- 8-12 Min Read
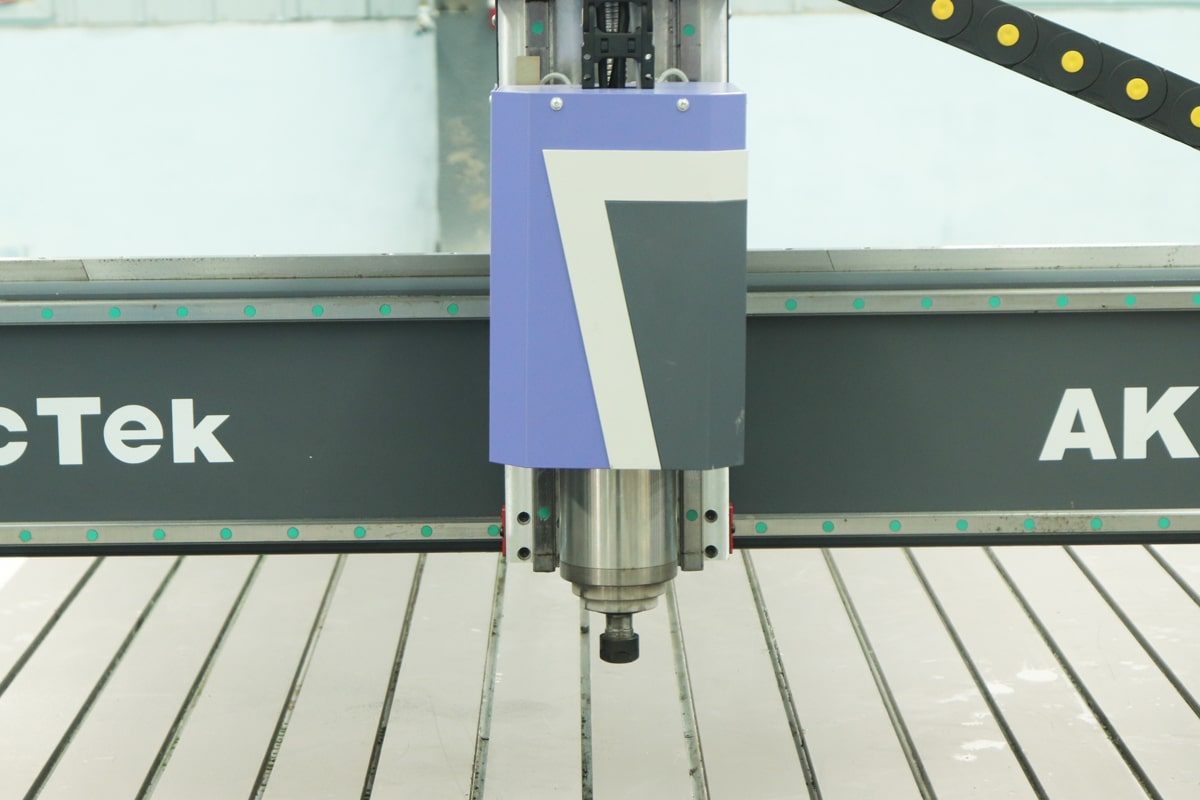
The spindle is the heart of a CNC router, responsible for driving the cutting tool with precision and power. However, like any high-performance component, it can be vulnerable to wear and overheating, especially under continuous or demanding workloads. Spindle overheating not only affects cutting accuracy and machine efficiency but can also lead to costly downtime and even permanent damage if left unresolved.
In this article, we’ll explore the most common reasons why CNC router spindle temperatures rise beyond safe limits and provide practical solutions to help you prevent or fix the issue before it escalates. Whether you’re using an air-cooled or water-cooled spindle, proper maintenance and early intervention are key to ensuring long-term machine performance and reliability.
Understanding CNC Router Spindles
The spindle is one of the most critical components of a CNC router. It acts as the main motor responsible for rotating the cutting tool at high speeds, enabling precise cutting, carving, drilling, engraving, and milling of a wide range of materials, such as wood, plastics, aluminum, and other metals.
