- 10-15 Min Read
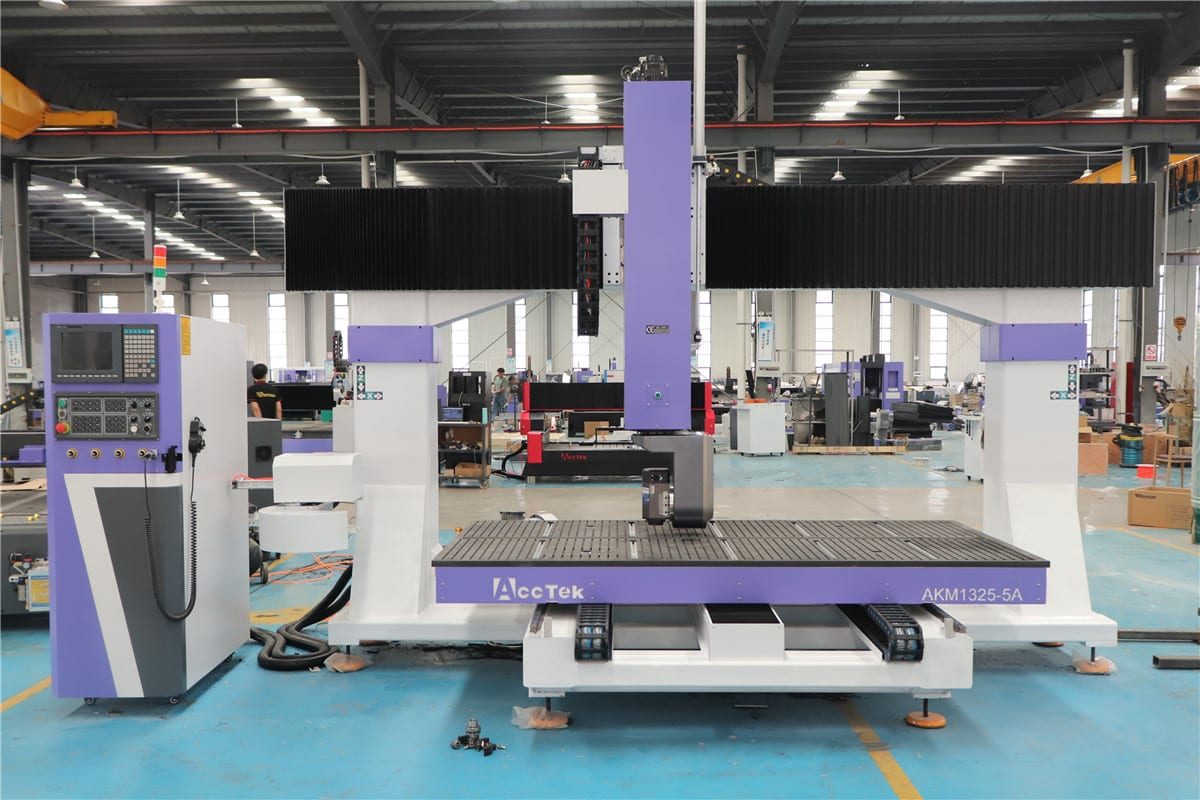
In the realm of advanced manufacturing and precision machining, the 5-axis CNC router stands as a pinnacle of versatility and accuracy. Unlike 3-axis CNC routers and 4-axis CNC routers, 5-axis CNC routers offer unparalleled freedom of motion, enabling precise manipulation of workpieces from multiple angles. This technology has revolutionized industries ranging, enabling complex designs and intricate details that were once challenging or impossible to achieve. The versatility and precision of 5-axis CNC routers have opened new horizons for designers, engineers, and artists alike. By enabling the machining of complex shapes and surfaces in a single setup, these machines significantly reduce production time and costs while improving accuracy and quality.
