- 7-11 Min Read
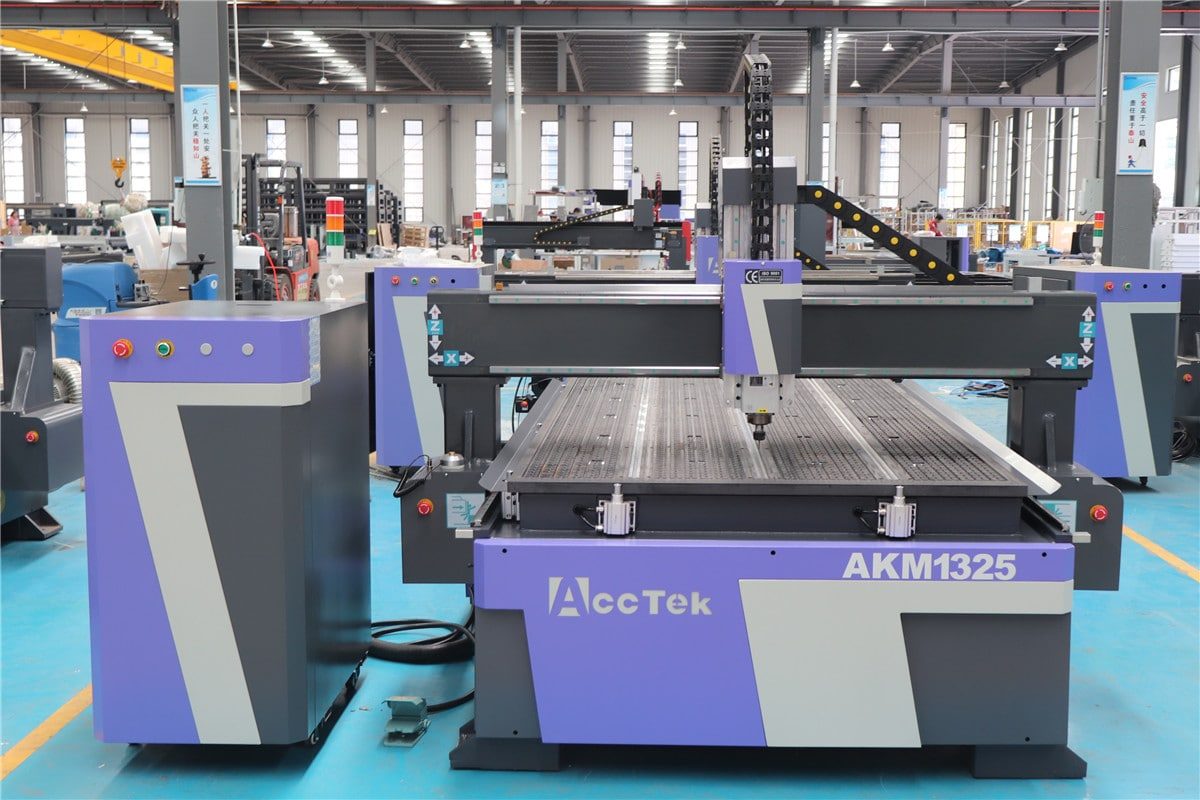
In the realm of modern manufacturing and woodworking, Computer Numerical Control (CNC) routers stand out as indispensable tools. These automated machines execute precise cuts, engravings, and carvings with remarkable efficiency and accuracy. While they undoubtedly enhance productivity and quality, it’s crucial to acknowledge that, like any machinery, CNC routers come with inherent risks. From mechanical perils to software complexities, from material hazards to human factors, the journey through CNC router operation is fraught with challenges that demand vigilance, expertise, and adherence to rigorous safety protocols. In this comprehensive exploration, we delve into the potential hazards associated with utilizing CNC routers and discuss strategies for mitigating them. From the workshop floor to the manufacturing facility, understanding these risks is not merely a matter of compliance but a cornerstone of ensuring the safety of all who operate within the realm of CNC machining.
