- 8-13 Min Read
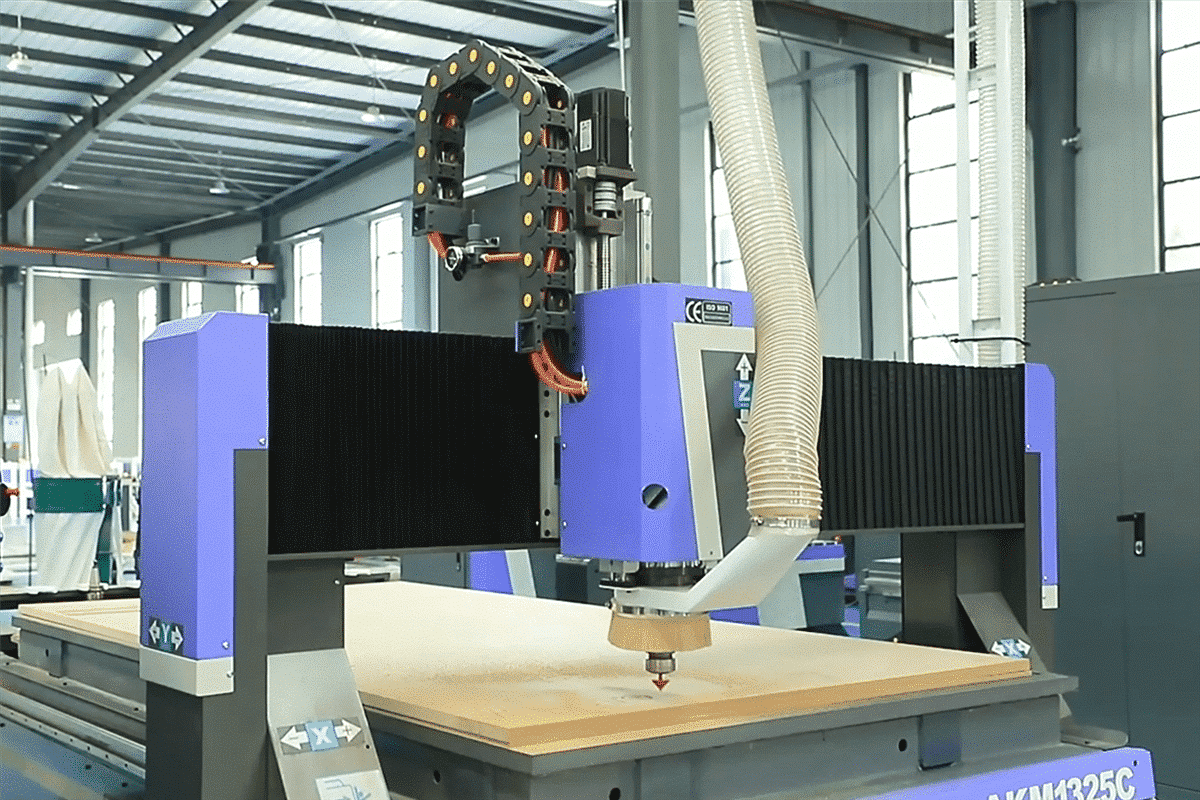
In the world of CNC (Computer Numerical Control) routing, precision and efficiency are paramount. One of the critical processes that ensure both is roughing. While finishing operations often receive the spotlight for their role in creating smooth and precise final products, roughing is an essential preliminary step that lays the groundwork for success. Roughing in CNC routing involves the rapid removal of large volumes of material to approximate the final shape of a part, significantly reducing the workload for subsequent finishing processes.
This article delves into the indispensable role of roughing in CNC routing, uncovering its profound impact on optimizing workflow efficiency, enhancing tool longevity, and ultimately delivering superior quality end products. Through a comprehensive exploration of the principles, techniques, and benefits of effective roughing, this article aims to illuminate the path toward mastering CNC routing for manufacturers seeking to elevate their production capabilities to new heights.
Understanding CNC Routing
CNC routing is a manufacturing process that uses computer-controlled machines to cut and shape materials into precise designs. This technology has revolutionized various industries, including woodworking, metalworking, and plastics, by providing a high degree of accuracy, repeatability, and efficiency.
