optimize longevity. From material quality and usage intensity to technological advancements and proactive care, this examination aims to provide specific information about the service life of a CNC router, empowering manufacturers to make informed decisions and maximize the value of their machining investments.
The Importance of Service Life
The service life of a CNC router holds significant importance across various aspects of manufacturing operations. Understanding and managing this aspect can profoundly impact a company’s bottom line, productivity, and overall competitiveness. Here are several key aspects highlighting the importance of the service life of CNC routers:
- Financial Investment: CNC routers represent a considerable financial investment for manufacturing businesses. Knowing the expected service life helps in assessing the return on investment (ROI) and determining the cost-effectiveness of the equipment over its lifespan. It enables businesses to budget for equipment replacement or upgrades more accurately, avoiding unexpected expenses.
- Production Efficiency and Downtime: The service life of CNC routers directly influences production efficiency. A well-maintained machine with a longer service life experiences fewer breakdowns and downtime, ensuring consistent production output. Understanding service life allows manufacturers to plan preventive maintenance schedules effectively, minimizing unplanned interruptions in production.
- Quality Assurance: CNC routers play a critical role in maintaining product quality and precision. As the machine ages, wear and tear can affect its ability to maintain tight tolerances and produce accurate parts. Monitoring service life helps businesses anticipate and address issues related to diminishing quality, ensuring that products meet or exceed customer expectations throughout the machine’s lifespan.
- Competitive Advantage: In today’s competitive manufacturing landscape, companies strive to differentiate themselves through speed, quality, and reliability. Maximizing the service life of CNC routers enables businesses to maintain consistent production capabilities over time, enhancing their reputation for reliability and customer satisfaction. It also allows companies to leverage their existing equipment investments efficiently, potentially outlasting competitors who must frequently replace aging machinery.
- Technology Integration and Upgrades: The service life of CNC routers also influences decisions regarding technology integration and upgrades. As advancements in CNC technology occur, businesses may need to assess whether upgrading existing equipment or investing in new machinery is the most cost-effective solution. Understanding the service life of current equipment helps inform these decisions, ensuring that businesses stay competitive while managing capital expenditures effectively.
- Environmental Impact: The environmental impact of manufacturing equipment is an increasingly important consideration for businesses. Maximizing the service life of CNC routers reduces the need for premature disposal or replacement, minimizing waste and conserving resources. Extending the lifespan of equipment aligns with sustainability initiatives and reduces the carbon footprint associated with manufacturing operations.
Factors Affecting The Service Life of CNC Router
The life of a CNC router is affected by many factors. By considering these factors and implementing appropriate measures, manufacturers can optimize the service life of their CNC routers, minimize downtime, and maximize productivity and profitability in their operations. Here are some key factors that affect the service life of CNC routers:
- Machine Quality and Construction: The quality of materials and construction techniques used in building the CNC router significantly impacts its service life. Machines constructed with durable components and robust frames tend to last longer and withstand heavy use more effectively.
- Usage Intensity and Workload: The frequency and intensity of use also affect the service life of the CNC router. Machines subjected to continuous operation or high-volume production may experience more wear and tear, potentially leading to premature failure if not properly maintained.
- Maintenance Practices: Regular and proactive maintenance is beneficial for extending the service life of CNC routers. Proper lubrication, cleaning, and inspection of critical components such as spindles, bearings, and drive systems can prevent premature wear and ensure optimal performance over time.
- Environmental Conditions: The operating environment can affect the lifespan of CNC routers. Exposure to dust, humidity, temperature fluctuations, and other environmental factors can accelerate wear on components and electronic systems. Implementing measures to control environmental conditions, such as installing dust collection systems or maintaining optimal temperature and humidity levels, can help prolong the machine’s service life.
- Material Compatibility and Cutting Parameters: The type of materials being processed and the cutting parameters used can influence the stress placed on the CNC router. Harder materials or aggressive cutting speeds may accelerate wear on cutting tools, spindles, and other components. Adjusting cutting parameters to optimize tool life and reduce stress on the machine can contribute to extending its service life.
- Technological Advancements and Upgrades: As CNC technology evolves, older machines may become outdated or less efficient compared to newer models. While regular maintenance can help extend the service life of existing equipment, eventually, technological advancements may necessitate upgrades or replacements to maintain competitiveness and productivity.
