- 14-20 Min Read
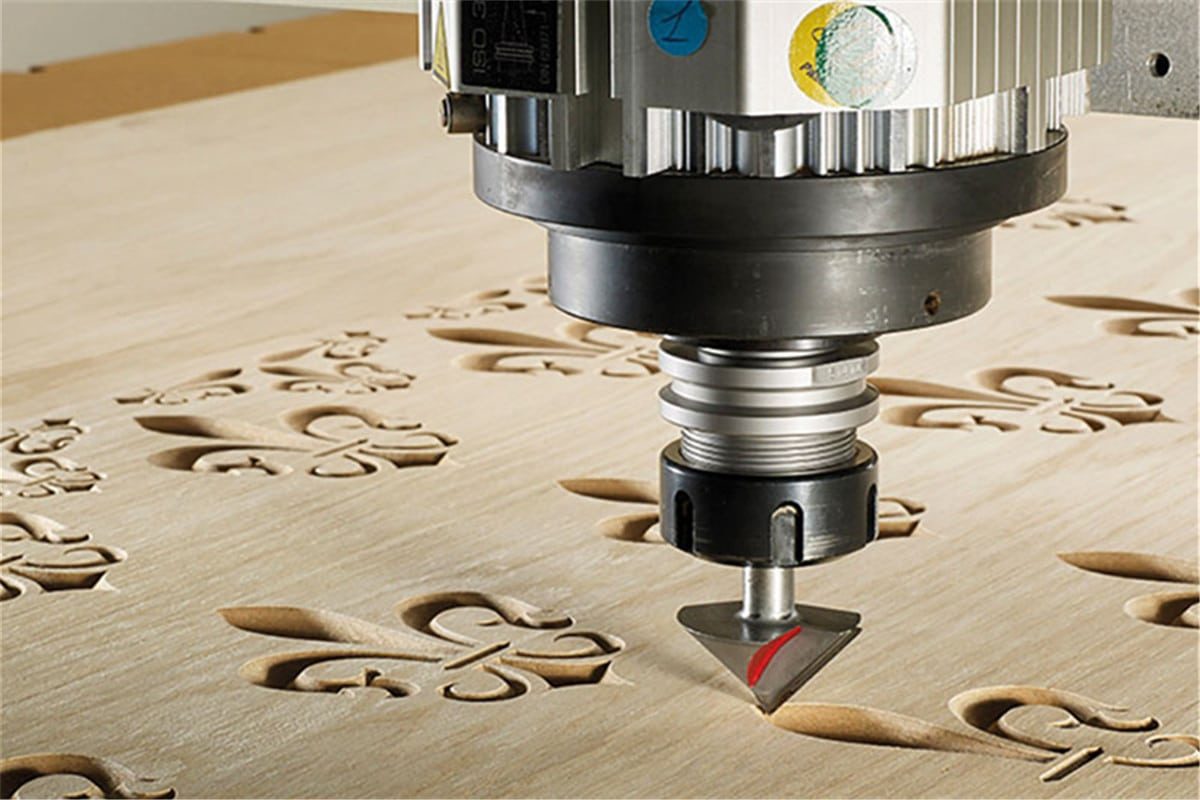
In the sophisticated domain of Computer Numerical Control (CNC) machining, the selection of tool materials emerges as a cornerstone that profoundly affects the machining process and final product quality. As CNC technology continues to revolutionize manufacturing across industries, the significance of choosing the right tool materials becomes increasingly pronounced. From wood to metals, plastics to composites, the intrinsic properties of both tool and workpiece materials intertwine to shape the outcome of machining endeavors.
This article embarks on a comprehensive exploration into the profound impact of CNC router tool material selection on the machining of diverse materials. Delving into the foundational understanding of tool materials, we elucidate the diverse types and functions, shedding light on their critical role in shaping machining processes. Through this in-depth analysis, manufacturers and CNC operators will gain valuable knowledge to make informed decisions about tool material selection, ultimately improving machining processes and achieving superior results across a variety of materials.
