- 10-15 Min Read
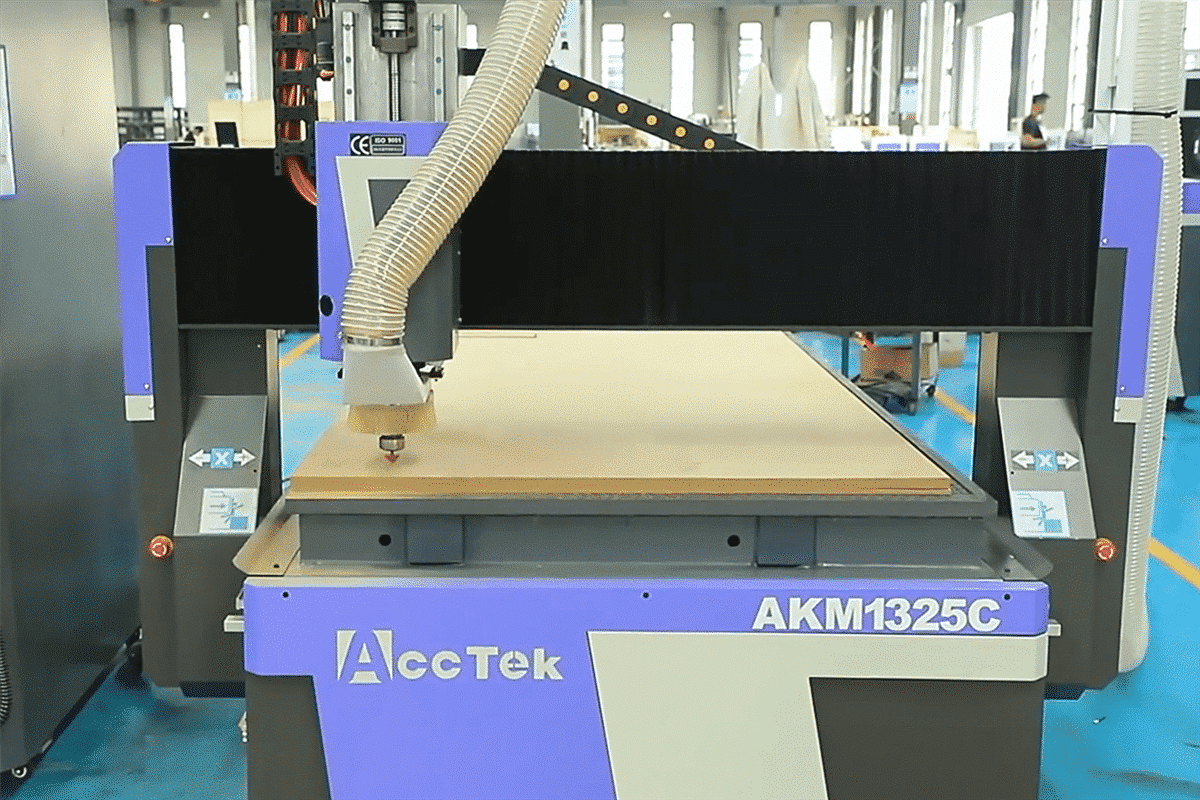
CNC (Computer Numerical Control) routers have revolutionized the woodworking industry by providing precision, efficiency, and versatility in processing various types of wood. Whether you are a professional woodworker, a furniture manufacturer, or a hobbyist, understanding the types of wood best suited for CNC router processing is beneficial to achieving high-quality results. Different woods offer unique characteristics in terms of hardness, grain pattern, density, and workability, which can significantly impact the outcome of your projects. Understanding these properties can help you select the most suitable wood for your specific projects, ensuring both aesthetic appeal and structural integrity.
In this article, we will explore a variety of wood types commonly used in CNC router machining. From hardwoods like oak and maple, known for their durability and fine grain, to softer woods like pine and cedar, valued for their ease of machining and affordability, we will provide a comprehensive guide to help you make informed decisions. By analyzing the factors that influence wood selection and clarifying tips for CNC router operation, we aim to provide you with the comprehensive knowledge you need to enhance your CNC router processing of wood.
