- 10-15 Min Read
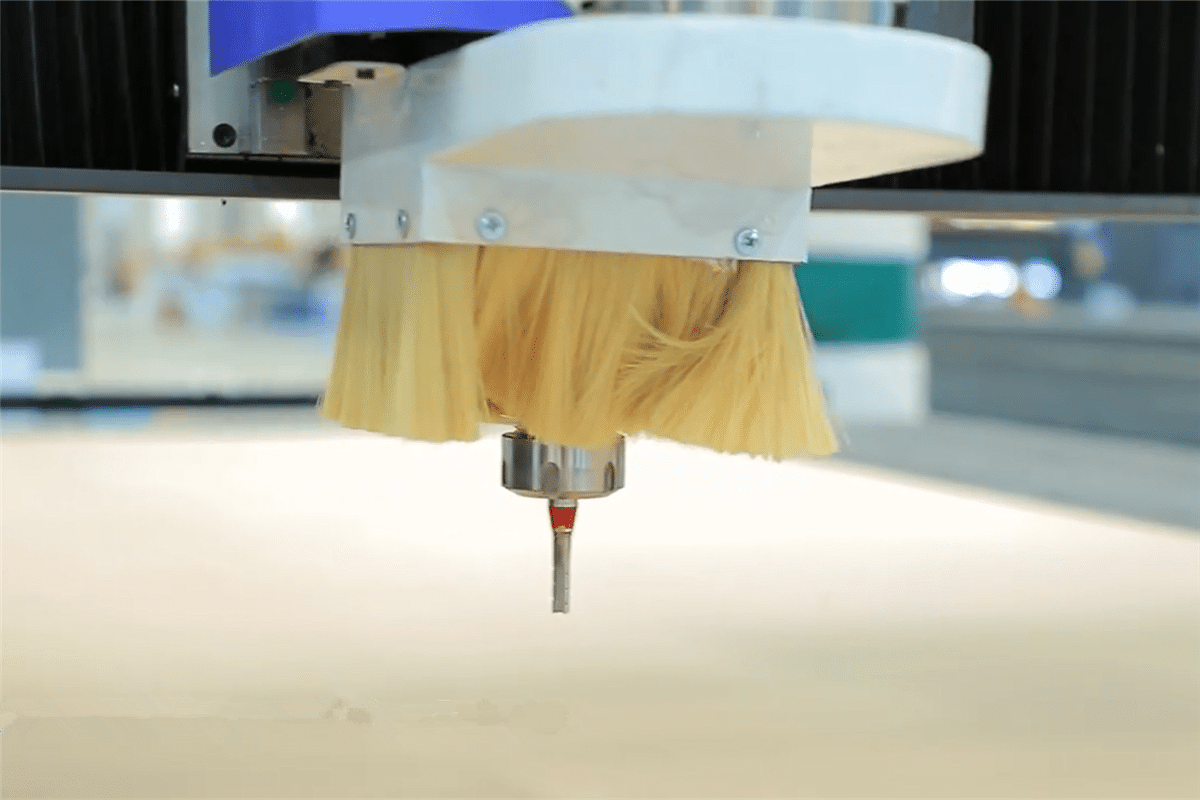
CNC routers have become indispensable tools in modern manufacturing, allowing for precision and efficiency in cutting, carving, and shaping a wide range of materials. However, like all mechanical components, CNC router bits wear down over time, affecting both the quality of cuts and the overall performance of the machine. By recognizing the conditions that affect a router bit’s lifespan, operators can make informed decisions on tool usage, maintenance, and replacement strategies.
In this article, we will explore the key elements that determine the longevity of CNC router bits, including the material being cut, cutting parameters, and the type of material from which the bit is made. Additionally, we will examine best practices for monitoring bit wear and knowing when it’s time for a replacement to ensure the continued success of your CNC routing operations. By exploring these factors, this article provides insights into how to maximize tool life, minimize costs, and ensure optimal performance in CNC routing operations.
Basic knowledge of router bit lifespan
The lifespan of a router bit refers to the amount of time or number of operations a router bit can perform before it begins to lose its cutting effectiveness or becomes worn to the point where it requires replacement or sharpening. The service life of the bit directly affects various aspects of manufacturing, including efficiency, cost-effectiveness, and product quality. Here’s a breakdown of its significance:
- Reduced Downtime: A longer lifespan for router bits means fewer replacements. This reduces machine downtime, which is beneficial for keeping production lines running smoothly. A shorter tool life may necessitate more frequent tool changes, causing interruptions and slowing down production.
- Cost Efficiency: Frequent replacement of router bits incurs significant costs, not only for the bits themselves but also for labor involved in changing tools, disposal of worn-out bits, and potential delays. Extending the service life of CNC router bits reduces these additional costs, making production more cost-effective over time.
