- 8-12 Min Read
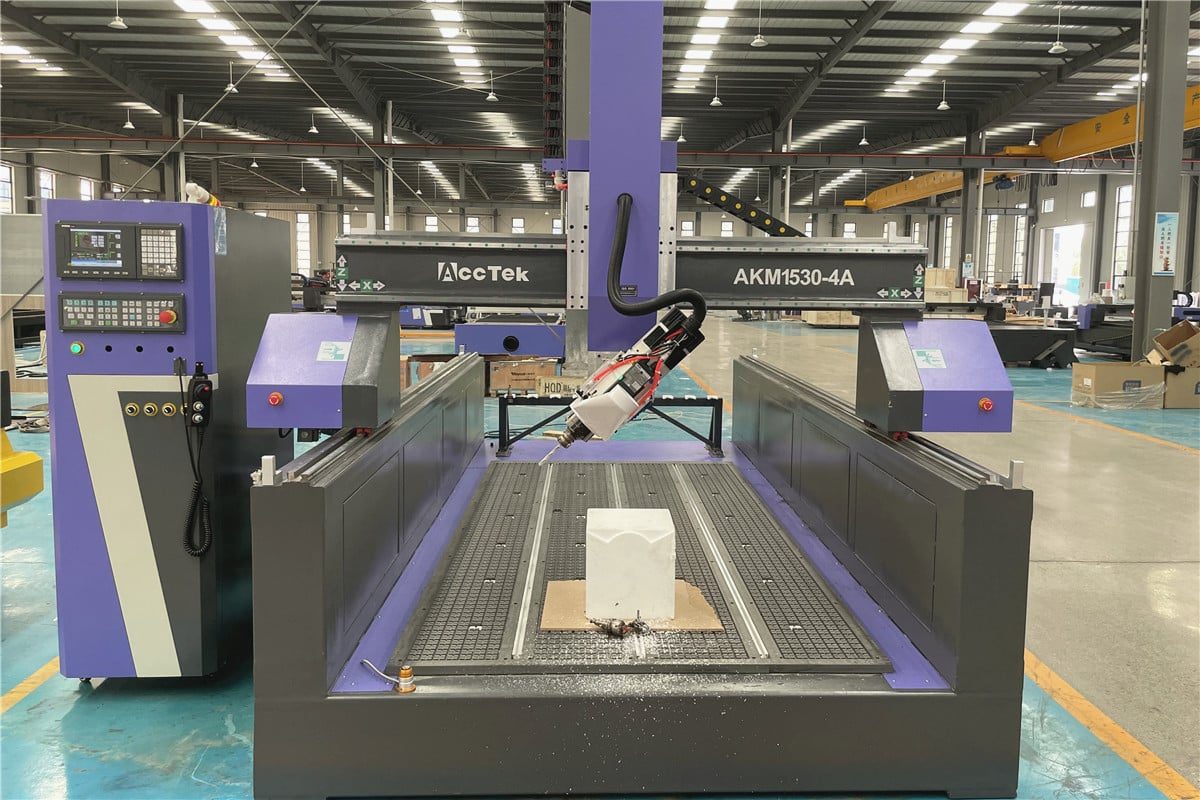
In the ever-evolving landscape of manufacturing and fabrication, Computer Numerical Control (CNC) technology continues to revolutionize the way we create intricate and precise components. Among the myriad of CNC machines available, CNC routers stand out for their ability to carve, cut, and shape various materials with unmatched accuracy. Within the realm of CNC routers, the distinction between 3-axis and 4-axis configurations represents a pivotal choice for manufacturers seeking optimal precision and efficiency in their operations.
In this article, we delve into the fundamental disparities between 3-axis and 4-axis CNC routers, exploring their respective capabilities, applications, and the nuanced advantages each configuration offers. By understanding these key differentiators, manufacturers can make informed decisions tailored to their specific production needs. Whether you’re delving into CNC machining for the first time or seeking to upgrade your existing setup, this article serves as a valuable resource for selecting the ideal CNC router to propel your projects to new heights of precision and efficiency.
