- 12-16 Min Read
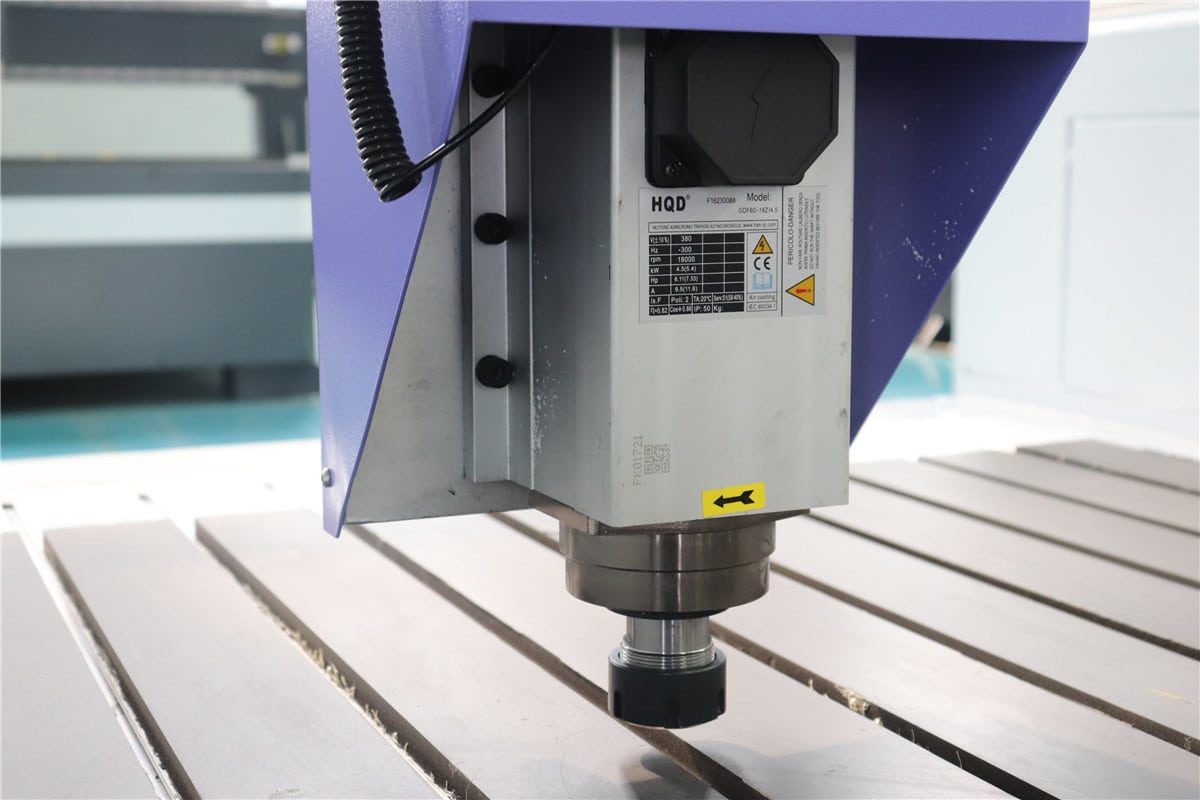
The spindle is the heart of any CNC router, dictating how effectively the machine can perform various cutting, carving, and shaping tasks. Spindle power influences everything from material compatibility to cutting speed and precision. Whether working with wood, metals, or plastics, the power of the spindle dictates how efficiently the CNC router can handle different materials. Machines with higher spindle power can make deeper and faster cuts, while those with lower power are typically more suited for delicate and intricate work. Understanding how spindle power impacts CNC router functionality is beneficial for optimizing both performance and productivity.
Selecting the right spindle power ensures long-term machine reliability and avoids potential problems such as tool wear or machine overload. A machine with insufficient spindle power may struggle to maintain accuracy or face frequent breakdowns when working with tougher materials. Conversely, choosing a CNC router with too much power for the intended application could result in higher energy costs and inefficient operation. This article will delve into how spindle power affects the overall functionality of CNC routers, helping users make informed decisions based on their specific production needs.
Understanding Spindle Power and Its Significance
Before discussing the impact of spindle power on the function of a CNC router, it is important to first understand what spindle power is and why it plays such a critical role in CNC operations. By understanding spindle power and its significance, we can better appreciate how it influences the overall functionality of CNC routers, guiding informed decisions in selecting and utilizing these machines.
Basic Knowledge of Spindle Power
Spindle power refers to the amount of mechanical energy that a CNC router’s spindle motor can transmit to the cutting tool, enabling the machine to carry out its cutting, carving, and shaping operations. It is typically measured in horsepower (HP) or kilowatts (kW). Spindle power is a key factor in determining how effectively a CNC router can remove material and the rate at which this can be achieved.
