- 10-15 Min Read
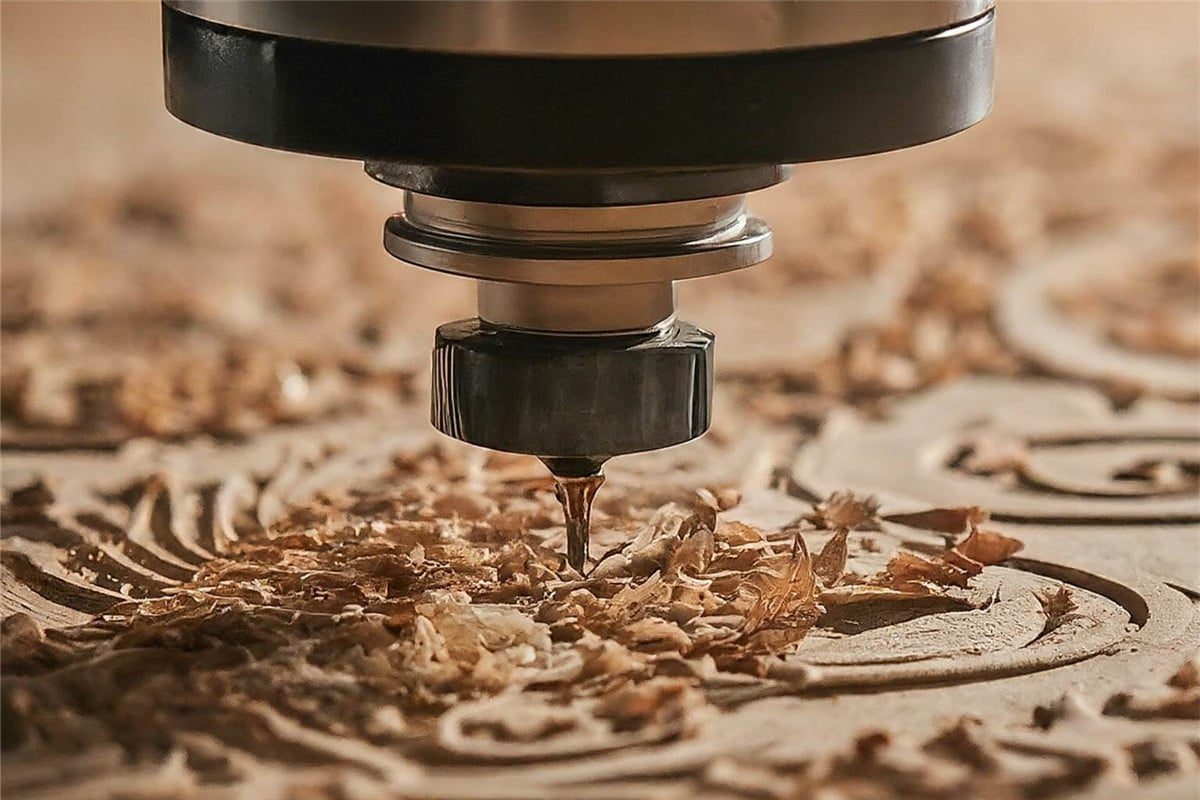
CNC router has revolutionized woodworking, offering precision and efficiency in crafting intricate designs, functional components, and decorative pieces. However, the success of any CNC routing project heavily depends on the type of wood you choose. Different woods have distinct properties, such as hardness, grain structure, and moisture content, which can influence the quality of cuts, the smoothness of finishes, and even the longevity of your CNC router bits. Understanding these characteristics is beneficial to selecting the best wood for your specific project, whether it’s a detailed engraving, furniture piece, or structural component.
In this article, we’ll explore the best wood species for CNC routing and discuss key factors that should influence your selection. Additionally, we’ll cover essential steps to prepare wood for CNC routing, ensuring smooth operations and high-quality outcomes. Finally, we’ll highlight important consideration to help you avoid common pitfalls and maximize the potential of your CNC router. Whether you’re a novice or an experienced professional, this guide will provide the insights you need to select and work with the ideal wood for your projects.
