- 12-17 Min Read
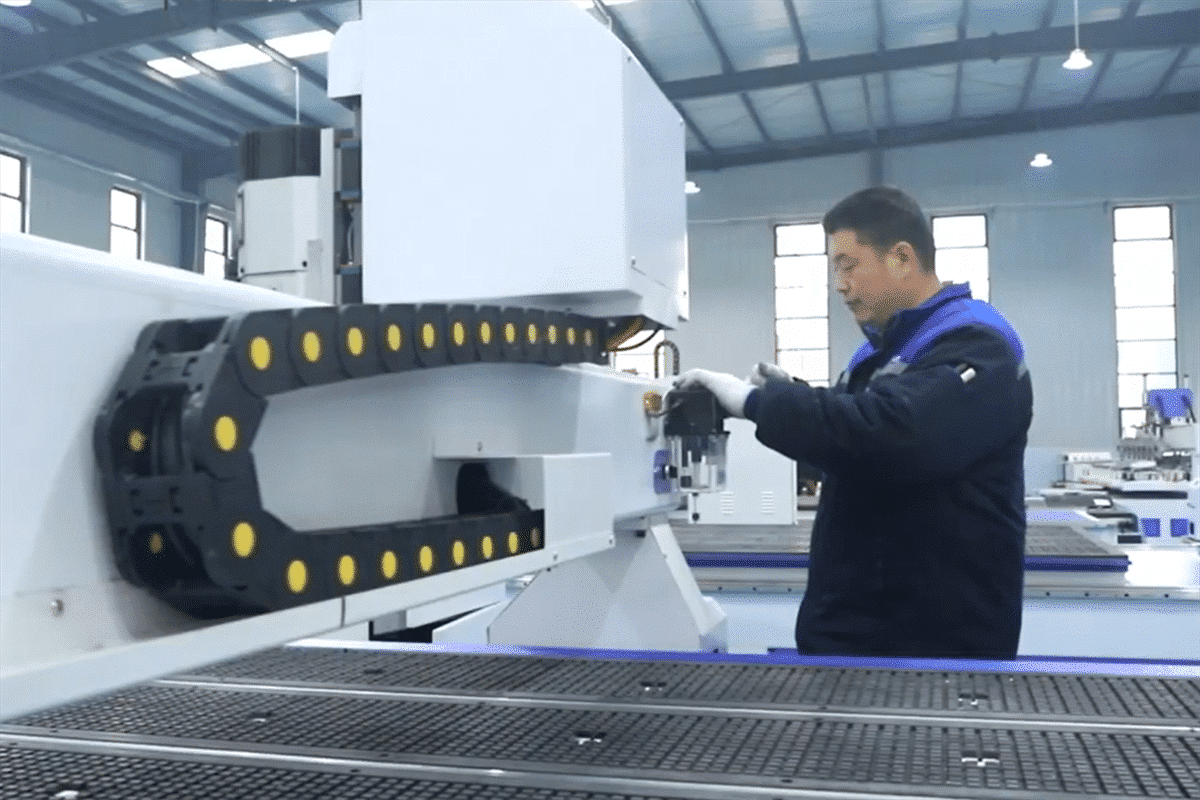
CNC routers are essential machines in modern manufacturing, known for their ability to deliver precise cuts and intricate designs across a wide range of materials. But like any complex equipment, CNC routers are prone to issues that can disrupt operations, delay projects, and lead to costly downtime. For professionals relying on consistent performance, these disruptions can be frustrating. Knowing how to identify and address common CNC router problems is a valuable skill that can save time and help maintain productivity.
This guide explores the most common CNC router problems, breaking down each issue with clear explanations and practical solutions. From mechanical failures to software glitches, understanding the root cause of these problems empowers users to make swift adjustments and avoid prolonged machine downtime. With the right troubleshooting steps, operators can ensure smoother workflows, minimize interruptions, and extend the lifespan of their CNC equipment. This guide is designed to support both beginners and seasoned professionals, providing insights to help maintain your CNC router in peak working condition.
Mechanical Problems
Mechanical problems in CNC routers are inevitable due to the high demands placed on these machines in manufacturing and fabrication environments. Key issues often arise from misalignment, rebound, and wear, each affecting the precision, quality, and efficiency of the work produced. This section will delve into each of these common mechanical problems, providing insights into how to diagnose and address them.