- Improved Cutting Quality: As CNC router bits wear down, they lose their sharpness and cutting precision. A worn-out tool may cause issues such as poor cut quality, rough edges, or inconsistent depths, which can affect the final product. Ensuring that tools have a longer service life helps maintain the quality of cuts throughout the production cycle.
- Consistency in Production: CNC router bits with a longer lifespan help maintain consistent cutting performance across a large number of parts. Inconsistent performance due to worn tools can lead to variations in parts, which may require rework or even scrap, resulting in additional costs and delays. Tools with a longer service life help keep production outputs uniform.
- Increased Machine Utilization: A bit with a longer lifespan allows for stable cutting speeds and performance over extended periods. CNC routers can operate at peak efficiency for longer periods, optimizing the throughput and capacity of the machines.
- Lower Maintenance Requirements: Longer bit life reduces the need for constant maintenance, such as sharpening or tool changes, simplifying the overall maintenance schedule and reducing the workload on maintenance staff. Consistent bit lifespan helps manufacturers predict when a tool will need replacement, leading to better inventory management and less emergency ordering.
- Extended Equipment Life: Worn-out router bits can cause more stress on the CNC machine itself. For instance, if a tool loses its sharpness or becomes imbalanced, it could lead to vibrations, which could cause premature wear on the machine’s spindle and other components. By using high-quality router bits with longer service lives, the machine can operate smoothly, extending its overall lifespan.
The service life of a CNC router bit is directly tied to production efficiency, cost management, product quality, and machine longevity. Manufacturers should prioritize using high-quality, durable router bits and monitor their condition to maximize their lifespan and optimize the overall production process.
Factors that affect the lifespan of router bits
The lifespan of router bits can vary significantly depending on various factors, which can impact their performance and longevity in production. Here are some key factors that affect the lifespan of router bits:
Material Characteristics
The material being cut is one of the most critical factors that determine the wear and tear on the router bit. Different materials will cause varying degrees of stress on the tool. Common materials include:
- Wood: Softwoods like pine will wear the router bit slower than hardwoods such as oak or maple, but softwoods can cause resin buildup on the bit, which may affect performance.
- Metal: Non-ferrous metals like aluminum are easier on router bits than harder materials like stainless steel or titanium, which can cause significant tool wear due to the toughness and hardness of the metal.
- Plastics: Materials like PVC, acrylic, and polycarbonate are relatively easy to cut but can cause chipping or heat buildup that shortens the lifespan of the bit.
Softer materials (e.g., wood, plastic) generally extend the life of the tool, while harder materials (e.g., metals) will cause more rapid wear, especially if the cutting parameters (feed rate, speed) are not properly optimized.
Tool Material and Coating
The material and coating used to manufacture the router bit is a critical determinant of its performance and longevity. They offer different balances of strength, wear resistance, and heat resistance. Common materials include:
- High-Speed Steel (HSS): A versatile and cost-effective material, but it wears out faster compared to carbide when cutting harder materials.
- Carbide: Known for its hardness, wear resistance, and heat resistance, carbide tools are ideal for cutting harder materials and provide a longer tool life, but they are more brittle than HSS.
- Polycrystalline Diamond (PCD): Used for cutting extremely hard materials, PCD tools provide exceptional wear resistance but are very expensive.
- Coatings: Router bits coated with materials like titanium nitride (TiN) or diamond can last longer, especially in demanding applications like metal cutting or abrasive material processing.
Tools made from harder materials, like carbide or PCD, last longer when cutting tougher or more abrasive materials. However, softer tools (e.g., HSS) may wear out faster but are often less expensive and more suited to softer materials. Coated router bits last longer because they are more resistant to wear, friction, and heat.
Cutting Parameters
Cutting parameters directly impact the wear and tear on a router bit.
- Cutting Speed: If the cutting speed is too high for the material or bit type, it can lead to excessive heat buildup, which accelerates wear on the cutting edge. On the other hand, too low a speed may cause inefficient cutting and force the bit to work harder, leading to premature dulling.
- Feed Rate: A high feed rate can generate more heat and vibration, increasing the likelihood of the bit becoming dull faster. A low feed rate, however, might result in excessive pressure on the bit, causing it to wear unevenly.
- Depth of Cut: Deeper cuts demand more from the router bit, especially on tougher materials. Excessive depth of cut can overload the bit, causing it to heat up and wear faster. Shallow cuts are often more efficient and result in less wear.
By balancing the cutting speed, feed rate, and depth of cut to match the material and machine, you reduce the overall strain on the bit, ensuring it remains sharp and functional longer.
Cooling and lubrication
The cooling and lubrication systems used in CNC routers can significantly impact the lifespan of router bits.