At its core, CNC routing involves the use of a computer to control the movement of a cutting tool along multiple axes. These machines can follow complex paths and execute intricate designs with minimal human intervention, making them ideal for both prototyping and mass production. The process begins with creating a digital design using CAD (Computer-Aided Design) software, which is then converted into a set of instructions that the CNC router can follow.
One of the primary advantages of CNC routing is its ability to produce highly accurate and consistent parts. The computer control ensures that each piece is manufactured to exact specifications, reducing the likelihood of errors and enhancing the quality of the final product. Additionally, CNC routers can operate continuously with minimal supervision, significantly boosting productivity and reducing labor costs.
CNC routing also offers remarkable versatility, capable of working with a wide range of materials, including wood, metal, plastic, and composites. This flexibility makes it suitable for various applications, from crafting intricate wooden furniture and decorative items to fabricating precise metal components for industrial machinery.
CNC routing represents a cutting-edge approach to manufacturing that combines advanced technology with precision engineering. By harnessing the power of computer control and automation, CNC routers offer limitless possibilities for creating high-quality, customized products across a multitude of industries.
The Main Reasons for Performing Roughing First
In CNC routing, roughing is the critical initial step that sets the stage for a successful machining process. By understanding the importance of roughing, manufacturers can optimize their machining processes and achieve superior results. The primary reasons for performing roughing first can be categorized into five main areas, which are described below:
- Material Removal: The main objective of roughing is to quickly remove large amounts of material from the workpiece. This step involves using aggressive cutting parameters and specialized roughing tools to eliminate the bulk of the material, leaving only a small amount for the finishing phase. Rapid material removal streamlines the machining process, reducing the overall time required to produce the part and preparing it for more precise finishing operations.
- Tool Preservation: Roughing operations are conducted with tools designed to handle high loads and aggressive cutting conditions. By using these robust tools for the initial heavy cuts, the finishing tools are reserved for more delicate, precise work. This approach helps to protect the finishing tools from excessive wear and tear, thereby extending their lifespan and maintaining their effectiveness. As a result, tool replacement costs are minimized, and tool performance is optimized throughout the production process.
- Heat Dissipation: Roughing helps manage and dissipate the heat generated during machining more effectively. Rapid material removal allows the workpiece to cool down more efficiently between passes, reducing the risk of thermal deformation and stress accumulation. Proper heat management is beneficiall for maintaining the dimensional stability and integrity of the part, ensuring that it remains within specified tolerances.
- Improved Surface Finish: Although roughing does not provide a finished surface, it prepares the workpiece for subsequent finishing operations. By leaving a consistent and manageable amount of material for the final cuts, roughing allows finishing tools to operate at slower speeds and with greater precision. This careful preparation results in a smoother, more precise surface finish, as the finishing tools can focus on achieving the desired quality and accuracy without the burden of heavy material removal.
- Increased Efficiency: Roughing significantly enhances the overall efficiency of the machining process. By quickly removing the bulk of the material, roughing reduces the time required for finishing operations. This staged approach ensures that the machining process is streamlined, leading to faster production cycles and higher throughput. Additionally, the reduced wear on finishing tools and improved heat management contribute to a more efficient and cost-effective manufacturing process.
The Principles of Roughing
Rough machining, or roughing, is a fundamental stage in the CNC routing process. Its primary purpose is to remove large volumes of material rapidly to shape the workpiece close to its final form, setting the stage for more precise and delicate finishing operations. The principle of rough machining revolves around the following key concepts:
Material Considerations
Different materials have varying properties that influence the roughing process. Understanding these properties helps in selecting appropriate tools and cutting parameters for efficient and effective roughing. Key considerations include:
- Material Hardness: Harder materials require more robust tools and slower cutting speeds to prevent tool wear.
- Ductility and Brittleness: Ductile materials might produce long chips requiring efficient chip evacuation, while brittle materials need careful handling to avoid fractures.
- Thermal Conductivity: Materials with low thermal conductivity can accumulate heat, necessitating effective cooling strategies.
Machining Strategies
Effective roughing involves selecting the right machining strategy to maximize material removal while maintaining tool life and workpiece integrity. Common strategies include:
- Zigzag (Raster) Pattern: Moves back and forth across the material, suitable for flat surfaces.
