- 12-17 Min Read
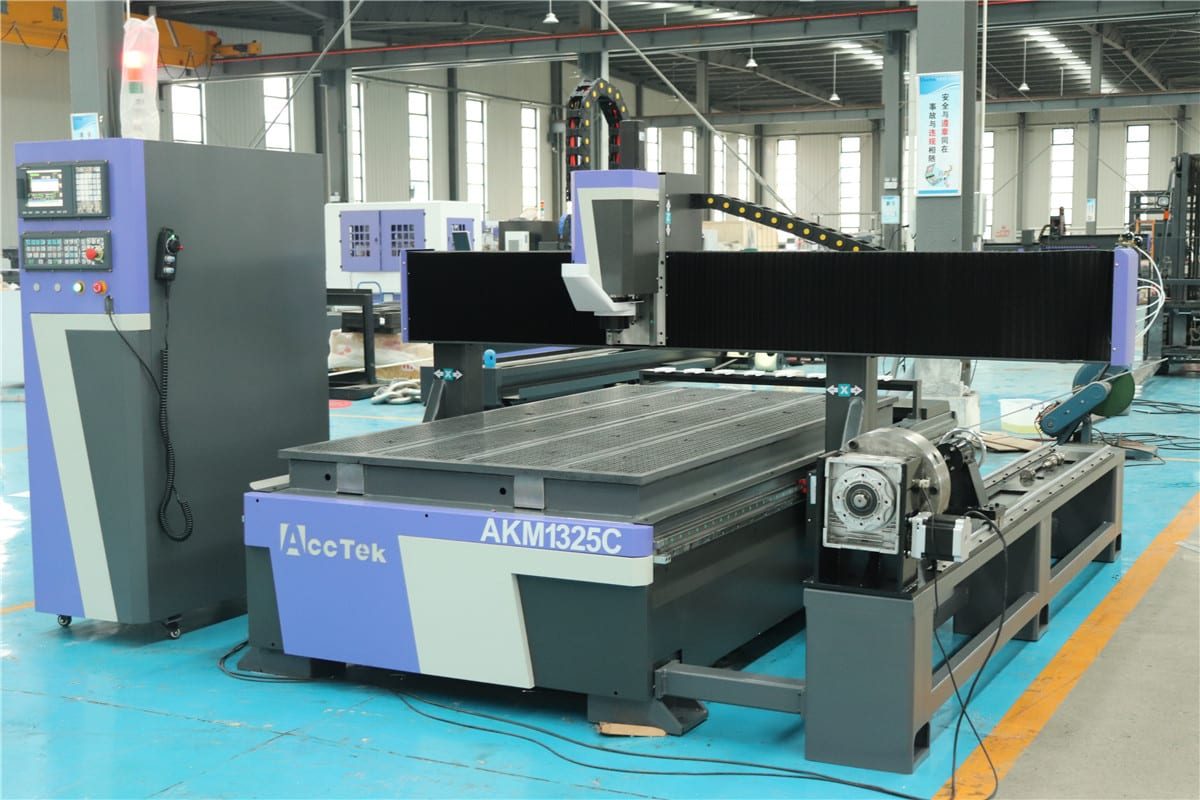
A rotary axis CNC router is a versatile and advanced piece of machinery that extends the capabilities of traditional CNC routers by adding a fourth rotational axis. This additional axis allows the machine to perform complex and intricate operations on cylindrical objects, such as carving, engraving, and machining round materials like wood, and plastic. This makes the rotary axis CNC router an essential tool for industries that require high-precision machining of complex shapes.
This article will delve into the fundamental aspects of rotary axis CNC routers, exploring their unique capabilities, applications, and the benefits they bring to various sectors. The integration of a rotary axis into a CNC router transforms the machine into a multifunctional tool capable of handling a wide range of applications. Whether you are a seasoned machinist or a curious enthusiast, exploring the world of rotary axis CNC routers can provide valuable insights into the advancements in modern machining technology.
Understanding Rotary Axis CNC Router
The Rotary Axis CNC Router is a revolutionary machine that enhances traditional CNC capabilities by introducing an additional rotary axis. Unlike standard CNC routers, which operate along three linear axes (X, Y, and Z), a rotary axis CNC router incorporates a fourth axis. This additional axis allows the machine to rotate the workpiece, enabling complex and intricate designs that are impossible to achieve with linear movement alone.