Misalignment
Misalignment occurs when the components of a CNC router, such as the spindle, cutting head, or linear guides, are not correctly aligned. This can lead to skewed or uneven cuts, reduced precision, and excess wear on the machine. Misalignment can happen due to heavy usage, accidental impacts, or gradual shifts over time, particularly in high-vibration environments.
- Example: A common misalignment issue is when the CNC router’s spindle is not perfectly square to the worktable, causing angled cuts. This becomes evident in projects requiring high precision, such as cabinetry or intricate metalwork, where even a small offset can result in visible errors and gaps in joints.
- Solution: To address misalignment, regularly check the machine’s alignment using a square, level, or specialized alignment tool. Adjust the spindle, guides, or cutting head as needed to restore proper alignment. Scheduling routine checks and calibrations can prevent misalignment from escalating and ensure that the CNC router continues to perform accurately.
Rebound
Rebound, or deflection, occurs when the router bit or tool head moves slightly out of position due to resistance from the material being cut. This can result in irregular cuts, chatter marks, or poor surface finishes, particularly when working with dense or hard materials. Rebound is often caused by excessive cutting force or improper feed rates.
- Example: If a CNC router is cutting through thick hardwood at a high speed, the bit may experience rebound, leading to uneven depths in the cut or noticeable vibration marks on the wood. This reduces the quality of the finished piece and can create inconsistencies in repetitive tasks.
- Solution: To prevent rebound, adjust the feed rate and spindle speed to match the material’s resistance level. Using a sharper, more rigid tool bit can also reduce deflection. Testing different settings on sample materials can help operators find the optimal balance, resulting in smoother, more accurate cuts.
Wear
Wear is inevitable over time as the moving parts of a CNC router, such as bearings, belts, and tool bits, endure repeated use. Worn components can decrease the machine’s performance, introduce inaccuracies, and increase the likelihood of other mechanical issues. Regular inspection and maintenance help to effectively manage wear and tear.
- Example: A frequently encountered wear issue is worn bearings in the CNC router’s spindle or guides. Worn bearings can lead to unwanted play or looseness, affecting the machine’s accuracy. This is especially problematic in projects requiring fine details or intricate designs, where even a slight reduction in precision is noticeable.
- Solution: Inspect key components for signs of wear and replace them when necessary. Bearings, belts, and tool bits should be routinely checked and replaced based on their usage and manufacturer recommendations. Establishing a maintenance schedule helps minimize the impact of wear, keeping the CNC router in peak operating condition and extending its lifespan.
Mechanical issues are among the most common problems CNC router operators face. Understanding and managing these mechanical challenges will enable CNC router users to get the most out of their equipment and achieve consistent, precise results.
Electrical Problems
Electrical problems in CNC routers are another common source of disruption that can lead to machine downtime, erratic performance, and potential safety hazards. Electrical problems can affect various aspects of the machine’s operation, from the control system’s responsiveness to the motor’s ability to drive movements accurately. This section will explore common electrical problems in CNC routers and provide practical solutions to keep the equipment functioning reliably.
Wiring Failure
Wiring failures in CNC routers can cause inconsistent power flow, signal disruptions, and even lead to system shutdowns. Over time, machine vibrations, environmental factors, or improper installation can cause wires to loosen, fray, or break, leading to connection issues. Wiring problems are often difficult to detect immediately but can create significant disruptions in machine performance.
- Example: One common wiring issue is a loose or disconnected ground wire, which can lead to static buildup and result in inaccurate cuts or abrupt machine stoppages. In more severe cases, wiring faults can cause a complete loss of communication between components, halting production until the issue is resolved.
- Solution: To prevent wiring failures, regularly inspect the machine’s wiring for signs of wear, loose connections, or damage. Secure loose wires with cable ties or clips, and replace damaged wires promptly. Scheduled maintenance checks can catch wiring issues early, preventing costly downtime and maintaining consistent machine performance.
Power Supply Problem
Power supply problems can arise from fluctuations, surges, or insufficient power delivery, affecting the CNC router’s stability and performance. An inconsistent or inadequate power supply can lead to machine malfunctions, erratic movement, or unexpected shutdowns, which disrupt production and can damage sensitive electronic components.
- Example: If the CNC router is connected to an unstable power source, power surges or brownouts can cause the control system to reset or lose calibration data, resulting in inaccurate cuts or misaligned parts. This issue is especially common in facilities where multiple machines are running on the same circuit, straining the available power supply.
