- 10-15 Min Read
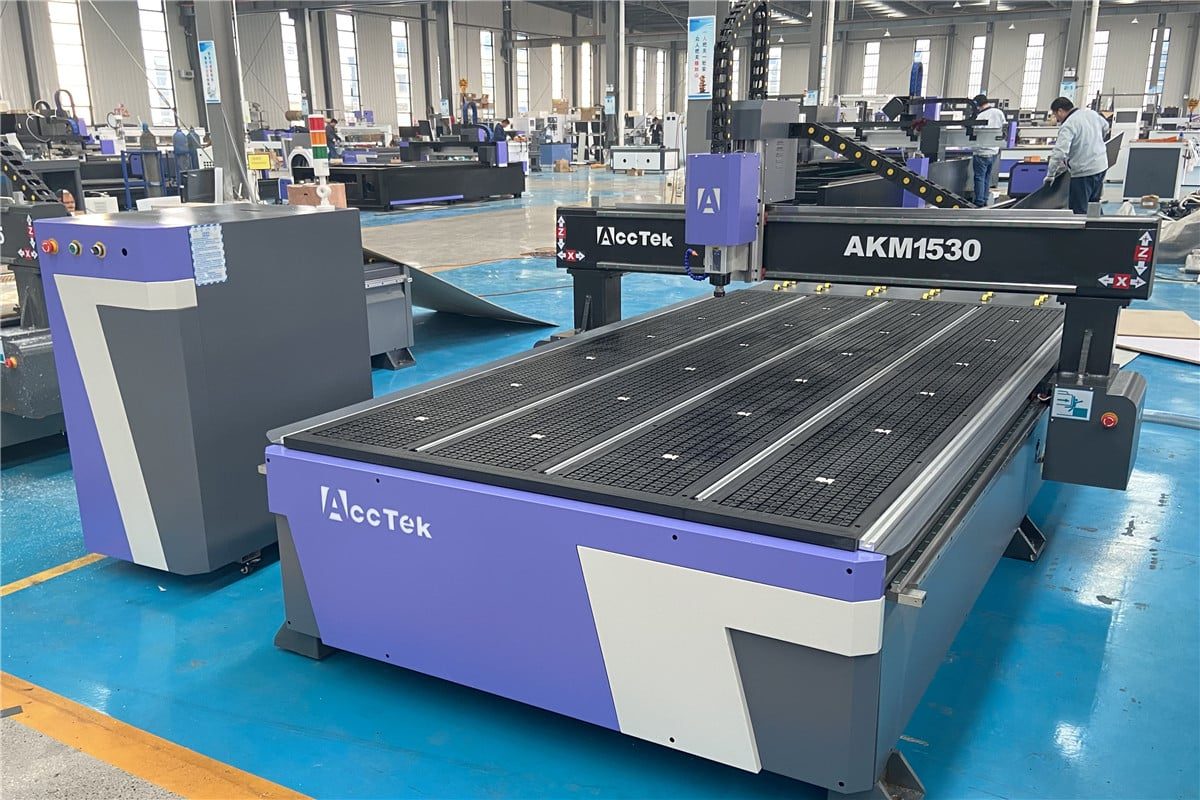
In the realm of modern manufacturing and woodworking, Computer Numerical Control (CNC) routers stand as the vanguard of precision and efficiency. Central to the performance of these cutting-edge machines is the worktable – the foundation upon which intricate designs take shape, and creative visions materialize into reality. From the initial setup and alignment to regular maintenance and specialized customization, understanding and optimizing the worktable can significantly enhance the performance and outcomes of CNC machining operations. Whether you’re a seasoned professional or a hobbyist stepping into the realm of CNC machining, understanding the intricacies of the CNC router worktable is essential. This comprehensive guide will delve into the various aspects of CNC router worktables, including their types, operating methods, maintenance, and customization options, equipping you with the knowledge to optimize your CNC router setup for superior results.
The importance of CNC router worktable
The importance of a CNC router worktable is reflected in several key aspects that highlight its impact on precision, efficiency, versatility, and overall workflow in woodworking and various other industries. Here are the primary areas where its significance is most evident:
- Stability and Rigidity: The worktable serves as the foundation upon which the material being routed is secured. A sturdy and rigid worktable is beneficial for maintaining stability during the machining process, minimizing vibrations, and ensuring accurate cuts and carvings. This is particularly important for detailed work, intricate designs, and repeatable production tasks.
