- 12-16 Min Read
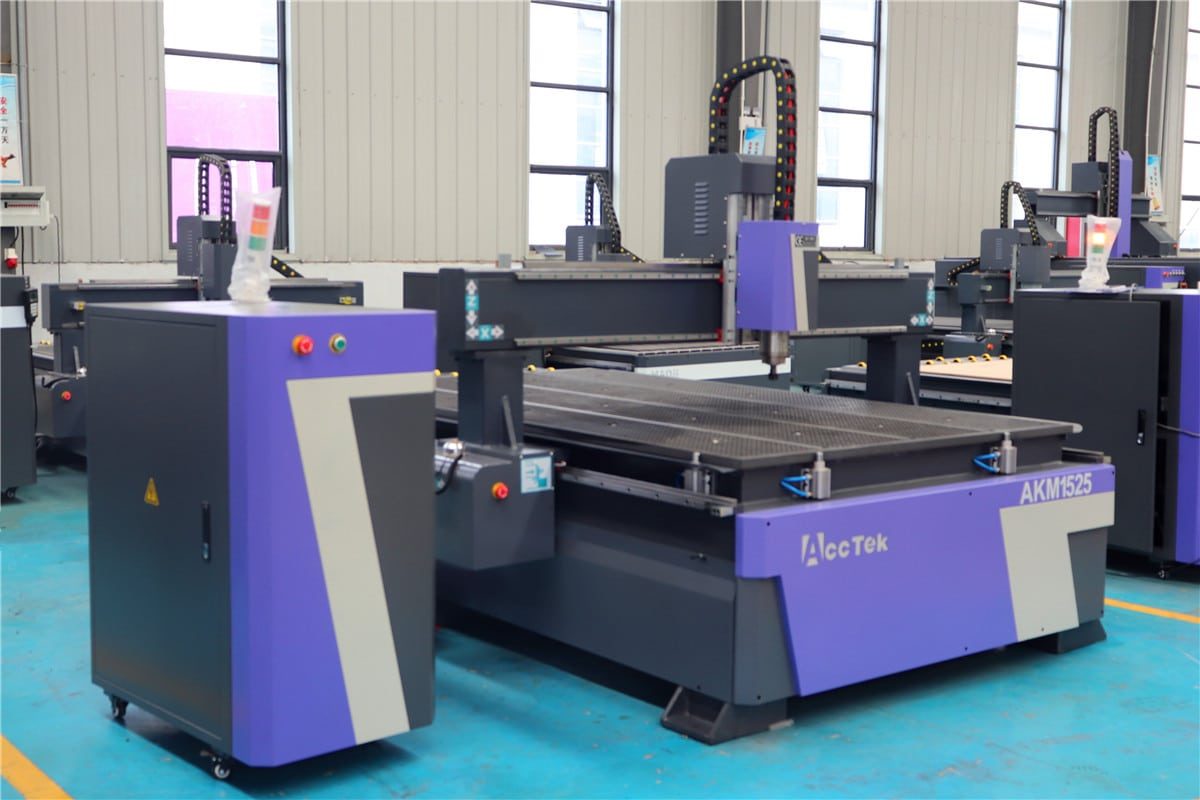
CNC routers have become an essential tool in modern manufacturing, known for their ability to execute precise cuts and intricate designs across a wide range of materials. From woodworking to metal fabrication, these machines have opened up new possibilities for efficiency and creativity in production processes. However, like any technology, CNC routers have inherent limitations that can impact their effectiveness in certain applications. Understanding these challenges is necessary for businesses aiming to maximize efficiency and avoid potential setbacks.
This article delves into the key limitations of CNC routers, exploring how factors such as precision and accuracy challenges, speed and efficiency constraints, and design and material limitations can impact their performance. Additionally, we will examine the intricacies of software and programming, and the ongoing maintenance and cost considerations that can affect long-term usability. By addressing these aspects, you can weigh CNC router capabilities against your production needs, enabling more informed decisions in your manufacturing processes.
Precision and Accuracy Challenges in CNC Routers
While CNC routers are designed to deliver high levels of precision and accuracy, several factors can compromise their performance. Here are the challenges that CNC routers face in terms of precision and accuracy:
Tool Deflection and Runout
Tool deflection and runout are common mechanical challenges that directly affect the precision of CNC routers.