Understanding CNC Router
What is CNC Router?
The CNC router is a computer-controlled cutting machine that utilizes a rotating cutting tool to carve, engrave, and shape various materials with exceptional accuracy. Unlike traditional manual routers, CNC routers automate the machining process, guided by digital designs or programs generated through CAD (Computer-Aided Design) software. This fusion of advanced technology and mechanical precision empowers manufacturers to fabricate intricate components and prototypes with efficiency and repeatability.
How Does CNC Router Work?
The working principle of a CNC router revolves around the integration of computer numerical control (CNC) technology and motorized motion systems. A computerized controller interprets digital instructions from CAD software, translating them into precise movements and commands for the CNC router’s cutting tool. These instructions guide the tool along designated paths, orchestrating intricate cuts and contours with meticulous precision, ultimately transforming virtual designs into tangible products.
Basic Knowledge of Axis
Traditional 3-axis CNC routers operate along three primary axes: X, Y, and Z. The X-axis controls the movement of a cutting tool or spindle along a horizontal plane, usually from left to right or right to left. The Y-axis controls the movement of the cutting tool or spindle along the vertical plane, the movement generally goes from front to back or back to front. The Z-axis is the depth axis, it controls the up and down movement of the cutting tool or spindle, allowing for cutting or engraving at different depths. This configuration enables the CNC router to navigate three-dimensional space, executing complex machining tasks with precision and accuracy.
For 4-axis CNC routers, it introduces an additional rotational axis, typically known as the A-axis. The A-axis introduces rotational movement around the X-axis. This rotational axis enables the machine to tilt or swivel the cutting tool and workpiece with a maximum swing range of 180°, thereby expanding the range of machining capabilities. By incorporating the A-axis into the CNC router’s configuration, manufacturers can achieve a higher degree of versatility and complexity in their machining operations.
The Difference Between 3-Axis and 4-Axis
In addition to the different number of axes we mentioned in the above introduction, the difference between 3-axis and 4-axis CNC routers lies primarily in their ability to manipulate the workpiece during machining operations. Here’s a breakdown of the distinctions between the two configurations:
Complexity of Machining Operations
- 3-axis CNC Router: Primarily suited for machining operations on flat or slightly contoured surfaces. Limited to linear and perpendicular movements along the X, Y, and Z axes, making it ideal for tasks such as cutting, drilling, and engraving on flat materials or simple three-dimensional objects.
- 4-axis CNC Router: The fourth axis allows more complex machining operations such as 3D carving, contouring, engraving, and rotary cutting. This enables the machine to tackle a wider range of applications and meet diverse manufacturing needs.
Setup and Programming Requirements
- 3-axis CNC Router: Relatively simpler to set up and program compared to 4-axis CNC Machining paths and tool movements are predominantly planar, requiring less intricate programming and toolpath generation.
- 4-axis CNC Router: Requires more advanced setup and programming due to the additional A axis. Programming software must account for rotary movements and coordinate transformations, adding complexity to the machining process.
Precision and Accuracy
- 3-axis CNC Router: Offers high precision and accuracy for machining operations within its three-dimensional workspace. Suitable for tasks where strict tolerances are required, such as precision cutting and milling.
- 4-axis CNC Router: Maintains high precision and accuracy while also accommodating rotational movements. Capable of achieving intricate details and complex geometries with precise alignment and orientation.
Tooling and Workholding Considerations
- 3-axis CNC Router: Typically uses standard cutting tools and workholding fixtures suitable for flat or slightly contoured surfaces. Tool changes and workpiece repositioning are straightforward.
- 4-axis CNC Router: Requires specialized tooling and workholding solutions to accommodate rotational machining operations. Collet chucks, rotary tables, and indexing fixtures may be utilized for securing workpieces and facilitating rotary cuts.
Applications
- 3-axis CNC Router: Commonly used in woodworking, signage production, prototyping, and general machining applications where intricate designs are needed on flat surfaces or three-dimensional objects.
- 4-axis CNC Router: Widely employed in 3D processing industries such as ship models, automobile molds, and character sculptures, where intricate geometries, curves, and contours are prevalent. Used for tasks such as sculpting, rotary cutting, and cylindrical machining.
