- 8-12 Min Read
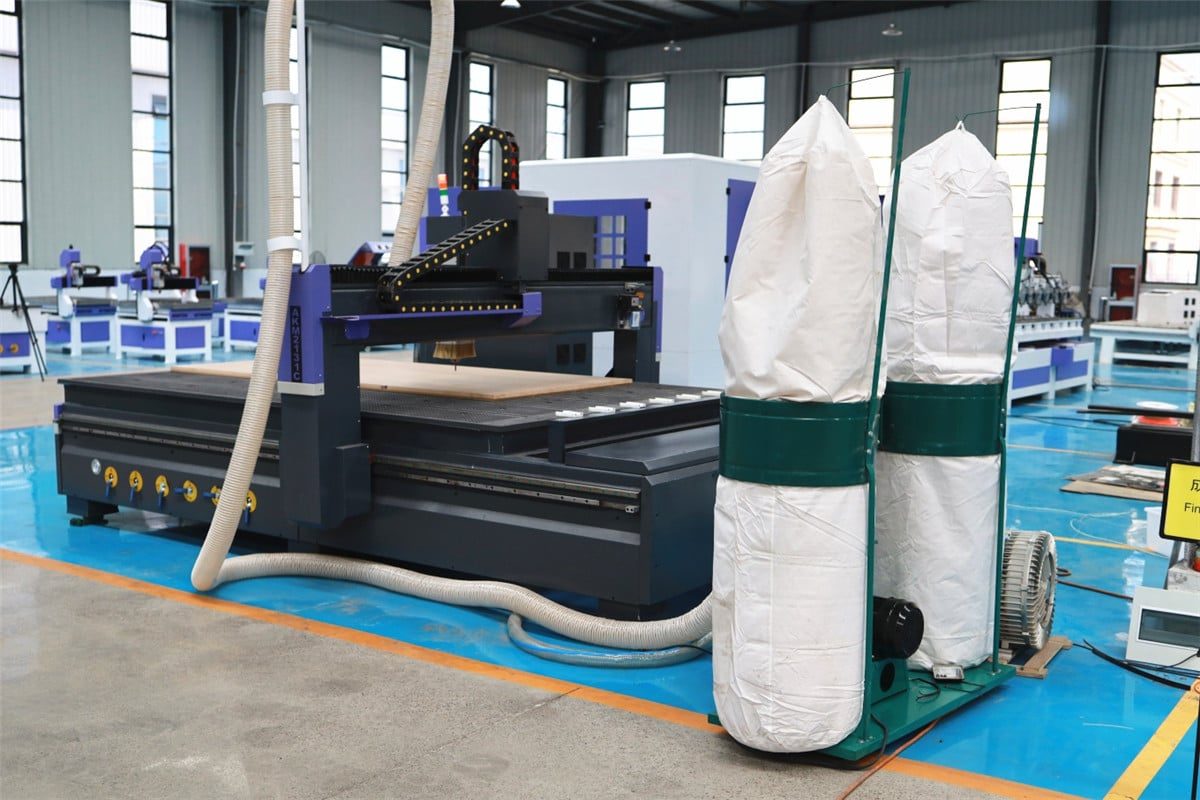
As CNC routers continue to revolutionize manufacturing processes across industries, ensuring proper ventilation and dust collection systems to maintain a productive and healthy workspace becomes an ongoing concern for users. The proliferation of fine particulate matter generated during CNC routing operations not only poses a threat to equipment longevity but also presents serious health risks to operators. Therefore, understanding the principles behind effective ventilation and dust extraction is necessary.
This comprehensive guide delves into the critical considerations for selecting an optimal ventilation and dust collection system tailored to your specific CNC router setup. We will explore the various types of systems available, their respective functions and applications, and essential factors such as workspace size, material types, and budget constraints. Whether you are setting up a small workshop or managing a large industrial operation, this guide aims to equip you with the knowledge needed to make informed decisions, ensuring a cleaner, healthier, and more efficient working environment.
