- 8-12 Min Read
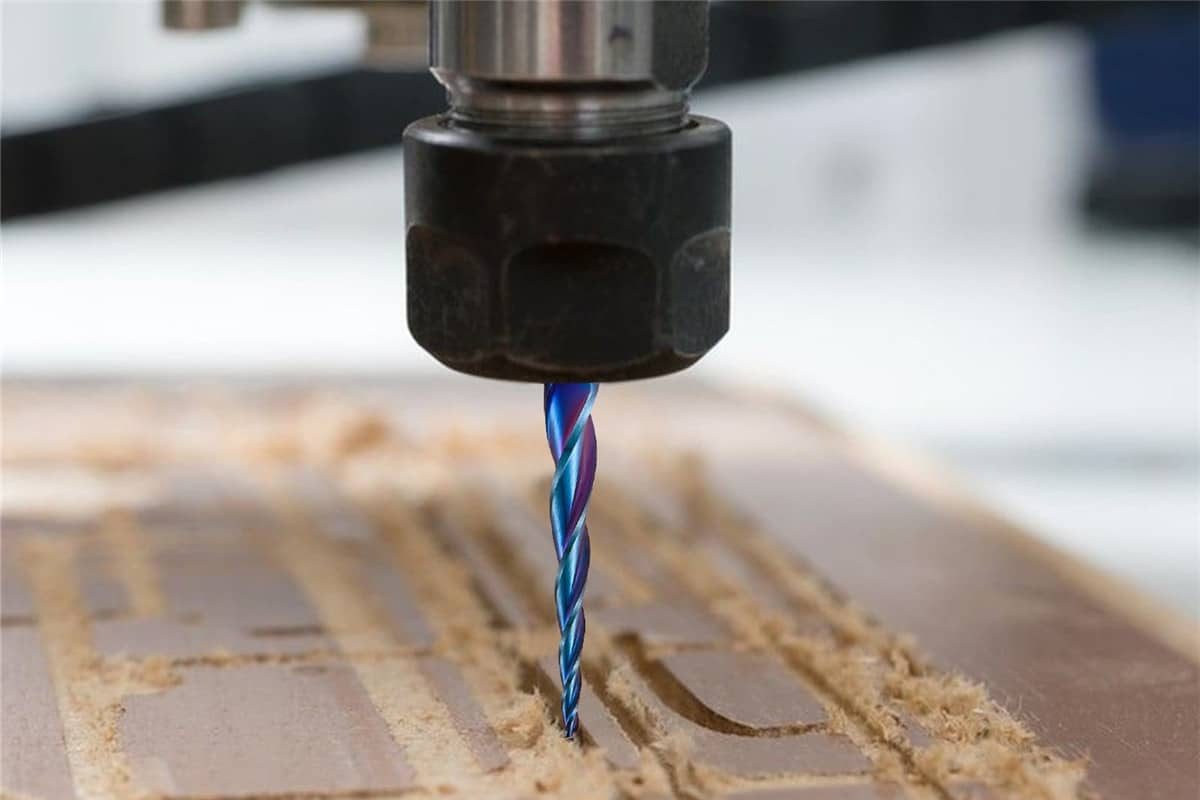
Selecting the right coatings for CNC router cutting tools is a critical decision that can greatly influence the efficiency, quality, and durability of your machining operations. As the demand for precision and longevity in CNC machining grows, understanding the various types of coatings available becomes necessary. These coatings not only protect the cutting tools from wear and tear but also enhance their performance by reducing friction and heat buildup.
This comprehensive guide delves into the properties, advantages, and applications of different coatings for CNC router cutting tools. From titanium nitride (TiN) to diamond-like carbon (DLC) coatings, each type offers unique characteristics that cater to specific machining needs. By understanding the various options and their specific advantages, manufacturers and machinists can make informed decisions that enhance productivity and extend the life of their tools. Whether you are a seasoned professional or new to the field, this guide provides valuable insights to help you choose the best coating for your CNC router cutting tools.