Understanding Wood Properties
When it comes to CNC routing, understanding the properties of wood is fundamental to achieving the best results. Each type of wood has unique characteristics that can influence how it behaves during cutting, engraving, or carving. These properties include grain structure, moisture content, hardness, and density, all of which play a role in determining the ease of machining, the finish quality, and the wear on your CNC tools.
Grain Structure
The grain structure of wood refers to the arrangement and orientation of wood fibers, which directly affects how the material behaves when cut or carved.
- Straight Grain: Woods with a straight grain, such as maple or walnut, are generally easier to work with for CNC routing. The fibers run in a consistent direction, reducing the risk of chipping or tear-out during machining. Straight-grained woods are ideal for projects that require clean, precise cuts.
- Interlocking Grain: Some woods, like mahogany, have interlocking or irregular grains. These can add visual appeal to finished pieces but present challenges during CNC routing, as the changing grain direction can cause splintering or uneven cuts.
- Open vs. Tight Grain: Open-grained woods, such as oak, have visible pores and may require additional finishing steps to achieve a smooth surface. Tight-grained woods, like cherry or birch, are naturally smoother and provide cleaner edges after routing.
- Figure and Patterns: Some woods have unique grain patterns, such as burl or curl, which can add aesthetic value but may demand specialized tools or techniques to handle the variable grain directions effectively.
Hardness and Density
Hardness and density determine the wood’s resistance to cutting and wear on CNC tools.
- Hardwoods vs. Softwoods: Hardwoods, such as oak, maple, and walnut, are denser and more resistant to wear. They produce sharp, detailed cuts but require higher tool durability and slower feed rates. Softwoods, like pine, spruce, and cedar, are lighter and less dense, making them easier to cut but prone to splintering or fuzziness at the edges.
- Density Impacts: Denser woods generally create smoother finishes due to their compact fiber structure. However, they also generate more heat and friction during cutting, potentially leading to quicker tool wear, and requiring periodic maintenance or replacement.
Moisture Content
Moisture content refers to the amount of water retained in the wood, which can significantly impact its behavior during CNC routing.
- Kiln-Dried vs. Green Wood: Kiln-dried wood is processed to achieve a stable moisture content, typically between 6% and 8%, making it less prone to warping, shrinking, or expanding. Green wood, or wood with high moisture content, is more likely to warp or deform during machining. It also tends to gum up tools and cause uneven cuts.
- Effects of Moisture Fluctuation: Even kiln-dried wood can absorb or lose moisture in response to its environment, which may result in slight dimensional changes. It’s important to store wood in a stable environment before CNC routing.
- Tools and Techniques for Moisture Management: Using a moisture meter to assess the wood before machining helps ensure consistent results. For projects requiring high precision, wood with consistent and low moisture content is required.
By thoroughly understanding these properties, CNC routing professionals and hobbyists can make informed decisions about wood selection, preparation, and tool settings, resulting in better performance and finished products.
Best Wood Types for CNC Routing
Selecting the right type of wood for CNC routing is beneficial to ensure high-quality results and efficiency in your projects. The following wood types are particularly well-suited for CNC routing, each offering unique benefits depending on your application:
Hardwoods
Hardwoods are denser and more durable, making them ideal for detailed work, furniture, and products that demand longevity.
- Maple: One of the most versatile hardwoods for CNC routing, maple is dense and produces crisp, detailed cuts. It’s great for intricate carvings, furniture, and cabinetry.
- Walnut: Known for its rich color and smooth grain, walnut is perfect for high-end decorative projects and fine furniture. Its moderate density allows for precise detailing.
- Oak: A durable hardwood with a prominent grain, oak is suitable for structural components, furniture, and rustic designs. It’s available in red and white varieties, both of which route well with sharp tools.
