- 12-17 Min Read
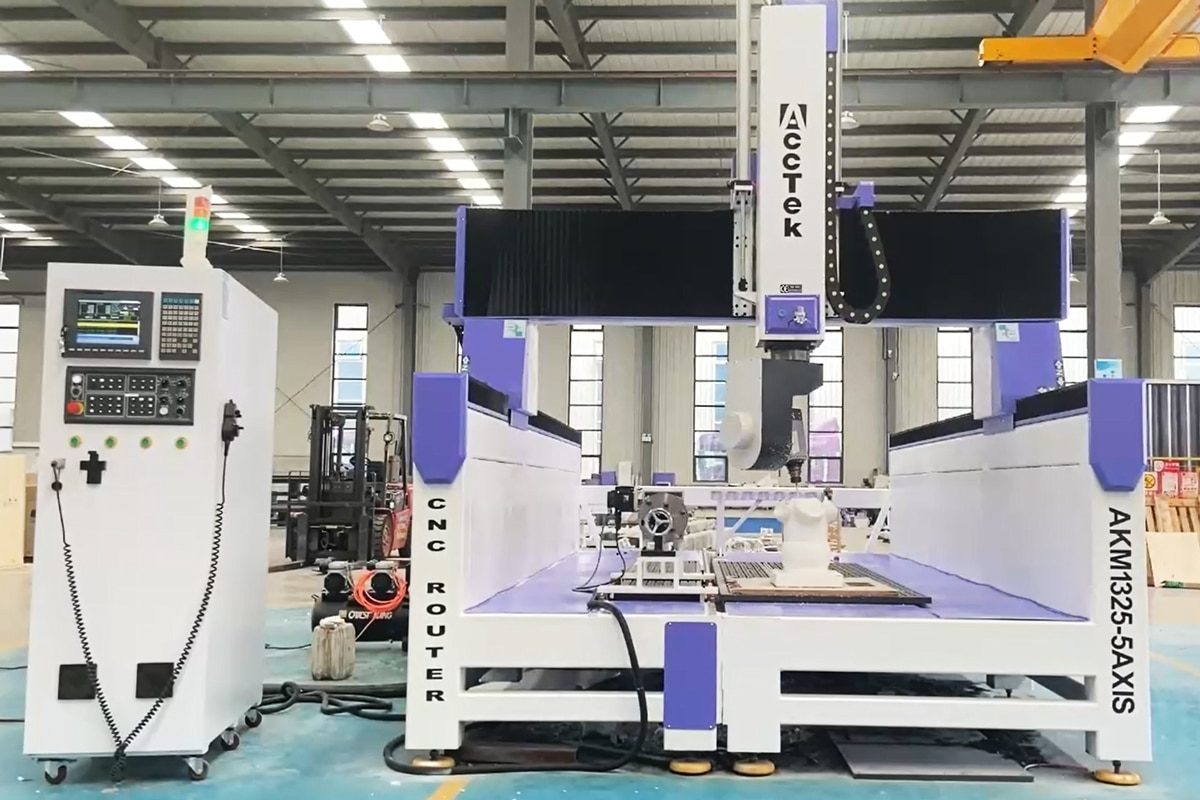
In the world of modern manufacturing and precision machining, 3D CNC routers have become indispensable tools for industries ranging from woodworking to prototyping. Unlike traditional CNC routers that primarily operate in two dimensions or limited 2.5D movements, 3D CNC router operates on more axes, allowing for complex carvings, intricate designs, and precise shaping of materials.
This comprehensive guide aims to provide a detailed understanding of 3D CNC routers, covering their types, key components, and practical applications. Whether you’re a beginner looking to explore CNC machining or an experienced professional seeking deeper insights, this guide will help you make informed decisions about choosing, operating, and maintaining a 3D CNC router.
What is a 3D CNC Router?
A 3D CNC router is an advanced computer-controlled cutting machine capable of processing complex three-dimensional shapes with high precision. Unlike standard 3-axis CNC routers that only move along the X, Y, and Z axes, 3D CNC routers include additional rotational or angular movements, enabling more intricate carving, engraving, and cutting processes. This advanced functionality makes it ideal for applications where detailed and curved surfaces are required.
Main Features of a 3D CNC Router
- Multi-Axis Movement: Unlike standard CNC routers, 3D CNC routers operate on four or five axes, allowing for deep, curved, and complex cuts.
- High Precision and Efficiency: Equipped with servo motors and intelligent control systems, ensuring precise cuts while minimizing waste.
- Capability for Complex Machining: Suitable for relief carving, model making, 3D furniture production, and portrait artwork, thanks to its ability to cut from multiple angles.