Understanding CNC Routing for Woodworking
CNC routers represent a significant advancement in the field of woodworking, bringing automation and precision to tasks that once required extensive manual labor. These machines are designed to follow programmed instructions to cut, carve, and shape materials, offering a high degree of accuracy and repeatability. CNC routers can produce complex designs and intricate patterns with ease, making them invaluable tools for furniture makers, cabinetry professionals, sign makers, and even artists. Their ability to handle a variety of materials, including different types of wood, adds to their versatility and widespread adoption in the industry.
The Importance of Wood Selection
- Finished Product Quality: The density and grain structure of the wood affect the smoothness of the cut surfaces. Denser woods allow for finer and more precise details in intricate designs, enhancing the overall quality of the finished product.
- Durability: Hardwoods are more resistant to dents, scratches, and wear, ensuring a longer-lasting product. Softwoods are more susceptible to damage and may not be suitable for high-use items.
- Aesthetics: The natural color and grain patterns of the wood significantly impact the product’s visual appeal. Different woods react differently to stains and finishes. Hardwoods generally accept stains more uniformly, allowing for a more consistent and attractive finish, whereas softwoods can result in blotchy staining.
- Efficient Processing: Softer woods are easier to machine and require less power, allowing for quicker processing times. However, they might require more care to avoid damage. Hardwoods, while more challenging to machine, produce cleaner cuts and finer details, which can reduce the need for additional finishing work.
- Reduced Wear on CNC Routers: The hardness of the wood directly affects the wear and tear on CNC router bits. Hardwoods can dull tools faster, necessitating more frequent sharpening or replacement, whereas softer woods cause less wear on the tools, extending their lifespan.
The importance of wood selection in CNC routing cannot be overstated. The type of wood used in your CNC project affects the quality, durability, and aesthetics of the finished product. Choosing the right wood type not only enhances the visual and structural qualities of the project but also ensures efficient machining and reduces wear and tear on the CNC equipment. Understanding these factors is essential for anyone looking to achieve the best results in their CNC routing endeavors.
Types of Wood Suitable for CNC Routing
Several types of wood are particularly suitable for CNC routing, each offering unique characteristics. Understanding these differences is beneficial for achieving the best results in any woodworking endeavor. Here are some of the most commonly used woods in CNC routing:
Hardwoods
- Oak: Known for its strength, durability, and distinct grain patterns, oak is an excellent choice for furniture and decorative pieces. Its hardness allows for fine details and a smooth finish.
- Maple: Maple is prized for its fine, even texture and hardness. It’s ideal for projects requiring precision and detail, such as cabinetry and intricate carvings.
- Cherry: Cherry wood offers a smooth texture and rich color, making it perfect for high-end furniture and decorative work. Its workability and smooth finish are highly valued in CNC routing.
- Walnut: With its dark, rich color and fine grain, walnut is favored for luxury items and intricate designs. It is sturdy and takes finishes well, providing an elegant appearance.
Softwoods
- Pine: Pine is widely used due to its affordability and ease of machining. It’s suitable for larger projects and less detailed work, such as furniture frames and signage.
- Cedar: Cedar is known for its natural resistance to decay and insects. It’s easy to machine and has a pleasant aroma, making it suitable for outdoor projects and storage chests.
- Redwood: Similar to cedar, redwood is durable and resistant to weather, making it a good choice for outdoor furniture and structures.
Engineered Woods
- Plywood: Plywood is a versatile and cost-effective material, consisting of multiple layers of wood veneer glued together. It is stable, easy to machine, and widely used for cabinetry, furniture, and paneling.
- MDF (Medium-Density Fiberboard): MDF is made from wood fibers compressed with resin. It provides a smooth, uniform surface that is excellent for painting and detailed work. It’s commonly used for interior projects, such as moldings, panels, and decorative elements.