Understand the risks of improper ventilation and dust collection
In any CNC machining environment, improper ventilation and dust collection can lead to a multitude of risks that affect both human health and operational efficiency. Understanding these risks is necessary for anyone involved in CNC routing, from hobbyists to industrial operators.
Health Risks
- Inhalation of Fine Particulates: CNC routers generate fine dust particles, which, when inhaled, can penetrate deep into the lungs, causing respiratory issues such as asthma, bronchitis, and other chronic respiratory conditions.
- Exposure to Hazardous Materials: Many materials processed by CNC routers, like certain types of wood, plastics, and composites, can release harmful chemicals or carcinogens into the air, increasing the risk of long-term health problems.
- Skin and Eye Irritations: Repeated exposure to certain wood dust or synthetic materials can trigger allergic reactions, leading to symptoms such as sneezing, runny nose, and skin rashes. Dust can cause skin irritations and eye discomfort, leading to decreased comfort and productivity among workers.
Operational Risks
- Equipment Malfunction and Reduced Lifespan: Dust can accumulate in the mechanical parts of CNC routers, leading to clogs and mechanical failures. This can result in increased downtime and higher maintenance costs. Poor ventilation can cause overheating of both the machinery and the dust collection system, potentially leading to equipment damage or even fire hazards.
- Decreased Productivity and Quality: Without proper dust collection, machinery requires more frequent cleaning and maintenance, which can significantly disrupt workflow and reduce overall productivity. Accumulated dust on the workpiece and in the workspace can interfere with the accuracy and precision of CNC operations, leading to subpar quality and increased waste.
Safety Risks
- Fire and Explosion Hazards: Certain types of dust, particularly from materials like wood, can be highly combustible. Inadequate dust collection can lead to the buildup of combustible dust, increasing the risk of fire and explosions.
- Slips and Falls: Dust settling on floors and surfaces can create slippery conditions, leading to a higher risk of slips, trips, and falls, which are common workplace accidents.
Regulatory and Legal Risks
- OSHA Violations: Failure to implement adequate ventilation and dust collection systems can result in non-compliance with OSHA standards and other regulatory requirements, leading to legal penalties, fines, and potential shutdowns.
- Worker Compensation Claims: Health issues and accidents caused by poor ventilation and dust collection can lead to increased worker compensation claims and higher insurance premiums.
Proper ventilation and dust collection are not merely optional upgrades but essential components of a safe and efficient CNC machining environment. Understanding the wide range of risks associated with improper systems highlights the importance of investing in high-quality, well-maintained ventilation and dust collection solutions.
Types of ventilation and dust collection systems
Selecting the appropriate ventilation and dust collection systems for CNC routers involves understanding the different types available and their respective features and applications. Here’s an overview of the most common types:
Local Exhaust Ventilation (LEV) Systems
LEV systems are designed to capture dust, fumes, and other airborne contaminants at their source before they can disperse into the workplace environment. This is particularly important for protecting workers’ health and maintaining a clean workspace. LEV systems work by creating a localized airflow that draws contaminants into a capture hood and then transports them through a series of ducts to a filtration unit where they are removed from the air. Here are its components and applications:
Components
- Capture Hood: Positioned close to the source of contaminants to capture them effectively.
- Ductwork: Connects the hood to the filtration system, transporting contaminants.
- Air Cleaning Device: Filters the air to remove contaminants. Common devices include cartridge filters, bag filters, or cyclones.
- Fan or Blower: This creates the necessary airflow to pull contaminants into the hood and through the system.
- Discharge System: Safely expels cleaned air back into the environment or outside the facility.
Applications
- CNC Routers: Capturing wood dust, plastic shavings, and metal particles directly at the cutting tool.
- Welding and Soldering Stations: Removing fumes and particulate matter generated during these processes.
- Chemical Processing: Capturing vapors and gases at the source.
