- 7-10 Min Read
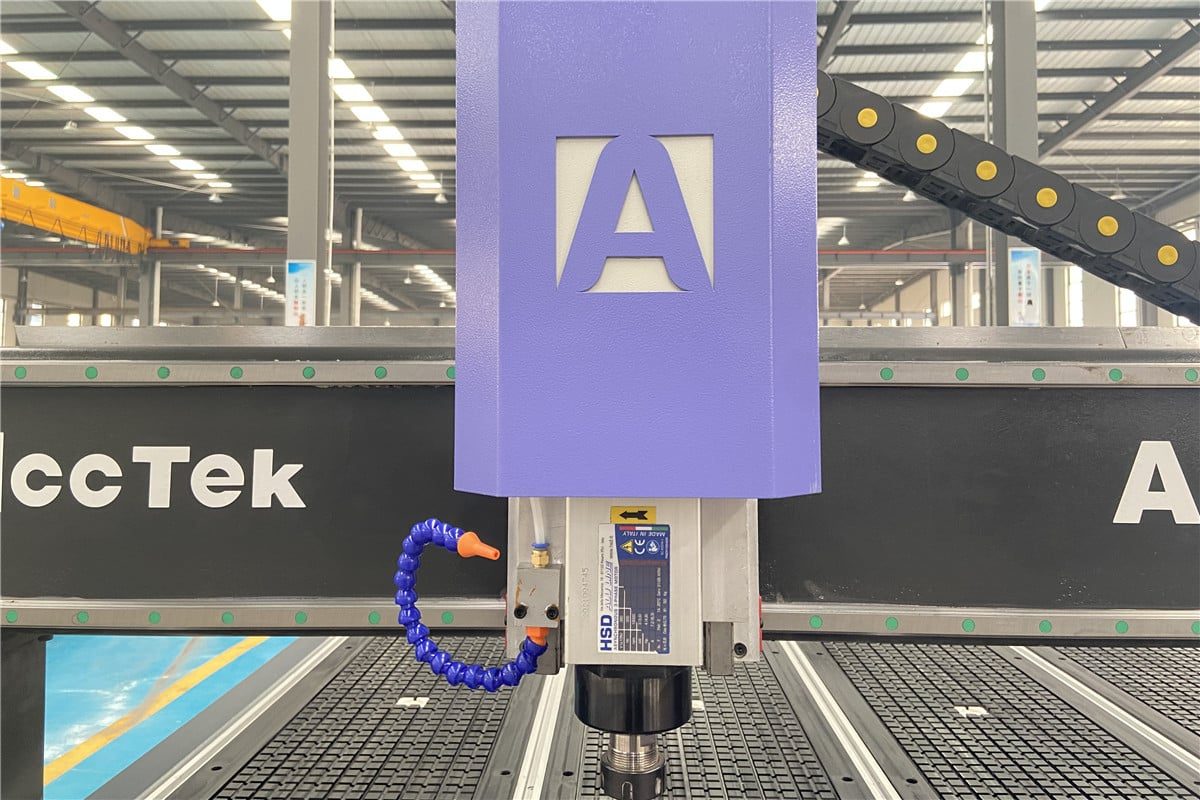
In the realm of Computer Numerical Control (CNC) machining, precision has always been a focus. Whether crafting intricate designs or mass-producing components, the efficacy of CNC routers hinges on the minutiae of their operation. Yet, lurking within this precision-driven domain is a subtle yet potentially disruptive factor: spindle runout.
Understanding the intricacies of spindle runout is not merely an academic pursuit but a practical necessity for those navigating the CNC machining landscape. This article delves into the depths of spindle runout, exploring its origins, manifestations, and the strategies employed to mitigate its deleterious effects. From its impact on surface finish to its role in tool wear, we unravel the multifaceted nature of spindle runout and equip practitioners with the knowledge to safeguard their machining endeavors against its encroaching influence.
Understanding Spindle Runout
Spindle runout refers to the deviation from the intended rotational axis of the spindle in a CNC router. In simpler terms, it’s the amount by which the axis of rotation of the spindle deviates from its ideal or intended path. This deviation can occur due to various factors, including mechanical imbalances, misalignments, wear and tear, or even the quality of the spindle itself. While seemingly innocuous, even minor discrepancies in spindle runout can ripple through the fabrication process, manifesting as defects, dimensional inaccuracies, and reduced tool longevity. The following introduces you to the types of spindle runout:
- Radial Runout: Radial runout, also known as eccentricity, occurs when the spindle wobbles or deviates from its intended axis in a radial direction. It’s typically measured perpendicular to the spindle’s rotational axis. Radial runout can result from factors such as imbalances in the spindle assembly, irregularities in bearing surfaces, or inaccuracies in spindle alignment. This type of runout can lead to surface imperfections, such as waviness or scalloping, particularly evident when machining circular or curved features.