In this article, we delve into what exactly defines a 5-axis CNC router, how it works, its applications across various sectors, and the advantages it brings to modern manufacturing processes. Whether you are a seasoned professional in the manufacturing field or a curious enthusiast, understanding the capabilities and advantages of 5-axis CNC routers will provide valuable insights into the future of precision engineering.
The Basics of 5 Axis CNC Router
In the realm of modern manufacturing and precision machining, the 5-axis CNC router represents a significant leap forward in technology and capability. Unlike traditional 3-axis CNC routers that operate along three linear axes (X, Y, and Z), 5-axis CNC routers add two rotational axes, offering unparalleled flexibility and precision. To fully appreciate the capabilities of this sophisticated equipment, it is essential to delve into its fundamental principles and configuration.
How a 5-Axis CNC Router Works
The operation of a 5-axis CNC router is a complex interplay of computer programming, mechanical precision, and material science. Here’s a step-by-step overview of how it works:
- Designing the Part: The process begins with designing the part using CAD software. The designer creates a detailed 3D model of the part, specifying all dimensions, shapes, and features.
- Generating the Toolpath: Once the design is complete, it is imported into CAM software, which generates the toolpath. The toolpath is a series of instructions that tell the CNC router how to move the cutting tool to create the part. This includes all movements in the X, Y, Z, A, and B axes.
- Setting Up the Machine: The material to be machined is secured to the worktable of the CNC router. The cutting tools are installed in the spindle, and the machine is calibrated to ensure precise movements.
- Machining the Part: The CNC router begins the machining process, following the toolpath generated by the CAM software. The machine moves the cutting tool along the programmed path, making precise cuts, carvings, or shapes in the material. The ability to rotate the workpiece or the cutting tool around the A and B axes allows for complex geometries and undercuts to be machined.
Configuration of a 5-Axis CNC Router
The configuration of a 5-axis CNC router can vary based on the design and intended application, but it typically includes several key components. Here’s an overview of its configuration:
- Axes: X, Y, and Z axes are the standard linear axes found in 3-axis CNC machines. They control the movement of the tool or workpiece in three-dimensional space. A and B Axes, these additional axes provide rotational movement, allowing the tool to approach the workpiece from different angles.
- Spindle: The spindle holds the cutting tool and is responsible for its rotation. In a 5-axis CNC router, the spindle must be highly precise and capable of rotating at high speeds to ensure accurate cutting and shaping.
- Controller: The controller is the brain of the CNC router. It interprets G-code (the programming language for CNC machines) and sends precise instructions to the motors that control the axes.
- Worktable: The workpiece is secured to the table, which can be stationary or have additional movement capabilities.
- Motors and Drives: High-precision motors (often servo motors) and drives are used to move the axes accurately. These components must provide smooth and precise motion to achieve the desired quality in the finished part.
- Software: CNC routers rely on CAD (Computer-Aided Design) and CAM (Computer-Aided Manufacturing) software to design parts and generate the necessary G-code for machining.
- Auto Tool Changer: Some 5-axis CNC routers are equipped with an automatic tool changer (ATC) that allows the machine to switch between different tools without manual intervention. This increases efficiency and allows for more complex machining operations.
- Cooling System: Machining generates heat, which can affect both the tool and the workpiece. A cooling system (usually involving a coolant fluid) helps to manage temperatures, prolong tool life, and ensure consistent machining quality.
Advantages and applications of 5-axis CNC router
5-axis CNC routers provide significant advantages in precision, efficiency, and versatility, making them indispensable tools in various high-demand industries. In this section, we will explore the key advantages of 5-axis CNC routers and delve into their diverse applications, highlighting how they contribute to innovation and excellence in production processes.
Advantages
The advantages of a 5-axis CNC router make it a valuable asset for manufacturers looking to enhance their machining capabilities, improve efficiency, and produce high-quality parts with greater precision and versatility. The 5-axis CNC router has many advantages compared with the traditional 3-axis CNC router, which is specifically reflected in the following aspects:
- Complex Geometries: 5-axis CNC routers can create highly complex and intricate shapes that are impossible with three-axis machines. This includes workpieces with curved surfaces, undercuts, and intricate details.
