- 8-12 Min Read
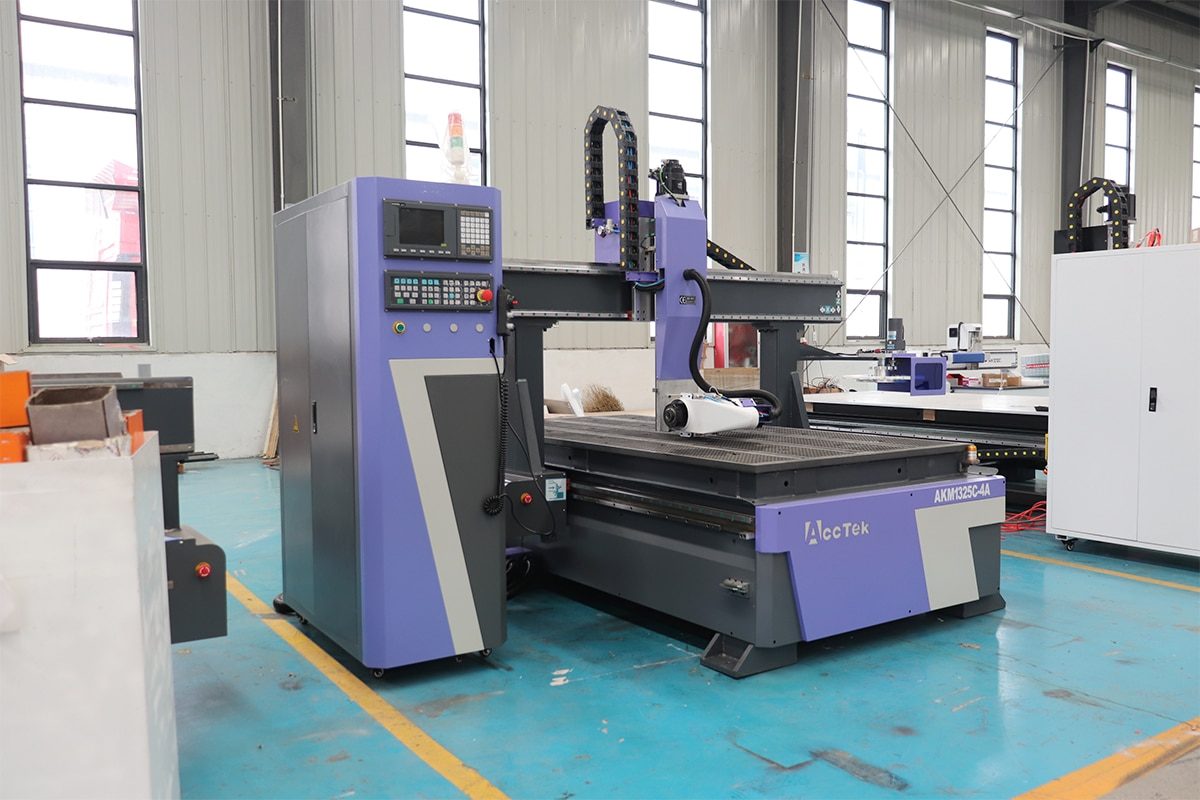
Application and Function of CNC Router
Woodworking
In the woodworking field, CNC routers usher in a new era of precision, efficiency, and boundless creative possibilities. As woodworkers continue to embrace and innovate with CNC technology, the boundaries of what can be achieved in woodworking are continually pushed, shaping a future where craftsmanship and technology converge to redefine the artistry of wood. Here are some key applications of CNC routers in woodworking:
- Precision Cutting: CNC routers excel at accurately cutting wood pieces into intricate shapes, curves, and designs. Whether it’s crafting furniture components, cabinetry parts, or decorative elements, CNC routers ensure precise cuts with consistent quality, reducing material waste and enhancing productivity.
- Carving and Engraving: CNC routers are used for carving intricate patterns, reliefs, and decorative motifs onto wood surfaces. This includes ornate details on furniture, personalized signage, artistic sculptures, and architectural elements.
- Panel Processing: CNC routers are widely used for processing large wood panels with speed and accuracy, facilitating tasks such as cutting panels to size, drilling holes for assembly, and adding edge profiles. This capability is especially beneficial in furniture manufacturing, cabinetry, and architectural woodworking.
- Inlay and Marquetry: CNC routers enable intricate inlay and marquetry work by precisely cutting and fitting pieces of contrasting wood or other materials into a wooden surface, creating stunning visual effects and patterns. This technique is employed in high-end furniture making, musical instrument construction, and decorative woodworking to add depth and richness to the finished pieces.
- Complex Joinery: CNC routers are capable of creating various types of joinery, such as dovetails, mortise and tenon joints, and finger joints, with precision and accuracy. This capability enhances the structural integrity and aesthetics of woodworking projects, ensuring durable and visually appealing assemblies.