- Automated Toolpath Generation: Works with advanced CAD/CAM software (such as Fusion 360, PowerMill, and Vectric Aspire) to generate optimized toolpaths for 3D machining.
- Versatile Material Processing: Can handle a variety of materials, including wood, MDF, plastics, foam, and composites, making it suitable for diverse industries.
Main Components of a 3D CNC Router
- Rotary Axis (A-Axis) or Multi-Axis System: Enables rotation or tilting of the workpiece or cutting head, depending on the machine type.
- Swing Head (4-Axis) or Tilting Spindle (5-Axis): Allows cutting from various angles without manual adjustments.
- Spindle Motor: High-speed cutting tool that varies in power depending on material and application needs.
- Worktable: This can include vacuum suction or T-slot clamping to hold materials securely.
- Stepper or Servo Motors: Provide precise control for multi-axis movement.
- Control System: Processes G-code instructions and manages real-time tool movement, often including DSP, Syntec, or Siemens controllers.
- Frame and Gantry: The structural body of the router that supports the spindle and enables movement.
- CAD/CAM Software: Converts 3D models into machine instructions, allowing the creation of intricate and detailed designs.
With their ability to process cylindrical, curved, and multi-angle surfaces, 3D CNC routers are essential for industries requiring complex, high-precision machining. These advanced machines significantly improve efficiency, reduce manual labor, and enable more creative and intricate production possibilities.
Types of 3D CNC Routers
3D CNC routers are advanced CNC machines designed to cut and carve complex three-dimensional shapes with high precision. Depending on the number of movement axes and cutting capabilities, they can be classified into three main types: rotary axis 3D CNC routers, 4-axis 3D CNC routers, and 5-axis 3D CNC routers. Each type has its unique structure, working principle, and application scope.
Rotary Axis 3D CNC Router
A rotary axis 3D CNC router is a 3-axis CNC machine equipped with a rotary attachment (A-axis) that allows for cylindrical material processing. This means the material can rotate while the spindle moves along the X, Y, and Z axes, enabling the machine to carve rounded and intricate designs on cylindrical objects.
Key Features
- Uses an A-axis rotary attachment for 360-degree engraving on round objects.
- Works similarly to a lathe but offers more detailed carving capabilities.
- Ideal for column engraving, chair legs, statues, and cylindrical furniture components.
Common Applications
- Woodworking: Sculpting table legs, railings, and cylindrical furniture.
- Advertising & Signage: Engraving letters or decorative elements on round surfaces.
- Art & Crafts: Carving statues, religious sculptures, and intricate cylindrical designs.
4-Axis 3D CNC Router (Swing Head CNC Router)
A 4-axis 3D CNC router features a swinging spindle that tilts along the A-axis, allowing it to cut materials at different angles without needing to reposition the workpiece manually. This design enhances the ability to machine angled surfaces, deep relief carvings, and more complex 3D designs compared to a standard 3-axis machine.
Key Features
- The spindle swings to an adjustable angle, allowing for angled and curved cutting.
- Offers more depth and contouring capabilities compared to a 3-axis CNC router.
- Reduces manual repositioning, improving workflow efficiency.
Common Applications
- Wood Carving: Creating 3D relief sculptures, cabinet doors, and artistic designs.
- Mold Making: Machining complex molds with inclined surfaces.
- Architectural Components: Engraving intricate designs into columns, door panels, and wall decorations.
5-Axis 3D CNC Router
A 5-axis 3D CNC router is the most advanced type, featuring simultaneous movement along X, Y, Z, A, and B axes. This allows the cutting tool to approach the workpiece from multiple angles, making it ideal for machining highly intricate and detailed parts without manual repositioning.
Key Features
- Full multi-directional cutting ability with tilting and rotating spindle movement.
- Capable of machining extremely complex 3D shapes and undercuts.
- Used for high-precision applications requiring flawless surface finishes.
Common Applications
- Art and Sculpture: Artists and sculptors use 5-axis CNC routers to create intricate and detailed works of art. The ability to machine from multiple angles allows for the creation of complex and realistic sculptures that would be difficult to achieve by hand.
- Custom Furniture and Cabinetry: 5-axis CNC routers enable the production of intricate furniture designs, custom cabinetry, and detailed carvings. The precision and versatility of these machines open up new possibilities for creativity and craftsmanship.
- 3D Model: The 5-axis CNC router machine is used for 3D milling in mold making, especially for car body making, boat mold building, and other 3D modeling projects.