- Tool Deflection: Tool deflection occurs when the cutting tool bends slightly under the force of the cutting process. This is especially prevalent in operations involving hard materials or long, thin tools. The bending of the tool causes deviations from the programmed cutting path, leading to dimensional inaccuracies and poor surface finishes. Factors contributing to tool deflection include excessive cutting forces, high feed rates, and inadequate tool stiffness.
- Runout: Runout refers to the misalignment of the cutting tool with the spindle axis, resulting in a wobbling effect during rotation. This misalignment can create uneven cuts, reduce tool life, and compromise the final product’s accuracy. Runout is often caused by poorly manufactured tool holders, improper tool installation, or wear in the spindle bearings.
To minimize tool deflection and runout, operators can use shorter and more rigid tools, optimize cutting parameters, and ensure that the tool and spindle are properly aligned and securely fastened. Regular inspection and replacement of worn components are also essential.
Material Variation
Material inconsistencies pose a significant challenge to CNC router precision, particularly when working with diverse or unpredictable materials.
- Material Hardness and Density: Variations in hardness or density within a material can cause uneven cutting forces. For example, in natural materials like wood, differences in grain density may lead to inconsistent cuts. In metals, impurities or uneven composition can create similar issues.
- Thermal and Mechanical Behavior: Materials respond differently to cutting forces and heat generated during the machining process. Soft materials may deform or melt under excessive pressure or heat, while hard materials can cause excessive wear on tools, leading to inaccuracies.
- Workpiece Stability: Uneven clamping or improper fixturing of the material can result in movement during machining. This instability can cause variations in the final dimensions and lead to surface irregularities.
Selecting materials with consistent properties, optimizing cutting parameters, and using proper fixturing techniques can reduce the impact of material variations. Pre-machining inspections and adjustments for specific material behaviors are also beneficial.
Calibration Issues
Calibration plays a critical role in ensuring that CNC routers operate within their designed tolerances. Inadequate or irregular calibration can lead to systematic errors that compromise accuracy.
- Misaligned Components: Over time, mechanical components such as linear guides, ball screws, and spindles can shift out of alignment due to wear, vibrations, or external impacts. Misalignment results in deviations from the intended cutting path.
- Software and Controller Errors: Calibration issues are not limited to mechanical components, software and control systems also require precise tuning. A mismatch between the machine’s software and its mechanical movements can cause positioning inaccuracies.
- Thermal Drift: Temperature changes during operation can affect machine calibration. Expansion or contraction of machine components can lead to shifts in alignment, particularly during prolonged or heavy-duty use.
Regular maintenance, including thorough cleaning and lubrication, is beneficial to maintain calibration accuracy. Periodic checks and realignment of mechanical components, combined with software updates and recalibrations, help prevent cumulative errors.
Precision and accuracy challenges in CNC routers often arise from mechanical, material, or calibration-related issues. Addressing these challenges requires a combination of proactive maintenance, careful material selection, and process optimization. By understanding and mitigating the factors that contribute to tool deflection and runout, material variation, and calibration issues, operators can significantly enhance the performance and reliability of CNC routers.
Speed and Efficiency Constraints in CNC Routers
CNC routers are celebrated for their ability to automate complex cutting and engraving tasks. However, their speed and efficiency can be limited by several factors, particularly when balancing quality with productivity. Below, we explore key speed and efficiency constraints, highlighting their causes and potential solutions.
Feed Rate and Cutting Speed
The feed rate (linear speed of the tool relative to the material) and cutting speed (rotational speed of the tool) are fundamental to a CNC router’s efficiency. However, these parameters are limited by factors such as material properties, tool capabilities, and machine rigidity:
- Material Properties: Harder materials like metals demand slower feed rates and cutting speeds to prevent overheating, excessive tool wear, and poor cut quality. Softer materials, like wood or plastic, can accommodate faster speeds but are prone to issues like chipping, melting, or tearing.
- Tool Durability: Faster speeds generate more heat and stress, leading to rapid tool wear. The quality of the cutting tool, including its material and coating, determines its tolerance for high-speed operations.
- Machine Rigidity: Lightweight or less robust CNC routers may vibrate at high feed rates or cutting speeds, causing inaccuracies and reduced surface quality.