- Spiral Pattern: Starts from the outside and spirals inward or vice versa, useful for circular or complex geometries.
- Pocketing: Removes material from the inside out, ideal for cavities and pockets.
- Trochoidal Milling: Uses a circular toolpath to reduce radial forces and heat buildup, extending tool life and improving efficiency.
Tool Selection
The tools used in rough machining are robust and designed to withstand the stresses associated with high material removal rates. These tools typically have features such as:
- Tool Material and Coating: Carbide tools with wear-resistant coatings like TiN (Titanium Nitride) or TiAlN (Titanium Aluminum Nitride) are preferred for their durability.
- Tool Geometry: Tools with more flutes (cutting edges) and specialized geometries for chip evacuation are ideal.
- Tool Size and Shape: Larger diameter tools can remove more material per pass, while shorter tools reduce deflection and improve rigidity.
Cutting Parameters
Rough machining employs aggressive cutting parameters, including high feed rates, deep cuts, and large step-overs. These settings are designed to maximize the material removal rate (MRR), which is the volume of material removed per unit of time. The focus is on speed and efficiency rather than achieving a fine surface finish.
- Feed Rate: The speed at which the tool moves through the material. Higher feed rates increase material removal but can also increase tool wear.
- Depth of Cut: The vertical distance the tool cuts into the material per pass. Taking deeper passes to remove more material per pass.
- Step-Over: The horizontal distance between successive tool passes. Using wide toolpaths to cover more area with each pass.
Workholding and Fixtures
Securing the workpiece properly is beneficiall to maintain precision and prevent movement during roughing. Considerations include:
- Fixture Design: Custom fixtures that match the workpiece geometry can provide stable and secure holding.
- Clamping Methods: Using appropriate clamps, vises, or vacuum tables to hold the workpiece in place.
- Vibration Damping: Employing techniques to reduce vibration, such as using damping materials or balancing clamping forces, to ensure a stable machining process.
The principle of rough machining is centered around efficient, aggressive material removal to rapidly bring the workpiece to a near-net shape. By employing durable tools, optimized cutting parameters, and effective workholding strategies, rough machining sets the foundation for high-quality, precise, and efficient CNC routing operations. Understanding and implementing these principles ensures that manufacturers can maximize productivity, reduce costs, and achieve superior results in their machining processes.
Rough Machining Technology
Roughing techniques in CNC routing encompass a variety of approaches aimed at efficiently removing bulk material to prepare the workpiece for subsequent finishing operations. Each technique offers unique advantages and is suited to different machining scenarios. Here are the key roughing techniques commonly used in CNC routing:
Conventional Routing
Conventional routing, also known as traditional roughing, involves using standard cutting parameters and tool paths to remove material. This method is characterized by its simplicity and versatility, making it suitable for a wide range of materials and geometries. However, it may not always optimize material removal rates or tool life compared to more advanced techniques.
High-Speed Machining (HSM)
High-Speed Machining (HSM) involves using aggressive cutting parameters, such as high spindle speeds, feed rates, and depth of cuts, to achieve rapid material removal while maintaining tool integrity. HSM is particularly effective for machining softer materials like aluminum and plastics, where higher speeds can be utilized without compromising tool life.
Adaptive Roughing
Adaptive roughing, also known as adaptive clearing or dynamic milling, is an advanced roughing technique that dynamically adjusts cutting parameters based on the material and geometry of the workpiece. This method optimizes tool engagement and chip load to maintain consistent cutting forces and maximize material removal rates. Adaptive roughing is ideal for complex geometries and hard materials, where traditional roughing techniques may struggle to achieve efficient results.
Trochoidal Routing
Trochoidal routing, or trochoidal milling, involves using circular tool paths to reduce radial cutting forces and heat buildup during roughing. By continuously engaging the tool with the material along a circular path, trochoidal routing minimizes tool wear and prolongs tool life while achieving high material removal rates. This technique is particularly effective for deep slotting and pocketing operations, where chip evacuation and heat dissipation are critical.
Plunge Roughing
Plunge roughing, also known as plunge milling, is a roughing technique that involves plunging the tool directly into the material to remove excess material rapidly. This method is often used for roughing deep pockets or cavities where conventional cutting paths may be inefficient or impractical. Plunge roughing can achieve high material removal rates with minimal lateral forces, making it suitable for both roughing and semi-finishing operations.