What is a Rotary Axis CNC Router
A rotary axis CNC router is an advanced computer numerical control (CNC) machine that integrates a rotational axis into its standard three-axis configuration. This addition, commonly known as the A-axis, enables the workpiece to be rotated around a fixed axis, allowing for more complex and detailed machining processes. The rotary axis adds a new dimension to the machine’s capabilities, making it ideal for projects requiring cylindrical or symmetrical components.
Functions of Rotary Axis CNC Routers
The primary function of a rotary axis CNC router is to provide enhanced flexibility and precision in machining tasks. By incorporating rotational movement, these routers can handle tasks that involve curved surfaces, cylindrical objects, and intricate patterns that are difficult or impossible to achieve with standard three-axis CNC routers. The rotary axis allows for continuous rotation of the workpiece, enabling seamless machining of 360-degree surfaces, detailed carvings, and intricate designs on round objects. Rotary axis CNC routers are especially valued in industries where cylindrical or irregularly shaped objects require precise machining.
Types of Rotary Axis
Rotary axes in CNC routers can be categorized based on their placement and mounting configuration, each offering unique advantages depending on the specific machining needs. The primary types include:
- Rotary Axis Placed Directly on the Worktable: These rotary axes are mounted directly onto the workbench or the bed of the CNC router. This setup allows for easy installation and removal, making it versatile for a variety of tasks. The direct placement on the workbench is ideal for projects that require machining of cylindrical or symmetrical objects, such as table legs, columns, and decorative spindles. This configuration is commonly used in woodworking and furniture manufacturing.
- Rotary Axis Fixed on the Side of the Machine: In this configuration, the rotary axis is mounted on the side of the CNC router, providing a fixed rotational point adjacent to the main working area. This setup is beneficiall for machining longer or larger workpieces that need to be supported along their length. Fixing the rotary axis on the side, it ensures stability and precision during the machining process, making it suitable for tasks such as engraving, milling, and complex surface detailing on elongated objects.
- Rotary Axis Fixed in Front of the Table: A rotary axis fixed in front of the table offers a distinct advantage for specific applications where the workpiece needs to be rotated and machined from the front. This configuration allows for unobstructed access to the workpiece, making it easier to perform intricate detailing and finishing tasks. It is particularly useful in scenarios where continuous access to the workpiece is required. The front-mounted rotary axis provides a stable and accessible platform for precision machining.
Components of a Rotary Axis CNC Router
A rotary axis CNC router enhances the capabilities of traditional CNC machines by incorporating an additional axis of rotation. Among them, the turntable, rotary axis drive system, and controller software are the key components of the rotary axis CNC router. Here are the details of these components:
- Turntable: The turntable enables the rotation of the workpiece to achieve complex machining tasks. The turntable often includes a chuck or other fixtures to securely hold the workpiece in place. These fixtures can be adjusted to accommodate different sizes and shapes of workpieces, ensuring versatility in machining applications.
- Rotary Axis Drive System: The rotary axis drive system is responsible for controlling the rotational movement of the turntable. This system typically features a high-precision motor, such as a stepper motor or a servo motor, to control the rotation of the turntable. Servo motors are often preferred for their ability to provide precise feedback to the control system, ensuring accurate positioning and movement.
- Controller Software: The controller software is the brain of the rotary axis CNC router, managing and coordinating all aspects of the machining process. The controller software interprets G-code, the programming language used to instruct CNC machines. It converts the design files into precise movements of the linear and rotary axes, ensuring that the machine follows the desired tool paths.
A rotary axis CNC router is a powerful tool that expands the capabilities of traditional CNC machines. By incorporating an additional rotational axis, these routers enable more complex and detailed machining processes, opening up new possibilities in various industries.
Application of Rotary Axis CNC Router
Rotary axis CNC routers have significantly expanded the capabilities of traditional CNC machines, enabling a range of advanced processing techniques. Its ability to rotate the workpiece along an additional axis allows for more intricate and complex machining tasks. Here are some key applications of rotary axis CNC routers:
3D Engraving
3D engraving with a rotary axis CNC router allows for the creation of intricate, three-dimensional designs on various materials. The rotary axis adds an extra dimension to the machine, enabling it to carve complex shapes and patterns that are not possible with a standard 2D CNC router. This is particularly useful for creating detailed sculptures, reliefs, and prototypes in wood, foam, and other materials. The ability to rotate the workpiece means that the machine can access all angles, ensuring a high level of detail and precision in the final product.