- Cherry: Valued for its smooth grain and warm tones, cherry is excellent for fine woodworking and projects requiring a premium finish.
Softwoods
Softwoods are easy to machine, lightweight, and cost-effective, making them popular for CNC routing projects that don’t require intricate details or heavy-duty durability.
- Pine: Known for its soft texture and ease of carving, pine is ideal for beginners and projects like signage or decorative pieces. However, its grain can sometimes splinter, requiring sharp tools and proper feed rates.
- Cedar: Lightweight and aromatic, cedar is excellent for outdoor applications like furniture or decorative items. Its straight grain ensures clean cuts, but it’s prone to minor chipping.
- Spruce: Often used in musical instruments and lightweight constructions, spruce offers a uniform texture that’s easy to work with on a CNC router.
Exotic Woods
For premium projects, exotic woods provide unique aesthetics and impressive strength, though they can be more challenging to work with.
- Teak: Known for its water resistance and rich grain, teak is ideal for outdoor furniture and luxury designs.
- Mahogany: A classic choice for fine furniture and decorative carvings, mahogany has a consistent grain that routes beautifully.
- Ebony: Ebony is extremely hard and dense, providing a high-gloss finish when polished. It is ideal for fine inlay work, musical instruments, and luxury items.
Engineered Woods
Engineered woods are manufactured products designed for consistency, making them ideal for CNC routing in specific applications.
- MDF (Medium-Density Fiberboard): MDF is one of the easiest materials to route, offering a uniform density and no grain to worry about. It’s widely used for signage, furniture, and prototypes. However, it creates fine dust, so proper ventilation and dust extraction are necessary.
- Plywood: Plywood is strong and versatile, with layers of wood veneer glued together. Baltic birch plywood is particularly popular for CNC projects due to its consistent core and durability.
- HDF (High-Density Fiberboard): Similar to MDF but denser and more durable, HDF is ideal for projects requiring a smooth finish and increased strength.
Choosing the best wood type for your CNC routing projects ensures optimal results, reduces waste, and enhances the overall quality of your work.
Factors Affecting Wood Selection for CNC Routing
The choice of wood for CNC routing is influenced by a variety of factors, particularly when considering the project requirements, processing complexity, and budget constraints. Below is a detailed exploration of each aspect:
Project Requirements
The specific needs of your project play a pivotal role in determining the best wood to use. Key considerations include:
- Aesthetics: Projects like furniture, decorative items, or signage often prioritize appearance. Woods such as walnut, cherry, or exotic species with rich grain patterns and vibrant colors are ideal for projects where visual appeal takes priority. For painted or veneered projects, cost-effective and uniform materials like MDF are suitable since the grain pattern is less important.
- Durability and Longevity: Projects exposed to wear and tear or environmental factors, such as outdoor furniture or load-bearing structures, require robust and weather-resistant woods like oak, teak, or cedar.
- Functional Application: Fine detailing or intricate carving requires woods with consistent grain and minimal splintering, such as maple, basswood, or birch. Structural projects, like framework or cabinetry, often benefit from denser hardwoods like ash or mahogany for strength and stability.
Processing Complexity
The machinability of wood is a critical factor, particularly for CNC routing. Woods vary in their workability based on their physical properties and how they interact with cutting tools.
- Grain Structure: Straight-grained woods, such as pine or maple, are easier to process, ensuring cleaner cuts and smoother finishes. Woods with interlocking or irregular grain, like mahogany, require slower feed rates and sharper tools to minimize chipping and tear-out.
- Hardness and Density: Hardwoods like oak or walnut provide excellent detail and durability but are harder to machine, requiring robust tools and careful settings. Softer woods like pine or cedar are easier to cut but may splinter or leave fuzzy edges that require additional sanding.
- Moisture Content: Kiln-dried wood with a stable moisture level (6-8%) is preferred for CNC processing to prevent warping or inconsistent cuts. High-moisture or green wood can clog tools and result in uneven machining, increasing processing difficulty.