- Operator Training and Skill Level: The competence of operators can impact the service life of CNC routers. Proper training in machine operation, maintenance procedures, and troubleshooting techniques can help minimize errors, reduce downtime, and prolong the life of the equipment.
- Manufacturer Support and Parts Availability: Access to manufacturer support, documentation, and genuine replacement parts is beneficial for maintaining CNC routers effectively. Manufacturers that provide comprehensive support and ensure the availability of spare parts can help prolong the service life of their equipment.
CNC Router Average Life Expectancy
The average life expectancy of a CNC router can vary significantly depending on several factors. Generally, high-quality CNC routers built with durable components and subjected to moderate usage can be expected to last anywhere from 10 to 20 years or more. However, this estimate is not set in stone and should be viewed as a rough guideline rather than a guarantee. The average expected service life of a CNC router should be evaluated from the following factors.
Signs of Wear and Aging
CNC routers undergo continuous use, leading to wear and aging of critical components. Signs of wear and aging serve as indicators of potential issues that could impact the service life of the machine. Observing signs such as reduced performance, increased noise, or erratic behavior can help manufacturers anticipate maintenance needs and address issues before they escalate. These signs are reflected in the following aspects:
Machine Parts
- Wear on cutting tools: Dull or chipped cutting tools indicate excessive wear and may result in decreased cutting efficiency and poor surface finish.
- Belt and chain wear: Loose or stretched belts and chains can lead to inconsistent motion and reduced accuracy in CNC router operations.
- Bearing deterioration: Noisy or rough movement in the spindle or axis bearings suggests wear and may result in decreased precision and increased friction.
Electronic Components
- Motor performance degradation: Reduced motor speed or torque output may signify aging electronic components, affecting overall machine performance.
- Control system glitches: Erratic behavior or intermittent faults in the CNC control system could indicate aging electronics or software issues.
- Sensor malfunction: Inaccurate or intermittent sensor readings may indicate sensor wear or electronic component degradation, leading to potential operational issues.
Maintenance Best Practices
Maximizing the average expected service life of CNC routers hinges on the implementation of robust maintenance best practices. These practices are beneficial for ensuring optimal performance, minimizing downtime, and extending the longevity of CNC router systems. The following are specific plans:
Regular Cleaning
Regular cleaning is fundamental in maintaining the cleanliness and functionality of CNC router systems. Dust, debris, and chip buildup can accumulate on machine surfaces, affecting performance and potentially causing damage to sensitive components. To mitigate these risks, operators should routinely clean CNC routers using appropriate methods and tools. This includes vacuuming or blowing away debris, wiping down surfaces with non-abrasive cleaners, and ensuring proper ventilation to minimize dust accumulation. By keeping CNC routers clean, manufacturers can prevent malfunctions, prolong component life, and maintain optimal machining conditions.
Lubrication of Moving Parts
Proper lubrication of moving parts is beneficial for reducing friction, minimizing wear, and ensuring smooth operation of CNC routers. Bearings, ball screws, guide rails, and other mechanical components require regular lubrication to maintain optimal performance. Manufacturers should follow manufacturer recommendations regarding lubrication intervals and use compatible lubricants suitable for specific components. By lubricating moving parts at appropriate intervals, manufacturers can prolong component life, prevent premature wear, and optimize machine reliability and precision.
Calibration Checks
Calibration checks are beneficial for maintaining machining accuracy and consistency in CNC router operations. Over time, factors such as thermal expansion, mechanical wear, and environmental conditions can affect machine calibration and alignment. Manufacturers should perform regular calibration checks on-axis alignment, tool offsets, spindle runouts, and other critical parameters. This involves using precision measurement tools and following established calibration procedures to ensure that CNC routers operate within specified tolerances. By conducting calibration checks regularly, manufacturers can uphold machining accuracy, minimize errors, and maximize part quality and consistency.
Component Inspections
Regular inspections of machine components are beneficial for identifying signs of wear, damage, or deterioration that may affect CNC router performance. Bearings, spindles, motors, belts, and electrical connections should be inspected periodically for signs of wear, misalignment, or malfunction. Any abnormalities or potential issues should be addressed promptly through repair or replacement. Additionally, thorough inspections should include checking for loose fasteners, damaged wiring, and other safety hazards to prevent accidents or machine failures. By conducting comprehensive component inspections, manufacturers can detect issues early, prevent catastrophic failures, and maintain CNC router reliability and uptime.
