- 18-23 Min Read
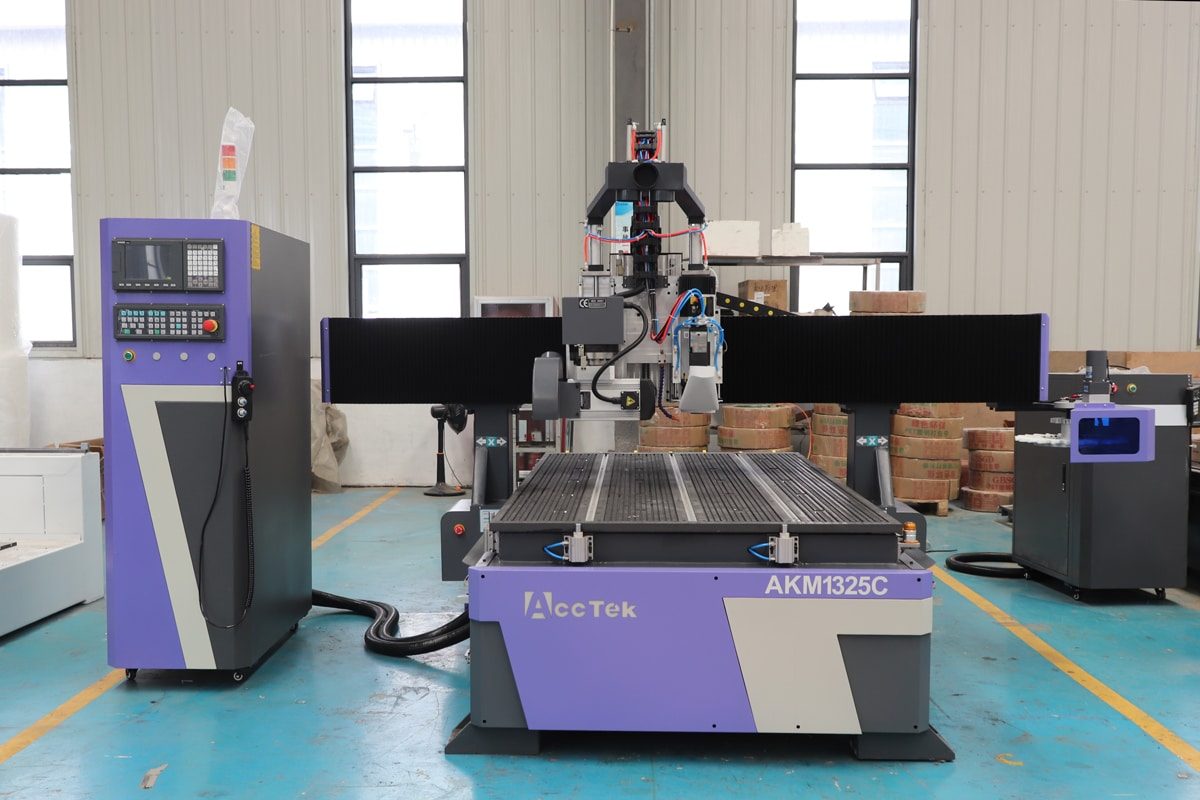
Custom furniture making has evolved significantly with the advent of CNC routers. These powerful machines allow furniture makers, hobbyists, and small businesses to design and produce intricate, high-quality pieces with precision and efficiency. Whether you’re crafting a one-of-a-kind coffee table, a custom-built cabinet, or a unique wooden chair, a CNC router opens up endless possibilities for creativity and customization.
This guide will take you through the entire process of making custom furniture with a CNC router, from selecting the right machine and materials to designing, cutting, engraving, and finishing your project. Whether you’re a beginner exploring CNC woodworking for the first time or an experienced craftsman looking to optimize production, this guide will provide valuable insights and practical tips to help you bring your furniture ideas to life with precision and ease.
Understanding Custom Furniture Making
Custom furniture making is the process of designing and building unique, tailor-made furniture pieces that cater to specific customer needs, space requirements, and personal preferences. Unlike mass-produced furniture, custom pieces allow for greater creativity, personalization, and high-quality craftsmanship.