- HDF (High-Density Fiberboard): Similar to MDF but denser and stronger, HDF is used for high-traffic areas and more durable applications. It is suitable for flooring, cabinetry, and furniture components.
Exotic Woods
- Teak: Teak is highly durable and resistant to moisture, making it ideal for outdoor furniture and marine applications. Its rich color and grain add a luxurious touch to projects.
- Mahogany: Mahogany is known for its deep, reddish-brown color and fine grain. It’s used in high-end furniture, musical instruments, and detailed carvings due to its stability and workability.
- Ebony: Ebony is extremely hard and dense, providing a high-gloss finish when polished. It is ideal for fine inlay work, musical instruments, and luxury items.
Each type of wood offers unique advantages, and the choice depends on the specific requirements of your project, including the desired appearance, durability, and ease of machining. By selecting the appropriate wood, you can optimize the performance of your CNC router and achieve the best possible results.
Factors Affecting Wood Selection
Choosing the right type of wood for CNC routing involves considering several key factors that can influence the quality, efficiency, and overall success of your project. Here are the primary factors to consider:
Density and Hardness
- Density: The density of wood refers to its mass per unit volume and significantly impacts its machinability and structural properties. Denser woods, such as oak and walnut, are heavier and offer better support and durability but require more powerful equipment and sharper tools for CNC routing. These woods can provide excellent structural integrity and resistance to wear and tear, making them suitable for high-stress applications.
- Hardness: Hardness measures the wood’s resistance to indentation and wear. Hardwoods, including maple and cherry, are prized for their ability to hold intricate details and smooth finishes. However, they can be challenging to machine due to their toughness, necessitating careful tool selection and maintenance. In contrast, softer woods like pine and cedar are easier to cut and shape but may not offer the same level of detail and durability.
Grain Orientation
- Straight Grain: Woods with a straight grain pattern, such as maple, are generally easier to machine and less likely to splinter or tear out during the routing process. The uniformity of the grain allows for smoother cuts and more predictable results, ideal for detailed work.
- Curly or Wavy Grain: Woods with more complex grain patterns, such as curly maple or figured walnut, can add visual interest and aesthetic appeal to the final product. However, these patterns can make the wood more challenging to machine, as the grain direction changes can cause irregularities in cutting. Special care and slower cutting speeds may be required to achieve the desired finish without damaging the wood.
Moisture Content
- Stability: The moisture content of wood significantly influences its stability and behavior during machining. Wood that is too wet can warp, twist, or shrink as it dries, leading to inaccuracies in cuts and potential structural issues in the finished product. Kiln-dried wood, which has been dried to a specific moisture level, is preferred for CNC routing due to its stability and reduced likelihood of dimensional changes.
- Machinability: Excess moisture can also affect the machinability of wood. Wet wood is more prone to gumming up tools, increasing wear and tear on the equipment and potentially leading to less clean cuts. Ensuring that the wood is adequately dried before machining can enhance the quality of the routed edges and prolong the life of the CNC tools.
Knots and Defects
- Knots: Knots are natural imperfections in wood where branches were once connected to the trunk. While they can add character and visual interest to a piece, knots can also present challenges during CNC routing. They are typically harder and denser than the surrounding wood, which can cause irregularities in cutting and increase the risk of tool damage or breakage.
- Defects: Other defects, such as cracks, splits, and checks, can compromise the structural integrity and aesthetic quality of the wood. When selecting wood for CNC routing, it is important to inspect for and either avoid or work around these imperfections. Using wood with minimal defects ensures a smoother machining process and a higher-quality finished product.
Cost and Availability
- Budget Constraints: The cost of the wood can significantly impact your project, especially if you are working on a larger scale. Exotic woods tend to be more expensive, while domestic hardwoods and softwoods are often more affordable.
- Local Availability: The availability of certain wood types can vary by region. Locally sourced woods are often more economical and sustainable options.
By carefully considering these factors, you can select the most appropriate wood for your CNC routing projects, ensuring that your finished products meet both your aesthetic and functional requirements.