- Tool Wear and Maintenance: Dense or abrasive woods, such as teak, can cause significant tool wear, necessitating frequent sharpening or replacement of CNC bits. Engineered woods like MDF are easy to machine but produce fine dust that may require additional cleanup and ventilation measures.
Budget Constraints
Cost is often a decisive factor when selecting wood for a project. Balancing the desired qualities of the wood with the available budget ensures that resources are allocated effectively.
- Softwoods for Budget-Friendly Options: Woods like pine or spruce are affordable, widely available, and easy to work with, making them suitable for large-scale projects or prototypes. Plywood and MDF are economical choices for functional or painted projects, providing consistent quality at a lower cost.
- Hardwoods for Premium Projects: High-quality hardwoods such as walnut, cherry, or maple are more expensive but deliver superior aesthetics and durability, making them ideal for high-end or decorative items. Exotic woods like ebony or mahogany command a premium price due to their rarity and unique appearance, but they add exceptional value to luxury projects.
- Engineered Woods for Cost-Effectiveness: Engineered materials like MDF or Baltic birch plywood offer a balance of affordability and performance, especially for projects requiring smooth finishes or uniformity.
- Waste Management: For projects with tight budgets, selecting wood that minimizes waste and offcuts can help reduce overall costs.
By evaluating wood selection through the lens of project requirements, processing complexity, and budget constraints, you can make informed decisions that meet both the practical and aesthetic goals of your CNC routing project while staying within financial limits.
Preparing Wood for CNC Routing
Proper preparation of wood is a critical step to ensure optimal performance and high-quality results in CNC routing. By taking the time to prepare the wood correctly, you can avoid issues such as uneven cuts, tool damage, or poor surface finishes. Here are the key steps to prepare wood for CNC routing:
Moisture Content
Managing the moisture content of wood is beneficial to achieving precise and consistent results in CNC routing. Excess moisture can lead to warping, swelling, or uneven cuts, while overly dry wood may become brittle and prone to splintering.
- Ideal Moisture Levels: The recommended moisture content for wood used in CNC routing is typically between 6% and 8%. This ensures the wood is stable and unlikely to warp or change dimensions during machining. Kiln-dried wood is preferred because it has a controlled and consistent moisture level, making it reliable for precise cuts.
- Testing Moisture Content: Use a moisture meter to measure the wood’s moisture level before CNC routing. Insert the meter probes into the wood to get an accurate reading. Avoid using wood that exceeds the ideal moisture range, as it may lead to tool clogging and dimensional inconsistencies.
- Drying the Wood: If the wood has excessive moisture, allow it to air-dry in a well-ventilated, temperature-controlled space. For faster results, use a dehumidifier or place the wood in a drying kiln. Let the wood acclimate to the workshop environment for several days to ensure it stabilizes at a consistent moisture level.
Surface Treatment
Proper surface treatment ensures the wood is smooth, clean, and ready for precise machining. This minimizes issues such as chipping, tear-out, or uneven finishes.
- Flattening the Surface: Pass the wood through a planer to achieve a uniform thickness and a flat surface. Use a jointer to create straight, square edges if needed. This step ensures accurate alignment during CNC routing.
- Sanding the Surface: Lightly sand the wood with fine-grit sandpaper to remove surface irregularities, small splinters, or rough patches. For woods with a coarse grain, additional sanding may be necessary to achieve a smooth finish.
- Cleaning the Surface: Remove dust, dirt, or debris using a damp cloth or compressed air. Clean wood ensures better tool contact and reduces wear on CNC router For engineered woods like MDF, wipe the surface gently to avoid raising fibers.
- Protective Coating (Optional): For softwoods or highly porous woods, apply a thin layer of sealant or use masking tape to protect the surface from splintering and reduce edge tear-out.