What is Custom Furniture?
Custom furniture is designed to meet individual specifications in terms of size, style, materials, and functionality. Whether it’s a handcrafted dining table, a built-in wardrobe, or an intricately carved bookshelf, custom furniture provides a level of uniqueness that store-bought furniture cannot match.
Importance of Custom Furniture Making
The demand for custom furniture has grown due to several key advantages:
- Personalization & Uniqueness: Customers can design furniture that reflects their style and matches their interior decor.
- Higher Quality Materials & Craftsmanship: Custom furniture makers often use premium materials and advanced techniques, leading to more durable and aesthetically refined products.
- Optimized Space & Functionality: Custom designs maximize space utilization, particularly in homes, offices, and commercial environments with specific layout constraints.
- Sustainability & Eco-Friendliness: Many custom furniture makers focus on sustainable materials and production methods, reducing waste and environmental impact.
Traditional Furniture Making Techniques
Before the advent of CNC technology, furniture making relied on traditional woodworking methods, which required exceptional skill and attention to detail. Some of the most common techniques include:
- Handmade Craftsmanship: Skilled artisans use hand tools such as chisels, saws, and planes to shape and assemble wooden furniture. This method allows for intricate detailing and artistic expression but requires significant time and expertise.
- Joinery techniques: Strong and durable furniture requires expert joinery. Traditional methods include dovetail joints, mortise and tenon joints, finger joints and lap joints.These technologies are mainly used for joining wood product parts.
- Finishing Methods: The final step in furniture making involves sanding, staining, painting, or sealing the surface to enhance durability and appearance. Traditional finishes such as hand-applied varnish, oil-based stains, and wax coatings contribute to the beauty and longevity of the furniture.
While these traditional techniques continue to be valued, the introduction of CNC routers has transformed the industry by streamlining design, cutting, and joinery processes, making custom furniture making more accessible and efficient. In the next sections, we will continue to learn about the types of CNC routers used for furniture manufacturing.
Understanding CNC Routers for Furniture Making
CNC routers have transformed furniture making by providing precision, efficiency, and flexibility in crafting custom pieces. This section explores what CNC routers are, their types, and their key components to help you understand their role in custom furniture production.
What is a CNC Router?
A CNC router is a computer-controlled cutting machine used for shaping and carving various materials, including wood, plastic, and composites. Unlike traditional hand tools, a CNC router follows digital design files (CAD/CAM) to execute precise cuts, engravings, and 3D carvings automatically. This eliminates human error, improves efficiency, and allows for complex designs that would be difficult to achieve manually.
Types of CNC Routers for Furniture Making
CNC routers come in different types based on size, structure, and functionality. Choosing the right machine depends on production needs, budget, and material compatibility.
- Hobbyist & Desktop CNC Routers: Small and compact, ideal for DIY furniture projects and prototyping.
- Industrial CNC Routers: Large-format machines designed for mass production with high-speed cutting and multi-tool capabilities.
- 3-Axis CNC Routers: The most common type, capable of moving in three directions (X, Y, and Z) for basic cutting and carving.
- 4-Axis& 5-Axis CNC Routers: Advanced machines that allow for rotation and multi-directional cutting, perfect for creating intricate, curved furniture designs.
- Rotary Axis CNC Router: Equipped with a rotary axis, it can engrave cylindrical objects. Very suitable for making furniture parts such as table legs, chair legs, Roman columns, and stair railings.
Key Components of a CNC Router
Understanding the essential parts of a CNC router helps in selecting, operating, and maintaining the machine effectively.
- Spindle: The cutting tool that rotates at high speeds to carve and shape materials.
- Worktable: The surface where materials are secured for cutting (vacuum tables or T-slot tables improve stability).
- Stepper or Servo Motors: Motors control the movement of the router in different axes, ensuring precision and smooth motion.
- Linear Guides & Rails: Provide accurate motion control for the cutting head.
- Controller & Software: The brain of the CNC router, which translates digital design files into precise movements.
