- 7-11 Min Read
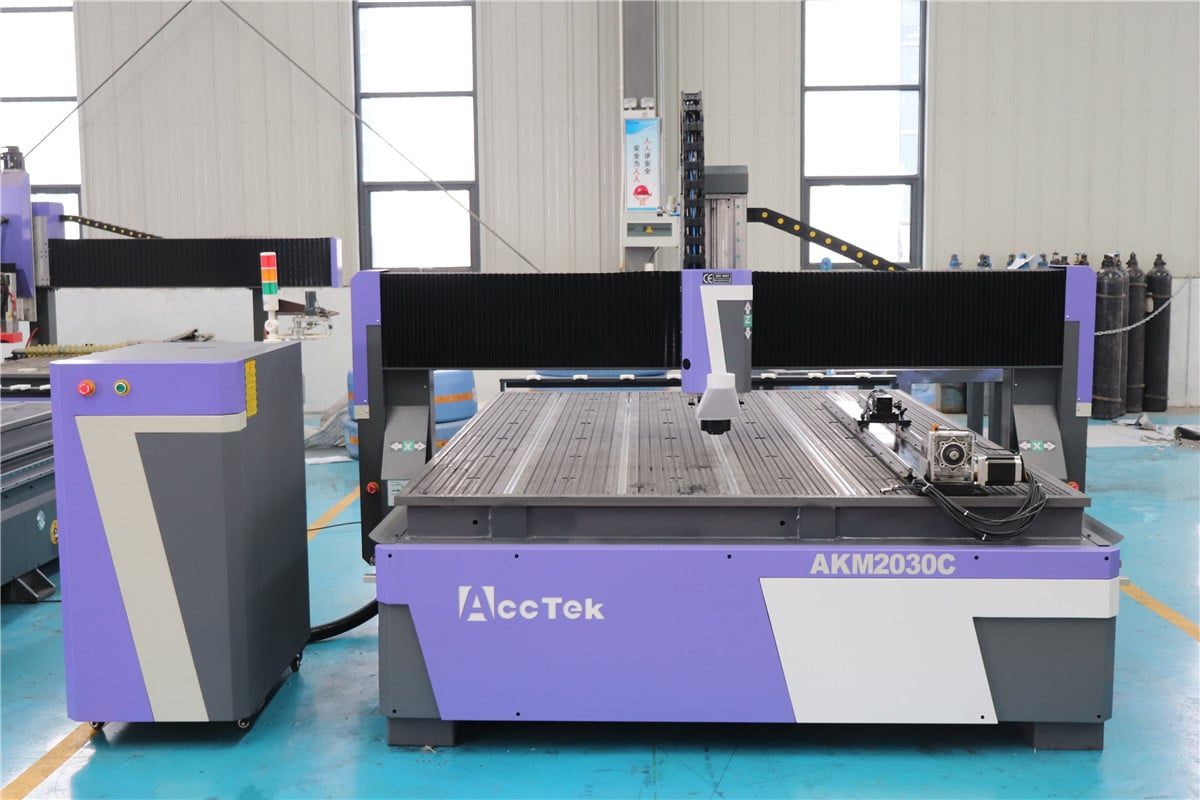
In CNC router operations, user focus often falls on factors like machine calibration, software, and material handling, so a critical aspect that is sometimes overlooked is proper machine grounding. Grounding serves as the foundation for electrical stability, protecting both the machine and its operators from potential hazards. A properly grounded CNC router ensures accurate performance by minimizing electrical noise and interference, prevents equipment damage from power surges, and enhances safety by reducing the risk of electric shock.
In this article, we will explore the effects of improper CNC router grounding and common machine grounding issues, aiming to provide you with strategies for proper grounding and best practices for maintaining your grounding system. Whether you’re troubleshooting grounding issues or looking to enhance your machine’s reliability and safety, this guide will provide the insights and solutions needed to keep your CNC router or other industrial equipment operating smoothly and safely.
Effects of Improper Grounding of CNC Router
In any industrial setup, proper grounding is a prerequisite for ensuring the safe and reliable operation of equipment, including CNC routers. Grounding provides a secure path for electrical current to dissipate, protecting both the machine and its operators from potential harm. However, improper or insufficient grounding can lead to a range of problems, from electrical instability and machine malfunctions to serious safety hazards. Here’s how improper grounding impacts the system:
Electrical Noise and Interference
CNC routers use sensitive electronics to control motion and precision. Poor grounding can result in electrical noise or interference, causing erratic behavior in the control system, including irregular movements, inaccurate cuts, or even sudden shutdowns. This can reduce machining accuracy, increase production errors, and lead to downtime for troubleshooting.