- Reduced Setup Time: With the ability to machine from multiple angles in a single setup, 5-axis CNC routers significantly reduce the need for multiple setups and repositioning of the workpiece. This saves time and increases efficiency.
- Improved Surface Finish: The ability to use shorter cutting tools and approach the workpiece from optimal angles reduces vibration and deflection, resulting in a superior surface finish.
- Greater Precision: The additional axes allow for more precise control over the cutting tool, resulting in higher accuracy and repeatability.
- Increased Productivity: By reducing setup times and enabling more complex parts to be machined in a single operation, 5-axis CNC routers can significantly increase productivity and throughput.
Applications
The applications of a 5-axis CNC router are diverse and varied across different industries due to its enhanced capabilities for complex machining operations. This demonstrates their versatility and importance in modern manufacturing and fabrication processes. Here are some common applications:
- Art and Sculpture: Artists and sculptors use 5-axis CNC routers to create intricate and detailed works of art. The ability to machine from multiple angles allows for the creation of complex and realistic sculptures that would be difficult to achieve by hand.
- Custom Furniture and Cabinetry: 5-axis CNC routers enable the production of intricate furniture designs, custom cabinetry, and detailed carvings. The precision and versatility of these machines open up new possibilities for creativity and craftsmanship.
- 3D Model: The 5-axis CNC router machine is used for 3D milling in mold making, especially for car body making, boat mold building, and other 3D modeling projects.
- Mold Making: Manufacturing molds for injection molding, vacuum forming, or other molding processes can benefit from the capabilities of a 5-axis CNC router. These machines can produce complex mold designs with precise details and contours, suitable for producing a wide range of plastic, metal, or composite parts.
- Prototyping and Model Making: In industries ranging from product design to architectural modeling, 5-axis CNC routers are used to create prototypes and models of various shapes and sizes with high accuracy. These machines can accurately replicate intricate designs, allowing for rapid prototyping and iterative design processes.
- Sign Making and Engraving: The versatility of 5-axis CNC routers makes them suitable for sign making, engraving, and artistic applications. They can produce detailed signage, plaques, and decorative elements on a variety of materials including wood, plastic, metal, and composites.
- Educational and Research Purposes: 5-axis CNC routers are also used in educational institutions and research facilities for teaching purposes and conducting experiments. They provide students and researchers with hands-on experience in computer-aided design (CAD) and computer-aided manufacturing (CAM) processes, as well as exploring advanced machining techniques.
Challenges in 5-Axis CNC Routing
While 5-axis CNC routers offer significant advantages in terms of precision, flexibility, and efficiency, they also present unique challenges. Understanding and addressing these challenges is beneficiall for successful operation and maximizing the potential of these advanced machines.
Technical Challenges
- Complexity of Programming: Creating accurate and efficient toolpaths for 5-axis machining is complex. CAM software must handle the intricate movements and rotations of the cutting tool, which requires advanced algorithms and a deep understanding of the machining process.
- Machine Calibration and Setup: Setting up the machine, securing the workpiece, and calibrating the tools can be time-consuming, especially for complex parts that require multiple fixtures and alignments. Any misalignment can result in dimensional errors and poor surface finish.
- Tool Selection and Management: The increased complexity and extended reach of 5-axis machining can lead to higher rates of tool wear and breakage, requiring frequent monitoring and replacement of tools.
Operational Challenges
- Material Considerations: Different materials have varying properties such as hardness, brittleness, and thermal expansion, which affect the cutting parameters and tool selection. Machining hard or abrasive materials can lead to rapid tool wear and increased machine stress, which may cause warping or dimensional changes after machining.
- Thermal Management: High-speed machining generates significant heat, which can affect tool life and material properties. Moreover, both the workpiece and the machine components can expand with heat, potentially affecting dimensional accuracy. Continuous monitoring and compensation for thermal expansion are necessary.