Types of tool materials and their properties
Each tool material possesses unique properties and is best suited for specific machining applications. A solid grasp of the basic types and functions of CNC router tool materials lays the foundation for making informed decisions in CNC machining. Here, we provide an overview of the essential types and functions of tool materials used in CNC machining.
High-Speed Steel (HSS)
High-speed steel (HSS) is a popular tool material known for its ability to maintain hardness at high temperatures. It is widely used in a variety of machining operations due to its toughness and versatility.
Characteristics
- Hardness: HSS maintains its hardness even at elevated temperatures, typically up to 600°C (1112°F), making it suitable for high-speed operations.
- Toughness: HSS is known for its toughness, allowing it to withstand significant stress and impact without fracturing. This toughness is particularly beneficiall in operations involving interrupted cuts or where shock loads are prevalent.
- Affordability: HSS tools are generally more affordable than carbide or ceramic tools, providing a cost-effective option for many machining applications.
- Ease of Sharpening: HSS tools can be easily sharpened and reconditioned, extending their usable life and making them a practical choice for many workshops.
Applications
- General Machining: HSS is commonly used for general-purpose machining of softer materials such as aluminum, brass, and plastics. Its toughness makes it suitable for operations involving complex shapes and intricate details.
- Drilling and Milling: HSS drills and end mills are widely used in both manual and CNC operations. They perform well in creating precise holes and milling contours in softer metals and non-metallic materials.
- Cutting Tools: HSS is frequently used for cutting tools like saw blades, reamers, taps, and broaches. These tools benefit from the material’s toughness and ability to retain sharp cutting edges.
- Woodworking: In woodworking, HSS tools are favored for their durability and ability to maintain sharpness, making them suitable for cutting and shaping various wood types.
- Thread Cutting: HSS taps and dies are used extensively for thread cutting due to their toughness and ability to produce clean, precise threads.
Precautions
- Heat Management: Excessive heat can degrade HSS tools. Adequate cooling and lubrication should be employed to prevent overheating and reduce tool wear.
- Proper Sharpening: Dull HSS tools can lead to poor surface finish and increased wear. Use appropriate sharpening techniques and equipment to ensure optimal tool performance.
- Material Compatibility: Avoid using HSS tools on very hard or abrasive materials. For such applications, carbide or ceramic tools may be more suitable. HSS is best suited for softer metals and non-metallic materials.
Carbide
Carbide tools are highly valued in machining for their extreme hardness and wear resistance. They are capable of operating at higher speeds and maintaining sharpness longer than HSS tools.
Characteristics
- Hardness: Carbide is one of the hardest tool materials available, which enables it to cut through tough materials with ease.
- Wear Resistance: The exceptional wear resistance of carbide extends tool life significantly compared to other materials like high-speed steel (HSS). This resistance reduces the frequency of tool changes and maintenance.
- Thermal Stability: Carbide can withstand high cutting temperatures, making it suitable for high-speed machining operations. This stability prevents tool deformation and maintains cutting precision.
- Rigidity: The rigidity of carbide tools ensures minimal deflection during cutting, which is beneficiall for maintaining tight tolerances and achieving high accuracy in machining operations.
Applications
- Metal Cutting: Carbide tools are widely used for cutting hard metals such as stainless steel, cast iron, and high-temperature alloys. They are preferred for operations like milling, turning, and drilling.
- High-Speed Machining: The ability to perform at high speeds makes carbide tools ideal for high-speed machining (HSM) applications, increasing productivity and efficiency in manufacturing processes.
- Tool and Die Making: The rigidity and durability of carbide make it a popular choice for tool and die making.
Precautions
- Proper Handling: Due to their hardness, carbide tools can be brittle and prone to chipping or breaking under improper handling. It is essential to handle them with care, avoiding any impact or sudden force.