- Dust Collection System: Maintained a clean workspace by removing sawdust and debris.
By integrating CNC routers into custom furniture making, designers and manufacturers can create high-quality, personalized furniture pieces with greater ease and efficiency. In the next sections, we’ll explore how to choose the right machine and the best materials for furniture making and the step-by-step process of turning digital designs into finished products.
Choosing the Right CNC Router for Custom Furniture
When selecting a CNC router for custom furniture manufacturing, it’s essential to consider several key factors to ensure the machine meets both your design needs and production requirements. With the vast array of CNC routers available on the market, understanding these factors will help you make an informed decision and choose a machine that enhances your capabilities.
Size and Work Area
One of the first considerations when choosing a CNC router is the size of the work area, which will determine the maximum dimensions of the material you can process. Custom furniture often requires working with large sheets of material, so selecting a CNC router with a spacious bed size is beneficial for accommodating larger pieces like tabletops, cabinet panels, and shelving units. If you’re working in a smaller shop or focusing on smaller, detailed pieces, a more compact machine may suffice.
Spindle Power and Speed
The spindle is the heart of the CNC router, responsible for rotating the cutting tools. The spindle power determines the machine’s ability to cut through various materials. For custom furniture making, especially when working with harder woods or composite materials, a more powerful spindle will allow you to cut through thicker materials efficiently. Additionally, spindle speed (RPM) is important for achieving clean cuts and smooth finishes, particularly when performing delicate carvings or engravings.
Number of Axes
The number of axes on a CNC router defines its movement capabilities. The most common CNC routers are 3-axis machines, which allow movement along the X, Y, and Z axes for basic cutting, carving, and shaping. However, for more intricate, sculptural designs or detailed joinery, a 4-axis or 5-axis router may be necessary. These machines provide additional rotational capabilities, enabling more complex shapes and carvings that would otherwise be difficult to achieve. If you plan on creating detailed 3D carvings or unique artistic furniture, investing in a multi-axis machine may be beneficial.
Software Compatibility
CNC routers are operated using CAD and CAM software, which convert digital designs into machine-readable instructions. To ensure that the CNC router you choose is compatible with the software you plan to use. Popular software options like AutoCAD, SolidWorks, and Fusion 360 require specific controller compatibility. Some CNC routers come with their own proprietary software, while others support third-party programs, so ensure that the system you choose integrates well with your design tools.
Budget and ROI
The cost of CNC routers can vary widely, from entry-level machines to high-end industrial models. While it’s tempting to opt for a budget-friendly model, consider the long-term benefits and return on investment (ROI). Investing in a more advanced machine with greater precision, larger work areas, and higher spindle power may cost more upfront but will increase productivity, reduce labor costs, and improve the quality of your custom furniture. Consider your budget, production volume, and the complexity of the designs you want to create when evaluating different machines.
Machine Durability and Maintenance
CNC routers are long-term investments, so it’s important to choose a machine built to last. Look for routers made from high-quality materials, such as steel frames and durable components, to ensure longevity. Additionally, consider the ease of maintenance. Machines that are easy to clean, have accessible parts for maintenance, and offer reliable performance over time will save you money and prevent disruptions in production.
Choosing the right CNC router for custom furniture manufacturing involves a careful balance of factors. By considering your specific production needs, budget, and the complexity of the designs you plan to create, you can select a CNC router that enhances both your creativity and efficiency.
Materials for CNC Furniture Making
Choosing the right material is important in the custom furniture-making process as it directly impacts the durability, appearance, and functionality of the final product. CNC routers can work with a wide variety of materials, each offering different benefits and challenges. This section explores the most common materials used in CNC furniture making to help you make informed decisions when designing and crafting custom furniture.
Wood
Wood remains one of the most popular and versatile materials for custom furniture making. CNC routers excel in shaping wood due to its workability, natural beauty, and wide range of finishes.
- Hardwood: These include oak, maple, walnut, and cherry. These woods are known for their strength, durability, and fine grain patterns, making them ideal for high-end furniture such as tables, cabinets, and chairs.