- Check for Defects: Inspect the wood for cracks, knots, or resin pockets that could interfere with machining. Remove or avoid these areas when positioning the material on the CNCrouter
By properly managing moisture content and performing thorough surface treatment, you can ensure that the wood is stable, smooth, and ready for precise CNC routing. These steps reduce the risk of machining errors, tool wear, and subpar finishes, leading to a more successful final project.
Precautions for CNC Routing
When routing wood using a CNC machine, adhering to specific precautions ensures safety, precision, and prolonged equipment life. Below are the key precautions categorized into tooling selection, speed and feed rate, and dust and chip removal. Below are the key factors to consider when working with wood in CNC routing:
Tooling Selection
Using the appropriate tools ensures clean cuts and prolongs tool life.
- Choose the Right Bit Type: Use carbide-tipped bits for hardwoods and engineered woods, as they are durable and resist heat better than high-speed steel (HSS) bits. For intricate details, select bits like V-bits or ball nose bits, while end mills are ideal for straight cuts.
- Inspect Tools Before Use: Ensure router bits are sharp and free from damage or resin buildup, which can cause rough edges and reduce cutting accuracy. Avoid using dull tools, as they can overheat, burn the wood, and strain the CNC router.
- Match the Bit to the Wood: Softer woods require bits with broader flutes for faster chip evacuation, while harder woods benefit from narrower flutes that provide better precision.
Speed and Feed Rate
Optimizing cutting parameters reduces errors and improves efficiency.
- Set Appropriate Spindle Speed: Adjust the spindle speed based on the wood’s hardness and density. Use higher spindle speeds for softwoods and slower speeds for hardwoods to avoid burning or excessive tool wear. For example, pine may require 18,000–20,000 RPM, while oak might perform best at 12,000–15,000 RPM.
- Adjust Feed Rate: A balanced feed rate prevents chipping and ensures smooth cuts. If the feed rate is too slow, the tool may overheat and burn the wood, if too fast, the wood may splinter or produce rough edges. Users can perform test cuts to fine-tune feed rates for specific materials and tools.
- Limit Depth of Cut: For harder woods or thicker pieces, make multiple shallow passes instead of a single deep cut. This reduces strain on the tool and improves precision.
Dust and Chip Removal
CNC routing generates wood chips and fine dust, which must be managed effectively.
- Use a Dust Collection System: CNC routing produces fine wood dust that can affect health and machine performance. Connect a dust extractor to the wood CNC router to capture dust at the source.
- Install Chip Evacuation Features: Use bits with specialized flute designs for efficient chip evacuation. Poor chip removal can clog tools, reduce cutting accuracy, and overheat the wood.
- Ensure Adequate Ventilation: Ensure proper airflow in the workspace to minimize health risks associated with inhaling wood dust.
- Keep the Workspace Clean: Regularly pause operations to clear accumulated chips and dust around the wood CNC router.
By prioritizing tooling selection, fine-tuning speed and feed rate, and managing dust and chip removal, you can ensure efficient, safe, and high-quality CNC routing of wood. These precautions not only enhance the final product but also extend the life of your tools and machinery.
Summarize
Selecting the best wood for CNC routing depends on your project requirements, processing capabilities, and budget considerations. Whether crafting intricate designs, producing durable furniture, or experimenting with creative prototypes, understanding the properties of different woods is key to achieving optimal results. Combined with proper preparation, tooling, and machine settings, your choice of wood can transform your CNC routing projects into precise and professional masterpieces. To learn more about woodworking CNC routing, read “How to Choose the Perfect Woodworking CNC Router Bit.”
If you’re looking for precision, reliability, and exceptional performance in CNC routing, AccTek CNC is the ideal choice. As a professional CNC router manufacturer in China, AccTek offers advanced machines designed to handle a wide variety of wood types with ease. Whether you’re working with softwoods, hardwoods, or engineered woods, AccTek’s CNC routers are equipped with robust tooling options, customizable settings, and efficient dust management systems to deliver superior results. AccTek CNC is your excellent partner for achieving precision and creativity in woodworking.