- Appropriate Tool Holders: Use appropriate tool holders and clamping systems to secure carbide tools firmly. This minimizes vibrations and reduces the risk of tool breakage during machining operations.
- Coolant Use: Employ adequate cooling methods to manage the heat generated during high-speed machining. Proper use of coolants can extend the tool life and maintain the quality of the machined surface.
- Storage: Store carbide tools in a clean, dry environment to prevent corrosion and damage. Use protective cases or holders to keep the cutting edges intact and ready for use.
Ceramics
Ceramic tools are known for their exceptional hardness and heat resistance, making them suitable for high-speed machining of hard materials. They are less commonly used than HSS and carbide but are invaluable in specific applications.
Characteristics
- Heat Resistance: They can withstand very high temperatures without losing their hardness or strength, making them suitable for high-speed machining operations.
- Wear Resistance: Ceramics exhibit excellent wear resistance, especially in abrasive environments, ensuring a longer tool life compared to many other tool materials.
- Chemical Stability: Ceramic tools are chemically stable and resistant to oxidation, which prevents reactions with the workpiece material and extends tool life.
- Brittleness: Despite their hardness, ceramics are brittle and can fracture under heavy mechanical or thermal shocks. This brittleness requires careful handling and specific machining strategies.
Applications
- Hard Material Machining: They are particularly effective for machining hard and abrasive materials, including hardened steels, superalloys, and cast iron.
- Finishing Operations: Ceramic tools are frequently used in finishing operations where a high-quality surface finish is required. Their sharp edges and wear resistance help achieve smooth finishes.
- High-Temperature Applications: Ceramic tools are used in environments where high temperatures are encountered, such as in the aerospace and automotive industries.
- Dry Machining: Ceramics are suitable for dry machining processes, reducing the need for cutting fluids and associated costs.
Precautions
- Avoiding Mechanical Shock: Due to their brittleness, ceramic tools should be protected from mechanical shocks and sudden impacts. Gradual engagement with the workpiece and avoiding interrupted cuts can help mitigate fracture risks.
- Optimizing Cutting Conditions: Appropriate cutting speeds and feeds should be maintained to prevent excessive stress on the tool. High cutting speeds with low to moderate feeds are generally recommended.
- Tool Path Planning: Careful planning of tool paths can prevent sudden changes in cutting forces, which can cause tool breakage. Smooth and continuous cutting motions are preferred.
Diamond
Diamond tools are the hardest cutting tools available, offering unparalleled cutting performance and longevity. Diamond tools are invaluable in CNC machining applications requiring high precision and superior surface finishes.
Characteristics
- Unparalleled Hardness: Diamond is the hardest known natural material, providing exceptional cutting capabilities. This extreme hardness allows for precise and sharp cutting edges, resulting in superior machining performance.
- High Thermal Conductivity: Diamonds possess high thermal conductivity, allowing them to dissipate heat rapidly. This property minimizes thermal deformation and maintains cutting precision, even during high-speed operations.
- Excellent Surface Finish: Due to their sharp cutting edges and stability, diamond tools can achieve extremely fine surface finishes, making them ideal for applications requiring high precision and aesthetic quality.
Applications
- Non-Ferrous Metal Machining: Ideal for machining non-ferrous metals like aluminum, copper, and their alloys due to their non-reactive nature.
- Composites: Widely used in machining composite materials, such as carbon fiber-reinforced plastics (CFRP), due to their abrasiveness.
- Ceramic and Stone Machining: Ceramics, natural stones (such as granite and marble), and engineered stones.
Precautions
- Avoid Ferrous Materials: Diamond tools are not suitable for machining ferrous metals (like iron and steel) because carbon atoms in diamond can react with iron at high temperatures, leading to rapid tool wear and degradation.
- Handle with Care: Despite their hardness, diamond tools are brittle and can fracture under impact or excessive force. Handle them with care during installation and use to avoid chipping or breakage.