Each roughing technique in CNC routing offers unique advantages and is suited to different machining scenarios based on factors such as material, geometry, and desired outcomes. By understanding and leveraging these techniques, manufacturers can optimize the roughing process to achieve efficient material removal, prolonged tool life, and high-quality finished products. Choosing the right roughing technique depends on the specific requirements of the machining operation and the desired balance between productivity and precision.
Benefits of Rough Machining
Rough machining is the initial phase of material removal that prepares a workpiece for the subsequent finishing stages. The primary goal of roughing is to quickly remove large amounts of material to approximate the final shape of the part, leaving a small amount of material for the finishing process. This approach offers several significant advantages:
Reducing Machining Time
One of the primary benefits of rough machining is the significant reduction in overall machining time. By employing aggressive cutting parameters and optimized tool paths, rough machining rapidly removes large volumes of material. This swift material removal shortens the total time required to bring a workpiece to its near-net shape, thereby accelerating the production process. This time-saving aspect is particularly crucial in high-volume manufacturing environments where meeting tight deadlines is essential.
Extending Tool Life
Rough machining helps extend the life of cutting tools by segregating the heavy material removal phase from the precision finishing phase. Roughing tools are specifically designed to handle the stresses and heat generated during high material removal rates. By using these robust tools for roughing, the more delicate finishing tools are preserved for their precise, low-stress tasks. This strategic use of tools minimizes wear and tear on finishing tools, enhancing their longevity and maintaining their cutting efficiency over time.
Improving Surface Quality
Although rough machining is primarily focused on bulk material removal rather than surface finish, it plays a vital role in setting up the conditions for superior surface quality during finishing. By effectively removing the majority of the excess material, rough machining allows finishing operations to be performed with minimal remaining stock. This precise stock removal enables finishing tools to operate at optimal speeds and feeds, achieving high-quality surface finishes. Additionally, a well-executed roughing process reduces the risk of defects such as chatter marks and uneven surfaces, leading to better overall surface quality.
Improving Dimensional Accuracy
While rough machining itself does not achieve the final dimensional accuracy, it sets the stage for precise finishing operations. By removing the bulk of the material and leaving a uniform layer for finishing, rough machining ensures that finishing tools can achieve tight tolerances and precise dimensions. The initial roughing phase helps manage and reduce internal stresses within the material, minimizing the risk of warping or deformation during subsequent machining steps. This careful preparation results in parts that meet stringent dimensional specifications.
Saving Costs
Cost savings in rough machining are realized through multiple avenues. Firstly, the reduction in machining time directly translates to lower labor and machine operation costs. Secondly, by extending the life of finishing tools, rough machining reduces the frequency of tool replacements and associated costs. Additionally, efficient material removal minimizes waste, leading to better utilization of raw materials. The cumulative effect of these factors results in a more cost-effective machining process, making rough machining a financially advantageous approach in manufacturing.
Rough machining offers a multitude of benefits that enhance the overall efficiency and effectiveness of the CNC routing process. By reducing machining time, extending tool life, improving surface quality, enhancing dimensional accuracy, and saving costs, rough machining sets the stage for successful and economical production operations. Understanding and leveraging these benefits ensures that manufacturers can achieve high-quality outcomes while maintaining competitive advantages in their machining practices.
Summarize
Rough machining serves as the foundational phase that ensures efficient material removal, protects and extends tool life, and sets up the workpiece for precise and high-quality finishing operations. Understanding the key role of rough machining in CNC routing helps optimize the manufacturing process and achieve superior results. As CNC technology continues to evolve, the importance of mastering rough machining techniques becomes even more pronounced, enabling manufacturers to stay competitive in an increasingly demanding industry.
When planning to choose a CNC router to enhance your workshop’s productivity, consider AccTek as a top choice. AccTek CNC offers a diverse range of machine models designed to meet various needs and applications. With their commitment to quality, precision, and customer satisfaction, we provide robust and reliable CNC routers that can significantly boost your operational efficiency and output. Whether you are looking for a machine for intricate designs, heavy-duty cutting, or versatile functionality, we have a solution that fits your requirements. Choose AccTek for excellent performance, and the support you need to take your workshop productivity to the next level.