- Softwood: These includes pine, cedar, fir, and spruce. These woods are lightweight, easy to machine, and more affordable than hardwoods, and are often used for casual or country-style furniture.
- Plywood: These include birch, maple, and pine. Plywood is a strong, stable material made from thin layers of wood glued together. It is versatile, cost-effective, and suitable for creating furniture like cabinets, shelving, and tables.
- Medium-Density Fiberboard: Smooth, dense, and easy to cut, MDF is perfect for precise, detailed work like intricate engravings. It’s also less prone to warping compared to solid wood.
Plastics
Plastics offer versatility and durability in CNC furniture making, particularly for modern, minimalistic, or functional designs.
- Acrylic (PMMA): Transparent, durable, and resistant to UV damage. Ideal for modern furniture pieces, decorative items, and even lighting installations.
- Polycarbonate: Stronger and more impact-resistant than acrylic. It’s often used for furniture requiring durability and transparency.
- PVC (Polyvinyl Chloride): Lightweight, durable, and water-resistant. It’s commonly used for practical furniture applications like outdoor furniture or storage units.
Metals
While less common for typical furniture making, metals are increasingly being used for modern, industrial-style furniture, especially for components like frames, legs, and accents. CNC routers with specialized tooling can cut and shape metals with great precision.
- Aluminum: Lightweight, strong, and resistant to rust and corrosion. Ideal for contemporary furniture and for creating sleek, minimalistic designs.
- Stainless Steel: Strong, durable, and resistant to rust, making it suitable for both indoor and outdoor furniture.
- Brass & Copper: Both materials have a luxurious appearance and are often used for accent pieces, handles, and decorative elements in furniture design.
Choosing the right material for CNC furniture making is a crucial step in achieving both the aesthetic and functional goals of your project. Wood, plastics, and metals each offer unique benefits depending on the design and intended use of the furniture. Understanding the properties and workability of these materials, along with the capabilities of your CNC router, will help you create custom pieces that are not only beautiful but also durable and practical.
Setting Up and Operating a CNC Router
Setting up and operating a CNC router for furniture making involves several important steps to ensure that the machine runs efficiently, safely, and with precision. From preparing your workspace to understanding how to load materials and adjust settings, this section will guide you through the necessary steps for a successful CNC routing experience.
Preparing the Workspace
Before starting, make sure your workspace is set up for both safety and efficiency. Here’s what to keep in mind:
- Adequate Space: Ensure that there is enough space around the CNC router to move freely, handle large pieces of material, and access all controls.
- Ventilation and Dust Control: CNC routers can generate a lot of dust and debris, especially when cutting wood or composite materials. Install a dust collection system to prevent the accumulation of sawdust and maintain air quality.
- Stable Foundation: Place the CNC router on a level, stable surface to ensure that the machine operates correctly. Vibrations or an uneven base can affect cutting accuracy.
Securing the Material
Proper material setup is beneficial to ensure accurate cuts and prevent any movement during the machining process. Here are some tips for securing your material:
- Vacuum Table or Clamps: Many CNC routers are equipped with a vacuum table that holds the material in place using suction. If your router doesn’t have one, use mechanical clamps or a combination of both to secure the workpiece.
- Material Size and Positioning: Measure and position the material on the table so that it aligns with the design and cutting path. Double-check dimensions to avoid material waste or mistakes in cutting.
- Ensure Flatness: Ensure that the material is flat against the table to avoid uneven cuts. Warped or bowed materials may result in inaccurate measurements or cuts.
Selecting and Installing the Cutting Tool
Choosing the right cutting tool is beneficial for achieving clean, precise cuts. Different materials and designs may require different types of bits. Here’s how to choose and install the appropriate tool:
- Tool Selection: Select the appropriate cutting bit or tool based on the material type (wood, plastic, metal) and the type of cut (engraving, carving, profiling).
- Tool Installation: Ensure the tool is properly secured in the spindle. Tighten it to prevent any movement or vibration during operation, which could affect the quality of the cuts.