Importance of Cutting Tool Coatings
The use of appropriate coatings on cutting tools is a strategic decision in machining because they significantly impact tool performance, durability, and efficiency. Here are some key reasons why cutting tool coatings are important:
- Extended Tool Life: Coatings provide a protective barrier against wear and tear, which is especially important when working with hard materials or at high speeds. This protection helps extend the life of the tools, which leads to fewer tool changes and lower replacement costs.
- Improved Cutting Performance: Coatings can significantly improve the cutting performance of tools. They reduce the coefficient of friction between the cutting tool and the material being machined, resulting in smoother cutting operations. This improves cutting speeds, feed rates, and overall machining efficiency.
- Enhanced Heat Resistance: High temperatures are generated during machining processes. Coatings help dissipate heat more effectively, preventing thermal damage to the cutting tools and maintaining their structural integrity.
- Improved Surface Finish: Coated tools produce better surface finishes on machined parts. The reduced friction and improved cutting action minimize the formation of burrs and other surface imperfections.
- Reduced Adhesion and Built-Up Edge: Certain materials, like aluminum, tend to adhere to the cutting tool, causing a built-up edge that can affect the quality of the cut. Coatings reduce the likelihood of material adhesion, maintaining a sharp cutting edge.
- Corrosion Resistance: Certain coatings provide a barrier against environmental elements, including moisture and corrosive substances, which can degrade the tool material. This is particularly important in industries where the tools are exposed to aggressive working environments.
- Versatility Across Materials: Different coatings are designed to handle various materials, from hard metals to softer plastics. This versatility allows manufacturers to select the most suitable coating for their specific machining needs.
- Reduced Production Costs: By enhancing tool life and performance, coatings help lower production downtime and maintenance costs. Longer tool life means fewer stops for tool changes, leading to higher productivity.
Common coating types for CNC router tools
Each of these coatings has unique properties that make them suitable for specific materials and machining conditions. Here are the common coating types for CNC router tools:
Titanium Nitride (TiN) Coating
- Performance: TiN is recognized for its golden hue, excellent hardness (around 2300 HV), and thermal stability up to 600° It reduces friction and increases lubricity during cutting operations.
- Advantages: By providing a smooth, lubricious surface, TiN reduces friction and improves cutting efficiency, extending tool life and enhancing performance. It minimizes gallery and seizure and improves cutting speeds and feed rates.
- Applications: Widely used for a range of cutting tools like drills, mills, and taps, particularly effective in machining carbon steels, alloy steels, and stainless steels.
Titanium Carbonitride (TiCN) Coating
- Performance: TiCN offers higher hardness (3000 HV) compared to TiN and provides excellent wear resistance due to the addition of carbon.
- Advantages: TiCN coating stands out with its higher hardness and superior wear resistance, particularly in abrasive environments. The addition of carbon enhances its performance, allowing for greater resistance to abrasive wear and a lower friction coefficient. This makes TiCN ideal for machining high-alloy materials.
- Applications: Ideal for tougher machining operations involving high-alloy steels, tool steels, and cast iron. It’s particularly effective in applications requiring additional wear resistance, such as forming and punching tools.
Titanium Aluminum Nitride (TiAlN) Coating
- Performance: TiAlN exhibits excellent thermal stability, supporting temperatures up to 800° It features a high hardness level (around 2800 HV) and enhances productivity under high heat conditions.
- Advantages: TiAlN coating is highly valued for its exceptional thermal stability and resistance to oxidation, making it suitable for high-speed and high-temperature applications. Its ability to maintain hardness at elevated temperatures significantly reduces thermal load on the cutting edge, enhancing tool life and productivity.
- Applications: Suited for cutting hard and abrasive materials like titanium and high-temperature alloys. Commonly used in high-speed machining and when machining without coolant (dry machining).
Aluminum Titanium Nitride (AlTiN) Coating
- Performance: AlTiN provides superior thermal stability and can withstand temperatures up to 900° It is extremely hard (up to 3500 HV), making it ideal for high-performance applications.
- Advantages: AlTiN coating provides superior performance in high-heat machining environments due to its exceptional thermal stability and high hardness. It excels in applications involving high-speed tooling, offering excellent wear resistance and prolonged tool life under extreme conditions.