Spindle power works alongside spindle speed (measured in RPM) and torque, which define how forcefully the tool can interact with the material. High power is needed to cut through thick or hard materials, while lower power may suffice for more delicate operations. Understanding spindle power is essential for anyone working with CNC routers, as it defines the machine’s cutting capacity and performance under different workloads.
The Importance of Spindle Power
The importance of spindle power lies in its direct impact on the efficiency and versatility of the CNC router. A spindle with adequate power allows the machine to perform heavy-duty operations, such as cutting through thick or hard materials, without causing strain or significant tool wear. Machines with higher spindle power can operate at faster speeds, reducing production time and enhancing throughput. Conversely, if a router has insufficient spindle power for the task at hand, it may lead to overheating, reduced cutting quality, increased wear on tools, and even machine breakdowns. Therefore, selecting the correct spindle power ensures the machine operates efficiently and effectively for the intended application.
Relationship with Material Compatibility
Spindle power is closely tied to the materials that a CNC router can effectively work with. The power of the spindle dictates how well the machine can handle different materials based on their hardness, thickness, and density. For instance, working with dense and tough materials like metals or hardwoods requires a high-power spindle to ensure clean, precise cuts without causing damage to the machine or the cutting tools. In contrast, softer materials such as plastics, foam, or softwoods require less spindle power, as excessive power could result in overcutting or material distortion.
Ensuring compatibility between spindle power and material type will achieve the best results, whether the goal is fast production, intricate detail, or minimal material waste. Selecting the correct spindle power for the material at hand ensures the CNC router can operate efficiently and produce high-quality finishes across a wide variety of projects.
Evaluating cutting capabilities based on CNC router spindle power
The cutting capacity of a CNC router is significantly influenced by its spindle power. The spindle power determines how much material the machine can remove during a cut, which directly affects the types of materials you can cut, the depth of the cuts, and the speed at which you can work. Below is an evaluation of how spindle power relates to cutting capacity:
Cutting Speed and Feed Rate
Spindle power significantly influences the cutting speed and feed rate that a CNC router can achieve. Higher spindle power (e.g., 6 kW and above) allows the machine to maintain higher feed rates, which means the cutting tool can move faster through the material without causing excessive stress or loss of accuracy. This has advantages when working with dense or hard materials, as increased power ensures that the machine can handle fast-paced operations while maintaining precision.
In contrast, CNC routers with lower spindle power (e.g., 1-3 kW) limit the feed rate and cutting speed, making the machine better suited for lighter tasks and softer materials like plywood, MDF, or plastics. A machine with insufficient spindle power may experience chatter or inaccuracies if pushed to higher speeds, making power a critical factor in determining optimal cutting speeds.
Material Removal Rate
The material removal rate (MRR) is directly tied to spindle power. A higher-powered spindle enables the CNC router to remove more material in a shorter period, leading to a higher Material Removal Rate (MRR). With more power, the machine can take larger passes, meaning more material is removed with each cut. This leads to faster completion times, especially when working with hard or thick materials like metals and hardwoods.
In contrast, CNC routers with lower spindle power must take lighter passes to avoid overloading the spindle, resulting in a slower material removal rate and a longer process time. The right spindle power for the task helps achieve an optimal balance between speed and precision, minimizing the chances of tool failure or suboptimal cutting quality.
Cutting Depth and Tool Engagement
The cutting depth that a CNC router can handle also depends on spindle power. With greater spindle power, the CNC router can achieve deeper cuts per pass while maintaining precision. This allows the machine to handle tougher and thicker materials in fewer passes, reducing overall machining time. This also increases tool engagement, as more of the tool’s cutting edge interacts with the material during the process.
CNC routers with lower spindle power must reduce the cutting depth in a single pass to avoid stalling the spindle, leading to a need for multiple shallow passes. This may be fine for less demanding materials, but it slows down the overall process for harder materials. Matching spindle power to the cutting depth requirements ensures that the CNC router can operate smoothly without placing undue stress on the machine or tools.
Tool Compatibility
Spindle power also affects the range of cutting tools that a CNC router can effectively use. High-powered spindles can accommodate larger and more robust cutting tools, such as heavy-duty end mills or bits designed for cutting hard materials. These tools require more power to function properly and deliver precise results without causing excessive wear or damage.
Conversely, CNC routers with lower spindle power have a more limited tool selection because larger cutters and certain tooling types may cause strain on the spindle. Using a tool that exceeds the machine’s spindle power can result in poor performance, reduced tool life, and subpar cutting quality. Users may need to opt for smaller tools that take lighter cuts. Selecting tools that match the spindle power ensures optimal tool performance and longevity.
Spindle power is a crucial factor in evaluating a CNC router’s cutting capabilities. It affects cutting speed, material removal rate, cutting depth, and the types of tools that can be used, all of which play a role in the overall efficiency, accuracy, and versatility of the machine. Understanding and matching spindle power to these factors allows users to maximize the CNC router’s performance for various cutting applications.