CNC Router Technology for Different Woods
CNC router technology offers precision and efficiency in woodworking, but working with different types of wood requires specific considerations to ensure optimal results. This section introduces the key aspects of CNC router technology suitable for various woods, focusing on tool precautions, fixing and clamping, and dust removal.
Tool Precautions
- Hardwoods (e.g., Oak, Maple): Use carbide or diamond-tipped tools due to the density and hardness of these woods. Regularly check and maintain the sharpness of your tools to ensure clean cuts and prolong tool life.
- Softwoods (e.g., Pine, Cedar): High-speed steel (HSS) tools are sufficient due to the softness of these woods. Ensure tools are sharp to avoid tearing and fuzzy edges.
- Exotic Woods (e.g., Teak, Ebony): Opt for carbide or diamond-coated tools because of the hardness and potential silica content in these woods. Frequent checks for tool wear are necessary to maintain cutting quality.
Adjust the feed rate and spindle speed according to the wood type. Hardwoods require slower feed rates and moderate spindle speeds to prevent burning and ensure smooth cuts. Softwoods can handle faster feed rates but still require moderate spindle speeds to avoid tear-out. Exotic woods may need even slower feed rates to handle their density and prevent tool wear.
Fixing and Clamping
- Hardwoods: Use strong clamps and fixtures to prevent movement due to the hardness of the wood, which can cause significant resistance during cutting. Ensure the wood is flat and stable on the worktable.
- Softwoods: While these woods are easier to cut, they are also more prone to shifting. Use a combination of clamps and vacuum tables to hold the wood securely in place.
- Exotic Woods: Given their high value and potential for movement due to density variations, use specialized clamps and possibly adhesive methods to ensure they remain firmly in place without damaging the surface.
Utilize a combination of mechanical clamps and vacuum hold-downs where applicable. For intricate cuts or smaller pieces, double-check that clamps do not interfere with the router’s path. Always test the stability of the wood before starting the machining process.
Dust Removal
- Hardwoods: Due to the high volume of dust produced, use a powerful dust extraction system. Ensure the dust collection ports on the CNC router are clear and connected to an efficient vacuum system.
- Softwoods: These woods produce lighter dust that can easily become airborne. Use a dust extraction system with fine filters to capture smaller particles and maintain a clean work environment.
- Exotic Woods: Some exotic woods produce fine, potentially hazardous dust. Use a dust extraction system with HEPA filters to ensure all fine particles are captured. Regularly check and replace filters to maintain optimal performance.
Maintain a clean workspace to prevent dust buildup, which can affect machine performance and pose health risks. Implement regular cleaning schedules and ensure that all workers use appropriate personal protective equipment (PPE), such as dust masks and safety glasses.
By paying close attention to tool precautions, fixing and clamping methods, and dust removal systems tailored to different types of wood, you can enhance the efficiency, safety, and quality of your CNC routing projects. These considerations are beneficial for achieving precise cuts, maintaining a clean working environment, and ensuring the longevity of both your tools and equipment.
Common Challenges and Troubleshooting in CNC Routing
CNC routing, while highly efficient and precise, can present several challenges. Understanding these challenges and knowing how to troubleshoot them can help ensure smooth operations and high-quality results. Here are some common issues and their solutions:
Chip Output
Inefficient chip removal can lead to tool clogging, reduced cutting efficiency, and poor surface finish. Troubleshooting should be carried out through the following strategies:
- Tool Selection: Use tools designed for optimal chip evacuation, such as up-cut bits, which pull chips upward and out of the cut.
- Feed Rate and Speed: Adjust the feed rate and spindle speed to ensure chips are effectively removed. Faster feed rates can help clear chips more efficiently.
- Dust Extraction: Implement a robust dust extraction system to continuously remove chips from the cutting area. Regularly check and maintain the system to ensure it operates effectively.
- Air Blowers: Use air blowers to help remove chips from the cutting path, keeping the work area clean and preventing chip re-cutting.