- Efficiency and Productivity: A well-designed CNC router worktable enhances efficiency by allowing for quicker setup times and smoother operation. Automated processes reduce manual labor, minimize errors, and speed up production cycles, making it possible to complete projects faster and more consistently.
- Versatility: The versatility of a CNC router worktable is reflected in its ability to handle a wide range of materials, including wood, plastics, composites, and metals. This flexibility allows users to take on diverse projects, from simple cuts to complex 3D carvings, expanding the scope of what can be created with a single machine.
- Workflow Optimization: An optimized worktable design can streamline the CNC routing workflow, minimizing setup time, reducing material waste, and maximizing productivity. Features such as integrated tool storage, material alignment guides, and automated workpiece loading/unloading systems enhance efficiency and workflow continuity.
- Safety: Safety is a paramount concern in any workshop. A stable and secure CNC router worktable minimizes the risk of material shifting or slipping during operation, thereby reducing the likelihood of accidents. Additionally, it can be equipped with safety features such as emergency stop buttons and protective barriers.
- Flatness and Levelness: A flat and level worktable surface is beneficial for achieving precise and consistent machining results. Any deviation in the flatness of the worktable can lead to inaccuracies in the finished product. CNC router worktables are meticulously engineered to maintain tight tolerances for flatness and levelness, ensuring uniform cutting depths and surface finishes.
- Material Support: CNC router worktables come in various designs and configurations to accommodate different types of materials, sizes, and shapes. Whether you’re working with wood, plastic, metal, or composite materials, the worktable provides the necessary support and clamping mechanisms to securely hold the workpiece in place throughout the machining operation.
- Customization and Scalability: The adaptability of a CNC router worktable allows for easy customization and scalability. Users can modify the worktable setup to accommodate different project sizes and complexities, making it suitable for both small-scale bespoke projects and large-scale industrial manufacturing.
The importance of the CNC router worktable lies in its role as the foundational element of the machining process, providing stability, support, and precision to ensure accurate and efficient production of a wide range of woodworking and fabrication projects.
Types of CNC router worktable
CNC router worktables come in various types, each designed to accommodate different materials, applications, and levels of precision. Here are some common types of CNC router worktables.
T-Slot Worktable
A T-slot worktable is a versatile and widely used type of CNC router worktable characterized by a grid of T-shaped slots machined into its surface. These slots allow for the flexible positioning and securing of workpieces using T-slot nuts, bolts, and clamps. The design provides an adaptable and robust platform for various machining operations.
Applications
- Woodworking: Holds components for detailed work such as dovetail joints and intricate carvings.
- Metalworking: Ideal for holding metal prototypes for drilling, milling, and shaping. Facilitates precise positioning and clamping of metal parts.
- Custom Parts: Holds irregularly shaped pieces for custom fabrication tasks.
- Sign Making: Secures various substrates such as metal, wood, and plastic for detailed engraving work.
Advantages
- Versatility: The T-slot design allows for flexible and customizable positioning of clamps, fixtures, and workpieces, accommodating a wide range of shapes and sizes.
- Secure Clamping: Provides strong and reliable clamping, minimizing workpiece movement and ensuring precision during machining.
- Ease of Use: Simple to set up and adjust, making it convenient for both experienced operators and beginners.
- Cost-Effective: Typically less expensive than more specialized worktables like vacuum tables, while still offering a high degree of functionality.
- Durability: Made from robust materials, T-slot tables can withstand the rigors of heavy-duty machining operations.
Disadvantages
- Setup Time: Clamping and securing workpieces can be time-consuming, especially for complex setups or when frequent adjustments are needed.
- Potential for Obstruction: The clamps and fixtures can obstruct the cutting tool path if not positioned carefully, which might limit accessibility to certain areas of the workpiece.
- Maintenance: The slots can accumulate debris and require regular cleaning to ensure the smooth operation of clamps and fixtures.
- Limited to Flat Workpieces: Best suited for flat or nearly flat workpieces,irregularly shaped or very thin materials may require additional fixturing or support systems.