To address these constraints, it is essential to select cutting tools designed for specific materials, such as carbide or coated tools, which can withstand higher speeds. Optimizing speed and feed settings for each material, following manufacturer recommendations, can help maintain a balance between speed and precision. Additionally, using coolant systems to manage heat buildup and investing in high-rigidity machines can allow faster operation without compromising accuracy or tool life.
Complexity and Programming Time
CNC routers require detailed programming to perform operations, and the complexity of a design significantly impacts the time and effort needed for preparation:
- Intricate Toolpaths: Complex shapes, tight tolerances, and multi-axis machining operations require more intricate programming and toolpath optimization, which increases preparation time.
- Advanced CAM Software: Generating toolpaths for complex designs often require sophisticated CAM (Computer-Aided Manufacturing) software, which may have a steep learning curve. Operators must have advanced skills to make effective use of these tools.
- Simulation and Debugging: To avoid errors during machining, extensive simulation and debugging are necessary, particularly for designs with tight tolerances or intricate details. These steps can be time-consuming.
Leveraging advanced CAD/CAM software with features like automated toolpath generation and built-in simulation can significantly reduce programming time. Operators can reuse templates or pre-programmed libraries for recurring design elements, minimizing the need to start from scratch. Investing in training for operators ensures efficient handling of complex designs, and simulation tools help identify potential issues early, saving time and reducing errors during machining.
Tool Change Time
Many CNC projects require multiple tools for different operations, such as cutting, drilling, and engraving. Each tool change introduces downtime, which can significantly affect overall efficiency:
- Manual Tool Changes: On machines without automatic tool changers (ATCs), operators must manually replace tools, align them, and recalibrate the machine, leading to considerable delays.
- Frequent Changes: Complex designs or multi-step operations often require several tool changes, further increasing production time. Improper planning can exacerbate this issue.
- Tool Alignment: Ensuring the precise alignment of tools during each change is critical for maintaining accuracy, adding to the time required for manual changes.
Implementing CNC routers with automatic tool changer (ATC) can drastically reduce downtime by automating the tool-changing process. For businesses without ATCs, planning toolpaths strategically to group operations by tool type minimizes the number of tool changes required. Using versatile tools that can perform multiple functions effectively also reduces the need for frequent changes, improving overall efficiency.
CNC routers face several speed and efficiency constraints related to feed rates, design complexity, and tool changes. Addressing these challenges requires a strategic approach, including optimizing cutting parameters, using advanced software, and adopting automation features. By mitigating these constraints, manufacturers can enhance the productivity and reliability of CNC routing processes while maintaining high-quality standards.
Design and Material Limitations in CNC Routers
CNC routers are capable of handling a wide range of tasks, but they face constraints when it comes to design intricacy and material compatibility. Below, these limitations are explored in detail, along with mitigation strategies.
Geometric Limitations
- Tool Reach and Accessibility: CNC routers rely on rotating tools to shape materials, and the geometry of the cutting tool imposes limits on the features that can be machined. For example, sharp internal corners, deep cavities, or intricate 3D contours may be inaccessible to standard tools. Even multi-axis CNC routers can struggle with designs requiring extreme detail or those involving undercuts and hidden geometries.
- Layer-by-Layer Approach for 3D Geometry: Unlike additive manufacturing processes, CNC routers carve away material to create designs, which may require a layer-by-layer or stepwise approach for complex 3D geometries. This method can leave visible tool marks or layering effects, requiring additional post-processing to achieve smooth finishes.
- Tolerances and Surface Quality: While CNC routers are precise, achieving ultra-tight tolerances and high-quality surface finishes on complex geometries can be difficult. Limitations in the machine’s resolution, tool sharpness, and feed rates can impact the final output.
To overcome design limitations, operators can use smaller, specialized tools for intricate details while combining them with larger tools for general cuts to optimize efficiency. Multi-axis CNC routers with advanced software can better handle complex geometries, and nesting software can help maximize material usage. Simulating the toolpath before machining ensures that the design can be executed effectively without risking errors.
Material Selection and Compatibility
- Material Rigidity and Hardness: CNC routers excel at machining soft to medium-hard materials like wood, plastics, and composites, but harder materials such as steel and titanium can exceed the machine’s capabilities. Routers with limited spindle power or rigidity may struggle to achieve effective cutting on such materials, leading to increased tool wear, vibrations, and inaccuracies.