Each type of 3D CNC router serves different needs depending on the complexity of the design and material requirements. Rotary axis CNC routers specialize in cylindrical workpieces, 4-axis CNC routers provide swinging spindle movement for angled and deep relief carving, and 5-axis CNC routers offer ultimate flexibility for complex 3D machining across multiple industries. Understanding the types of 3D CNC routers and their respective application areas can provide direction for you to choose the right machine.
Materials Compatible with 3D CNC Routers
A 3D CNC router is a versatile machine capable of cutting, carving, and engraving a wide range of materials. Depending on the spindle power, cutting tools, and machine configuration, these routers can process both soft and hard materials with high precision. Below are the main categories of materials compatible with 3D CNC routers.
Wood and Wood-Based Materials
Wood is one of the most commonly processed materials for 3D CNC routers, especially in woodworking, furniture making, and artistic carving. Here are the compatible wood types:
- Softwood (Pine, Cedar, Spruce): Used for general carvings, furniture, and sculptures.
- Hardwood (Oak, Mahogany, Walnut, Teak): Ideal for intricate designs, fine furniture, and durable applications.
- Plywood & MDF (Medium-Density Fiberboard): Great for cabinets, panels, and layered 3D carvings.
- Bamboo: Used in eco-friendly furniture and decorative panels.
Metals (Soft & Non-Ferrous Metals)
ile standard CNC routers are not designed for cutting thick metal, high-powered 3D CNC routers with strong spindles can handle soft and non-ferrous metals. Here are the compatible metal types:
- Aluminum: Widely used for signage, prototypes, and industrial components.
- Brass & Copper: Commonly used for decorative engravings, jewelry, and electrical components.
- Bronze: Ideal for artistic sculptures, nameplates, and heritage engravings.
It is important to note that cutting metal requires a high-speed spindle, proper cooling systems, and carbide or diamond-coated cutting tools to prevent overheating.
Plastics & Composites
3D CNC routers are highly effective in cutting plastics and composite materials used in signage, industrial parts, and prototyping. Here are the compatible plastic types:
- Acrylic (PMMA): Used in signage, decorative panels, and artistic engravings.
- Polycarbonate (PC): Strong and durable, used in protective shields and machine parts.
- PVC (Polyvinyl Chloride): Common for industrial applications and plastic enclosures.
- HDPE (High-Density Polyethylene): Ideal for molds, engineering plastics, and marine applications.
Foam & Soft Materials
Foam materials are widely used in packaging, prototyping, and artistic models due to their lightweight and easy machinability. Here are the compatible foam types:
- EPS (Expanded Polystyrene): Ideal for large 3D sculptures, mold patterns, and architectural prototypes.
- PU Foam (Polyurethane Foam): Used in automotive, medical models, and lightweight signage.
- EVA Foam: Popular for costume making, padding, and protective cases.
3D CNC routers are highly adaptable machines capable of cutting, carving, and engraving a broad range of materials. The type of material you can process depends on the machine’s spindle power, cutting tool selection, and cooling system.
Choosing the Right 3D CNC Router
Choosing the right 3D CNC router involves evaluating key factors such as application, material compatibility, machine specifications, and budget. Whether selecting a rotary axis CNC router, a 4-axis CNC router, or a 5-axis CNC router, careful consideration of these aspects ensures the best machine for your needs.
- Main Application: The first step in selecting a 3D CNC router is identifying the primary application. If you need to engrave cylindrical objects, a rotary axis CNC router is ideal. For angled cuts and deep relief carving, a 4-axis CNC router provides better flexibility. A 5-axis CNC router is the best choice for complex 3D machining, such as mold making and intricate sculpting.
- Material Type and Size: Different 3D CNC routers support various materials, including wood, plastic, metal, foam, and composites. Softer materials like MDF, acrylic, and foam require less spindle power, whereas metals and dense hardwoods demand a rigid machine frame and high-powered spindle. The working area size should match your project requirements, ensuring ample space for larger materials.
- Spindle Power and Speed: Spindle power affects cutting capability and efficiency. 1.5kW–3kW spindles are suitable for light-duty carving, while 3kW–9kW spindles are better for heavy-duty machining of dense materials. A high-speed spindle (18,000–24,000 RPM) is preferred for fine-detail engraving, whereas lower-speed spindles (up to 12,000 RPM) handle deep cuts in tougher materials.
- Machining Speed and Efficiency: Production efficiency depends on feed rates, spindle speed, and toolpath optimization. 5-axis CNC routers offer superior efficiency by machining complex parts in a single setup, whereas rotary axis and 4-axis machines may require multiple operations. Machines with servo motors and advanced control systems offer faster, more stable performance.