- Proper Storage: Store diamond tools in a clean, dry environment to prevent contamination and damage. Use protective covers or cases to shield the cutting edges when not in use.
Cubic Boron Nitride (CBN)
Cubic boron nitride (CBN) tools offer significant advantages in machining hard and abrasive materials, particularly ferrous metals. With their exceptional hardness, thermal stability, and wear resistance, CBN tools are indispensable in high-precision and high-performance machining applications.
Characteristics
- Exceptional Hardness: CBN is one of the hardest materials known, second only to diamond. This exceptional hardness makes it highly effective for cutting and grinding operations, particularly on hard and abrasive materials.
- Thermal Stability: Unlike diamond, CBN retains its hardness at high temperatures. This makes it ideal for high-speed machining where significant heat is generated.
- Chemical Inertness: CBN is chemically inert to iron-based materials, unlike diamond, which reacts with iron. This makes it particularly suitable for machining ferrous materials.
- High Thermal Conductivity: CBN has high thermal conductivity, which helps dissipate heat quickly from the cutting zone. This reduces the risk of thermal damage to the workpiece and extends tool life.
Applications
- Machining Hardened Steels: CBN is widely used for machining hardened steels (above 45 HRC) due to its ability to maintain sharpness and resist wear at high temperatures.
- Ferrous Materials: Effective for machining cast iron and other ferrous metals, especially in applications requiring high-speed cutting.
- Turning and Boring: CBN inserts are used for turning and boring operations on ferrous materials. They are especially useful for finishing operations where a high-quality surface finish is required.
- Cutting Superalloys: CBN tools are employed in the cutting of superalloys and other difficult-to-machine materials, often found in the aerospace and energy sectors.
Precautions
- Avoid Impact Loads: CBN is hard but relatively brittle. It can fracture under high impact loads, so it is important to avoid conditions that could cause sudden impacts or excessive tool pressure.
- Ensure Rigidity: The machining setup must be rigid to minimize vibrations and tool deflection, which can lead to tool breakage or poor surface finish.
- Appropriate Workpiece Materials: Best suited for ferrous materials, using CBN on non-ferrous materials is generally not recommended.
By understanding their characteristics, applications, and necessary precautions, manufacturers can effectively utilize these advanced tools to achieve superior machining results and operational efficiency.
The influence of tool materials on processing different materials
The material of a machining tool significantly affects its performance and the quality of the machining process. Different workpiece materials require specific tool materials to optimize efficiency, precision, and tool life. Here’s a detailed look at the impact of tool materials on machining these various materials:
Metals
Metals can be broadly classified into ferrous and non-ferrous materials, and each type requires specific tool materials for effective machining.
- High-Speed Steel (HSS): Commonly used for machining softer metals like aluminum, brass, and mild steel. HSS tools are durable and have good toughness but wear out quickly when machining harder materials.
- Carbide: Suitable for machining harder metals like stainless steel and titanium. Carbide tools maintain sharpness longer and can handle higher cutting speeds and feeds, reducing machining time.
- Ceramics: Used for high-speed machining of hard metals and cast iron. Ceramic tools can withstand high temperatures but are brittle and may chip or break under heavy loads or interrupted cuts.
- Cubic Boron Nitride (CBN): Ideal for super-hard metals and hardened steel. CBN tools provide excellent wear resistance and maintain dimensional accuracy over longer periods.
Diamond: Used for non-ferrous metals and non-metallic materials. Diamond tools offer the highest hardness and wear resistance but are expensive and can react chemically with iron.
Plastics
Machining plastics requires careful consideration due to their low melting points and tendency to deform.
- HSS: Suitable for softer plastics like polyethylene and PVC. HSS tools need to be sharp to avoid heat buildup and melting.