- Axial Runout: Axial runout refers to the deviation of the spindle from its intended axis along the length of the spindle, parallel to its rotational axis. This type of runout can occur due to issues such as misalignment of spindle components, worn bearings, or improper installation of tooling. Axial runout can affect the consistency and depth of cuts, leading to variations in part dimensions and surface finish. It’s especially critical in operations where precise depth control is required, such as contour milling or drilling.
- Total Indicated Runout (TIR): Total Indicated Runout encompasses both radial and axial runout and provides a comprehensive measure of the overall deviation of the spindle from its intended axis. It’s typically measured at a specific point along the length of the spindle and is expressed as the total amount of deviation observed. TIR is a critical metric for evaluating the overall performance and alignment of the spindle, helping machinists assess its accuracy and precision across various machining tasks.
What are the causes of spindle runout?
Spindle runout in CNC routers can stem from various factors, both mechanical and operational. Here are some common causes:
Tool Holder
- Inadequate Clamping Force: If the tool holder does not apply sufficient clamping force to secure the tool properly, the tool may experience excessive movement during machining, leading to runout.
- Poor Taper Contact: Improper seating of the tool in the tool holder taper can result in insufficient contact between the mating surfaces. This can allow the tool to wobble or shift, introducing runout into the machining process.
- Worn or Damaged Holder Components: Wear or damage to components such as collets, collet nuts, or retention knobs can compromise the stability and rigidity of the tool holder, contributing to increased runout.
Chuck
- Incorrect Chuck Size: Using a chuck that is not properly sized for the spindle can result in misalignment between the chuck and the spindle taper. This misalignment can cause the tool to be off-center, leading to runout during machining.
- Worn or Damaged Chuck: Wear or damage to the chuck components, such as the chuck jaws or internal mechanisms, can result in increased runout. A worn or damaged chuck may not grip the tool securely, allowing it to wobble or shift during machining.
Tool
- Tool Wear: As cutting tools wear down over time, they may become less concentric or exhibit irregularities in their geometry. This can introduce runout into the machining process, particularly if the tool is not replaced or sharpened regularly.
- Tool Damage: Chips, nicks, or other damage to the cutting edges of the tool can cause it to cut unevenly or vibrate during machining, resulting in runout.
- Improper Tool Installation: Improper installation of the tool in the tool holder taper can result in insufficient contact between the tool and the tool holder. This can lead to instability and runout during machining.
Spindle
- Bearing Wear: Wear and tear on spindle bearings can lead to increased play or misalignment, causing the spindle to deviate from its intended axis and introduce runout into the machining process.
- Spindle Misalignment: Misalignment between the spindle shaft and housing, or between spindle components such as bearings and shafts, can result in runout during machining. Misalignment may occur during installation, due to improper assembly procedures, or over time as a result of wear and tear.
- Spindle Wear: Wear and tear on the spindle itself, including damage to the spindle shaft or housing, can contribute to spindle runout. Over time, corrosion, abrasion, or fatigue can degrade the precision and alignment of the spindle, leading to increased runout.
Addressing spindle runouts requires a thorough understanding of these potential causes, as well as proactive maintenance and troubleshooting strategies to minimize their impact on CNC router performance. By identifying and addressing issues in each of these areas, CNC operators can minimize runout and optimize machining accuracy and quality.
The impact of spindle runout on CNC router performance
Spindle runout can have significant effects on CNC router performance, impacting various aspects of machining operations. Here are some common effects:
Machining Accuracy is Reduced
- Surface Finish Defects: Runout can manifest as surface imperfections on machined parts, such as waviness, scalloping, or chatter marks. These defects degrade the surface finish of the workpiece, compromising its aesthetic appeal and functional properties.
- Poor Edge Quality: Runout can cause irregularities along the edges of machined features, such as burrs or feathering. These imperfections detract from the precision and cleanliness of part edges, necessitating additional finishing operations to achieve desired quality standards.
- Dimensional Inaccuracy: Spindle runout can cause deviations from the intended dimensions of machined parts. As the spindle deviates from its ideal rotational axis, the tool may cut too deep, too shallow, or at an incorrect angle, leading to dimensional inaccuracies in machined parts. These inaccuracies can result in parts that do not meet design specifications, compromising product quality and functionality.
Tool Wear and Damage
- Increased Tool Wear: Spindle runout contributes to uneven loading and stress on cutting tools during machining operations. As the tool deviates from its intended path due to runout, it may experience erratic cutting forces and contact with the workpiece. This uneven wear pattern accelerates tool degradation, leading to premature dulling or chipping of cutting edges. Increased tool wear not only reduces tool life but also necessitates more frequent tool changes, resulting in higher tooling costs and downtime.