- Material Thickness and Durability: Processing very thick materials may require multiple passes, increasing machining time and affecting precision. Brittle materials pose additional challenges due to their tendency to crack or chip under the stress of machining.
- Hazardous and Specialized Materials: Some materials, such as composites with embedded metals, release hazardous dust or fumes when cut. These byproducts can pose health risks to operators and damage machine components if not adequately managed. Furthermore, specialized materials like foams or rubbers may require unique tools and settings to ensure clean cuts.
- Surface Coatings or Treatments: Materials with surface coatings or finishes, such as anodized aluminum or laminated wood, can pose compatibility challenges. The coating may degrade unevenly during machining, affecting the final appearance and functionality of the part.
When machining metal or hard materials, choose a CNC router with spindle power and cutting tools appropriate for the target material. For brittle materials, specialized tools with high cutting speeds and appropriate feeds minimize damage. Use cooling systems or lubricants to reduce heat and wear when machining hard or thick materials. Dust collection systems and proper ventilation mitigate safety risks associated with hazardous materials.
CNC routers are constrained by their geometric limitations and the types of materials they can handle effectively. While they perform well with many common materials and designs, intricate geometries and certain hard or brittle materials may present significant challenges. By leveraging advanced equipment, specialized tooling, and optimized strategies, operators can navigate these limitations to expand the functional range of CNC routers while maintaining quality and efficiency.
Software and Programming Challenges in CNC Routers
CNC routers rely heavily on software and programming to translate designs into precise machine movements. However, several challenges can hinder efficiency and productivity. Below, we explore the key software and programming challenges CNC routers face and how they impact machining processes.
CAD/CAM Limitations
CAD (Computer-Aided Design) and CAM (Computer-Aided Manufacturing) software are essential tools for creating designs and generating toolpaths for CNC routers. Despite their importance, these tools have several limitations:
- Steep Learning Curve: CAD/CAM software often has complex interfaces and features that require extensive training to master. New users may struggle with advanced functionalities, such as multi-axis machining, toolpath optimization, or simulation tools.
- Software Incompatibility: Not all CAD/CAM software is compatible with every CNC router. File format issues, post-processor mismatches, and a lack of standardized tool libraries can lead to errors in translating designs into machine-readable instructions. This incompatibility requires manual adjustments, which are time-consuming and prone to errors.
- Inaccurate Toolpath Generation: Generating accurate toolpaths depends on the software’s ability to handle complex designs and material-specific parameters. Some CAD/CAM software struggles with intricate designs or non-standard materials, leading to inefficient or incorrect toolpaths.
- Updates and Maintenance: Frequent updates in software can cause disruptions, as new features may require retraining and adjustments in workflows. Older software versions may lack support for modern CNC router functionalities, reducing their effectiveness.
To address these challenges, invest in user-friendly CAD/CAM software with intuitive interfaces and automated features like toolpath optimization. Provide comprehensive training for operators to master the software and stay updated on new versions. Using pre-defined templates and libraries for recurring designs can also streamline programming tasks.
Programming Complexity
Programming a CNC router involves converting CAD designs into G-code, a machine-readable language that dictates the router’s movements. The complexity of this process presents several challenges:
- Customization and Optimization: Generating a G-code that is both functional and optimized for efficiency requires a deep understanding of the machine’s capabilities, material properties, and tool behavior. Misconfigured settings, such as feed rates, spindle speeds, or tool offsets, can lead to suboptimal machining, tool damage, or material waste.
- Debugging and Error Correction: Errors in programming can result in tool crashes, incorrect cuts, or poor surface finishes. Debugging these errors is a time-intensive process, particularly for complex designs with intricate toolpaths.
- Post-Processing Challenges: Post-processing is the step where a generic G-code is tailored to the specific CNC router being used. Variations in machine configurations, such as worktable size, tool alignment, or spindle power, require manual adjustments in the G-code. These adjustments demand expertise and introduce additional steps in the programming workflow.
- Lack of Standardization: Different CNC routers and software solutions often use variations of G-code or proprietary commands. This lack of standardization makes it difficult to transfer programs between machines or adapt existing code to new setups.
To address these challenges, use advanced CAM software with automated parameter recommendations and material-specific libraries to simplify programming. Employ simulation tools to debug and refine G-code before execution, reducing errors during machining. Invest in post-processors that are pre-configured for the specific CNC router model, minimizing the need for manual adjustments. Train operators to understand the nuances of G-code programming and machine-specific configurations to ensure more efficient workflows.