- Carbide: Used for harder plastics like polycarbonate and ABS. Carbide tools provide a sharper edge and longer life, reducing the risk of melting and achieving better surface finishes.
- Diamond: Polycrystalline diamond tools can be used for very hard plastics and composites. They offer superior wear resistance and produce the best surface finishes.
Wood
Wood machining benefits from tools that can handle the fibrous and often inconsistent nature of the material.
- HSS: Widely used for general wood machining due to its sharpness and toughness. HSS tools are good for softwoods and most hardwoods but may wear quickly with abrasive woods.
- Carbide: Ideal for harder woods and engineered wood products like MDF and plywood. Carbide tools maintain sharpness longer and can handle the abrasiveness of these materials.
- Diamond: Occasionally used for specialized wood machining, especially for high-precision applications or very abrasive woods. Diamond tools offer the longest life but are expensive.
Composites
Composites, such as carbon fiber-reinforced polymers (CFRP) and glass fiber-reinforced polymers (GFRP), are abrasive and pose unique challenges.
- Carbide: The most common tool material for composites. Carbide tools resist wear from the abrasive fibers and maintain sharp edges for longer periods.
- Diamond: PCD tools are increasingly used for composites due to their superior wear resistance and ability to produce clean cuts without delamination or fraying.
Ceramics
Ceramic materials are extremely hard and brittle, requiring tools that can handle their specific characteristics.
- Carbide: Suitable for some ceramic materials, especially in roughing operations. Carbide tools can handle the hardness but may wear quickly.
- Diamond: The preferred tool material for machining ceramics. Diamond tools provide the necessary hardness and wear resistance, allowing for precise and fine machining without excessive tool wear.
Understanding the specific requirements of the workpiece material ensures optimal tool selection and machining outcomes.
Factors affecting tool material selection
Selecting the appropriate tool material for machining is influenced by several factors that determine the efficiency, quality, and cost-effectiveness of the machining process. Here are the key factors:
Material Properties
- Hardness: Harder materials require harder and more wear-resistant tool materials like carbide or ceramics.
- Toughness: Materials prone to chipping or fracturing, such as brittle plastics or certain ceramics, might require tougher tool materials.
- Thermal Conductivity: Materials with high thermal conductivity may cause excessive heat buildup, necessitating tools with good thermal resistance.
- Abrasiveness: Abrasive materials like composites can wear down tools quickly, making diamond or carbide tools preferable.
Cutting Conditions
- Cutting Speed: Higher cutting speeds generate more heat, requiring tool materials that can withstand higher temperatures, like carbide or ceramics.
- Feed Rate and Depth of Cut: Aggressive cutting conditions with higher feed rates and deeper cuts demand tougher tool materials that can resist chipping and breakage.
- Type of Machining Operation: Different operations have varying demands. Finishing operations need high precision and smooth surfaces, favoring materials with excellent edge retention.
- Coolant Usage: The presence or absence of coolants affects heat dissipation and tool wear. Some tool materials perform better with specific coolants, enhancing their longevity and effectiveness.
Tool Life and Wear Resistance
- Durability: Tool materials with high wear resistance, like carbide or diamond, provide longer tool life, reducing downtime and tool change frequency.
- Edge Retention: The ability of the tool material to maintain a sharp cutting edge directly affects the quality of the machined surface and overall tool life.
- Coatings: Advanced coatings (e.g., TiN, TiAlN, diamond) can significantly enhance wear resistance, reduce friction, and improve thermal stability, thus extending tool life.
- Thermal Conductivity: Materials with good thermal conductivity (e.g., carbide) can dissipate heat more effectively, reducing thermal wear and prolonging tool life.
Cost Considerations
- Initial Tool Cost: The upfront cost of tool materials varies widely, with options like high-speed steel (HSS) being less expensive than carbide or diamond. The choice depends on the budget and specific machining needs.
- Tool Life and Replacement Frequency: While more expensive materials like carbide or diamond may have higher initial costs, their longer tool life and lower replacement frequency can justify the investment in high-production environments.