Rotary Engraving
Rotary engraving involves the continuous rotation of the workpiece while the router bit carves into it. This technique is ideal for cylindrical objects like columns, balusters, table legs, and other rounded components. The rotary axis ensures that the design is evenly distributed around the circumference of the object, providing a seamless finish. This application is highly valued in furniture manufacturing, decorative arts, and custom woodwork, where detailed patterns and text can be engraved onto the surface of cylindrical items.
Tube Cutting
Tube cutting involves precisely cutting and machining tubular materials, allowing for complex cuts, holes, and shapes to be made along the length of the tube. The rotary axis ensures that the cuts are uniform and can be made at various angles, enhancing the versatility of the machine. This capability helps create custom tubing components for furniture frames, legs, and supports.
Multi-Faceted Processing
Multi-faceted processing refers to the ability of the rotary axis CNC router to machine different sides of a workpiece without the need for manual repositioning. This feature is highly beneficiall for creating workpieces that require complex shapes to be machined on multiple faces. The rotary axis can rotate the workpiece to expose different surfaces to the cutting tool, ensuring consistent accuracy and reducing production time.
The applications of rotary axis CNC routers in 3D engraving, rotary engraving, tube cutting, and multi-faceted processing demonstrate their versatility and precision. These capabilities enable the creation of intricate and detailed products across various industries, enhancing productivity and expanding the possibilities in modern machining and fabrication. Whether for artistic endeavors, industrial manufacturing, or educational purposes, rotary axis CNC routers are essential tools in modern machining and fabrication.
Advantages and Limitations of Rotary Axis CNC Routers
Rotary axis CNC routers offer enhanced capabilities and precision compared to traditional three-axis CNC machines. However, like any advanced technology, they come with their own set of advantages and limitations. Understanding these can help users make informed decisions about their applications and uses.
Advantages
- Enhanced Versatility: Rotary axis CNC routers can machine complex shapes and designs that are difficult or impossible to achieve with traditional 3 axis CNC routers. This includes cylindrical objects, 3D surfaces, and intricate patterns. This versatility means that a single machine can handle a wide range of projects, from intricate sculptures and detailed furniture components to precision-engineered tubes and multi-surface parts.
- Improve Precision and Accuracy: The additional axis allows for precise control over the rotation of the workpiece, enabling high-precision machining of detailed designs and intricate patterns. The ability to rotate the workpiece ensures uniformity and consistency in machining, resulting in higher quality finished products. The enhanced precision reduces the likelihood of errors and ensures that the final product meets stringent quality standards.
- Time and Cost Savings: The rotary axis eliminates the need for frequent repositioning of the workpiece, saving time and reducing the risk of errors. This is particularly beneficiall for complex multi-faceted processing. This streamlining of operations leads to faster production times and lower labor costs.
- Reduced Material Waste: Accurate cuts and engravings mean that there is less scrap material and fewer mistakes that require starting over with new materials. This efficiency is not only cost-effective but also environmentally friendly, as it maximizes the use of raw materials and minimizes waste. The ability to perform detailed work on cylindrical objects and multiple surfaces without repositioning also reduces the risk of errors that can lead to wasted material.
Limitations
- Higher Cost: Rotary axis CNC routers are generally more expensive than traditional three-axis CNC machines due to their advanced components and capabilities. The additional complexity of the machine may result in higher maintenance and repair costs over time. While the long-term benefits and efficiencies gained from using a rotary axis CNC router can offset the initial expense, the high upfront cost remains a barrier for some potential users.
- Increased Complexity: The addition of a rotary axis introduces a higher level of operational complexity to CNC routers. Operators need to be skilled in setting up and programming the machine for multi-axis operations, which can require additional training and experience. The complexity of the software and the need for precise calibration of the rotary axis can also present challenges. Ensuring that the workpiece is correctly positioned and aligned for each operation adds to the complexity of using these advanced machines.
- Potential for Increased Wear and Tear: The continuous rotation and additional axis movements can lead to increased wear and tear on the machine components, potentially reducing the lifespan of certain parts. Over time, the precision of the rotary axis may degrade due to mechanical wear, necessitating regular maintenance and calibration.
While rotary axis CNC routers offer significant advantages in terms of versatility, precision, and efficiency, they also come with certain limitations such as higher costs and increased complexity. Despite the limitations, the long-term gains in efficiency and capability often justify the investment in a rotary axis CNC router.
Considerations for Selecting a Rotary Axis CNC Router
Choosing the right rotary axis CNC router for your needs involves evaluating several critical factors to ensure it meets your specific requirements. Here are key considerations to keep in mind when selecting a rotary axis CNC router:
Machine Size and Capacity
- Work Area Dimensions: Ensure that the CNC router has a sufficient work area to accommodate the largest workpieces you plan to machine. The size of the machine should match your production needs and fit within your available workspace.