Cost of Investment
- 3-axis CNC router: Compared with the 4-axis CNCrouter, the structure and accessories are simpler, so the cost is lower. Suitable for standard machining tasks on flat or three-dimensional surfaces.
- 4-axis CNC router: More complex design and usually more expensive due to the addition of additional rotational axes. Offers enhanced versatility and the ability to machine complex shapes and surfaces, but at a higher investment cost.
Advantages and Challenges
3-Axis CNC Routers
- Advantages: 3-axis CNC routers are relatively straightforward to set up and operate, making them accessible to users with varying levels of expertise. These machines typically entail lower initial investment costs compared to their multi-axis counterparts, making them an attractive option for budget-conscious manufacturers. While limited to three primary axes, 3-axis CNC routers are highly versatile and can tackle a wide range of machining tasks, including cutting, drilling, engraving, and surface milling.
- Challenges: They are less adept at machining intricate 3D shapes and curved surfaces compared to 4-axis CNC routers, restricting their applicability in certain industries and projects. In addition, achieving complex geometries may require multiple setups and additional machining operations, leading to longer production times and reduced efficiency for certain tasks.
4-Axis CNC Routers
- Advantages: 4-axis CNC routers offer enhanced capabilities for machining complex geometries and curved surfaces, providing manufacturers with numerous advantages. First, the addition of a rotational axis enables 4-axis CNC routers to execute intricate cuts, carvings, and engravings on curved or cylindrical surfaces with unparalleled precision. In addition, by reducing the need for multiple setups and machining operations, 4-axis CNC routers can streamline production processes and shorten lead times for projects involving complex geometries.
- Challenges: However, 4-axis CNC routers also present certain challenges. The integration of an additional axis introduces complexity to programming and operating the CNC router, requiring advanced skills and expertise. On the other hand, due to their enhanced capabilities, 4-axis CNC routers typically entail higher initial investment costs compared to 3-axis CNC routers, which may pose a barrier to entry for some manufacturers.
Both 3-axis and 4-axis CNC routers offer distinct advantages and challenges, catering to different machining requirements and project objectives. By carefully evaluating the specific needs of their operations, manufacturers can determine the most suitable configuration to optimize productivity, precision, and innovation in their machining endeavors.
Choose 3 Axis or 4 Axis
Choosing between a 3-axis and 4-axis CNC router depends on various factors such as the specific machining requirements, desired capabilities, budget constraints, and long-term goals. Here’s a step-by-step guide to help you make an informed decision:
- Evaluate Machining Requirements: Assess the types of projects and machining tasks you will primarily undertake. Determine whether your applications involve predominantly flat or contoured surfaces, and whether rotational machining capabilities are necessary.
- Consider Material and Design Complexity: Determine the complexity of the parts or components you’ll be machining. If your projects involve intricate designs, curved surfaces, or 3D contours, a 4-axis CNC router may be more suitable for achieving precise and detailed results.
- Assess Precision and Accuracy Needs: Evaluate the level of precision and accuracy required for your machining applications. Consider whether strict tolerances are necessary and whether rotational capabilities would enhance the precision of your finished products.
- Review Budget and Cost Considerations: Determine your budget for purchasing and operating a CNC router. While 3-axis CNC routers are generally more affordable upfront, 4-axis CNC routers may offer enhanced capabilities at a higher initial investment cost. Consider your long-term return on investment (ROI) and the potential benefits of investing in an additional axis.
- Evaluate Programming and Training Requirements: Assess the complexity of programming and operating each type of CNC router. Consider the availability of skilled operators and the training required to effectively utilize the chosen machine. Keep in mind that 4-axis CNC routers may require more advanced programming skills and training due to the additional axis.
- Factor in Future Expansion and Growth: Anticipate future needs and potential growth in your machining operations. Consider whether investing in a 4-axis CNC router would provide flexibility and scalability to accommodate evolving project requirements and expand your capabilities.