- Productivity: Higher-quality tool materials can increase machining speeds and feed rates, enhancing overall productivity and reducing machining time.
- Availability: The availability of specific tool materials and their compatibility with existing tooling systems and processes can impact the selection process.
By considering these factors, manufacturers can optimize tool material selection to enhance machining performance, reduce costs, and achieve desired outcomes for a wide range of workpiece materials and machining conditions.
Advances in tool material technology
Advances in tool material technology have significantly enhanced the performance, durability, and efficiency of machining processes. These innovations address various challenges associated with cutting harder, tougher, and more abrasive materials, as well as meeting the demands of high-speed and precision machining. Here are some notable advances in tool material technology:
Coated Tool Materials
Coated tool materials are conventional cutting tools (e.g., high-speed steel, carbide) that have been enhanced with a thin layer of coating material. This coating is designed to improve the tool’s performance by providing a harder, more wear-resistant surface, reducing friction, and increasing heat resistance.
Advantages
- Titanium Nitride (TiN): A widely used coating that provides a hard, wear-resistant layer. Increases tool life, reduces friction, and can be applied to various base materials.
- Titanium Carbonitride (TiCN): An improved version of TiN with the addition of carbon, resulting in a harder and more wear-resistant coating. Suitable for high-speed and high-feed machining, especially for harder materials.
- Titanium Aluminum Nitride (TiAlN) / Aluminum Titanium Nitride (AlTiN): These coatings have higher aluminum content, providing excellent oxidation resistance and hardness. Ideal for high-temperature applications, maintaining hardness and wear resistance under extreme conditions.
- Diamond-Like Carbon (DLC): A carbon-based coating that provides a very hard and low-friction surface. Excellent for non-ferrous materials, offering superior wear resistance and a smooth finish.
Disadvantages
- Cost: Coated tools are generally more expensive than uncoated tools due to the additional processing steps involved.
- Brittleness: Some coatings can be brittle and may chip or crack under heavy or impact loads.
- Adhesion Issues: Poor adhesion between the coating and the substrate can lead to delamination and failure of the coating.
- Limited Effectiveness on Soft Materials: Coatings may not provide significant benefits when machining softer materials where wear resistance is less critical.
Nanomaterials and Nanostructured Coatings
The incorporation of nanotechnology in tool materials has led to significant improvements in tool performance. Nanomaterials and nanostructured coatings provide exceptional hardness, wear resistance, and thermal stability due to their unique properties at the nanoscale.
Advantages
- Enhanced Wear Resistance: Nanostructured coatings have a high surface hardness, which significantly improves wear resistance, extending tool life.
- Improved Heat Dissipation: Nanomaterials can enhance thermal conductivity, allowing better heat dissipation and reducing thermal damage to the tool.
- Reduced Friction: Nanostructured surfaces often exhibit lower friction coefficients, reducing cutting forces and improving machining efficiency.
- Tailored Properties: The ability to engineer coatings at the nanoscale allows for the customization of properties to meet specific machining requirements.
Disadvantages
- Complex Manufacturing: The production of nanomaterials often involves sophisticated and costly manufacturing processes. The application of nanostructured coatings requires specialized equipment and expertise, which may not be readily available in all manufacturing environments.
- High Cost: The advanced techniques and materials used in creating nanostructured coatings result in higher costs compared to conventional coatings.
- Adhesion Challenges: Ensuring strong adhesion between the nanostructured coating and the substrate can be challenging, with the potential for delamination if not properly applied.
Advancements in coated tool materials and the development of nanomaterials and nanostructured coatings have revolutionized machining technology. Coated tools provide enhanced durability and performance, while nanotechnology offers unprecedented improvements in hardness, wear resistance, and thermal stability. These innovations enable more efficient and precise machining processes, catering to the evolving demands of modern manufacturing.