Material Compatibility and Spindle Power Requirements
Spindle power is one of the key factors that determine a CNC router’s ability to handle different materials effectively. The power requirements for cutting or shaping a material vary based on its hardness, thickness, and overall composition. Understanding the relationship between material properties and spindle power ensures that the CNC router performs optimally and achieves the desired quality of cut without overloading the machine.
Wood and Plastic
Wood and plastic are commonly used materials in CNC routing, and they generally require moderate spindle power to ensure efficient cutting while maintaining precision. For softwoods like pine or spruce, and plastics such as acrylic or PVC, spindle power between 1 kW to 3 kW is typically sufficient.
Softwoods are easy to cut, and excessive spindle power could lead to splintering or rough edges. Plastics, especially softer variants, are prone to melting if the spindle power is too high, so moderate power helps achieve clean, precise cuts. Hardwoods, such as oak or mahogany, require slightly more power, typically between 3 kW to 4 kW, to handle the material’s density while still providing smooth finishes.
Metal
Metal cutting places significantly higher demands on spindle power due to the toughness and hardness of materials like aluminum, steel, brass, and copper. These materials require significant cutting force to penetrate their surfaces, and only a powerful spindle can provide the necessary torque and speed. Metals generally require high spindle power, starting at around 5 kW and going higher depending on the material’s thickness and hardness.
For example, aluminum may need around 5 kW, while cutting through thicker steel may require even more power to ensure proper tool engagement and material removal without damaging the cutting tools or the machine. Lower spindle power will result in slower cutting speeds, increased tool wear, and poor-quality finishes when working with metals, so the spindle power should be matched to the material.
Composites and Advanced Materials
Composites and advanced materials often require specialized spindle power due to their unique properties. These materials can be abrasive or difficult to cut cleanly, necessitating a combination of high spindle power and careful tool selection. Typically, spindle power between 4 kW to 6 kW is recommended for cutting composites, ensuring that the CNC router can handle the material’s density without causing excessive wear on tools. Proper spindle power ensures that the cutting process is smooth, with minimal chipping or cracking.
Other Materials
For materials outside the typical categories, such as foam, or rubber, spindle power requirements vary greatly depending on their flexibility and thickness. Softer materials like foam or rubber generally need low spindle power, often below 1 kW, as they are easily cut and too much power could cause tearing or deformation. Thin veneers also require minimal spindle power to maintain accuracy and prevent damage. These delicate materials benefit from precision routing, and too much power can lead to fraying, ripping, or burning. For these materials, careful control and low spindle power ensure smooth, precise cuts.
Material compatibility and spindle power requirements are closely linked. By selecting the appropriate spindle power for the material at hand based on the above information, operators can achieve the best balance between efficiency, accuracy, and tool longevity.
Balancing Spindle Power and Machine Stability
Balancing spindle power and machine stability is beneficial for optimizing CNC router performance, ensuring high-quality results, and prolonging machine and tool life. Higher spindle power can enhance cutting capabilities and production speed, but if the machine’s stability is inadequate, it can lead to excessive vibration, poor accuracy, and potential damage to both the router and the workpiece. Achieving the right balance requires considering the following factors:
Rigidity Requirements
The rigidity of a CNC router is fundamental to balancing spindle power. Rigidity refers to the machine’s ability to resist deformation, vibration, and movement during cutting operations. Higher spindle power introduces greater cutting forces, which the machine must absorb without bending or vibrating. To achieve balance, the machine’s frame, gantry, and linear guides must be sufficiently robust to handle the power and torque generated by the spindle.
If the machine is not rigid enough, even the best spindle power will result in deflections, poor cut quality, and imprecision. Therefore, to maintain performance, you need to ensure that the machine is built with high-quality, sturdy materials and components that can handle the loads created by higher spindle power. This includes reinforced frames, solid bases, and precision components designed to limit unwanted movement or flexing during operations.
Spindle-Tool-Workpiece Dynamics
The interaction between the spindle, tool, and workpiece also needs to be balanced to ensure stable cutting performance. As spindle power increases, the interaction between the cutting tool and the material becomes more intense, resulting in greater forces acting on the machine. These forces can lead to vibrations if the machine lacks sufficient rigidity, which negatively affects cutting accuracy and surface finish.
Additionally, the tool’s engagement with the workpiece needs to be optimized based on spindle power. A powerful spindle requires a tool capable of withstanding high cutting forces without excessive wear or breakage, while the workpiece must remain securely fixed in place to avoid movement during cutting. By ensuring proper alignment between spindle power, tool durability, and workpiece stability, the machine can maintain precision without introducing excessive stress into the system.