Economic Considerations
- High Initial Investment: 5-axis CNC routers are more expensive than their 3-axis CNC router counterparts due to their advanced capabilities and complex design. Investing in advanced CAM software and training operators to use 5-axis machines effectively adds to the initial costs.
- Operational Costs: Regular maintenance is helpful to keep the machine in optimal condition, which incurs additional costs. Downtime for maintenance or calibration can impact production schedules. 5-axis CNC routers require high-quality, specialized cutting tools and frequent replacement, which results in higher operating costs.
Skill and Training
- Operator Skill Level: Operating a 5-axis CNC router requires advanced training and experience. Operators must understand the intricacies of multi-axis machining, toolpath generation, and machine calibration.
- Safety Considerations: The additional axes of movement introduce more potential points of failure or collision, making safety protocols even more critical. Operators must be trained to handle emergencies, such as tool breakage or machine malfunction, to minimize risks and ensure a safe working environment.
5-axis CNC routing offers unparalleled capabilities in terms of precision, complexity, and efficiency. However, these benefits come with a set of challenges that require careful consideration and management. By addressing the technical, operational, economic, and skill-related challenges, manufacturers can fully leverage the advantages of 5-axis CNC routers to achieve high-quality results and remain competitive in the market.
Operating and setting up a 5-Axis CNC Router
Setting up and operating a 5-axis CNC router requires a meticulous approach to ensure safety, precision, and efficiency. Below are some critical areas to follow during the setup and operation phases:
Tool Path Strategy for 5-Axis Operation
- Tool Path Optimization: Advanced software algorithms are used to calculate tool paths that avoid collisions between the tool, workpiece, and machine components.
- Simulation: Before actual machining, simulations are run to detect potential collisions and adjust tool paths accordingly.
- Tool Orientation Control: Adjusts the tool angle dynamically to maintain optimal cutting conditions and improve surface finish. Setting appropriate lead and lag angles can enhance cutting efficiency and prolong tool life.
Workpiece Fixture Solution for 5-Axis Machining
- Fixture Design: Fixtures must allow access to multiple sides of the workpiece without the need for repositioning. The fixture must ensure that the workpiece is held rigidly to minimize vibrations and ensure accuracy during machining. Custom fixtures are often designed to securely hold the workpiece while providing the necessary clearance for the tool.
- Modular Fixtures: Modular fixtures can be adjusted and reconfigured to accommodate different shapes and sizes of workpieces, providing flexibility for various projects. These systems allow for rapid switching of fixtures, reducing downtime and improving productivity.
- Vacuum Fixtures: Vacuum fixtures use suction to hold the workpiece in place, which is particularly useful for delicate or thin materials where traditional clamping might cause damage. Moreover, vacuum fixtures provide uniform holding force, reducing the risk of deformation.
Programming and G-Code for 5-Axis Machining
- Advanced CAM Software: CAM software is used to generate complex tool paths required for 5-axis machining. The software must support 5-axis operations and provide features for collision detection, tool orientation control, and path optimization. The generated tool paths must be post-processed to produce G-code compatible with the specific 5-axis CNC router being used.
- G-Code Specifics: G-code must include commands for controlling the rotary axes (A and B axes). These commands ensure the tool is correctly oriented relative to the workpiece. G-code must synchronize the movement of all five axes to achieve the desired tool path and avoid collisions.
- Programming Techniques: The use of subprograms and macros can simplify programming and reduce code redundancy. These are particularly useful for repeating complex sequences. Parametric programming allows for more flexible and adaptive programming, enabling the adjustment of tool paths based on varying parameters such as tool length or workpiece dimensions.
By carefully planning tool paths, designing effective fixture solutions, and ensuring precise programming and G-code generation, operators can maximize the capabilities of a 5-axis CNC router. This leads to higher efficiency, improved accuracy, and the ability to produce complex parts with exceptional quality.