- Manual Adjustment: Adjusting and repositioning clamps and fixtures manually can be labor-intensive, particularly for high-volume or repetitive tasks.
Vacuum Worktable
A vacuum worktable, also known as a vacuum table or vacuum hold-down table, is a type of CNC router worktable that uses suction to secure the workpiece firmly in place during machining operations. The table consists of a flat surface with a network of vacuum channels and ports connected to a vacuum pump. When the vacuum pump is activated, it creates a strong suction force that holds the workpiece securely against the table surface, minimizing movement and vibration.
Applications
- Woodworking: Ideal for holding large, flat wooden panels during cutting and engraving.
- Large Format Signs: Holds down large sheets of materials like PVC, acrylic, and foam boards for precise cutting.
- Thin Materials: Perfect for handling delicate, thin materials that might be damaged by mechanical clamping.
- Layered Material Work: Keeps multiple layers of thin materials securely in place during machining.
Advantages
- Uniform Hold: Provides even suction across the entire surface, ensuring the workpiece is held securely and uniformly without warping.
- Quick Setup: Simplifies the setup process as it eliminates the need for mechanical clamps or fixtures, reducing preparation time.
- Damage Prevention: Reduces the risk of damaging delicate or thin materials that might be marred by traditional clamping methods.
- Increased Productivity: Streamlines the machining process by allowing for quick and easy material changes, enhancing overall productivity.
Disadvantages
- Cost: Initial setup costs can be high due to the need for a vacuum pump, plumbing, and maintenance.
- Power Requirements: Requires a continuous power supply to maintain suction, which can increase operational costs.
- Material Limitations: Not suitable for very porous materials that allow air to pass through, as they may not generate sufficient hold-down force.
- Maintenance: Vacuum systems require regular maintenance to ensure optimal performance, including cleaning vacuum channels and ensuring the pump operates efficiently.
- Workpiece Size: Best suited for flat, relatively thin workpieces,irregularly shaped or very thick items might not be held as effectively.
T-slot Vacuum Combination Worktable
A T-slot vacuum combination worktable merges the functionalities of both T-slot and vacuum tables, providing a versatile and flexible solution for CNC routing. This hybrid worktable features T-slot channels for mechanical clamping and a vacuum system for holding down workpieces. This dual approach allows users to leverage the benefits of both clamping methods depending on the requirements of their projects.
Applications
- Woodworking: Ideal for securing large, flat wooden panels or boards using the vacuum system, while the T-slots can clamp smaller, irregularly shaped pieces or fixtures.
- Sign Making: Useful for holding down thin, flexible materials like vinyl or plastic sheets with the vacuum, and using T-slots for thicker materials or specialized fixtures.
- Composite Materials: Efficiently manages different material types used in composite manufacturing by combining vacuum hold for flat sheets and T-slots for custom-shaped components.
- Prototyping and Custom Fabrication: Offers the flexibility needed for prototype work where varied and complex setups are common, enabling easy adjustments and repositioning.
- Metalworking: Suitable for non-ferrous metals, where vacuum holds can secure flat sheets, and T-slots can handle heavier, irregularly shaped parts.
Advantages
- Versatility: Combines the strengths of vacuum hold-down for flat, smooth materials and mechanical clamping for irregular or thick workpieces.
- Efficiency: Reduces setup time by allowing quick switching between vacuum and T-slot clamping methods, depending on the task at hand.
- Enhanced Holding Power: Provides multiple options to secure workpieces, ensuring stability and precision during machining operations.
- Flexibility: Adaptable to a wide range of materials and project types, making it suitable for various industries and applications.
Disadvantages
- Cost: Higher initial investment compared to single-purpose worktables due to the integration of both vacuum and T-slot systems.
- Complexity: More complex setup and maintenance, requiring familiarity with both vacuum and mechanical clamping systems.
- Power and Air Requirements: The vacuum system requires a reliable source of vacuum pressure, which may involve additional equipment such as vacuum pumps or compressors.
- Potential for Reduced Vacuum Efficiency: If the T-slot channels are not properly sealed when using the vacuum system, it can lead to air leaks and reduced vacuum efficiency.
- Weight and Size: Combined systems can be heavier and bulkier, which might pose challenges in smaller workshops or for mobile setups.