- Rotary Axis Capacity: Assess the maximum diameter and length of the workpieces that the rotary axis can handle. This has a significant impact on projects involving large cylindrical or tubular components.
- Footprint: Consider the overall footprint of the machine, including the space required for the rotary axis. Ensure that it fits comfortably within your workshop or manufacturing facility without causing space constraints.
Rotary Axis Configuration
- Placement and Flexibility: Determine whether the rotary axis is placed directly on the workbench, fixed on the side of the machine, or mounted in front of the table. Each configuration has its benefits and should be chosen based on your specific machining tasks and workpiece requirements.
- Rotary Table or Chuck: Evaluate the type of rotary table or chuck used to hold the workpiece. Ensure it provides secure and stable clamping for various workpiece shapes and sizes.
- Rotation Speed and Precision: Check the rotation speed and precision of the rotary axis. High precision and variable speed control are beneficiall for achieving detailed and accurate machining on cylindrical surfaces.
Machine Rigidity and Stability
- Frame Construction: The machine frame and base should be made from durable materials such as steel or cast iron to ensure rigidity and minimize vibrations during operation.
- Support Structures: Consider the quality of linear guides, bearings, and support structures. High-quality components contribute to the overall stability and longevity of the machine, ensuring consistent performance over time.
- Vibration Dampening: Look for features that help dampen vibrations, such as reinforced frames, additional support beams, or specialized damping materials. Reducing vibrations improves machining accuracy and surface finish quality.
Compatibility with CAM Software
- Software Integration: Ensure that the CNC router is compatible with your existing CAD/CAM software. Seamless integration allows for efficient workflow and reduces the learning curve for operators.
- Advanced Features: Check if the software supports advanced features such as simulation, error detection, and toolpath optimization. These features enhance productivity and help prevent costly mistakes.
- User Interface: The software should have an intuitive and user-friendly interface, allowing operators to easily create and modify machining programs. Training and support for the software are also important considerations.
Tooling and Workpiece Fixtures
- Tool Holders and Spindles: Evaluate the types of tool holders and spindles available with the machine. Ensure they are suitable for the materials and cutting tools you will be using. High-speed spindles and quick-change tool holders can enhance efficiency.
- Fixture Versatility: The machine should come with versatile fixtures that can securely hold various shapes and sizes of workpieces. Adjustable fixtures increase the machine’s adaptability to different projects.
- Custom Fixtures: Depending on your specific needs, you may require custom fixtures or clamps to hold irregularly shaped workpieces. Ensure that the machine can accommodate and integrate custom fixtures as needed.
By evaluating these factors, you can ensure that the CNC router you choose will meet your machining requirements, provide high precision and efficiency, and support your production goals effectively.
Tips for Effectively Using Rotary Axis CNC Routers
Effectively using a rotary axis CNC router requires understanding its capabilities, proper setup, and efficient operation. Here are some practical tips to help you get the most out of your rotary axis CNC router:
Proper Setup and Calibration
- Accurate Alignment: Ensure that the rotary axis is precisely aligned with the CNC router’s linear axes. Misalignment can lead to errors and inaccuracies in your machining projects.
- Secure Clamping: Use appropriate fixtures and clamps to securely hold the workpiece on the rotary axis. A stable workpiece ensures accurate and consistent machining results.
- Tool Calibration: Regularly calibrate your tools to maintain cutting precision. Incorrect tool calibration can result in poor-quality cuts and increased wear on the tool and machine.
Optimized Toolpaths and Machining Strategies
- Use CAM Software: Utilize advanced CAD/CAM software to generate optimized toolpaths for your machining projects. This software helps in planning efficient cutting sequences and avoiding collisions.
- Simulation: Run simulations of your toolpaths before actual machining to identify potential issues and make necessary adjustments. This step helps prevent costly errors and material waste.
- Appropriate Cutting Parameters: Adjust the cutting speed, feed rate, and depth of cut based on the material and the complexity of the design. Using the right parameters ensures better surface finish and prolongs tool life.
Test Cuts and Prototyping
- Initial Test Cuts: Perform test cuts on scrap material before starting on the actual workpiece. This practice helps in verifying the toolpath and adjusting settings as needed.
- Prototyping: Create prototypes to test the design and machining process. Prototyping helps in refining the design and ensuring that the final product meets the desired specifications.
- Iterative Adjustments: Based on the results of test cuts and prototypes, make iterative adjustments to the toolpath, cutting parameters, and workpiece setup to achieve optimal results.