- Precision and Accuracy: 5-axis CNC routers provide the highest accuracy, allowing for multi-angle cutting without repositioning. Machines with linear guide rails, ball screws, and high-resolution encoders ensure smooth and precise movement, minimizing cutting errors.
- Rigidity and Manufacturing Quality: The frame structure and build quality impact the machine’s durability and stability. CNC routers made from heavy-duty cast iron or steel absorb vibrations better, reducing cutting inconsistencies. Machines with reinforced gantries and sturdy drive systems offer longer service life and improved machining performance.
- Control System: The control system determines machine performance and user experience. Popular CNC controllers include DSP, Mach3, Syntec, Siemens, and Fanuc. Machines with user-friendly interfaces, offline operation, and advanced motion control provide greater flexibility and ease of use.
- Safety Features: A reliable safety system protects both the operator and the machine. Features such as emergency stop buttons, limit switches, dust extraction systems, and protective covers enhance workplace safety. 5-axis CNC routers often include collision avoidance technology to prevent tool or workpiece damage.
- Comments and Suggestions: Before purchasing, consider feedback from existing users, industry experts, and manufacturers. Checking customer reviews, machine demonstrations, and real-world case studies can help assess performance and reliability. Consulting with CNC experts ensures the selected machine meets specific business needs.
- Budget Considerations: Prices vary depending on machine type, features, and specifications. Rotary axis CNC routers are more affordable for small businesses, whereas 4-axis and 5-axis CNC routers are more expensive due to their advanced motion control and high-precision components. Evaluating cost vs. productivity gains ensures a profitable investment.
- Operator Training and Support: A well-supported CNC router includes training, technical support, and maintenance assistance. Manufacturers offering installation guidance, software tutorials, and after-sales service ensure smoother machine operation. Investing in training for operators maximizes efficiency and reduces errors.
Choosing the right 3D CNC router depends on application type, material compatibility, machining precision, automation features, and budget constraints. Whether selecting a rotary axis, 4-axis, or 5-axis CNC router, considering these factors will ensure the best performance, efficiency, and return on investment for your business or creative projects.
Setting Up and Operating a 3D CNC Router
The future development of CNC routers is likely to involve advancements in technology, addressing current challenges, and expanding capabilities to meet the evolving needs of industries. In this section, by understanding the challenges faced by CNC routers, we explore some of its potential development areas in the future. As these technologies continue to advance, CNC routers are likely to play a crucial role in shaping the future of manufacturing.
Pre-Setup Considerations
Before installation, ensure the workspace is suitable for CNC operation. Consider:
- Stable and Level Work Surface: Prevents machine vibrations.
- Power Requirements: Check voltage compatibility and grounding.
- Dust Collection System: Reduces debris buildup.
- Safety Precautions: Use protective barriers, emergency stops, and ventilation if needed.
Machine Installation and Calibration
- Frame and Bed Leveling: Secure the router on a flat surface to avoid misalignment.
- Spindle and Tool Calibration: Align the spindle and install the cutting tool properly.
- Axis Zeroing and Work Coordinate Setup: Set the X, Y, and Z zero points to ensure correct cutting paths.
- Rotary Axis (If Applicable): For rotary CNC routers, secure the A-axis attachment and calibrate it.
Choosing and Securing the Workpiece
- Material Selection: Ensure compatibility with the spindle power and tooling.
- Workpiece Fixing: Use clamps, vacuum tables, or screws to secure the material.
- Workpiece Alignment: Ensure the workpiece is square to the machine’s axes for accurate machining.
CNC Software and G-Code Preparation
- Design in CAD Software: Create or import a 3D model using software like AutoCAD, Fusion 360, or ArtCAM.
- Generate Toolpaths in CAM Software: Convert the design into G-code instructions using CAM software like Vectric Aspire or Mastercam.
- Simulation Check: Run a simulation of the toolpath to detect errors before cutting.
Running the CNC Router
- Load the G-Code: Transfer the program to the machine using a USB, LAN, or direct PC connection.
- Set Spindle Speed and Feed Rate: Adjust based on material type and cutting tool.
- Start the Machining Process: Begin with a test cut before full production.
- Monitor the Operation: Observe for unexpected vibrations, tool wear, or material shifting.
Post-Processing and Machine Maintenance
- Remove the Workpiece: Carefully detach the finished product and check for precision and finishing quality.
- Tool Cleaning and Inspection: Clean the spindle, tools, and worktable to prevent debris buildup.
- Lubricate Moving Parts: Ensure smooth axis movement by maintaining rails, ball screws, and motors.