Worktable setup and alignment
Setting up and aligning a CNC router worktable is a fundamental process that ensures precise and efficient machining. The initial setting procedure and the establishment of reference points are critical steps that lay the foundation for accurate operations. This part will walk you through the essential steps involved in setting up and aligning your CNC router worktable, starting from the initial setup to the establishment of crucial reference points.
Initial Setting Procedure
- worktablePreparation: Place your CNC router worktable on a stable, vibration-free surface. The location should be spacious enough to accommodate both the machine and the operator’s movement.
- Frame Assembly: Assemble the CNC router’s frame according to the manufacturer’s instructions, ensuring that all components are securely fastened and aligned.
- Electrical Connections: Connect the CNC router to a reliable power source, ensuring that the voltage matches the machine’s requirements.
Establishment of Reference Points
- Setting the Home Position: Define the home position, the fundamental reference point from which all machine movements are measured. Typically, this position is located at one corner of the work area. Utilize the CNC control software to designate and configure this point as the home position, establishing a consistent starting point for subsequent operations.
- Establishing Workpiece Zero: Secure the workpiece on the worktableusing appropriate clamping or vacuum systems. Use a touch probe, edge finder, or manual method to locate the exact starting point on the workpiece. Set this point in the control software, aligning it with the home position for accurate toolpath execution.
- Probing and Recording Reference Surfaces: Use a tool probe or dial indicator to touch known reference points on the worktable Enter the coordinates of these reference points into the CNC control software. This data serves as a baseline for machine calibration and future setups.
- By following a systematic procedure, you can ensure your CNC router is properly aligned and calibrated. This meticulous approach to setup and alignment lays the foundation for efficient and accurate CNC operations, ultimately enhancing productivity and ensuring high-quality outputs.
Worktable Maintenance
Maintaining a CNC router worktable is beneficial for ensuring its longevity, precision, and efficiency. Regular maintenance helps prevent breakdowns, maintains accuracy, and extends the life of the machine. Here are the key maintenance tasks that should be performed on a CNC router worktable:
Regular Cleaning Procedures
- Removing Dust and Debris: At the end of each workday, use a vacuum or compressed air to remove dust and debris from the worktablesurface, including T-slots and vacuum ports. Use a soft brush to clean areas that are difficult to reach with a vacuum. Ensure that all nooks and crannies are free of accumulated debris.
- Avoiding Contamination of the Vacuum worktable: If using a vacuum table, check the vacuum pump and filters. Clean or replace filters and ensure the vacuum channels are clear of obstructions. Clean the vacuum seals and gaskets periodically with a mild detergent to remove any dust, debris, or residue that may affect their sealing capability.
Inspection for Wear and Damage
- Checking T-Slot Wear: Regularly inspect the T-slots on the worktablesurface for signs of wear, deformation, or damage. Look for burrs, scratches, or uneven surfaces that may affect clamping effectiveness. Use precision measuring tools such as calipers or micrometers to check the dimensions of the T-slots. Ensure that they meet the manufacturer’s specifications for size and alignment.
- Inspecting Vacuum Seals and Punctures: Inspect the vacuum seals and gaskets regularly for any signs of wear, damage, or deterioration. Pay close attention to areas where seals meet the worktable Replace any worn seals to maintain vacuum integrity.
By following these maintenance guidelines, you can ensure that the worktable of your CNC router remains in optimal condition. Regular maintenance helps prevent issues such as contamination, wear, and vacuum leaks, allowing you to maximize productivity and efficiency in your machining operations.
Customized Worktable for Special Applications
Designing a customized worktable for a special application involves tailoring the worktable’s features and configuration to meet specific requirements and challenges unique to the application. Whether it’s accommodating oversized workpieces, enhancing material handling capabilities, or optimizing workflow efficiency, a customized worktable can provide tailored solutions to address the needs of specialized projects. Here’s a guide on how to create a customized worktable for a special application:
Identify Application Requirements
- Understand the Project: Gain a comprehensive understanding of the project requirements, including the type of materials, dimensions of workpieces, machining processes involved, and any specific challenges or constraints.
- Consider Workflow: Evaluate the workflow from material preparation to final machining and consider how the worktable can streamline processes and improve efficiency.
- Address Special Challenges: Identify any unique challenges or limitations that require specialized solutions, such as handling delicate materials, accommodating irregular shapes, or integrating additional equipment.