Function of the CNC Spindle
At its core, the spindle holds and spins the cutting bit or tool. It receives commands from the CNC controller to operate at specific speeds and feeds, and transmits torque to the tool to cut through the workpiece. A high-quality spindle ensures smooth, accurate, and consistent machining results.
Types of CNC Router Spindles
There are two main types of CNC router spindles:
- Air-Cooled Spindle: It relies on built-in fans to dissipate heat generated during operation. As the spindle runs, the fan forces air over the spindle body to cool it down. These spindles are generally easier to install and maintain as they don’t require external cooling equipment like pumps or chillers. They are typically louder and may struggle with heat management during extended use, making them more suitable for light to medium-duty tasks, such as woodworking or plastics machining.
- Water-Cooled Spindle: It uses circulating water, usually pumped through a chiller or cooling tank, to absorb and carry away heat from the spindle body. This method provides more efficient and consistent cooling, resulting in quieter operation and reduced thermal expansion during long machining sessions. While they offer superior performance for heavy-duty and high-speed applications, water-cooled spindles require more complex setup and regular maintenance of the water-cooling system.
Why the Spindle Matters
The spindle directly impacts:
- Cutting Quality: Higher speed and torque provide smoother cuts
- Material Versatility: More powerful spindles handle harder materials
- Production Efficiency: Faster RPMs and better cooling enable longer operation
- Tool Life: Stable operation reduces tool wear and breakage
A poorly performing spindle can lead to burn marks, uneven cuts, tool breakage, and even machine damage.
The CNC router spindle is the core of the machine’s cutting capability. Whether you’re a hobbyist or running a commercial operation, understanding how your spindle works and how to care for it can make a big difference in both the quality of your work and the longevity of your equipment.
Common Causes of CNC Router Spindle Overheating
CNC router spindle overheating is a common but serious issue that can significantly reduce machine performance, damage internal components, and interrupt production. Whether you’re using an air-cooled or water-cooled spindle, multiple factors can contribute to excessive heat buildup. This section explores the most frequent causes of spindle overheating, helping you identify potential problems before they escalate.
Inadequate Cooling System
The cooling system is responsible for regulating the spindle temperature. If the spindle’s cooling system is not functioning properly, heat builds up quickly during operation.
- Air-Cooled Spindle Issues: Clogged or weak fans can reduce airflow, causing heat to accumulate. Operating the spindle in a poorly ventilated or dusty environment can further hinder cooling efficiency.
- Water-Cooled Spindle Issues: Common problems include low water levels, pump failure, blocked coolant pipes, or an ineffective chiller. Any of these can lead to poor heat dissipation and rapid overheating.
Improper Lubrication
Spindles have internal bearings that rely on proper lubrication to minimize friction and heat.
- Dry Bearings: If the grease dries out or is insufficient, the metal-to-metal contact creates excessive heat.
- Contaminated Lubricant: Dirt, dust, or degraded grease can reduce lubrication effectiveness and accelerate wear, further contributing to overheating.
Overloading the Spindle
Running the spindle beyond its rated capacity or under incorrect cutting parameters can lead to excess heat generation.
- Too Much Load: Cutting too deep or too fast causes the spindle to work harder than intended.
- Incorrect Tooling: Using dull tools, oversized bits, or improper feed rates increases resistance during cutting, making the spindle motor strain and heat up.
- Continuous Operation: Long operating hours without pauses for cooling can result in cumulative heat buildup.
Electrical Issues
Electrical instability can cause the spindle motor and drive components to operate inefficiently or unsafely.
- Voltage Fluctuations: Inconsistent or insufficient voltage affects motor performance, leading to higher heat output.
- Faulty Inverter (VFD): A malfunctioning VFD may fail to deliver the correct frequency and voltage to the spindle, causing inefficient power conversion and excessive heat.
Dust and Debris Accumulation
Dust buildup can clog ventilation paths or coolant channels, especially in wood or composite cutting environments.