- Solution: Using a stable power source, preferably with a surge protector or an uninterruptible power supply (UPS), can help prevent power-related problems. Regularly check the machine’s power connections, ensure circuits are not overloaded, and monitor for voltage fluctuations. These measures can safeguard the CNC router from power disturbances and enhance operational consistency.
Controller Failure
The controller is the central unit that interprets design instructions and directs the machine’s movements. A malfunctioning controller can cause errors in the cutting paths, loss of control over speed and position, and inconsistent quality in outputs. Controller issues are often linked to software bugs, hardware failures, or issues with the connection between the controller and other components.
- Example: A typical controller failure might manifest as delayed responses to input commands or incorrect execution of programmed paths, leading to off-course cuts. This can cause parts to be rendered unusable and increase material waste, particularly when working on complex designs or high-precision tasks.
- Solution: To address controller failures, ensure that the controller firmware and software are regularly updated. Check all connections between the controller and other components, and ensure they are secure. In cases where the controller itself is failing, consider a replacement or consult the manufacturer for repair options. Routine diagnostics and software checks can prevent many controller issues, keeping the CNC router running accurately and efficiently.
Electrical issues can significantly hinder CNC router performance and, if left unresolved, may lead to costly repairs. By performing routine inspections, ensuring proper grounding, and replacing faulty components, operators can mitigate these electrical challenges. Being vigilant about electrical maintenance not only helps maintain CNC router efficiency but also enhances safety and reduces the risk of unexpected machine failure.
Software and Programming Problems
Software and programming transform designs into precise cuts and complex shapes. However, errors in programming, software compatibility issues, and unexpected software failures can cause significant disruptions, resulting in inaccurate outputs, wasted materials, or even machine damage. This section explores common software and programming problems encountered with CNC routers, offering insights into how to identify and resolve them effectively.
Programming Errors
designs from CAD/CAM software.
- Example: A common programming error is setting an incorrect tool path, which can cause the CNC router to cut outside the intended area or in the wrong sequence. For instance, if the cutting depth is set too deep due to a programming error, it can overload the machine and damage both the tool and the material.
- Solution: To prevent programming errors, thoroughly review the code before running it on the CNC router. Using simulation features in CAM software can help detect and visualize errors before execution. Additionally, training operators on proper coding techniques and regularly reviewing program parameters can minimize the risk of programming mistakes.
Compatibility Issues
Compatibility issues occur when the software used to design or program the CNC router is not fully compatible with the machine’s control system. This can lead to partial or incorrect interpretations of commands, resulting in poor machine performance or errors during operation. Compatibility issues often arise when using software versions or file formats that are not supported by the machine’s controller.
- Example: If a CNC router’s control system only supports specific G-code formats, using an incompatible file format from CAD/CAM software can cause the machine to misinterpret instructions, leading to inaccurate cuts or a complete failure to execute the program.
- Solution: To avoid compatibility issues, ensure that all software used is compatible with the CNC router’s control system and is up to date. Consulting the machine’s documentation to verify compatible software and file formats can help prevent these problems. In some cases, software plugins or converters may be needed to bridge compatibility gaps between different systems.
Software Failures
Software failures are unexpected issues within the CNC router’s control software or CAD/CAM software that can cause it to freeze, crash, or fail to respond to commands. These failures may be due to software bugs, system overloads, or conflicts with other programs, disrupting operations and potentially compromising project quality.
- Example: A software failure might occur when the CAD software crashes mid-design or when the CNC control software freezes during a critical cutting operation, forcing the operator to restart and potentially lose progress. Frequent crashes can lead to material waste and delays in production schedules.
- Solution: To minimize software failures, keep all programs updated to the latest versions, as updates often include bug fixes and stability improvements. Running diagnostics, clearing unnecessary files, and ensuring the computer or controller is optimized can also prevent software crashes. For critical operations, performing a test run on simpler materials can help confirm stability before engaging in full-scale production.
By carefully reviewing programming codes, ensuring compatibility between software and control systems, and maintaining stable software environments, operators can minimize disruptions and optimize machine output. Proactive troubleshooting and regular software updates can prevent many common issues, reducing waste and enhancing productivity.