Ambient Air Filtration Systems
Ambient air filtration systems aim to clean the overall air within a workspace, reducing the concentration of airborne contaminants that escape localized capture systems. They help improve overall air quality in the facility. These systems circulate the air within the workspace, passing it through filtration units that remove dust, fumes, and other contaminants before recirculating the clean air back into the room. Here are its components and applications:
Components
- Air Circulators/Fans: Move air through the filtration unit.
- Filtration Unit: Contains filters (HEPA, carbon, or electrostatic) that trap contaminants as air passes through.
- Pre-filters: Capture larger particles to extend the life of the main filters.
- Housing/Enclosure: Encases the system components and may include indicators for filter maintenance.
Applications
- General Workshop Air Quality: Ensuring clean air in woodworking shops, metalworking shops, and fabrication areas.
- Supplemental to LEV Systems: Providing additional air cleaning where LEV systems are in use but not sufficient on their own.
- Large Open Spaces: Warehouses and large workshops where contaminants can disperse widely.
Centralized Dust Collection Systems
Centralized dust collection systems are designed to handle large volumes of dust and debris from multiple sources or machines within a facility. They provide a comprehensive solution for dust management in large workshops and industrial settings. These systems use a network of ducts to collect dust from various points in the facility, transporting it to a central collection unit where it is filtered and either stored for disposal or expelled as clean air. Here are its components and applications:
Components
- Ductwork: Extensive network of pipes and ducts connecting multiple dust sources to the central collection unit.
- Collection Unit: Central unit housing the primary dust collection mechanism, such as a cyclone separator or baghouse.
- Filtration System: Includes various filters to capture fine dust particles.
- Fan or Blower: Provides the suction necessary to transport dust through the ductwork.
- Dust Storage: Containers or bins that collect and store dust for later disposal.
- Control System: Manages the operation of the entire system, often with automated features for filter cleaning and dust disposal.
Applications
- Large Manufacturing Facilities: Handling dust from multiple CNC machines, sanding stations, and other dust-generating equipment.
- Woodworking Shops: Centralized dust collection for saws, routers, planers, and sanders.
- Metalworking Shops: Collecting metal shavings and dust from cutting, grinding, and finishing operations.
Choosing the right system depends on the specific needs of your workspace. LEV systems are ideal for capturing contaminants at the source, ambient air filtration systems are best for overall air quality, and centralized dust collection systems are suited for managing large volumes of dust from multiple sources. Understanding the purpose, function, components, and applications of each system helps ensure a clean, safe, and efficient CNC machining environment.
Factors to consider when selecting a ventilation and dust collection system
Selecting the right ventilation and dust collection system for your CNC router setup involves a comprehensive understanding of various factors that can impact both the effectiveness and efficiency of the system. Here are the key factors to consider:
Machine-Specific Requirements
- CNC Router Size and Power: Consider the physical dimensions and power of your CNC router. Larger and higher-powered machines may require more robust ventilation and dust collection systems to adequately capture and remove contaminants generated during operation.
- Material Compatibility: Identify the materials processed by your CNC router, such as wood, metal, plastic, or composites. Different materials produce varying types and sizes of dust and may require specialized filtration systems to effectively capture contaminants.
- Dust Particle Size: Evaluate the particle size distribution of the dust generated by your CNC router. Fine particles, often less than 10 microns in diameter, can remain airborne for extended periods and pose respiratory health risks. Ensure the ventilation and dust collection system can effectively capture these fine particles.
Workshop Layout and Size
- Size of the Workspace: The physical size of your workshop significantly influences the design and selection of ventilation and dust collection systems. Larger spaces may necessitate more extensive ductwork and multiple capture points to effectively manage dust and fumes across the entire area.
- Machine Placement and Workflow: The arrangement of CNC machines and other dust-generating equipment affects how you plan the ductwork and position capture hoods. An optimized layout ensures efficient dust collection and minimizes airflow resistance, enhancing system performance.
- Ventilation Routes and Accessibility: Efficient routing of ductwork helps minimize pressure drops and maintain effective airflow. The accessibility of system components for maintenance and filter replacement also needs consideration to ensure the long-term functionality of the system.