Tearing
Tear-out occurs when wood fibers are torn rather than cut cleanly, leading to rough edges and damaged surfaces. Troubleshooting should be carried out through the following strategies:
- Tool Selection: Use sharp, high-quality tools designed for the specific wood type. Down-cut bits can minimize tear-out on the top surface by pushing chips downward.
- Feed Rate and Speed: Adjust feed rates and spindle speeds to reduce the chance of tear-out. Slower speeds and feed rates can help achieve cleaner cuts in delicate or complex grain patterns.
- Support Material: Use sacrificial boards or masking tape to support the wood fibers and minimize tear-out. Applying a backing board can also help prevent tear-out on the underside.
- Cutting Direction: Where possible, cut with the grain rather than against it to reduce the likelihood of tear-out.
Burning
Burning occurs when excessive heat builds up during the cutting process, leading to scorched edges and discolored surfaces. Troubleshooting should be carried out through the following strategies:
- Sharp Tools: Ensure tools are sharp and in good condition. Dull tools generate more friction and heat, increasing the risk of burning.
- Feed Rate and Speed: Increase the feed rate or decrease the spindle speed to reduce the amount of time the tool spends in one spot, thus minimizing heat buildup.
- Cooling and Lubrication: Use air blowers or cooling systems to dissipate heat and keep the cutting area cool. In some cases, applying a light mist of lubricant can help reduce friction.
- Multiple Passes: Use multiple shallow passes instead of a single deep cut to distribute heat more evenly and reduce the risk of burning.
Vibration and Chatter
Excessive vibration during cutting can lead to inaccurate cuts, poor surface finish, and increased wear on tools and the machine. Chatter marks appear as wavy or uneven surfaces caused by these vibrations. Troubleshooting should be carried out through the following strategies:
- Secure Clamping: Ensure the wood is securely clamped to prevent movement. Use additional supports or a vacuum table for enhanced stability.
- Tool Selection: Choose the appropriate tool length and diameter for the cut. Longer tools are more prone to vibration, so use the shortest possible tool for the job.
- Feed Rate and Speed: Adjust the feed rate and spindle speed to find a balance that minimizes vibration. Often, reducing the speed slightly can help reduce chatter.
- Machine Maintenance: Regularly maintain and inspect the CNC router for any loose components or worn parts that could contribute to vibration. Ensure the machine operates on a stable and level surface.
- Cutting Strategy: Implement strategies such as climb milling (where the tool rotates in the direction of feed) to reduce the forces that cause vibration. Additionally, using multiple passes with shallow cuts can help maintain stability and reduce chatter.
By understanding these common issues and implementing effective troubleshooting strategies, you can enhance the performance of your CNC router, improve the quality of your finished products, and maintain a safe and efficient workspace. Regular maintenance, proper tool selection, and optimal machine settings are key to overcoming these challenges and achieving consistent, high-quality results.
Summarize
Understanding the properties of each wood type is beneficial for optimizing CNC router settings and achieving the desired outcome. By carefully considering these factors and adapting your CNC routing techniques accordingly, you can enhance both the aesthetic and functional aspects of your projects. Ultimately, the right wood selection not only improves the machining process but also ensures the longevity and beauty of your finished pieces. Whether you are a professional or a hobbyist, making informed choices about wood types will help you make the most of your CNC router’s capabilities and bring your creative visions to life.
At AccTek CNC, we manufacture professional CNC routers specifically designed for wood engraving and cutting. Our machines are built to deliver precision, efficiency, and versatility, catering to a wide range of woodworking needs. Whether you are working on intricate engravings, detailed carvings, or large-scale cutting projects, AccTek wood CNC routers provide the reliability and performance required to achieve exceptional results. Our commitment to quality ensures that our CNC routers are equipped with the latest technology, robust construction, and user-friendly features, making them the ideal choice for both professional woodworkers and hobbyists. Trust AccTek CNC routing solutions to enhance your woodworking projects.