Determine Worktable Features
- Size and Configuration: Determine the optimal size and configuration of the worktable based on the dimensions of the workpieces and available space in the workshop.
- Clamping and Fixturing: Choose appropriate clamping mechanisms and fixturing options to securely hold the workpieces in place during machining. Consider factors such as material compatibility, holding capacity, and accessibility.
- Material Compatibility: Select materials for the worktable construction that are compatible with the machining processes and materials being used. Consider factors such as rigidity, stability, and resistance to wear and corrosion.
Integrate Specialized Components
- Custom Fixtures: Design and fabricate custom fixtures or tooling components tailored to the specific requirements of the application. These fixtures may include vices, clamps, jigs, or specialized holding devices.
- Material Handling Systems: Integrate material handling systems such as conveyor belts, roller tables, or robotic arms to streamline material loading, unloading, and transfer processes.
- Auxiliary Equipment: Incorporate auxiliary equipment such as dust collection systems, coolant systems, or part marking systems to enhance the functionality and performance of the worktable.
Incorporate Ergonomic Considerations
- Operator Accessibility: Ensure that the design of the worktable facilitates easy access for operators to load, unload, and maneuver workpieces safely and efficiently.
- Ergonomic Design: Consider ergonomic factors such as work height, reach distances, and operator comfort to minimize fatigue and maximize productivity during prolonged machining operations.
By following these steps, you can design and implement a customized worktable tailored to the specific requirements of your special application. Whether it’s improving efficiency, enhancing precision, or overcoming unique challenges, a customized worktable can provide the specialized solutions needed to achieve success in your projects.
Operator worktable use training
Training operators on the use of a CNC router worktable is beneficial for ensuring safety, efficiency, and optimal performance. A well-structured training program should cover the fundamentals of CNC router operation, specific worktable features, and best practices for handling materials and tools. Here are the steps for training operators on using a CNC router worktable:
- Introduction to CNC Router Basics: Provide a basic understanding of what a CNC router is, its applications, and how it operates. Introduce the main components of the CNC router, including the worktable, spindle, gantry, control panel, and software.
- Safety Training: Instruct operators on the importance of wearing appropriate PPE, such as safety glasses, ear protection, and gloves. Explain the location and use of emergency stop buttons.
- Understanding the Worktable: Explain different types of worktables (e.g., T-slot, vacuum, combination) and their specific features. Demonstrate how to use various clamping and fixturing methods to secure workpieces on the worktable. Highlight the importance of ensuring that workpieces are firmly secured to avoid movement during machining.
- Setting Up the Worktable: Show how to check and adjust the level and alignment of the worktable to ensure precision machining. Teach how to set the home position and workpiece zero using the CNC control software and probing tools. For vacuum tables, explain how to activate and maintain the vacuum system, ensuring that seals are intact and vacuum channels are clear.
- Maintenance Procedures: Teach operators how to clean the worktable and machine after each use, removing dust, debris, and material residues. Instruct on how to perform regular inspections of the worktable, checking for wear, damage, and ensuring all components are functioning properly.
- Troubleshooting and Problem-Solving: Identify common problems that may arise during CNC router operation, such as alignment issues, clamping failures, or software errors. Provide troubleshooting steps and techniques for diagnosing and resolving these issues.
A comprehensive training program for CNC router worktable use ensures that operators are knowledgeable, skilled, and confident in their abilities. By covering safety, worktable setup, machine operation, maintenance, and troubleshooting, you can help operators achieve optimal performance and maintain a safe working environment.
Summarize
Mastering the CNC router worktable transforms it from a simple platform into a dynamic tool that drives innovation, accuracy, and excellence in machining. By following the comprehensive guidelines provided in this guide, operators can ensure that their CNC router worktables are meticulously prepared, accurately aligned, and well-maintained. This not only minimizes downtime and extends the lifespan of the machine but also guarantees the highest quality results in every project.
At AccTek CNC, we offer a range of CNC routers designed to meet diverse machining needs, with customizable options available to suit specific applications. Our team of experts is dedicated to providing comprehensive support and guidance to help you select the right CNC router and worktable configuration for your projects. With our reliable equipment and expert assistance, you can achieve superior results and maximize productivity in your CNC machining operations.