Equipment Damage
Improper grounding can cause voltage spikes or surges, especially during power fluctuations or lightning storms. These surges can damage vital components like the CNC’s power supply, spindle motor, and control systems. Damaged components result in costly repairs and replacements, along with extended downtime for the machine.
Safety Hazards
Poor grounding poses a risk of electric shock to operators. In case of a fault, such as a short circuit, a properly grounded system directs excess electrical energy safely into the ground. Without proper grounding, this energy could pass through the machine frame, potentially causing injury. This can put operator safety at risk and increase the risk of injury or fire.
Static Electricity Build-Up
CNC routers often generate static electricity during operations like cutting and milling, especially when working with non-conductive materials such as wood or plastic. Improper grounding prevents the safe dissipation of static charges. Static discharge can cause electronic malfunctions, reduce component life, and potentially ignite flammable materials in the workspace.
Reduced Lifespan of Components
Without adequate grounding, the CNC router’s electronic components are exposed to higher electrical stress. Over time, this can degrade the performance of motors, sensors, and control circuits. This can shorten the overall life of the machine, leading to premature part failure and frequent maintenance.
Data Corruption
CNC routers rely on precise digital signals to operate. Electrical noise caused by improper grounding can corrupt the data being transferred between the control computer and the machine. This leads to lost CNC programs, interrupted jobs, and the need to recalibrate or restart processes.
Increased Downtime
Diagnosing problems related to grounding can be time-consuming, as symptoms may be intermittent or hard to trace. Production delays and increased downtime are common as technicians work to locate and fix grounding issues.
Ensuring proper grounding of your CNC router is beneficial to maintaining the machine’s accuracy, protecting its components, and ensuring a safe working environment. Ignoring this aspect will lead to a host of challenges. By understanding the effects of these improper groundings, CNC operators can take proactive measures to both maintain the efficiency of their machines and ensure a safe working environment.
Identifying Common Machine Grounding Problems
Understanding the most common grounding issues is beneficial for maintaining the performance and longevity of your CNC router. In this section, we’ll explore these problems in detail, helping you identify grounding issues to ensure your machinery operates smoothly and safely. Here are some common machine grounding problems that can occur in CNC routers and similar equipment:
Poor Grounding
Poor grounding occurs when the CNC router is either inadequately grounded or the grounding connection is faulty due to loose wires, corroded terminals, or poor installation practices. This is one of the most common questions. Poor grounding compromises electrical safety and leads to electrical instability, causing voltage fluctuations, static buildup, and machine malfunctions. It also increases the risk of electric shock to operators and potential damage to electronic components.
Ground Loop Formation
A ground loop occurs when there are multiple grounding paths for the same system, causing unwanted circulating currents between the different paths. Ground loops introduce electrical noise and voltage differences that disrupt the control signals of CNC routers. This can cause erratic machine behavior, inaccurate tool movement, and interference with sensor readings.
Ground Path Impedance
High ground path impedance results when the resistance in the grounding path is too high, preventing proper dissipation of electrical surges or noise. High impedance in the grounding path can lead to voltage buildup, which may cause electrical noise, damage sensitive electronic components, and create hazardous conditions during power surges. This can lead to unpredictable machine performance and frequent breakdowns.
Grounding in a Multi-Equipment Environment
Sharing a grounding point with other machines or electrical systems is a common issue, especially in busy industrial environments. Shared grounds can lead to cross-interference between different machines, causing electrical noise and signal disruption. This cross-interference can lead to erratic CNC machine operation, inaccurate cuts, and corrupted data communication. Machines may pick up noise from nearby equipment, particularly in electrically noisy environments, affecting overall system stability.
By understanding and addressing these grounding issues, CNC router operators can reduce interference, ensure electrical stability, and improve machine reliability in complex operational environments.
Strategies for Ensuring Proper Grounding of Machinery
Proper grounding is the basis for the safe and reliable operation of machinery like CNC routers. By implementing the following strategies, you can ensure that your equipment is grounded effectively, reducing the risk of electrical instability, interference, and safety hazards:
Grounding System Design
The grounding system design forms the foundation of proper grounding. It must be carefully planned to ensure that all components of the CNC router, including the control system, power supply, and motors, are properly connected to a reliable ground. Implement a star grounding configuration, where each component of the machine has an individual ground connection that converges at a single grounding point. This approach minimizes the risk of ground loops, which can introduce noise and instability into the system.
Grounding Electrode Selection
Choosing the right grounding electrode is beneficial for effective electrical dissipation. The grounding electrode is the physical connection between the machine and the earth, and its selection determines how efficiently electrical currents are transferred to the ground. Use high-quality materials like copper or galvanized steel rods with low resistance. Ensure that the electrode is placed in a location with good conductivity and soil moisture for optimal performance.