Setting Machining Parameters
Setting the right parameters is beneficial for ensuring that the CNC router operates at optimal efficiency. Here are some important factors to adjust:
- Feed Rate: This refers to the speed at which the tool moves through the material. Too fast, and the tool may chatter or burn the material. Too slow, and the cutting process will be inefficient. Refer to the manufacturer’s recommendations or test cuts to find the optimal feed rate.
- Spindle Speed: This controls the speed at which the cutting tool spins. For softwoods, a higher speed may work well, but harder materials may require a slower speed to avoid overheating or tool damage.
- Cutting Depth: Set the depth of each cut based on the material and the tool. Shallow cuts reduce stress on the machine and tool but may require multiple passes for thicker materials.
- Passes & Stepovers: For deep cuts, it’s often better to make several shallow passes rather than one deep cut. Similarly, setting an appropriate stepover can result in smoother finishes.
Loading and Running the CNC Router Program
Once the material is secured and the tool is installed, it’s time to load your design and start the CNC router:
- CAD/CAM Software: Before running the CNC router, you need a digital design of the furniture piece. Use CAD software to create or modify your design, then convert the file to a format that the CNC router can understand.
- Upload to Controller: Transfer the design file to the CNC router’s controller. Make sure that the file is correctly formatted and all paths are set up for cutting.
- Zeroing the Machine: Ensure the CNC router is properly calibrated by zeroing the machine.
- Running a Test Cut: It’s always recommended to run a test cut on scrap material before beginning the actual project.
Monitoring the Process and Troubleshooting
While the CNC router is running, it’s important to monitor its performance and check for any issues that could arise. Here are some tips:
- Listen for Unusual Sounds: Pay attention to any strange noises (such as grinding or chattering) that may indicate the machine is under stress. If this happens, stop the machine and check the setup.
- Watch for Material Movement: Ensure that the material remains securely in place during the cutting process. Any movement can cause inaccuracies or misalignments.
- Check Tool Wear: If the tool becomes dull or damaged, it may cause poor cutting quality or even break. Replace or sharpen the tool as necessary.
Setting up and operating a CNC router may seem complex, but by following the proper steps and taking time to understand the equipment and settings, you can achieve precise, high-quality custom furniture. From workspace preparation to running your program and performing post-cutting procedures, mastering these techniques will help you maximize the potential of your CNC router and create exceptional furniture pieces.
CNC Techniques for Furniture Making
CNC routers can create complex designs that are difficult or time-consuming to accomplish using traditional methods. Below are some of the most common CNC techniques used in custom furniture making, each contributing to the efficiency, detail, and quality of the final product.
Cutting
Cutting is one of the most fundamental CNC techniques used in furniture making. CNC routers allow for fast, precise cuts that are consistent across multiple pieces, ensuring uniformity and accuracy in large or complex designs.
- Straight Cuts: These are basic cuts along the X, Y, or Z axes. They are used for cutting material sheets into smaller sections, such as cutting a plywood sheet into a table top or drawer faces.
- Curved Cuts: CNC routers can cut intricate curved shapes, which are ideal for creating unique, custom furniture pieces like chairs, table legs, and decorative panels.
- Profiling: Profiling is used to create edges with a specific shape or pattern. This technique is often used on furniture like cabinets, desks, and shelves, where the edges are designed to be visually appealing.
Engraving and Carving
Engraving and carving are advanced CNC techniques that allow for intricate designs and detailed artwork to be incorporated into furniture. These techniques are often used for decorative elements such as logos, patterns, and textures.
- Engraving: CNC routers can precisely carve designs onto the surface of materials such as wood, plastic, or metal. This technique is often used to add decorative features like intricate patterns, brand logos, or personalized engravings on furniture like headboards, tabletops, or doors.
- 3D Carving: This technique involves creating three-dimensional designs by gradually removing material in multiple passes. It’s particularly useful for adding sculptural elements to furniture, such as ornate designs on cabinet doors or the intricate carving of chair backs.
Joinery
Joinery is a key component of furniture construction, ensuring that the various pieces of a project fit together securely and accurately. CNC routers excel at producing precise joints with minimal effort, allowing for strong, repeatable connections.