Maintenance and tool life optimization
Maintenance and tool life optimization are crucial aspects of CNC machining operations, directly impacting productivity, efficiency, and cost-effectiveness. Proper maintenance practices and optimization techniques help prolong tool life, reduce downtime, and ensure consistent machining performance. Here’s an overview of strategies for maintenance and tool life optimization:
Regular Maintenance
- Cleaning: Regularly clean tools and machinery to remove chips, debris, and coolant buildup. Use appropriate cleaning agents and methods to prevent corrosion and maintain tool integrity.
- Lubrication: Ensure proper lubrication of tool holders, spindle bearings, and other moving parts to minimize friction and wear. Use recommended lubricants and follow manufacturer guidelines.
- Tool Inspection: Periodically inspect tools for signs of wear, damage, or chipping. Replace worn or damaged tools promptly to prevent poor machining quality and potential damage to workpieces.
- Reconditioning: Regularly sharpen cutting edges to maintain optimal performance. Use the correct sharpening techniques and equipment for each tool material. For tools like drills and end mills, regrind worn sections to restore their geometry and cutting efficiency.
- Proper Storage: Store tools in a clean, dry environment to prevent rust and corrosion. Use protective coatings if necessary.
Cutting Parameters Optimization
- Speeds and Feeds: Optimize cutting speeds, feed rates, and depth of cut based on material properties, tool geometry, and machining conditions. Use cutting parameter optimization software or machining simulations to identify the most efficient parameters.
- Tool Path Optimization: Design tool paths that minimize unnecessary tool movements and reduce machining time. Use adaptive toolpath strategies and high-speed machining techniques to reduce cutting forces and extend tool life.
- Coolant Management: Use coolant effectively to dissipate heat and lubricate cutting edges. Adjust coolant flow rates, pressure, and nozzle positioning to optimize cooling and chip evacuation, reducing tool wear and improving surface finish.
Tool Life Monitoring
- Tool Wear Monitoring: Implement tool wear monitoring systems that use sensors to detect wear and predict tool life. This enables timely tool changes and reduces the risk of tool failure.
- Data Analysis: Analyze machining data to identify patterns and optimize tool usage. Use historical data to predict tool performance and plan maintenance schedules.
Tool Coating and Surface Treatments
- Coating Selection: Choose appropriate tool coatings (e.g., TiN, TiCN, TiAlN) to enhance tool wear resistance, lubricity, and thermal stability. Select coatings based on material compatibility, cutting conditions, and desired performance.
- Surface Treatments: Implement surface treatments such as nitriding, carbonitriding, or PVD/CVD coatings to improve tool hardness, wear resistance, and surface finish. Treat cutting edges and contact surfaces to reduce friction, adhesion, and tool wear.
Maintenance and tool life optimization are essential components of successful CNC machining operations. By implementing regular maintenance practices, optimizing cutting parameters, monitoring tool wear, utilizing advanced coatings and treatments, and fostering a culture of continuous improvement, manufacturers can maximize tool life, enhance machining efficiency, and achieve superior quality in their production processes.
Summarize
The influence of tool material selection on machining various materials is undeniable, as it directly impacts machining efficiency, tool longevity, and ultimately, the quality of the finished product. Each material presents unique challenges and requirements that demand careful consideration when selecting the appropriate tool material. By leveraging the latest technological advancements, manufacturers can optimize their machining processes, achieve higher productivity, and produce higher-quality products.
When it comes to CNC router solutions, AccTek CNC stands out as a trusted manufacturer renowned for delivering top-notch machines and comprehensive technical support. By choosing AccTek, you’re not just investing in a high-quality CNC router, you’re gaining access to a wealth of expertise and assistance to ensure optimal performance. From setup and installation to troubleshooting and maintenance, our team of experts is dedicated to guiding you every step of the way. Your success is our priority, and we’re here to support you every step of the journey.