Connection and Equipotential Grounding
Ensure that the connection between machine components and the ground is safe and reliable. Equipotential grounding refers to the practice of connecting all components to the same grounding potential to prevent voltage differences that can lead to electrical noise or hazards. Use low-impedance conductors and ensure solid, corrosion-free connections. Verify that all parts of the machine are grounded to the same point to eliminate ground loops and voltage imbalances.
Surge Protection and Isolation
Protecting the machine from external electrical disturbances, such as power surges or lightning strikes, is beneficial to maintaining long-term stability and safety. Install surge protection devices (SPDs) to divert excess voltage away from the machine and isolate sensitive components from electrical disturbances. This prevents damage to the machine’s electronics and ensures stable operations in fluctuating power environments.
Compliance with Local Electrical Codes and Standards
Follow local and international electrical codes and standards when designing and installing grounding systems for machinery. Compliance ensures that the grounding system is safe, effective, and designed to handle the electrical load of the machine, reducing the risk of accidents and equipment failure.
Regular Maintenance and Inspection
Over time, grounding systems can degrade due to wear, corrosion, or environmental factors, leading to reduced effectiveness. Schedule periodic inspections to check the integrity of grounding connections, clean terminals, and replace any worn or corroded components. Regular maintenance ensures that the grounding system continues to function optimally and prevents electrical failures.
By implementing these strategies, you can ensure that your machinery is properly grounded, reducing electrical noise, improving operational stability, and enhancing safety.
Best Practices for Keeping Your Machine Properly Grounded
Maintaining an effective grounding system during CNC router operation requires more than just initial setup, it involves ongoing practice. In this section, we will explore the best practices that can help keep your machinery properly grounded, minimizing risks and enhancing operational performance.
Operator Training and Awareness
Provide comprehensive training to CNC router operators on the importance of proper grounding and how to identify potential grounding issues. By educating operators, they can take immediate action when issues arise, ensuring the machine stays properly grounded and operational. Here are the key actions:
- Train operators to recognize signs of grounding issues like static discharge, erratic behavior, or electric shocks.
- Implement safety training on how to safely handle machines with grounding issues.
Documentation and Record Keeping
Maintain detailed documentation of the machine’s grounding system, including installation details, grounding points, materials used, and any maintenance or inspections conducted. Accurate records help trace and troubleshoot grounding problems quickly and ensure that grounding systems are maintained consistently over time. Here are the key actions:
- Record all grounding inspections, maintenance activities, and any modifications to the grounding system.
- Keep up-to-date records of equipment-specific grounding needs and configurations.
Collaboration with Electrical Professionals
Electrical professionals can ensure that the grounding system meets industry standards, complies with electrical codes, and addresses the specific power and safety needs of the machine. Therefore, the machine’s grounding system should be designed, installed and maintained in close cooperation with qualified electricians and electrical engineers. Here are the key actions:
- Schedule regular inspections and audits of the grounding system by certified electrical professionals.
- Consult electrical experts for complex grounding challenges, especially in multi-equipment environments or when upgrading machinery.
Continuous Improvement
Regularly review and update the grounding system to incorporate new technologies, improve safety measures, and ensure that it meets the changing demands of the machinery and production environment. As new technologies and practices emerge, continuous improvement ensures the grounding system remains efficient, safe, and compliant with the latest standards. It also reduces the likelihood of grounding-related failures as the system ages or as production demands increase. Here are the key actions:
- Periodically assess the grounding system’sperformance and look for areas to improve efficiency, such as upgrading materials or redesigning the grounding layout.
- Stay informed about advancements in grounding techniques and technologies and implement them where applicable.
Keeping a robust grounding system is beneficial for the smooth operation and safety of industrial CNC routers. By following the best practices above, you can ensure that your grounding system remains effective over time. These measures not only prevent costly downtime and equipment damage but also safeguard the well-being of your workforce. In the end, a well-grounded CNC router is a cornerstone of both operational efficiency and workplace safety, making it a priority for any industrial environment.
Summarize
Proper grounding of CNC routers is not just a technical requirement but a foundational aspect of safe and precise CNC operations. By understanding common grounding issues, implementing effective grounding strategies based on the scenarios provided in this article, and adhering to best practices, you can create a stable, interference-free environment that ensures your CNC router operates at peak efficiency, consistently delivering accurate results. To learn more about CNC router operation, you can continue reading “CNC Router Safety Operation Guide“.
AccTek CNC, a well-known CNC router manufacturer in China, is a trusted name in the industry for delivering precision and reliability in their machines. With a strong focus on addressing common grounding issues and implementing best practices, AccTek CNC routers provide a stable, interference-free environment that enhances operational efficiency and accuracy. Whether for small workshops or large-scale industrial applications, AccTek CNC’s machines are designed to meet the highest standards of safety and precision, making them a top choice for businesses seeking reliable and high-performance CNC solutions.