- Dovetail Joints: Used in drawers and cabinets, dovetail joints are one of the most common types of joinery that CNC routers can create with high precision. These interlocking joints provide strength and an aesthetically pleasing look.
- Mortise and Tenon Joints: A classic woodworking joint used for furniture like chairs, tables, and frames. The CNC router can accurately cut the mortise (the hole) and the tenon (the protruding piece) to ensure a tight fit.
- Finger Joints: These interlocking joints are often used for joining smaller pieces of wood into a longer piece, such as in the construction of table legs or decorative panels. CNC routers allow for precise cutting, resulting in stronger, seamless joints.
Inlaying and Laminating
Inlaying and laminating are techniques that combine multiple materials or patterns to create unique, detailed furniture pieces. CNC routers can execute these techniques with high precision, allowing for more complex designs.
- Inlaying: Inlaying is the process of inserting one material into a recess in another. CNC routers are used to cut precise grooves and cavities for the inlay material (such as metal, resin, or wood). Common uses include adding decorative wood inlays to table surfaces or inserting metal accents into chair frames.
- Laminating: CNC routers can cut laminated surfaces for furniture like countertops, tabletops, and cabinet doors. Lamination allows multiple layers of material to be bonded together to achieve greater strength, a smooth finish, or aesthetic effects. The CNC machine can precisely cut these layers for a perfect fit.
Finishing Operations
While finishing is typically done by hand, CNC routers can also assist in certain finishing operations, ensuring a clean and polished appearance. These techniques include smoothing rough edges, sanding, and polishing the surface.
- Edge Profiling and Rounding: CNC routers can perform edge profiling to create smooth, aesthetically pleasing finishes on all exposed edges of a piece.
- Sanding: Some advanced CNC machines can be fitted with sanding attachments to remove surface imperfections, ensuring a smoother finish before the final coating or treatment.
CNC routers offer a broad range of techniques that enhance the creativity, precision, and efficiency of custom furniture making. Whether you are cutting, engraving, carving, or doing surface treatment, these advanced machines allow furniture makers to achieve high-quality, intricate designs with consistency. By mastering these CNC techniques, you can transform raw materials into beautiful, functional, custom furniture.
Advantages and Challenges of CNC Furniture Making
CNC routers have transformed the furniture-making industry by allowing for high precision, faster production times, and the ability to create complex, custom designs. However, as with any technology, CNC furniture-making comes with both significant advantages and potential challenges.
Advantages of CNC Furniture Making
- Precision and Consistency: CNC routers excel at delivering extremely accurate cuts and shapes, ensuring that every piece of furniture is made with consistent quality. The digital design files control the process, meaning that all parts of a project will be identical, making it easy to replicate designs for batch production.
- Increased Production Speed: CNC machines operate faster than traditional hand tools, significantly reducing production time. This makes them ideal for larger-scale furniture production.
- Complexity and Creativity: With a CNC router, furniture makers can easily create intricate, complex designs that would be difficult or impossible to achieve by hand. Whether it’s detailed carvings, complex curves, or precise joinery, CNC routers can handle sophisticated designs with ease.
- Reduced Labor Costs: While CNC routers require skilled operators to set up and maintain, they can reduce the need for extensive manual labor. Since the machine is automated, it can perform repetitive tasks efficiently without tiring, which leads to cost savings in terms of labor.
- Customization and Flexibility: One of the greatest advantages of CNC furniture making is the ability to easily create custom, one-of-a-kind pieces. Whether you’re making furniture to fit a specific space or designing unique pieces for clients, CNC routers make customization a simple and cost-effective process.
Challenges of CNC Furniture Making
- Initial Investment Costs: One of the most significant challenges of CNC furniture making is the upfront cost of the equipment. High-quality CNC routers can be expensive, particularly those with advanced features or larger cutting capacities.
- Learning Curve and Skill Requirements: While CNC routers automate many aspects of the furniture-making process, they still require skilled operators to set up, program, and manage the machines. Additionally, troubleshooting and machine calibration require technical expertise.