- Applications: Perfect for high-speed machining of titanium alloys, hardened steels, and nickel-based alloys. Frequently used in applications where excessive heat is generated, such as drilling and milling operations.
Diamond-Like Carbon (DLC) Coating
- Performance: DLC features an extremely low friction coefficient and superior hardness (up to 5000 HV), offering excellent wear resistance and smooth operation.
- Advantages: DLC coating is renowned for its extremely low friction coefficient and outstanding hardness, making it ideal for applications requiring minimal adhesive wear and high surface smoothness. Its ability to significantly reduce friction and maintain sharp cutting edges enhances tool life and performance.
- Applications: Particularly beneficiall for machining aluminum, brass, and other non-ferrous materials. Also used in automotive components, plastic molds, and precision engineering due to its ability to maintain sharp edges and clean surfaces.
Each of these coatings offers unique properties tailored to specific machining needs. Selecting the right coating for your CNC router tools can significantly improve cutting performance, extend tool life, and enhance the quality of the finished product.
Coating Application Technology
Coating application technologies are methods used to deposit thin films of materials onto the surfaces of cutting tools to enhance their properties, such as hardness, wear resistance, and thermal stability. Here are two key coating application technologies:
Physical Vapor Deposition (PVD)
PVD is a process that involves the physical transfer of material from a source to a substrate in a vacuum environment. Common techniques include evaporation, sputtering, and arc deposition. The process typically requires a high vacuum chamber where the coating material is vaporized and then deposited onto the substrate to form a thin film.
Advantages
- High Purity and Density: PVD coatings are often pure and dense, leading to high-quality finishes.
- Controlled Thickness and Composition: The process allows for precise control over the coating’s thickness and composition.
- Adhesion: PVD coatings adhere well to the substrate, enhancing durability.
- Environmental Safety: PVD processes generally produce less hazardous waste compared to other methods.
Limitations
- Line-of-Sight Deposition: The technique primarily coats surfaces that are directly exposed to the vapor stream, making it challenging to coat complex geometries uniformly.
- High Equipment Cost: The initial setup and maintenance costs for PVD equipment can be high.
- Vacuum Requirement: The need for a high-vacuum environment can limit the size of components that can be coated and increase processing time.
Chemical Vapor Deposition (CVD)
CVD involves chemical reactions between gaseous precursors and the substrate surface at high temperatures, leading to the formation of a solid coating. The process occurs in a controlled atmosphere, where the gases react or decompose on the substrate surface to form the desired coating.
Advantages
- Uniform Coatings: CVD can produce very uniform and adherent coatings, even on complex shapes and large areas.
- High Deposition Rates: The process can achieve high deposition rates, making it efficient for industrial applications.
- Material Versatility: CVD can deposit a wide range of materials, including metals, ceramics, and composites.
- Surface Coverage: It allows for coating intricate geometries and internal surfaces due to the nature of gas phase reactions.
Limitations
- High Processing Temperatures: The high temperatures required can limit the use of CVD on temperature-sensitive substrates.
- Hazardous Precursors: Some CVD processes involve toxic or hazardous precursors, necessitating careful handling and disposal.
- Complexity: The process setup can be complex and require precise control over reaction conditions.
Comparison of PVD and CVD
- Deposition Mechanism: PVD involves the physical transfer of material in a vacuum environment, typically through evaporation or sputtering. CVD relies on chemical reactions between gaseous precursors and the substrate surface at high temperatures.
- Coating Uniformity: PVD generally produces coatings with good adhesion but is limited by line-of-sight deposition, making it less effective for complex geometries. CVD provides excellent uniformity and can coat complex shapes and internal surfaces due to gas phase reactions.
- Temperature Requirements: PVD operates at lower temperatures compared to CVD, making it suitable for temperature-sensitive substrates. CVD requires high temperatures, which can limit the materials that can be coated without damage.
- Material Range: PVD is effective for a range of materials including metals and ceramics, but is generally not as versatile as CVD. CVD is capable of depositing a wide variety of materials, including metals, ceramics, and composite coatings.
- Environmental and Safety Concerns: PVD is typically safer and produces less hazardous waste. CVD may involve hazardous precursors and requires careful handling and disposal.