Plastic Processing
CNC routers are indispensable tools in the plastic processing industry, offering precision, versatility, and efficiency for a wide range of applications, from prototyping and product development to custom fabrication and mold making. Their ability to handle various plastic materials with precision makes them essential equipment for manufacturers seeking to optimize their production processes and deliver high-quality plastic products. Here are some key applications of CNC routers in plastic processing:
- Cutting and Shaping: CNC routers excel in accurately cutting plastic sheets, panels, and blocks into precise shapes and dimensions. Whether it’s cutting out parts for prototypes, signage, or custom products, CNC routers ensure clean edges and consistent results, minimizing material waste and enhancing productivity.
- Routing and Engraving: Plastic CNC routers are used to route grooves, channels, and intricate designs onto plastic surfaces. This includes engraving logos, text, and decorative patterns on items such as nameplates, displays, and signage. CNC routers offer precise control over cutting depths and speeds, allowing for detailed engraving with sharp, clean lines.
- Prototyping and Product Development: CNC routers are indispensable tools for prototyping plastic parts and products. Whether it’s creating prototypes for consumer goods, electronic enclosures, or kid’s toys, CNC routers enable designers and engineers to quickly iterate designs, test functionality, and validate concepts before full-scale production.
- Plastic Signage and Displays: CNC routers are widely used in the signage and display industry for cutting and engraving plastic materials like acrylic, PVC, and polycarbonate. Whether it’s crafting dimensional letters, illuminated signs, or point-of-sale displays, CNC routers offer precision and versatility for creating eye-catching signage and promotional materials.
Composite Materials Processing
CNC routers play a key role in composite processing by offering versatile machining capabilities that are beneficial for manufacturing high-performance composite structures across a wide range of industries. Here are some key applications of CNC routers in composite processing:
- Trimming and Cutting: CNC routers are used to accurately trim composite materials, such as carbon fiber, fiberglass, and Kevlar, to precise dimensions and shapes. This includes cutting composite panels, sheets, and laminates.
- Surface Profiling and Contouring: CNC routers excel at profiling and contouring composite surfaces, allowing for the creation of complex shapes and geometries with smooth finishes. This is particularly valuable in industries like marine manufacturing, where hulls and other composite components require precise shaping for hydrodynamic performance.
Art and Design
Overall, CNC routers offer artists and designers a powerful tool for realizing their creative visions with precision, efficiency, and versatility across various materials and applications in art and design. Some of the key applications include:
- Artistic Millwork: CNC routers are used in architectural and interior design for creating custom millwork elements such as moldings, trim, panels, and decorative motifs. They can produce intricate patterns and details with high accuracy, enhancing the aesthetic appeal of architectural spaces.
- Mixed Media Art: Artists often combine traditional art techniques with CNC machining to create mixed media artworks. CNC routers can cut out shapes, patterns, and stencils that artists can incorporate into paintings, collages, and other multimedia pieces.
- Jewelry Making: CNC routers equipped with fine cutting tools are employed in jewelry making to precisely carve intricate designs into metals, gemstones, and other materials. This allows jewelry designers to create detailed and customized pieces with intricate patterns and textures.
- Customized Decor and Accessories: From personalized home decor items like clocks and picture frames to custom accessories such as phone cases and laptop stands, CNC routers enable the production of unique and customized items with intricate detailing.
Education and Research
CNC routers play a key role in education and research by providing hands-on experience, fostering creativity and innovation, and preparing students and researchers for careers in technology and manufacturing. Here are some of the key applications:
- Teaching needs: Use CNC routers for practical operations, and teach CNC machining principles and techniques in vocational schools and colleges and universities. They provide hands-on experience in programming, design, and manufacturing processes, which are valuable in both academic and professional settings.
- Scientific Research: Conducting research in manufacturing processes, automation, and materials science. Studying CNC routers exposes students and researchers to automated manufacturing processes, including CAD/CAM (Computer-Aided Design/Computer-Aided Manufacturing) integration, toolpath generation, and machining optimization.
- Stimulate Creativity: In educational settings, CNC routers allow students to bring their ideas to life and iterate upon them. Inspire students to explore creativity in art and design projects.
What are the advancements in CNC routing technology?
Advances in CNC routing technology have been pivotal in revolutionizing industrial applications across a multitude of sectors. These advancements have not only enhanced the precision and efficiency of manufacturing processes but have also expanded the scope of what can be achieved with CNC routers. Here are some key advances:
- Advancements in Precision and Speed: One of the most notable advancements in CNC routing technology is the enhancement of precision and speed. High-speed spindles, improved servo motors, and advanced control systems enable CNC routers to achieve unparalleled accuracy and faster production rates. This allows manufacturers to meet tighter tolerances and deliver products more efficiently, thus enhancing overall productivity.
- Multi-Axis Machining: Traditional CNC routers were limited to three-axis movement, restricting the complexity of shapes that could be machined. However, advances in CNC technology have led to the development of multi-axis machining capabilities, including 4-axis and 5-axis configurations. These additional axes enable CNC routers to approach workpieces from multiple angles, allowing for the fabrication of intricate geometries and complex contours with greater ease and accuracy.