- Risk of Tool Breakage: Runout-induced vibrations and erratic tool movements pose a significant risk of tool breakage during CNC router operations. As the tool encounters unexpected forces and impacts due to runout, it becomes more susceptible to fracture or chipping, especially in brittle materials or high-speed machining applications. Tool breakage not only interrupts production but also poses safety hazards to machine operators and nearby equipment.
Vibration and Noise
- Generation of Vibration During Processing: Spindle runout generates vibrations and noise that propagate through the CNC router system during processing. These vibrations can manifest as chatter, resonance, or oscillations, compromising machining accuracy and surface finish. Excessive vibration also accelerates wear on machine components, such as bearings, drive mechanisms, and structural elements. Moreover, vibrations and noise contribute to operator discomfort and fatigue, detracting from the working environment’s safety and productivity.
- Impact on the Stability of CNC Milling Machines: Runout affects the overall stability and precision of CNC milling machines, compromising their ability to maintain tight tolerances and produce high-quality parts. As the spindle deviates from its intended axis, it introduces dynamic loads and disturbances into the machine structure. These disturbances can cause deflections, flexing, or resonance in machine components, leading to reduced machining accuracy and repeatability.
Spindle runout can significantly impede CNC router performance, affecting part quality, tool life, productivity, and operational efficiency. Minimizing runout through proper maintenance, calibration, and tooling practices is beneficial for achieving optimal machining results and maximizing the capabilities of CNC routers.
Preventive Maintenance Strategy
Preventive maintenance is beneficial for ensuring the optimal performance and longevity of CNC router spindles. Here are some preventive maintenance strategies to consider:
Regular Inspection and Cleaning
- Dust and Debris Management: Regularly remove dust, chips, and debris from the spindle and surrounding areas to prevent interference with spindle operation and cooling.
- Identifying Early Signs of Wear: Conduct routine visual inspections of the spindle assembly, including the spindle housing, shaft, bearings, and cooling system. Look for signs of wear, damage, or contamination that could affect spindle performance.
- Cooling System Maintenance: Ensure that the spindle cooling system is functioning correctly and that coolant levels are adequate. Clean or replace coolant filters as needed to prevent clogging and maintain optimal cooling efficiency.
- Tool Holder Maintenance: Inspect tool holders regularly for signs of wear, damage, or deformation. Clean and lubricate tool holder interfaces to ensure proper seating and clamping of cutting tools, minimizing runout and tool wear.
Proper Tool Installation and Maintenance
- Following Manufacturer Guidelines: Adhere to manufacturer-recommended tool installation procedures and maintenance schedule. From meticulous tool holder seating to precise tool alignment, every aspect of tool installation plays a pivotal role in spindle health.
- Tool Inspection and Replacement: Inspect cutting tools and tool holders regularly for signs of wear, damage, or deformation. Replace worn or damaged tools promptly to prevent premature tool failure and spindle damage.
Spindle Maintenance
- Lubrication: Follow manufacturer recommendations for lubricating spindle bearings and other moving parts. Proper lubrication helps reduce friction, heat, and wear, prolonging the life of the spindle components.
- Balancing: Balance the spindle assembly periodically to minimize vibration and runout. Imbalanced spindles can cause premature wear on bearings and other components, leading to reduced performance and reliability.
- Bearing Maintenance: Monitor spindle bearing condition regularly and replace bearings at recommended intervals or if signs of wear or damage are observed. Proper bearing preload and alignment are beneficial for spindle performance and longevity.
- Alignment Checks and Adjustments: Periodically check spindle alignment and make adjustments as necessary to minimize runout and ensure proper tool centerline alignment.
These preventive maintenance strategies collectively contribute to the longevity, reliability, and performance of CNC router spindles. By proactively addressing potential issues and implementing regular maintenance routines, CNC operators can minimize downtime, reduce the risk of costly repairs, and optimize the productivity of their machining operations.
Summarize
Spindle runout is a critical issue that can significantly impact the performance and quality of CNC router operations. From diminished accuracy to compromised surface finishes, the problems stemming from spindle runout are diverse and far-reaching. However, amidst these challenges lie opportunities for understanding, innovation, and mastery. Armed with knowledge and awareness, machinists can implement proactive measures to minimize spindle runouts and optimize performance. By addressing spindle runouts comprehensively and integrating best practices into their machining processes, CNC router users can achieve higher quality outputs and maximize the potential of their machining operations.
For those seeking a dependable and versatile CNC router, AccTek CNC is the ideal choice. Whether you’re seeking precision in woodworking, metalworking, plastics machining, or other industries, we have the expertise and solutions to meet your needs. AccTek CNC is committed to delivering quality, reliability, and efficiency in every aspect of our products and services. Contact us today, and we look forward to helping you unlock the full potential of your CNC router and achieve your machining goals with precision and efficiency.