- Ventilation Blockage: Dust-covered fans and vents in air-cooled spindles reduce airflow.
- Clogged Coolant Channels: In water-cooled systems, debris in the water or pipe blockages disrupt flow, causing heat retention.
- Heat Transfer Obstruction: A dirty spindle body can also hinder proper heat dissipation into the surrounding air or water.
Bearing Wear or Failure
Bearings naturally wear over time, and as they degrade, they generate more friction and heat.
- Worn Bearings: Loose or damaged bearings increase internal resistance and cause vibration, heat, and eventual spindle failure.
- Poor Installation or Misalignment: Improper bearing alignment increases pressure and results in localized overheating.
Inadequate Machine Maintenance
Neglecting regular maintenance increases the likelihood of all the above problems occurring.
- Skipped Inspections: Missed warning signs such as abnormal spindle temperature, noise, or vibration often lead to unnoticed overheating.
- Failure to Replace Parts: Components like filters, fans, pumps, and bearings have a limited service life and should be replaced periodically.
From cooling system failures to overloading and electrical issues, each factor plays a role in spindle health. Understanding the root causes of spindle overheating is the first step toward preventing costly repairs and downtime. By recognizing these common causes of spindle overheating, CNC operators can take proactive steps to protect their equipment and ensure stable, efficient performance.
Solutions and Preventive Measures
Spindle overheating can severely affect the performance and lifespan of a CNC router. Fortunately, with proper preventive measures and timely interventions, this issue can be effectively controlled. Below are practical solutions and preventive measures to keep your CNC router spindle running at optimal temperature.
Improving Cooling Efficiency
Cooling is fundamental to maintaining the spindle temperature during operation. Whether the spindle is air-cooled or water-cooled, ensuring effective heat dissipation is the first line of defense against overheating.
- For Air-Cooled Spindles: Regularly inspect the cooling fan for dust buildup or obstruction. Clean the fan blades and ventilation paths to ensure smooth airflow. Position the CNC router in a well-ventilated space to prevent hot air from accumulating around the machine.
- For Water-Cooled Spindles: Check the coolant level and top it off with clean, filtered water when necessary. Inspect hoses and the circulation pump for clogs, leaks, or damage. Ensure the chiller or cooling tank is functioning properly and flush the system periodically to remove any accumulated debris or algae.
Regular Lubrication and Maintenance
Bearings inside the spindle generate friction, and without proper lubrication, they can quickly overheat and wear out.
- Use only high-quality lubricants compatible with high-speed spindle bearings. Over-lubrication can be as harmful as under-lubrication, so the manufacturer’s lubrication schedule should be followed closely.
- Check for signs of lubricant degradation, such as discoloration, thickening, or foul odor. Clean and re-grease or replace bearings as needed.
- Schedule regular maintenance checks to examine spindle integrity, alignment, and overall performance.
Optimizing Cutting Parameters
Running the spindle with improper parameters can lead to overloading, which directly contributes to excessive heat.
- Always match the cutting speed, feed rate, and tool size with the material type and spindle capacity.
- Avoid aggressive cuts or excessive depths, especially on hard materials. If necessary, make multiple shallow passes instead of one deep cut.
- Monitor spindle load indicators (if available) on the control system to prevent overworking the spindle during prolonged operations.
Checking Electrical Components
Electrical irregularities can cause inefficient motor operation, leading to excessive heat buildup in the spindle.
- Ensure the spindle receives stable voltage as specified by the manufacturer. Use voltage regulators or surge protectors if your facility has unstable power.
- Inspect the Variable Frequency Drive (VFD) for signs of wear, incorrect settings, or overheating. Faulty VFDs can send improper signals to the spindle and overheat it.
- Examine electrical cables and connectors for signs of fraying, corrosion, or loose connections, which can contribute to power loss and overheating.
Cleaning the Spindle and Surrounding Areas
Dust and debris can obstruct cooling paths, accumulate around bearings, or even enter the spindle casing, all of which impair cooling efficiency.
- Clean the spindle body, fans, and nearby surfaces regularly with compressed air or a vacuum to prevent dust accumulation.