Future Trends in Multi-Axis CNC Routing
The field of multi-axis CNC routing is constantly evolving, driven by advancements in technology and increasing demands for precision, efficiency, and versatility. Here are some of the key future trends in multi-axis CNC routing:
Integration of Artificial Intelligence and Machine Learning
- Predictive Maintenance: The use of AI algorithms to predict machine maintenance needs before failures occur can reduce downtime and extend the life of CNC router Predictive maintenance uses data from sensors to analyze machine performance and predict when maintenance is required.
- Process Optimization: AI and machine learning can optimize machining processes by adjusting parameters in real-time based on tool wear, material properties, and other variables. This adaptive approach can improve efficiency and product quality.
Enhanced Software Capabilities
- Advanced CAD/CAM Software: Improvements in CAD/CAM software will enhance the accuracy and speed of toolpath simulation and verification, reducing the risk of errors and collisions.
- Automated Toolpath Generation: More sophisticated algorithms will automate the generation of complex toolpaths, making it easier to design and manufacture intricate parts.
- Cloud-Based Solutions: Cloud-based CAD/CAM solutions will facilitate collaboration among design and manufacturing teams, allowing for real-time sharing and updating of designs and machining parameters.
Improved Machine Design and Capabilities
- Advanced Control Systems: Next-generation control systems will offer higher precision and faster response times, enabling more accurate and efficient machining operations.
- Reduced Vibration and Deflection: Innovations in machine design, such as improved damping systems and more rigid structures, will minimize vibration and tool deflection, enhancing surface finish and dimensional accuracy.
- Multi-Material Machining: Advances in machine design will enable the machining of multiple materials within a single setup, expanding the range of applications and improving process efficiency.
Advanced Materials and Techniques
- Cryogenic Machining: Cryogenic machining, which uses liquid nitrogen to cool the cutting area, will become more prevalent. This technique improves tool life, reduces thermal deformation, and enhances surface finish.
- Eco-Friendly Coolants: The use of biodegradable and eco-friendly coolants and lubricants will reduce the environmental impact of CNC machining.
- Energy Efficiency: Advances in machine design and operation will focus on reducing energy consumption and improving overall efficiency, contributing to more sustainable manufacturing practices.
Customization and Flexibility
- Personalized Products: The flexibility of multi-axis CNC routers will enable the production of highly customized products on a mass scale, catering to individual customer preferences.
- Rapid Prototyping: CNC routers will continue to play a crucial role in rapid prototyping, allowing for the quick iteration and development of new products.
- Reconfigurable Machines: Modular machine designs will allow manufacturers to reconfigure their CNC routers for different applications easily. This flexibility will enable more efficient use of equipment and faster adaptation to changing production needs.
The future of multi-axis CNC routing is set to be transformative, driven by advancements in artificial intelligence, software capabilities, materials science, automation, sustainability, and customization. By staying ahead of these trends, manufacturers can leverage the full potential of multi-axis CNC routers to enhance productivity, efficiency, and innovation in the manufacturing process. As technology continues to evolve, it will open up new possibilities and applications, further revolutionizing the world of manufacturing.
Summarize
A 5-axis CNC router represents a significant advancement in machining technology, offering unparalleled precision, efficiency, and versatility. As technology continues to evolve, the applications and efficiency of 5-axis CNC routers are likely to expand even further, driving innovation and excellence in production processes. For manufacturers seeking to stay at the forefront of their industries, investing in 5-axis CNC machining is a strategic move that promises to deliver significant competitive advantages.
If you are in the market for high-quality CNC routers, look no further than AccTek CNC. As a professional CNC router manufacturer, AccTek CNC offers a comprehensive range of solutions to meet your machining needs. Whether you require the versatility of a 3-axis CNC router, the enhanced capabilities of a 4-axis CNC router, or the advanced precision of a 5-axis CNC router, AccTek CNC has you covered. Our commitment to excellence and innovation ensures that you receive reliable, efficient, and precise machines tailored to your specific requirements. Trust AccTek CNC to provide the technology and support you need to elevate your manufacturing processes.