- Automation Capabilities: Automation has become increasingly prevalent in industrial manufacturing, and CNC routing technology is no exception. Integrating CNC routers with automated tool changers, and material handling systems has led to significant improvements in productivity, efficiency, and flexibility. Automated processes minimize manual intervention and reduce cycle times, allowing manufacturers to handle complex tasks more easily.
- Enhanced Software Capabilities: The evolution of CAD/CAM software has played a key role in advancing CNC routing technology. Modern software packages offer sophisticated modeling, simulation, and optimization tools that streamline the design-to-production workflow. Features such as toolpath optimization, collision detection, and adaptive machining algorithms help maximize efficiency and minimize material waste. Furthermore, cloud-based software solutions facilitate collaboration, version control, and remote monitoring of CNC routing operations.
- Material Versatility: CNC routers are now capable of machining a wide range of materials beyond traditional substrates like wood, plastic, and aluminum. Advances in cutting tool technology, spindle designs, and machining strategies have expanded the scope to include composites, ceramics, and even certain types of metals. This versatility enables manufacturers to explore new applications.
What challenges does CNC routing technology face?
CNC routing technology offers numerous advantages, but it also presents its own set of challenges and considerations. Addressing these challenges requires careful planning, training, and investment to ensure that CNC routing technology is effectively utilized and delivers the desired benefits.
- Cost-Benefit Analysis: When implementing CNC routing technology in industrial applications, a thorough cost-benefit analysis is required. Factors such as initial investment costs, operational expenses, productivity gains, and return on investment (ROI) must be carefully evaluated to determine the viability and profitability of adopting CNC routing solutions.
- Complexity of Programming and Setup: Despite advancements in software usability, programming and setting up CNC routing systems for specific tasks can still be complex and time-consuming. Manufacturers often face challenges in optimizing tool paths, selecting cutting parameters, and calibrating machine settings to achieve desired outcomes. Addressing these challenges requires skilled personnel with expertise in CNC programming and machining operations.
- Safety and Compliance: Industrial CNC routing environments pose inherent safety risks, including hazards associated with high-speed rotating machinery, sharp cutting tools, and airborne particles. Ensuring compliance with safety regulations, implementing proper safety protocols, and providing personal protective equipment (PPE) are critical considerations to safeguard worker health and mitigate workplace accidents.
- Material Selection: Not all materials are suitable for CNC routing. Some materials, such as metals or very hard woods, may require specialized equipment or tooling, which can increase costs and complexity.
- Maintenance: Like any mechanical equipment, CNC routers require regular maintenance to ensure optimal performance and longevity. This includes tasks such as cleaning, lubrication, calibration, and replacing worn or damaged parts.
- Software Compatibility: Compatibility issues between different software packages (CAD, CAM, machine control software) can sometimes arise, leading to errors or inefficiencies in the machining process.
- Scalability: As production volumes increase, the capacity of the CNC router may become a limiting factor. Businesses need to consider scalability when investing in CNC technology and plan for potential future growth.
What is the future trend of CNC routing?
The future of CNC routing will be characterized by increased automation, precision, flexibility, and sustainability, driven by advancements in technology and evolving industry demands. These trends will continue to reshape manufacturing processes and enable new possibilities in product design and production.
- Automation: There will be a continued push towards automation in CNC routing, with advancements in robotics, machine learning, and artificial intelligence enabling greater levels of autonomy in machine operation, setup, and toolpath optimization. This automation will help reduce manual intervention, increase productivity, and improve efficiency.
- Integration with Industry 4.0: CNC routers will increasingly be integrated into the broader framework of Industry 4.0, with connectivity and data exchange capabilities allowing for real-time monitoring, predictive maintenance, and remote operation. This integration will enable manufacturers to optimize production processes, reduce downtime, and improve overall equipment effectiveness.
- Enhanced Precision and Accuracy: Future CNC routing machines will likely feature advancements in motion control systems, feedback mechanisms, and sensor technology to achieve higher levels of precision and accuracy. This will enable the machining of more complex geometries and tighter tolerances.
- Multi-axis Machining: There will be a growing demand for CNC routers capable of multi-axis machining, allowing for the production of more intricate and three-dimensional workpieces. Advancements in machine design, control algorithms, and tooling technology will enable greater flexibility and capability in multi-axis machining applications.
- Materials Innovation: Future CNC routing machines will be capable of machining a wider range of materials, including advanced composites, ceramics, and high-performance alloys. This will be facilitated by advancements in cutting tool technology, coolant systems, and machining strategies tailored to specific material properties.
- Sustainability: There will be a greater emphasis on sustainability in CNC routing, with a focus on reducing waste, energy consumption, and environmental impact. This may involve the development of eco-friendly machining processes, recycling of machining waste, and the use of renewable materials.