Understand the Importance of Risk
In the realm of manufacturing and woodworking, the advent of CNC routers has ushered in a new era of precision and efficiency. These automated machines, guided by intricate programming, execute intricate cuts and carvings with remarkable accuracy. However, amidst their capabilities lies a crucial aspect often overlooked: the importance of understanding and mitigating the risks associated with CNC router operation.
- Ensuring Operator Safety: The foremost reason for comprehending risks in CNC router operation is to prioritize the safety of operators. By understanding these risks, operators can adopt appropriate safety measures and protocols to minimize the likelihood of accidents and injuries.
- Protecting Equipment and Workpieces: CNC routers represent a significant investment for manufacturing facilities and woodworking shops. Understanding the potential hazards, allows operators to implement preventive measures to safeguard the equipment and the integrity of the workpieces being processed.
- Mitigating Financial and Legal Liabilities: Accidents or injuries resulting from CNC router operations can have profound financial and legal ramifications for businesses. By understanding and addressing potential risks proactively, businesses can mitigate these liabilities and uphold their commitment to workplace safety.
- Optimizing Productivity and Efficiency: A comprehensive understanding of risks in CNC router operation enables businesses to optimize productivity and efficiency. By identifying potential bottlenecks, safety hazards, or inefficiencies in workflow processes, operators can implement corrective actions to streamline operations and maximize throughput without compromising safety or quality.
- Fostering a Culture of Safety: Lastly, understanding risks in CNC router operations fosters a culture of safety within manufacturing facilities and woodworking shops. This promotes collaboration, communication, and accountability among team members, ultimately creating a safer and more conducive work environment for everyone involved.
The importance of understanding risks in CNC router operation cannot be overstated. By prioritizing safety, investing in training and education, and fostering a culture of continuous improvement, organizations can ensure the safe and efficient operation of CNC routers while maximizing their potential for innovation and growth.
What are the risks of using CNC router?
Operating a CNC router presents a range of potential risks that must be carefully managed to ensure the safety of operators, protect equipment, and maintain productivity. Here are some common risks associated with using CNC routers:
Mechanical Hazards
- Tooling Accidents: High-speed rotating cutting tools pose a significant risk of accidents if they break or become dislodged during operation. This can result in flying debris or tool fragments, endangering nearby operators.
- Moving Parts: CNC routers consist of numerous moving parts, including motors, spindles, and gantry systems. Accidental contact with these moving components can lead to injuries such as lacerations, crush injuries, or amputations.
- Workpiece Mishaps: Improper clamping or securing of workpieces can cause them to shift or dislodge during cutting operations, potentially leading to damage to the workpiece or the machine itself.
Electrical Hazards
- Electric Shock: CNC routers are powered by electricity and contain numerous electrical components. Faulty wiring, damaged insulation, or improper grounding can increase the risk of electric shock or electrocution for operators.
- Fire Hazards: Electrical malfunctions, short circuits, or overheating components can pose a fire hazard in CNC router environments, especially if flammable materials such as wood dust are present.
Environmental Risks
- Airborne Particles: Cutting, milling, or engraving various materials can generate airborne particles such as dust, chips, or fumes. Inhaling these particles can lead to respiratory issues, irritation of the eyes, nose, or throat, and long-term health problems.
- Toxicity: Some materials processed on CNC routers, such as certain woods, plastics, or metals, may release toxic fumes or chemicals when cut or heated. Prolonged exposure to these substances can have adverse health effects on operators.
Material Handling Risks
- Lifting and Carrying: Moving heavy or awkwardly shaped materials, such as large sheets of plywood, poses the risk of musculoskeletal injuries to operators. Repetitive movements, or exceeding weight limits can strain muscles, cause back injuries, or lead to slips and falls.
- Loading and Unloading: Placing materials onto the CNC router’s worktable or removing finished workpieces requires careful coordination and physical exertion. Without proper training or assistance, operators may risk injuries from lifting, reaching, or maneuvering heavy objects.
Software and Programming Risks
- Programming Errors: Errors or inaccuracies in CNC router programming can lead to unexpected machine behavior, resulting in damage to the workpiece or the machine itself. This includes issues such as incorrect tool paths, feed rates, or cutting depths.