Material and Tooling Challenges
Material and tooling problems can lead to costly disruptions, compromised precision, and additional finishing work. This section describes common material and tooling challenges and offers practical solutions to overcome them.
Material Inconsistency
Material inconsistency is a common challenge in CNC routing, as variations in the composition, density, or thickness of materials can lead to unpredictable cutting results. These inconsistencies may cause changes in resistance or cutting behavior, making it difficult to achieve uniform quality across multiple pieces.
- Example: A piece of wood with varying grain density may produce an uneven surface finish or create resistance that affects the cutting path. This can lead to unexpected variations in depth, resulting in less precise or inconsistent cuts.
- Solution: To manage material inconsistencies, carefully select materials from reliable suppliers and, where possible, use materials with a more uniform composition. Adjusting feed rates and speeds can also help accommodate variations in density or texture, allowing the CNC router to handle inconsistencies more effectively. Conducting test cuts on sample pieces can also reveal any unexpected characteristics before full production begins.
Tool Wear
Tool wear is a natural consequence of prolonged use, where the cutting edges of bits and tools gradually lose sharpness. As tools wear down, they become less efficient, requiring more force to cut through materials and leading to poorer quality results. Tool wear can also increase the risk of overheating and stress on the CNC router, potentially reducing its overall lifespan.
- Example: CNC router bit becomes dull after repeated use on hardwood, resulting in frayed edges and a rough finish instead of clean cuts. This reduces the precision of the cuts and may require additional sanding or finishing, which increases production time.
- Solution: Regularly inspect and replace worn tools to maintain optimal cutting quality. Establishing a maintenance schedule based on usage intensity and the types of materials being cut can help anticipate tool wear and ensure tools are always in good condition. Using high-quality, durable tool bits also helps extend their lifespan, reducing downtime and improving consistency.
Tool Chipping or Breakage
Tool chipping or breakage occurs when the cutting tool experiences excessive force, improper feed rates, or is used on materials that exceed its specifications. This can lead to broken or chipped tool edges, rendering them unusable and potentially damaging the workpiece.
- Example: A common scenario is when a router bit chips or breaks while cutting dense materials at a high feed rate. The breakage may cause the CNC router to stop abruptly, leading to potential damage to the machine or the workpiece and creating downtime for repairs and tool replacement.
- Solution: Prevent tool breakage by choosing the appropriate tool for each material and carefully setting feed rates and speeds within recommended limits. Avoid overloading tools by selecting bits that match the hardness and density of the material, and use more robust tools for particularly challenging materials. Regular tool inspection and replacement, along with test cuts, can further reduce the risk of chipping or breakage, ensuring a safer and more efficient operation.
By understanding and addressing issues like material inconsistency, tool wear, and the risk of tool breakage, operators can maintain high-quality standards, reduce downtime, and extend tool life. With these best practices, CNC operators can tackle material and tooling challenges with confidence, optimizing productivity and ensuring precision in every project.
Environmental Factors
While CNC routers are designed to handle precise operations, fluctuations in environmental conditions can lead to material distortion, mechanical wear, and compromised output quality. This section will explore how temperature and humidity, along with dust and debris, impact CNC operations and offer practical strategies to mitigate these challenges.
Temperature and Humidity
Temperature and humidity can significantly impact CNC router performance and the materials being processed. Extreme temperatures can lead to thermal expansion or contraction of machine components, affecting precision and alignment. Similarly, high or fluctuating humidity levels can cause swelling or warping in certain materials and may lead to rust or corrosion of metal parts.
- Example: In a high-humidity environment, wooden workpieces can absorb moisture, causing them to expand and potentially altering the dimensions of cuts. This can lead to inaccuracies and necessitate additional finishing work to achieve the desired results. Excessive heat, on the other hand, may cause components in the CNC router’s control system or electronic circuits to overheat, leading to performance issues or damage.
- Solution: To mitigate the impact of temperature and humidity, maintain a controlled environment for CNC router operations whenever possible. Dehumidifiers, air conditioning, and proper insulation can help stabilize conditions. For sensitive materials, pre-conditioning or acclimating them to the shop’s environment can reduce the risk of expansion or warping. Regularly inspecting components for signs of rust, corrosion, or overheating is also beneficial to prolong the machine’s lifespan.