Regulatory Compliance
- OSHA Standards: Adhere to OSHA’s permissible exposure limits (PELs) for airborne contaminants, which specify the maximum allowable concentrations of hazardous substances in the workplace air. Select a ventilation and dust collection system capable of maintaining airborne contaminant levels below these limits.
- Local Regulations: Ensure compliance with local regulations governing workplace safety and environmental protection. Local authorities may impose specific requirements regarding ventilation, dust collection, and air quality management in industrial settings.
Budget Considerations
- Initial Investment and Installation Costs: The upfront costs of purchasing and installing a ventilation and dust collection system can be significant. It’s important to consider these initial expenses in the context of your overall budget and long-term operational goals.
- Operating and Maintenance Expenses: Beyond the initial investment, ongoing costs such as energy consumption, filter replacements, and routine maintenance need to be factored into your budget. Systems that are energy-efficient and have low maintenance requirements can offer cost savings over time.
- Cost-Benefit Analysis: Conducting a cost-benefit analysis can help in evaluating the potential return on investment (ROI) of different systems. Consider how a well-chosen system can improve productivity, reduce equipment downtime, enhance worker health and safety, and ultimately contribute to operational efficiency.
Selecting the right ventilation and dust collection system for your CNC router involves careful consideration of the various factors listed above. By evaluating these factors comprehensively, you can implement an effective ventilation and dust collection solution that safeguards worker health, ensures regulatory compliance, and promotes a productive work environment.
Installation and maintenance best practices
Ensuring the effectiveness and longevity of your ventilation and dust collection systems requires careful attention to both installation and maintenance practices. Proper installation ensures optimal performance, while regular maintenance keeps the system running efficiently and safely. Here are the best practices to follow:
Professional Installation
- Consulting an Expert: Engage a certified industrial hygienist or a ventilation engineer to assess your specific needs and design a system tailored to your operations. Experts can provide insights into the latest technologies and system configurations that maximize efficiency and safety.
- Complying with Regulations: Obtain all necessary permits for your ventilation and dust collection systems. Stay informed about updates to OSHA and NFPA standards. Regularly review these standards to ensure your system remains compliant with the latest safety regulations.
Regular Maintenance
- Equipment Inspections: Establish a routine inspection schedule, typically monthly or quarterly, depending on the system’s usage and the environment. Use detailed checklists during inspections to ensure all components, including ducts, hoods, fans, and filters, are thoroughly examined.
- Filter Changes: Follow the manufacturer’s recommended schedule for filter changes. This typically involves replacing filters every few months or more frequently if operating conditions are severe. Use high-quality filters appropriate for the specific contaminants generated by your CNC operations.
- Ductwork Maintenance: Regularly clean the interior of ducts to prevent dust buildup, which can reduce airflow and increase the risk of fire. Check seals and connections for any leaks and repair them promptly to maintain system integrity.
- Fan and Motor Maintenance: Lubricate moving parts, check belt tensions, and inspect motors for overheating. Replace worn parts to prevent system downtime.
Implementing these installation and maintenance best practices ensures that your ventilation and dust collection systems operate efficiently and safely, protecting both workers and equipment. By following these guidelines, you can maintain a clean, safe, and compliant workspace.
Summarize
Selecting the right ventilation and dust collection system for your CNC router operations is a multifaceted endeavor that requires careful consideration of various factors. This comprehensive guide aims to provide you with the knowledge and insights necessary to make informed decisions, leading to improved air quality, enhanced worker safety, and increased operational efficiency. By implementing these best practices, you can create a healthier and more productive workspace, ultimately contributing to the success of your CNC operations.
For those seeking high-quality CNC routers with integrated dust removal solutions, we highly recommend considering AccTek CNC. AccTek CNC offers a range of 3-axis, 4-axis, and 5-axis CNC routers, each equipped with matching dust removal systems tailored to ensure optimal performance and maintain a clean, safe working environment. Their comprehensive approach to machine design and dust management makes them a reliable choice for both industrial and commercial applications.