- Software Malfunctions: CNC router software may experience glitches, bugs, or compatibility issues that can disrupt operations or compromise the accuracy of cuts.
Operator Errors and Fatigue
- Lack of Training: Inadequate training or lack of familiarity with CNC router operation and safety procedures increases the likelihood of accidents or injuries.
- Fatigue and Distraction: Operating CNC routers for extended periods can lead to operator fatigue, impairing judgment and reaction times. Distractions in the workplace, such as noise, interruptions, or multitasking, can also increase the risk of accidents.
Operator Health and Safety Risks
- Noise Pollution: CNC routers generate significant noise levels during operation, which can exceed recommended exposure limits and contribute to hearing loss over time.
- Ergonomic Strain: Prolonged standing or repetitive movements associated with CNC router operation can lead to musculoskeletal disorders such as back pain, neck strain, or carpal tunnel syndrome.
Maintenance and Inspection Risks
- Lack of Maintenance: Neglecting routine maintenance and inspection of CNC routers can lead to equipment malfunctions, breakdowns, or premature wear of components.
- Improper Repairs: Attempting to repair or modify CNC routers without proper training or expertise can pose additional risks. Improper repairs may worsen existing issues, compromise machine safety, or void warranties.
Precautions and Best Practices
To prevent risks associated with CNC router operation, it’s essential to implement a comprehensive set of measures and best practices that address various aspects of machine safety, material handling, maintenance, and workflow management. Here are some key strategies to mitigate CNC router risks:
Operator Training and Certification
- Provide comprehensive training programs for operators covering machine operation, safety protocols, emergency procedures, and material handling techniques.
- Ensure operators are familiar with CNC router software, programming languages, and troubleshooting procedures to prevent errors and minimize downtime.
- Offer certification programs to validate operators’ skills and knowledge, ensuring they meet competency standards for safe and efficient CNC router operation.
Machine Safety Features and Guarding
- Install and maintain safety features such as emergency stop buttons, interlocks, and perimeter guarding to prevent unauthorized access and stop the machine quickly in case of emergencies.
- Implement safety light curtains or laser scanners to detect the presence of operators within the machine’s work area and automatically halt machine operation to prevent accidents.
- Regularly inspect and test safety systems to ensure they function correctly and comply with regulatory requirements and industry standards.
Personal Protective Equipment (PPE)
- Provide operators with appropriate PPE such as safety glasses, hearing protection, gloves, and respiratory masks to mitigate the risks of injuries from flying debris, noise, chemical exposure, and airborne particles.
- Ensure PPE is properly fitted, maintained, and worn consistently during CNC router operation, and replace damaged or worn-out equipment promptly to ensure maximum effectiveness.
- PPE requirements may vary depending on the specific tasks being performed and the materials being processed. Employers should provide adequate PPE and ensure its proper use and maintenance.
Material Handling Practices
- Develop standardized procedures for material handling tasks, including loading, unloading, and securing workpieces onto the CNC router’s worktable, to minimize the risk of accidents and errors.
- Use lifting aids, hoists, or mechanical assistance devices to safely handle heavy or bulky materials and reduce the strain on operators’ muscles and joints.
- Educate operators on proper lifting techniques, ergonomic principles, and weight limits to prevent musculoskeletal injuries and ensure safe material handling practices.
Software and Programming Safety
- Implement robust quality control measures to verify the accuracy and integrity of CNC router programs before execution, including simulation, verification, and testing on virtual or scrap material.
- Regularly update and maintain CNC router software to address security vulnerabilities, software bugs, and compatibility issues, reducing the risk of program errors or malfunctions during operation.
- Provide ongoing training and support to programmers and operators on CNC router software, programming languages, and best practices to improve programming efficiency and minimize errors.
Workplace Organization and Housekeeping
- Maintain a clean and organized work environment around the CNC router, including the work area, tool storage, and material staging areas, to minimize the risk of slips, trips, and falls.