- Coolant System: Heat buildup during cutting can be a significant factor in reducing the life of the router bit. Excessive heat causes tool materials (such as carbide or high-speed steel) to degrade more rapidly. Using an effective cooling system—whether air, liquid coolant, or mist—can significantly extend the service life of the router bit by keeping the cutting edge cool and reducing thermal stress. Insufficient cooling may lead to premature dulling, overheating, or even tool failure.
- Lubrication: Lubricants help reduce friction between the cutting surface and the bit, decreasing wear. A good lubrication system can also help to carry away heat and chips, preventing them from building up in the cut zone. Proper lubrication not only reduces wear but also improves the quality of the cut. However, improper lubrication may attract dust and debris, which could potentially accelerate wear or cause damage to the bit.
The cooling prevents the bit from overheating, while the lubrication maintains the proper cutting conditions. This allows the router bit to operate efficiently without excessive wear or damage.
Machine Rigidity and Stability
The rigidity and stability of the router machine itself significantly affect the performance and longevity of the router bit.
- Tool Chatter and Vibration: A rigid machine setup ensures minimal flexing or vibration during the cutting process. If the machine lacks rigidity, vibrations can cause micro-chipping or uneven wear on the router bit, leading to quicker dulling. A machine with high rigidity will support the bit better, ensuring smoother cuts and longer bit life.
- Tool Holding: The quality and precision of the tool holding system also influence the service life of the bit. Loose or misaligned tool holders can lead to vibrations, causing the router bit to wear unevenly. The stability of the machine’s components helps maintain consistent cutting conditions.
A rigid and stable machine setup reduces vibration and ensures that the cutting forces are evenly distributed across the bit. This helps the bit maintain sharpness longer and reduces the risk of premature wear.
By considering these factors, manufacturers can optimize the lifespan of their router bits, reduce downtime, and improve overall production efficiency. Proper care and attention to the conditions in which router bits are used can result in significant cost savings and improved cutting performance over time.
How to monitor CNC router bit wear
Regular inspection and measurement ensure that any signs of wear are caught early, preventing damage to the machine and maintaining optimal cutting performance. Here’s how to effectively monitor bit wear:
Visual Inspection
Visual inspection is the simplest and most immediate method for identifying wear and damage to CNC router bits. The process involves visually examining the bit for signs of wear such as:
- Chipped or Fractured Edges: Inspect the cutting edges for any visible chips or cracks, which can indicate excessive wear.
- Dulling of the Cutting Edge: Over time, the sharpness of the edge may diminish, leading to a dull appearance. A dull bit requires more effort to cut, which can affect the quality of the workpiece.
- Discoloration: Heat generated during cutting can cause discoloration of the material, indicating that the bit may be overheating and losing its hardness.
- Excessive Wear Patterns: Uneven wear along the edges or tip of the bit could suggest improper usage or material buildup.
- Debris Accumulation: Look for excessive material build-up on the bit, which can cause clogging and uneven cutting.
Wear Measuring Instruments
While visual inspection provides a quick assessment, more precise and reliable wear monitoring can be done with specialized tools:
- Micrometers and Calipers: These instruments can measure the diameter of the bit or the thickness of the cutting edge. Regular measurement of the tool’s geometry helps detect wear progression. A reduction in diameter or width can indicate excessive wear or damage.
- Tool sensors: CNC routers may also be equipped with sensors that monitor tool pressure, temperature, or deflection, which can be indicators of tool wear. These sensors can automatically adjust the tool path or alert operators when wear reaches a critical level.
Wear Patterns
Understanding wear patterns on the CNC router bit can help diagnose the cause and predict the future performance of the tool:
- Symmetric Wear: If wear is uniform across the entire cutting edge, it generally indicates normal wear caused by regular use. This can be managed by routine tool replacement.
- Uneven Wear: If one side of the bit wears faster than the other, it could indicate improper tool alignment, imbalance, or incorrect machine settings.
- Groove Formation: If grooves appear in the cutting edge, this might indicate that the bit is encountering hard spots in the material, or it may suggest that the router bit is not sharp enough to cut cleanly.
- Pitting and Burring: Pitting, where small holes or craters appear, may suggest overheating or inadequate cooling. Burring, or the formation of burrs along the edges, can occur due to incorrect feed rates or tool settings.
- Burn Marks: Overheating from excessive cutting pressure or insufficient cooling can result in burn marks on the bit, which can weaken the material and affect cutting quality.
By using a combination of visual inspection, precision measuring tools, and understanding wear patterns, CNC router bit wear can be effectively monitored. Proactive monitoring ensures that the router bit is maintained or replaced before excessive wear leads to poor quality cuts, machine damage, or extended downtime.