- Software Updates and System Checks: Regularly update CNC control software and check calibration settings.
Setting up and operating a 3D CNC router requires proper calibration, secure workpiece placement, optimized software settings, and ongoing maintenance. By following these steps, operators can maximize the precision, efficiency, and longevity of their rotary axis, 4-axis, or 5-axis CNC router.
Maintenance and Safety Considerations
Whether using a rotary axis CNC router, a 4-axis CNC router, or a 5-axis CNC router, regular upkeep minimizes downtime and prevents accidents. Below are key maintenance routines and safety considerations for optimal performance.
Maintenance Considerations
- Routine Cleaning and Dust Management: After each use, dust, debris, and material particles should be removed from the worktable, spindle, and motion components. Using a dust collection system helps prevent buildup that can cause overheating and affect precision. Regularly cleaning the cooling fans, air vents, and electrical enclosures ensures proper airflow and prevents system malfunctions.
- Spindle and Tool Maintenance: Spindle bearings should be checked for wear and unusual noises, as faulty bearings can reduce accuracy. Cutting tools must be properly secured to prevent vibration, and dull or damaged tools should be replaced to maintain precision and efficiency. Lubricating the spindle and tool holder mechanism also helps extend their lifespan and ensures smooth operation.
- Lubrication and Motion System Checks: Lubricating the linear rails, ball screws, and bearings reduces friction and wear on moving parts. Regularly inspecting belts, couplings, and drive motors ensures that the motion system functions smoothly. Any loose or worn-out parts should be tightened or replaced immediately to avoid machine misalignment and accuracy loss.
- Electrical and Control System Maintenance: The electrical system of a 3D CNC router must be regularly inspected for loose or damaged components. Any exposed wiring should be addressed immediately to prevent short circuits. CNC control software should also be updated to the latest version to improve efficiency, compatibility, and operational stability.
- Calibration and Alignment: Over time, the machine’s accuracy can drift due to regular operation, making routine calibration necessary. Checking the zeroing points of the X, Y, and Z axes ensures that the machine cuts precisely as programmed.
Safety Considerations
- Personal Protective Equipment (PPE): Safety gear is essential when operating a 3D CNC router to protect against dust, noise, and flying debris. Operators should always wear safety glasses, hearing protection, and dust masks, especially when working with wood, plastic, or composite materials.
- Workpiece and Tool Safety: Ensuring that the workpiece is securely clamped or vacuum-held prevents movement that could cause inaccurate cuts or potential injury. Always use the correct cutting tool and appropriate feed rates to avoid excessive tool pressure and breakage.
- Emergency Stop and Safety Features: Every CNC router should have easily accessible emergency stop buttons to immediately halt operations in case of an issue. Safety features such as limit switches and safety enclosures should be checked regularly to ensure they are working properly.
- Fire and Overheating Precautions: Working with materials like wood, plastic, and foam generates fine dust that can pose a fire hazard. A fire extinguisher should always be available near the machine, and dust collection should be active to prevent combustible dust accumulation. Also, ensure proper cooling systems are functioning to prevent spindle overheating.
- Operator Awareness and Training: Only trained personnel should operate a 3D CNC router. Operators should be familiar with the control software, machine functions, and safety protocols before running a program. CNC machines should never be left unattended during operation, as unexpected errors can cause tool breakage, material wastage, or even damage to the machine itself.
Regular maintenance and strict adherence to safety protocols ensure the efficient and safe operation of a 3D CNC router. By performing routine inspections, keeping components clean and lubricated, and following safety guidelines, operators can maximize machine lifespan and prevent workplace hazards.
Summarize
A 3D CNC router is a powerful tool that brings precision, efficiency, and creativity to industries ranging from woodworking to prototyping. Selecting and using a 3D CNC router requires careful consideration of your project requirements, material compatibility, machine type, and precision needs. Investing in the right CNC router and maintaining it properly ensures efficiency, accuracy, and long-term performance in your machining operations. As CNC technology continues to evolve, you can take your craftsmanship and production capabilities to the next level.
As a professional CNC router manufacturer in China, AccTek CNC is a trusted provider of high-quality 3D CNC routers tailored to meet the demands of various industries. Whether you need a rotary axis CNC router for cylindrical engraving, a 4-axis CNC router for intricate relief carvings, or a 5-axis CNC router for complex multi-directional machining, we offer precise, efficient, and durable solutions for your projects. By choosing AccTek CNC, you gain access to expert craftsmanship, and reliable customer service, ensuring that your CNC machining operations achieve maximum precision, efficiency, and profitability.