- Implement regular housekeeping routines to remove dust, debris, and waste materials from the machine and surrounding areas, reducing the risk of fire, equipment damage, and respiratory hazards.
- Establish clear signage, markings, and storage systems to identify hazardous areas, materials, and equipment and promote safe navigation and operation within the CNC router facility.
Emergency Preparedness and Response
- Every CNC router facility should have robust emergency response plans in place to address potential accidents, machine malfunctions, or medical emergencies.
- Emergency stop buttons, fire extinguishers, first aid kits, and evacuation routes should be readily accessible and marked. Operators should be trained to respond promptly and effectively to emergencies.
- Maintain emergency contact lists, communication systems, and reporting mechanisms to facilitate rapid communication and coordination in the event of an emergency or incident involving the CNC router.
Regular Maintenance and Inspection
- Establish a routine maintenance schedule for CNC routers. Regularly inspect machine components such as motors, spindles, drive systems, and tooling for signs of wear, damage, or malfunctions.
- Periodically calibrate and align CNC router axes, tooling, and cutting paths to ensure accuracy and repeatability of machining operations.
- Scheduled lubrication, calibration, and alignment checks help maintain the machine’s performance and prolong its service life.
By implementing these measures and best practices, businesses can effectively mitigate the risks associated with CNC router operation, safeguarding the safety of operators, protecting equipment, and ensuring the efficient and reliable performance of CNC router systems.
Challenges Faced in Risk Mitigation
Even though CNC router security measures are very necessary, there are still some additional challenges faced during the actual implementation process. The following are possible challenges in risk mitigation:
- Budget Constraints: Limited financial resources can hinder the implementation of necessary safety measures and maintenance practices. This could result in postponing crucial maintenance tasks, opting for cheaper but less effective safety equipment, or skimping on employee training. As a result, there may be an increased risk of accidents, machine malfunctions, and workplace injuries.
- Resistance to Security Measures: Some individuals within the organization may resist the implementation of security measures due to perceived inconvenience or disruptions to workflow. Resistance could manifest as reluctance to adopt new safety protocols, bypassing safety features for efficiency, or neglecting cybersecurity measures for CNC programming and data management. Overcoming this resistance requires effective communication, demonstrating the importance of security measures, and involving employees in the decision-making process.
- Awareness Gaps: Lack of awareness or understanding of potential risks and safety protocols among operators and management can exacerbate safety issues. Without proper education and training, operators may not recognize hazardous situations or know how to respond effectively. Similarly, management may overlook critical safety measures or fail to allocate resources for training and maintenance. Addressing awareness gaps involves comprehensive training programs, regular safety briefings, and promoting a culture of safety throughout the organization.
To mitigate these challenges effectively, organizations need to prioritize risk management within their budgets, foster a culture of safety and security, and invest in continuous education and training for employees. Additionally, collaborating with stakeholders and seeking external expertise can provide valuable insights and resources for implementing robust risk mitigation strategies within the constraints of budget, resistance, and awareness gaps.
Summarize
Using CNC routers presents many risks that necessitate careful consideration and proactive mitigation strategies. From the potential for operator injury due to moving parts and high-speed cutting tools to the risks associated with machine malfunctions, material hazards, and software errors, each aspect of CNC router operation demands attention to ensure safety and efficiency. Moreover, challenges such as dust management, electrical hazards, and environmental factors further underscore the need for comprehensive risk management protocols. Organizations can navigate these risks effectively and foster a safer working environment while maximizing the benefits of CNC router technology by prioritizing operator training, implementing robust maintenance practices, adhering to safety standards, and embracing technological advancements.
Specializing in precision and versatility, AccTek CNC provides users with 3-axis, 4-axis, and 5-axis CNC routers, empowering manufacturers, artisans, and hobbyists alike to bring their creative visions to life with unparalleled accuracy and efficiency. In addition to delivering state-of-the-art machinery, AccTek CNC prioritizes user safety by offering a safety guide. These manuals serve as indispensable resources, equipping operators with the knowledge and protocols necessary to mitigate risks and ensure safe operation in diverse machining environments. Contact us to learn more about CNC routers.