- Install and maintain a reliable dust extraction system, especially when working with wood or other particulate-generating materials.
- In water-cooled systems, use a filter to keep debris out of the water loop and clean the reservoir to prevent biological growth.
Replacing Worn Bearings in Time
Bearings naturally wear over time and can become a significant heat source if not replaced promptly.
- Signs of bearing wear include unusual noise, increased vibration, reduced cutting precision, and rising spindle temperature.
- Do not delay bearing replacement once wear is detected. Continued use of damaged bearings can lead to catastrophic spindle failure.
- Use OEM-recommended bearings and tools for replacement, and ensure proper installation to avoid misalignment or over-tightening.
CNC router spindle overheating is a manageable issue when addressed with a proactive maintenance routine and mindful operation. By implementing these solutions and preventive strategies, operators can significantly reduce the risk of spindle failure. These best practices not only improve productivity but also extend the service life of your CNC equipment.
When to Seek Professional Help
While many spindle overheating issues can be resolved through routine maintenance and careful operation, there are situations where professional intervention is necessary. Ignoring persistent or severe problems may lead to irreversible damage and costly downtime. Knowing when to call in a technician can save both time and money.
Persistent Overheating Despite Maintenance
If your spindle continues to overheat even after you’ve cleaned the cooling system, lubricated the bearings, and adjusted your cutting parameters, it could indicate a deeper issue, such as internal motor failure, advanced bearing wear, or a malfunctioning inverter. At this point, it’s best to stop using the machine and have it inspected by a qualified technician.
Unusual Noises or Vibrations
Grinding, rattling, or whining sounds coming from the spindle during operation are clear signs of mechanical problems, most likely related to the bearings or internal components. Excessive vibration can also signal misalignment or structural damage. These symptoms should be investigated immediately by a professional to avoid catastrophic spindle failure.
Sudden Performance Drops
If you notice reduced cutting precision, increased resistance, or sluggish spindle speed, it may be due to internal wear or electrical faults. These performance drops are often early indicators of a more serious issue that requires diagnostic tools and expertise beyond basic troubleshooting.
Electrical or VFD Malfunctions
Electrical issues like tripped breakers, fluctuating spindle speed, or error codes from the Variable Frequency Drive (VFD) may point to power supply problems, damaged drive components, or software errors. These issues should only be handled by qualified personnel to avoid risk of electrical shock or further damage.
Overheating After Bearing Replacement or Maintenance
If your spindle starts overheating after a recent repair or bearing replacement, it may have been improperly reassembled or misaligned. In such cases, continued operation can cause even more damage. Contacting a service professional ensures that the spindle is calibrated and reinstalled correctly.
You Lack the Tools or Experience
Some repairs require precision tools, technical knowledge, or access to replacement parts that may not be readily available to the average user. Rather than risking further damage through trial and error, it’s safer and more efficient to consult a professional service provider.
Spindle overheating should never be ignored, especially when basic troubleshooting doesn’t resolve the issue. If you observe persistent problems, strange sounds, or electrical anomalies, it’s time to bring in professional help. A certified technician can perform in-depth diagnostics, make accurate repairs, and restore your CNC router to full working condition.
Summarize
Spindle overheating is a common yet preventable issue in CNC router operations. By understanding the root causes and implementing targeted solutions, you can significantly extend the life of your spindle and ensure stable machine performance. And when problems persist beyond basic troubleshooting, seeking professional help is the smartest way to protect your investment. With a proactive approach to spindle care, you’ll not only prevent overheating but also keep your CNC router running efficiently for the long haul. To learn more about spindles, you can continue reading “How to correctly choose the CNC router spindle?“.
If you’re looking for a reliable and high-performance CNC router, AccTek CNC is a professional manufacturer in China that stands out for its quality engineering and customer-focused solutions. Whether you’re a small workshop or an industrial user, AccTek offers a range of CNC routers tailored to your needs, along with strong after-sales support and expert guidance. Choosing AccTek means investing in machines built to last and perform.