Challenges in software and programming, particularly CAD/CAM limitations and programming complexity, can hinder the efficiency and precision of CNC routers. These issues require a combination of the right software tools, operator training, and process optimization to overcome. By addressing these challenges, manufacturers can ensure smoother workflows and maximize the potential of their CNC routing operations.
Maintenance and Cost Considerations for CNC Routers
CNC routers are valuable tools for precision machining, but their operation and upkeep come with challenges related to maintenance and cost. Below, we explore these aspects in detail, outlining their impact and potential mitigation strategies.
Maintenance Challenges
Proper maintenance is beneficial to ensure the longevity and consistent performance of CNC routers, but several factors complicate this process:
- Regular Wear and Tear: CNC routers consist of moving components such as linear guides, ball screws, and spindles, which are subject to wear over time. This natural degradation can lead to reduced accuracy, vibration, and inefficient machining if not addressed.
- Tool and Component Life: Cutting tools, spindles, and other consumables have a limited lifespan. Regular tool changes and component replacements are necessary but can be time-consuming and increase downtime.
- Cleaning and Lubrication: Accumulated dust, chips, and debris from machining operations can obstruct components and reduce machine performance. Additionally, improper lubrication can cause friction, overheating, and mechanical failures.
- Calibration Needs: CNC routers require periodic calibration to maintain accuracy. Neglecting this process can result in alignment errors, compromised precision, and material waste.
Mitigation strategies for these challenges include implementing a rigorous preventive maintenance schedule to inspect, clean, lubricate, and calibrate the machine regularly. Operators should be trained to recognize early signs of wear or misalignment, and using high-quality lubricants and efficient dust collection systems can help reduce component stress and maintain machine performance.
Cost Considerations
CNC routers come with various direct and indirect costs that businesses must account for to ensure cost-effective operations:
- Initial Investment: Purchasing a CNC router involves a significant upfront cost, which varies based on machine specifications, features, and brand. High-performance routers with advanced capabilities, such as multi-axis machining or automated tool changers, are considerably more expensive.
- Operational Costs: Operating a CNC router involves expenses for power consumption, tool replacements, coolant usage, and consumables. For larger or high-power machines, energy costs can be substantial.
- Downtime and Repairs: Unplanned downtime due to machine breakdowns or component failures can disrupt production schedules, leading to financial losses. Additionally, repair costs for major components, such as spindles or control systems, can be high.
- Software and Training Costs: Advanced CAD/CAM software licenses and regular updates represent ongoing costs. Training operators to use the software and machine effectively also requires investment.
To mitigate these costs, businesses can perform a thorough cost-benefit analysis before purchasing to ensure the machine matches production needs. Investing in energy-efficient models reduces operational expenses, while predictive maintenance systems help identify potential issues early, minimizing costly repairs and downtime. Allocating budgets for regular software updates, operator training, and maintaining a stock of essential spare parts ensures smooth and cost-effective operations over the machine’s lifecycle.
Maintenance and cost considerations are significant aspects of owning and operating a CNC router. Proper maintenance ensures machine reliability and longevity, while strategic cost management maximizes the return on investment. By adopting preventive maintenance practices, choosing the right machine for their needs, and planning for operational expenses, businesses can mitigate these challenges and achieve sustainable productivity with their CNC routers.
Summarize
CNC routers are powerful tools that bring precision, efficiency, and versatility to a wide range of applications. However, their performance is not without constraints. By understanding the specific limitations of CNC routers, businesses can implement strategies to mitigate their impact, whether it’s through preventive maintenance, software training, or selecting the right machine for their needs. While no tool is perfect, addressing these challenges allows manufacturers to harness the full potential of CNC routers, ensuring reliable performance, high-quality results, and sustainable operations in today’s competitive landscape.
AccTek CNC is a professional CNC router manufacturer committed to delivering high-performance machines that address the common limitations CNC router users face. With features like automated tool changers and dust collection systems, AccTek CNC routers enhance operational efficiency while reducing downtime and operational costs. Whether you need a CNC router for intricate designs or large-scale production, we deliver tailored solutions that meet your needs. Choose AccTek CNC for a cost-effective CNC routing experience backed.