- Seek Expert Advice and Consultation: If you’re uncertain about which type of CNC router is best suited for your needs, consult with industry experts, CNC machine suppliers, or experienced machinists. They can provide valuable insights and recommendations based on your specific requirements and objectives.
- Compare Features and Specifications: Compare the features, specifications, and performance capabilities of different 3-axis and 4-axis CNC routers available in the market. Consider factors such as spindle power, cutting speeds, tool capacity, and axis travel to determine which machine aligns best with your machining requirements.
By carefully evaluating these factors and considering your unique machining needs and objectives, you can make an informed decision when choosing between a 3-axis and 4-axis CNC router. Ultimately, selecting the right machine will empower you to optimize productivity, achieve superior machining results, and drive success in your manufacturing endeavors.
The Future Trend of Multi-Axis CNC Router
The future trend of multi-axis CNC routers is expected to be characterized by continuous advancements in technology, driven by the evolving needs of manufacturing industries and the quest for higher efficiency, precision, and versatility. Several key trends are likely to shape the future landscape of multi-axis CNC routers:
- Integration of Automation and Industry 4.0 Technologies: Multi-axis CNC routers will increasingly incorporate automation features and connectivity capabilities aligned with the principles of Industry 4.0. This includes the integration of IoT (Internet of Things) sensors, real-time monitoring systems, and data analytics platforms to optimize production processes, enhance predictive maintenance, and enable remote monitoring and control.
- Enhanced Precision and Accuracy: Future multi-axis CNC routers will leverage advancements in machine design, control systems, and servo motor technology to achieve higher levels of precision and accuracy. This will enable manufacturers to meet increasingly stringent quality requirements and produce intricate components with micron-level tolerances.
- Expansion of Axis Configurations: While 3-axis and 4-axis configurations are currently prevalent, there will be a growing demand for CNC routers with higher axis counts, such as 5-axis and even 6-axis machines. These configurations offer unparalleled versatility for machining complex geometries and multi-sided parts, opening up new possibilities for innovative design and manufacturing techniques.
- Advancements in Materials and Tooling: Future multi-axis CNC routers will be equipped to handle a broader range of materials, including advanced composites, ceramics, and metal alloys. This will necessitate the development of specialized cutting tools, coatings, and machining techniques tailored to specific material properties, enabling manufacturers to push the boundaries of material innovation and application diversity.
- Customization and Personalization: Multi-axis CNC routers will play a pivotal role in enabling mass customization and personalized manufacturing, catering to the growing demand for bespoke products and tailored solutions. Advanced CAM (Computer-Aided Manufacturing) software and AI-driven design tools will facilitate the rapid prototyping and production of custom components, empowering manufacturers to respond swiftly to evolving customer preferences and market trends.
The future trend of multi-axis CNC routers will be characterized by a convergence of advanced technologies, expanded capabilities, and a relentless pursuit of innovation to meet the evolving demands of modern manufacturing. By embracing these trends, manufacturers can unlock new opportunities for efficiency, flexibility, and competitiveness in the global marketplace.
Summarize
While both systems, 3-axis and 4-axis, offer remarkable precision and versatility, they serve distinct purposes and suit different applications. The 3-axis CNC router excels in producing flat and simple three-dimensional shapes with efficiency and accuracy, making it ideal for basic milling tasks. Conversely, the 4-axis CNC router introduces the capability to manipulate tools along an additional rotational axis, enabling the creation of more intricate and complex designs. This added axis enhances productivity and opens doors to a broader range of creative possibilities. By grasping the nuances between these CNC router configurations, manufacturers and hobbyists alike can optimize their machining processes and unlock the full potential of computer numerical control technology.
AccTek CNC is a well-known CNC router manufacturer in China. Our extensive product series can meet the production needs of different customers. From advanced 3-axis CNC routers to our versatile 4-axis models, each machine is meticulously engineered to deliver exceptional precision, reliability, and performance. At AccTek CNC, we understand that every project is unique, and that’s why we provide tailored CNC solutions to suit your specific requirements. Join us on a journey to elevate your machining experience and unlock new possibilities with AccTek CNC.