Operator Training and Safety
- Proper Training: Ensure that operators are properly trained in using the rotary axis CNC router. Training should cover machine setup, operation, maintenance, and safety protocols.
- Safety First: Always prioritize safety when operating the CNC router. Use personal protective equipment (PPE) such as safety glasses, ear protection, and dust masks. Follow safety guidelines and procedures to prevent accidents.
- Emergency Protocols: Familiarize operators with emergency stop procedures and other safety features of the machine. Quick response in case of an emergency can prevent injuries and damage.
By following these tips, you can effectively utilize your rotary axis CNC router, achieving high precision, efficiency, and quality in your machining projects. Proper setup, maintenance, and continuous learning are key to maximizing the potential of your CNC router and ensuring long-term success.
Maintenance and Care of Rotary Axis CNC Router
Proper maintenance and care are beneficial for ensuring the longevity, performance, and accuracy of a rotary axis CNC router. Regular maintenance helps prevent unexpected downtime, reduces repair costs, and extends the machine’s lifespan. Here are key areas to focus on for maintaining and caring for your rotary axis CNC router:
Routine Cleaning and Lubrication
- Daily Cleaning: After each use, clean the machine thoroughly to remove dust, debris, and chips. Pay special attention to the rotary axis and linear guides, as accumulated debris can affect precision and movement.
- Lubrication: Regularly lubricate all moving parts, including the linear guides, bearings, and rotary axis. Use the manufacturer-recommended lubricants and follow the specified lubrication schedule to ensure smooth operation.
- Coolant System: If your CNC router uses a coolant system, check and clean the coolant reservoir regularly. Replace the coolant as needed to maintain its effectiveness and prevent contamination.
Inspection and Adjustment
- Alignments: Regularly check the alignment of the rotary axis and linear axes. Misalignment can lead to inaccuracies and increased wear on machine components. Adjust as necessary to maintain precise alignment.
- Component Inspection: Inspect critical components such as belts, pulleys, and motors for signs of wear or damage. Replace worn or damaged parts promptly to avoid further issues and ensure optimal performance.
- Rotary Axis Bearings: Check the rotary axis bearings for smooth operation. If you notice any roughness or play, it may be time to replace the bearings to maintain accuracy.
Tool and Spindle Maintenance
- Tool Inspection: Regularly inspect cutting tools for wear and damage. Dull or damaged tools can negatively impact the quality of your work and increase the strain on the machine. Replace tools as needed.
- Spindle Care: Check the spindle for any signs of wear or overheating. Ensure that the spindle is properly lubricated and balanced. If the spindle shows signs of excessive wear or damage, consider professional servicing or replacement.
Electrical System Checks
- Connections: Inspect electrical connections for signs of wear, corrosion, or looseness. Tighten any loose connections and replace damaged wires or connectors.
- Control System: Ensure that the control system and its components, such as the controller and interface, are functioning correctly. Look for any error messages or unusual behavior that might indicate a problem.
Environmental Control
- Dust and Debris Management: Use a dust collection system to manage dust and debris generated during machining. Keeping the work area clean reduces wear on the machine and improves air quality.
- Temperature and Humidity: Maintain a stable temperature and humidity level in the workshop. Extreme conditions can affect the machine’s components and accuracy. Use climate control systems if necessary.
By following these maintenance and care tips, you can ensure that your rotary axis CNC router operates efficiently and reliably. Regular maintenance not only extends the machine’s lifespan but also ensures that it continues to produce high-quality work with precision and consistency.
Summarize
In the dynamic world of manufacturing and machining, the rotary axis CNC router stands out as a versatile and powerful tool, capable of transforming complex designs into tangible products with precision and efficiency. By integrating an additional axis of rotation, these machines unlock new dimensions of creativity and functionality, enabling the production of intricate and detailed workpieces that are beyond the reach of traditional three-axis CNC routers. As technology continues to evolve, rotary axis CNC routers will undoubtedly play a pivotal role in pushing the boundaries of what is possible in machining.
If you are in the market for high-quality CNC routers, look no further than AccTek CNC. As a professional CNC router manufacturer, AccTek CNC offers a comprehensive range of machines designed to meet the diverse needs of modern machining and manufacturing. Whether you need a standard 3-axis CNC router or a sophisticated 5-axis or rotary axis CNC router, AccTek CNC has the perfect solution to meet your machining needs. Discover the difference that professional-grade CNC routers can make in your operations by choosing AccTek CNC.