Dust and Debris
Dust and debris generated during CNC routing can pose serious challenges to machine performance and safety. Accumulation of dust and chips can obstruct moving parts, clog cooling systems, and contaminate sensitive electronic components. Excess dust can also reduce the machine’s precision, degrade the quality of cuts, and pose health risks to operators if not managed effectively.
- Example: When cutting wood, significant dust can build up around the CNC router’s moving parts, causing friction and potentially leading to misalignment or tool binding. Dust may also accumulate in cooling fans and filters, restricting airflow and causing components to overheat. In extreme cases, it can lead to motor failures or inaccuracies in cutting depth and path.
- Solution: Implementing effective dust collection systems, such as vacuum attachments or air filtration units, is beneficial to control dust and debris during machine operations. Regularly clean and maintain all areas around the CNC router, including fans, filters, and mechanical components, to prevent buildup. Establishing a cleaning schedule, wearing appropriate personal protective equipment (PPE), and ensuring proper ventilation can further minimize the impact of dust and debris on both the machine and operator safety.
With proactive measures in place, CNC router operators can create a stable work environment that optimizes productivity, prolongs equipment life, and delivers high-quality output across various projects.
Operator Error and Training
The performance and longevity of CNC routers are heavily influenced by the skill and knowledge of their operators. This section highlights the importance of proper training and careful operation to prevent costly errors and maximize the potential of CNC routers.
Improper Setup and Operation
Improper setup and operation of a CNC router by operators can lead to serious issues, including inaccurate cuts, machine damage, and even safety hazards. These errors often occur due to incorrect tool selection, improper calibration, or a lack of understanding of machine settings and capabilities. When a CNC router is not set up correctly, it can fail to produce consistent and precise results, leading to material waste and increased production costs.
- Example: An operator may inadvertently select an incorrect feed rate or spindle speed for a specific material, causing excessive vibration, poor surface finish, or tool breakage. Similarly, failing to properly secure the workpiece can lead to movement during cutting, resulting in imprecise cuts or even collisions with the tool.
- Solution: To minimize errors in setup and operation, operators should receive thorough training on CNC router operation, including understanding material requirements, tool selection, and software configurations. Clear, step-by-step setup procedures and access to documentation or support resources can help ensure consistency. Routine checks before starting a job, such as verifying tool paths and securing materials, further reduce the risk of mistakes.
Lack of Maintenance and Inspection
Regular maintenance and inspection are beneficial for keeping a CNC router in peak condition. A lack of these practices can lead to gradual wear of machine components, unexpected breakdowns, and decreased precision. Neglecting routine inspections can allow small issues, such as loose belts or worn bearings, to escalate into larger and costlier problems over time.
- Example: If an operator fails to inspect and lubricate moving parts regularly, friction may increase, leading to component wear and reduced machine efficiency. Neglecting to replace worn tools or clean dust buildup can also compromise the CNC router’s performance and affect product quality.
- Solution: Establishing a consistent maintenance and inspection schedule is beneficial for preventing problems caused by neglect. Operators should be trained to perform regular checks on critical machine components, including belts, bearings, and tools. Maintenance logs can help track completed tasks and identify recurring issues. Providing operators with the skills to recognize signs of wear or malfunction empowers them to take corrective action before more significant problems occur, improving both machine longevity and production quality.
Operator error and insufficient training can undermine the efficiency and reliability of CNC routers, but these challenges can be mitigated through comprehensive training and a proactive approach to maintenance. By investing in proper training and establishing routine maintenance protocols, businesses can reduce downtime, maintain precision, and maximize productivity in their CNC router operations.
Summarize
CNC routers are intricate machines that offer exceptional precision and versatility in various manufacturing processes. However, they are not without their challenges. Proactive maintenance, operator training, and regular inspections play a critical role in minimizing disruptions and maximizing productivity. By following this troubleshooting guide, operators can tackle issues with confidence, reduce downtime, and maintain high-quality output. A well-maintained CNC router not only boosts operational efficiency but also extends the machine’s lifespan, providing lasting value and reliability in every project.
AccTek CNC, as a well-known CNC router manufacturer in China, offers advanced and reliable CNC solutions designed to meet the diverse needs of industries worldwide. By equipping customers with the knowledge and tools they need, AccTek enables businesses to get the most out of their CNC equipment. Whether you’re a seasoned professional or new to CNC technology, AccTek CNC is a trusted partner dedicated to delivering exceptional performance, reliability, and productivity in every project.