PVD and CVD are both valuable coating technologies with distinct mechanisms, advantages, and limitations. PVD is favored for its purity, adhesion, and environmental safety, while CVD excels in coating uniformity and versatility but requires higher processing temperatures and careful handling of hazardous materials. The choice between the two depends on the specific application requirements, including the type of substrate, desired coating properties, and cost considerations.
Factors Affecting Coating Selection
When selecting coatings for CNC router tools, several key factors need to be considered to ensure optimal performance and durability. Here’s a detailed look at the factors affecting the selection in terms:
Material Compatibility
The type of material being machined significantly influences the choice of coating. Different coatings perform better with specific materials.
- Hard Materials: For hard materials like stainless steel, titanium, and high-alloy steels, coatings such as TiAlN and AlTiN are preferred due to their high hardness and wear resistance.
- Soft Materials: For softer materials like aluminum and plastics, coatings like DLC are ideal as they provide low friction and prevent material adhesion.
- Abrasive Materials: Materials like composites and ceramics require coatings with extreme hardness and wear resistance, such as PCD (Polycrystalline Diamond).
Processing Conditions
The specific conditions under which the CNC router operates, including cutting speed, feed rate, and the use of coolant, affect coating selection.
- High-Speed Machining: Requires coatings that can withstand high temperatures and reduce friction, such as TiAlN or AlTiN.
- Dry Machining: For operations without coolant, coatings with excellent thermal stability and oxidation resistance, like TiAlN, are ideal choices.
- Wet Machining: When coolant is used, coatings that can handle thermal cycling without degradation, such as TiCN, are advantageous.
Tool Substrate Material
The material of the tool substrate must be compatible with the coating to ensure proper adhesion and performance.
- Carbide Substrates: Common in CNC tools, carbide works well with coatings like TiN, TiCN, and TiAlN, which enhance hardness and wear resistance.
- High-Speed Steel (HSS): HSS tools benefit from coatings like TiN and TiCN, which improve wear resistance and cutting performance without compromising the toughness of the substrate.
- Cermet Substrates: These composite materials often use coatings like TiAlN to maximize the benefits of both the ceramic and metallic components.
Temperature and Wear Resistance
The ability of the coating to withstand high temperatures and resist wear is key for tool performance and longevity.
- Temperature Resistance: Coatings such as TiAlN and AlTiN are designed to maintain hardness and performance at elevated temperatures, making them suitable for high-speed and high-temperature machining operations.
- Heat Dissipation: Effective heat dissipation is beneficiall to prevent tool deformation and prolong tool life. Coatings with high thermal conductivity, like TiCN, help manage heat more effectively.
- Wear Resistance: The resistance of the coating to abrasive wear, adhesive wear, and erosion during machining. For materials that cause significant abrasion, such as cast iron or hard steels, coatings like TiCN and TiAlN provide excellent wear resistance. DLC coatings, which offer low friction and prevent material buildup, are ideal for reducing adhesive wear when machining sticky materials like aluminum.
By carefully considering these factors, manufacturers and machinists can select the most appropriate coating for their specific needs, ensuring optimal performance, durability, and cost-effectiveness in their machining operations.
Summarize
In the ever-evolving world of CNC machining, the selection of appropriate cutting tool coatings plays a pivotal role in enhancing the performance, efficiency, and longevity of tools. Understanding the properties and applications of these coatings allows machinists to make informed decisions, ultimately leading to improved productivity, reduced tool costs, and higher quality finishes on machined parts. As technology advances, staying abreast of the latest developments in coating technologies will ensure that manufacturers continue to maintain a competitive edge in their respective industries. With the right coating selection, CNC router tools can perform at their peak, delivering exceptional results in even the most demanding machining environments. In addition, if you want to know more about router bits, you can continue reading the “CNC Router Bits: Complete Buyer’s Guide“.
AccTek CNC is a professional CNC router manufacturer that provides different models of machines to meet different manufacturing needs. For businesses looking to optimize production efficiency and achieve exceptional machining results, AccTek CNC stands ready to provide reliable, cutting-edge CNC router solutions that empower manufacturers to excel in today’s competitive market.