Software Updates
Software updates play a key role in maintaining the functionality, security, and compatibility of CNC router systems. Manufacturers should regularly check for updates from CNC controller software vendors and apply them as needed. These updates may include bug fixes, performance enhancements, new features, and security patches. Additionally, operators should ensure that machine parameters, tool databases, and post-processing configurations are kept up-to-date to reflect changes in machining requirements. By staying current with software updates, manufacturers can optimize CNC router performance, mitigate potential risks, and ensure long-term compatibility with evolving manufacturing technologies.
Usage Practices
Correct machine usage practices can effectively extend the expected service life of CNC routers. In this part, we introduce to you from multiple angles how to maximize the service life of CNC routers in practice.
Optimal Operating Conditions
Maintaining stable environmental factors such as temperature, humidity, and cleanliness is beneficial for ensuring machine reliability and performance. Additionally, providing adequate ventilation and dust extraction systems helps prevent dust and debris buildup, which can lead to premature wear and component damage. By operating CNC routers in optimal conditions, manufacturers can minimize stress on machine components and extend their service life.
Tooling Best Practices
Using high-quality cutting tools suitable for specific materials and applications helps minimize tool wear and prevent premature tool failure. Additionally, adhering to recommended cutting parameters, such as spindle speed, feed rate, and depth of cut, ensures efficient material removal while minimizing stress on machine components. By employing tooling best practices, manufacturers can prolong tool life, reduce maintenance costs, and enhance machining accuracy.
Program Optimization
Program optimization is beneficial for optimizing CNC router performance and minimizing wear on machine components. Optimizing machining programs involves optimizing tool paths, minimizing tool changes, and reducing unnecessary movements to streamline machining operations. Additionally, implementing efficient tool change routines and minimizing rapid movements helps minimize wear on spindle bearings and other mechanical components. By optimizing machining programs, manufacturers can increase productivity, reduce cycle times, and prolong the life of CNC routers.
Operator Training
Operator training plays a significant role in maximizing the lifespan of CNC routers and ensuring safe and efficient operation. Well-trained operators understand machine capabilities, tooling requirements, and programming principles, allowing them to operate CNC routers effectively and troubleshoot potential issues. Additionally, providing training on proper maintenance procedures, including regular cleaning, lubrication, and inspection, helps prevent premature wear and component damage. By investing in operator training, manufacturers can improve machine uptime, minimize errors, and prolong the service life of CNC routers.
Planned Downtime
Planned downtime is an essential aspect of CNC router maintenance and contributes to maximizing machine lifespan. Scheduled maintenance activities, such as lubrication, calibration checks, and component inspections, should be performed regularly to prevent unexpected failures and optimize machine performance. Additionally, scheduling downtime for software updates and machine upgrades ensures that CNC routers remain up-to-date with the latest advancements and technologies. By planning downtime strategically, manufacturers can minimize disruptions to production schedules, reduce the risk of unplanned downtime, and extend the service life of CNC routers.
The average life expectancy of CNC routers is influenced by various factors, while there is no definitive answer to the average life expectancy of a CNC router, proactive maintenance and correct operation can help maximize the lifespan and performance of these valuable manufacturing assets.
Summarize
Understanding the service life of CNC routers involves a multifaceted approach encompassing various factors. In essence, the service life of CNC routers is not merely determined by the number of years in operation, but rather by the effectiveness of maintenance practices and the adaptability to evolving technological advancements. By staying proactive and embracing a culture of continuous improvement, manufacturers can unlock the full potential of their CNC router investments and achieve long-term success and competitiveness in the ever-changing manufacturing landscape.
AccTek CNC is a well-known CNC router manufacturer in China, and the components for our machines are sourced from world-class suppliers and innovators in machine control. At AccTek CNC, we are committed not only to providing you with high-quality machines but also to offering professional operating guidance and technical support whenever you need it. By following the correct operating instructions and daily maintenance tips, you can keep your machine running smoothly and stably for over ten years. We understand the importance of reliability and consistency in your operations, and we’re here to support you every step of the way.