- Tool Wear and Replacement Costs: Just like any high-precision machine, CNC routers require regular tool changes and maintenance. The costs of replacing worn tools can add up, especially for businesses that produce large quantities of furniture or work with particularly hard materials.
- Space Requirements: CNC routers, particularly larger industrial models, require significant floor space to operate. This can be a challenge for small businesses or home-based workshops, as the machine’s size, combined with the need for materials and storage, can take up a considerable amount of room.
CNC routers offer significant advantages in furniture making, including enhanced precision, increased production speed, and the ability to create complex, custom designs. However, challenges such as initial costs, workshop size, and the need for skilled operators should be considered when deciding whether to adopt CNC technology. With careful planning and proper use, CNC routers can significantly enhance the capabilities of furniture makers and open up new possibilities for creativity and efficiency.
Application of CNC Router in Custom Furniture Manufacturing
CNC routers have a wide range of applications in custom furniture manufacturing, with the ability to create high-quality, unique, and functional pieces for various sectors. From residential to commercial settings, as well as in artistic and outdoor furniture designs, CNC routers enhance both the functionality and aesthetics of the final products.
Residential Furniture
CNC routers are widely used in the creation of custom residential furniture, offering precision in cutting, shaping, and detailing unique pieces such as dining tables, cabinets, and shelving units. They allow for personalized designs, ensuring that each piece fits perfectly into specific spaces and meets the client’s aesthetic preferences. The ability to carve intricate patterns, create custom joinery, and optimize material usage makes CNC routers ideal for producing high-quality, one-of-a-kind furniture for homes.
Commercial Furniture
In commercial furniture manufacturing, CNC routers streamline production by enabling the creation of high-quality, durable, and custom furniture for office spaces, restaurants, hotels, and retail environments. These machines can quickly and accurately cut and shape materials like plywood, laminate, and metal, ensuring uniformity and efficiency in mass production. CNC routers also allow for customization, whether it’s for branded designs, functional features, or tailoring pieces to fit specific business needs.
Art Furniture
CNC routers allow designers to push the boundaries of creativity, producing intricate 3D carvings, sculptural elements, and customized inlays that would be difficult to achieve by hand. CNC technology enhances the ability to create unique, statement pieces that reflect the artist’s vision, providing precision in crafting elaborate details, abstract forms, and personalized designs for one-of-a-kind furniture pieces.
Outdoor Furniture
For outdoor furniture, CNC routers offer the precision necessary to create durable and weather-resistant pieces from materials like treated wood, aluminum, and composite plastics. These machines ensure that custom designs for patios, garden benches, and outdoor tables are not only functional but also aesthetically pleasing, with precise cuts and ergonomic shapes.
From residential furniture that fits perfectly into living spaces, to commercial furniture that meets the demands of businesses, to art furniture that pushes the boundaries of creativity, CNC routers enhance precision, reduce production times, and enable complex designs. They also allow for customization in outdoor furniture, ensuring durability and comfort in harsh environments. Whether for a single custom piece or mass production, CNC routers provide furniture manufacturers with the tools to meet diverse needs and deliver exceptional results.
Summarize
CNC routers have fundamentally transformed the way custom furniture is made, offering unparalleled precision, speed, and design flexibility. By enabling highly detailed cuts, intricate carvings, and seamless joinery, CNC routers create bespoke, high-quality furniture. Although the initial investment may seem substantial, the long-term benefits in terms of reduced labor costs and increased production capabilities make CNC routers a valuable tool for anyone looking to elevate their custom furniture business. Continue reading “CNC Router Safety Operation Guide” and you can get tips on using the machine correctly.
AccTek CNC stands out as a professional manufacturer of high-quality CNC routers, offering state-of-the-art technology that aligns perfectly with the needs of custom furniture makers. With a range of customizable features and excellent customer support, AccTek CNC is the ideal choice for anyone seeking to elevate their custom furniture manufacturing process. If you’re looking to enhance your furniture production with precision and creativity, consult now and you will receive a free machine customization plan.