Best Replacement Strategy for CNC Router Bits
When it comes to CNC router bits, having a strategic approach to replacement is beneficial to maintain efficiency, accuracy, and quality. Here are some of the best strategies to replace CNC router bits:
Create a Maintenance Schedule
Develop a maintenance checklist based on the specific needs of your CNC machine and the materials being cut. Regular maintenance ensures that CNC router bits function at their best and that issues are caught before they cause significant damage.
- Cleaning: Regularly clean the bits to remove any built-up residue from materials like wood, plastic, or metal. Clogged bits reduce cutting efficiency and can cause premature wear.
- Lubrication: Lubricate the CNC router’s spindle and other moving parts regularly to prevent unnecessary friction that can affect tool life.
- Alignment and Calibration: Ensure the machine is properly aligned and calibrated to prevent uneven wear on the router bits, leading to premature failure.
Use a Monitoring System
Invest in a condition monitoring system (CMS) that provides real-time feedback on tool condition and machine performance. A robust CMS helps track tool performance in real-time and detect wear or damage early. This can involve:
- Vibration Monitoring: Excessive vibrations during cutting can indicate problems with the tool or machine, causing abnormal wear. A CMS can help identify vibrations that could lead to premature tool failure.
- Temperature Monitoring: High temperatures can accelerate tool wear. Installing temperature sensors on the CNC router can help track overheating and help adjust cutting parameters before damage occurs.
- Sound Analysis: Using sound sensors to detect abnormal noise during operation can help identify tool wear or damage. A sudden change in sound may indicate a dull or damaged bit.
Track Tool Performance
Log the usage data of CNC router bits to understand tool wear patterns and calculate life expectancy. Tool life expectancy calculation is beneficial to understanding when to replace or regrind a tool.
- Digital Tool Monitoring: Some modern CNC routers come with software that tracks the tool’s wear and provides an estimate of its remaining life based on cutting time, material, and type of cut.
- Time-based Replacement: If your CNC router doesn’t track tool life, use a time-based approach, where you replace bits after a set amount of cutting hours or cycles. For example, replace bits after every 100-200 hours of operation or after a set number of cuts.
- Job-based Tracking: For high-precision jobs, use a job-based approach, where the tool is replaced after processing a specific material type or batch.
Conduct Failure Analysis
Regular failure analysis can help you identify patterns in tool damage, allowing for better planning of tool replacement or regrinding.
- Types of Failures: The common causes of router bit failure include chipping, cracking, excessive wear, and thermal damage. Each of these failure types may point to different underlying issues such as poor material quality, incorrect cutting parameters, or improper maintenance.
- Root Cause Analysis: After each failure, conduct a root cause analysis to determine why the tool failed. This could involve reviewing tool material specifications, feed rates, spindle speed, and the quality of the material being cut.
Schedule Regular Tool Checks
Regularly inspect and measure tool wear to assess when regrinding or replacement is needed.
- When to Regrind or Recoat: Monitor tool performance through the condition monitoring system. If the tool shows signs of wear (such as reduced cutting efficiency or surface finish quality), it may be time to regrind or recoat.
- Regrinding: CNC router bits can often be reconditioned by regrinding the cutting edges to restore their sharpness. Regrinding should be done when tool wear reaches a threshold but before the tool has failed completely. It can significantly extend the tool’s life.
- Recoating: The tool can also be recoated with a hard material (such as titanium nitride, diamond-like carbon, or TiAlN) to improve its resistance to wear and high temperatures. A recoated bit performs better and lasts longer than an uncoated one.
Consider Environmental Factors
Environmental conditions play a major role in the longevity of CNC router bits.
- Humidity and Temperature: High humidity can cause rusting, while extreme temperatures can soften the bit and reduce its durability. Ensure the CNC routeris housed in an environment with controlled temperature and humidity.
- Dust and Contamination: Dust from cutting operations can affect both the tool and the CNC router. Use air filtration and vacuum systems to keep the workspace clean and reduce contamination.
By integrating regular maintenance, condition monitoring, and smart tool management techniques into your CNC operations, you can maximize the lifespan of your router bits, improve cutting performance, and reduce downtime caused by tool failures.
Summarize
Maintaining and extending the life of CNC router bits is beneficial for ensuring high-quality results and reducing downtime. By understanding the factors that affect router bit life expectancy, operators can decisions on when to replace their bits and how to optimize their use. A proactive approach to router bit management not only saves costs in the long term but also enhances the overall performance of CNC machinery. Continue reading “How to Prevent CNC Router Bit Damage?” to keep your router bit in top condition.
AccTek CNC stands out as a reliable and professional CNC router manufacturer, offering a range of advanced solutions tailored to meet diverse industry needs. Whether you require intricate carvings or precise cuts, our CNC routers provide the flexibility to meet your unique production demands. AccTek CNC routers ensure great value for your investment at competitive prices.