Overcoming Limitations
If there is an imbalance between spindle power and machine rigidity or stability, various methods can be applied to overcome these limitations. One approach is adjusting cutting parameters, such as reducing the feed rate or depth of cut, which minimizes the cutting forces and reduces the load on the machine. Another strategy is upgrading the machine with vibration dampening systems or improving the rigidity of specific components, such as adding reinforced gantries or stronger linear motion systems.
In cases where the machine cannot be easily upgraded, adaptive control systems can adjust spindle speeds and cutting paths in real time to compensate for vibrations or instability. These adjustments allow for the effective use of spindle power while minimizing the risks of tool wear, poor-quality cuts, or machine strain.
Balancing spindle power and machine stability requires understanding the rigidity requirements of the machine, managing the spindle-tool-workpiece dynamics, and overcoming potential limitations through adjustments and enhancements. By aligning these factors, the CNC router can operate smoothly and efficiently, achieving high-quality cutting results while maximizing the performance of both the spindle and the machine structure.
Choosing the Right Spindle Power for Your CNC Router Application
The spindle power determines the machine’s cutting speed, material compatibility, and overall efficiency, and choosing the right power level requires careful consideration of various factors. Below are the key aspects to consider when selecting the right spindle power for your CNC router application:
Application-Specific Requirements
When selecting the right spindle power for a CNC router, the first and most important consideration is the specific requirements of your application. Harder materials such as metals, hardwoods, and composites require more spindle power to cut effectively. For example, cutting metals like aluminum or steel typically requires a spindle power of 5 kW or more to ensure the machine can handle the material’s density without causing tool wear or overheating. In contrast, softer materials like plastics, foam, or softwoods require less power, often between 1 kW and 3 kW, to achieve precise, clean cuts without damaging the material.
Additionally, the complexity of the job also plays a role in determining the appropriate power level. Tasks such as 3D contouring, milling, or working with complex geometries often require more spindle power, as the CNC router needs to manage various cutting angles and forces across different planes. Simpler applications, such as basic cutting or engraving, may not require as much power, allowing you to opt for a more economical, lower-power spindle. Aligning spindle power with your specific application ensures optimal performance and precision.
Future Growth and Flexibility
While immediate application needs are a primary factor, it’s also important to consider potential future growth and flexibility. If your business is likely to expand into more demanding projects, investing in a CNC router with higher spindle power may future-proof your investment.
For example, if your current operations involve cutting soft materials, but you anticipate working with metals or composites in the future, selecting a spindle with more power than is currently needed (within reason) can offer the flexibility to take on more complex tasks down the line. Choosing a spindle that provides room for growth allows you to adapt to new opportunities without needing significant machine upgrades later.
Customization and Optimization
Customization is another key factor in selecting the right spindle power. Depending on your production needs, you may want a spindle that can be customized for specific applications. For instance, adjustable speed ranges or compatibility with specialized cutting tools can enhance the CNC router’s versatility.
Additionally, spindle power optimization ensures that you’re not overloading or underutilizing the spindle for the task at hand. Overpowered spindles can increase operational costs without adding significant benefits, while underpowered spindles may lead to inefficiencies and tool wear. Customizing your spindle setup based on power needs helps achieve the right balance between performance, precision, and energy efficiency.
Total Cost of Ownership (TCO) Analysis
Higher spindle power typically comes with increased upfront costs, higher energy consumption, and potential maintenance expenses. However, a more powerful spindle may also lead to greater productivity, faster cycle times, and the ability to handle a wider variety of materials, reducing overall costs in the long run.
Conducting a TCO analysis helps you weigh the initial investment against long-term benefits. Consider factors like energy efficiency, maintenance needs, tool life, and potential downtime when selecting the spindle power that provides the best return on investment. A well-chosen spindle power that aligns with your budget and operational goals will minimize unnecessary costs while maximizing productivity.
Choosing the right spindle power for your CNC router involves evaluating immediate application requirements, considering future flexibility, optimizing the spindle’s customization for efficiency, and performing a thorough TCO analysis. Balancing these factors ensures that you invest in a spindle that meets your current needs, accommodates growth, and provides long-term value.
Summarize
From influencing cutting speed, depth, and material compatibility to shaping the precision and efficiency of the machine, spindle power directly impacts how effectively a CNC router can handle various tasks. Choosing the right spindle power ensures that the machine can meet the demands of specific applications while balancing productivity, precision, and cost efficiency. Continue reading How to Choose CNC Router Spindle Correctly? You can get more effective suggestions.
AccTek CNC is a professional CNC router manufacturer in China, known for delivering high-quality machines that meet the needs of various industries. Our expertise in designing and producing CNC routers ensures that each machine is equipped with the right spindle power to maximize performance and efficiency. Whether you are cutting soft materials like wood and plastic or working with tough metals and composites, AccTek’s CNC routers offer the ideal balance of power, rigidity, and stability to handle any task with ease.