- 11-16 Min Read
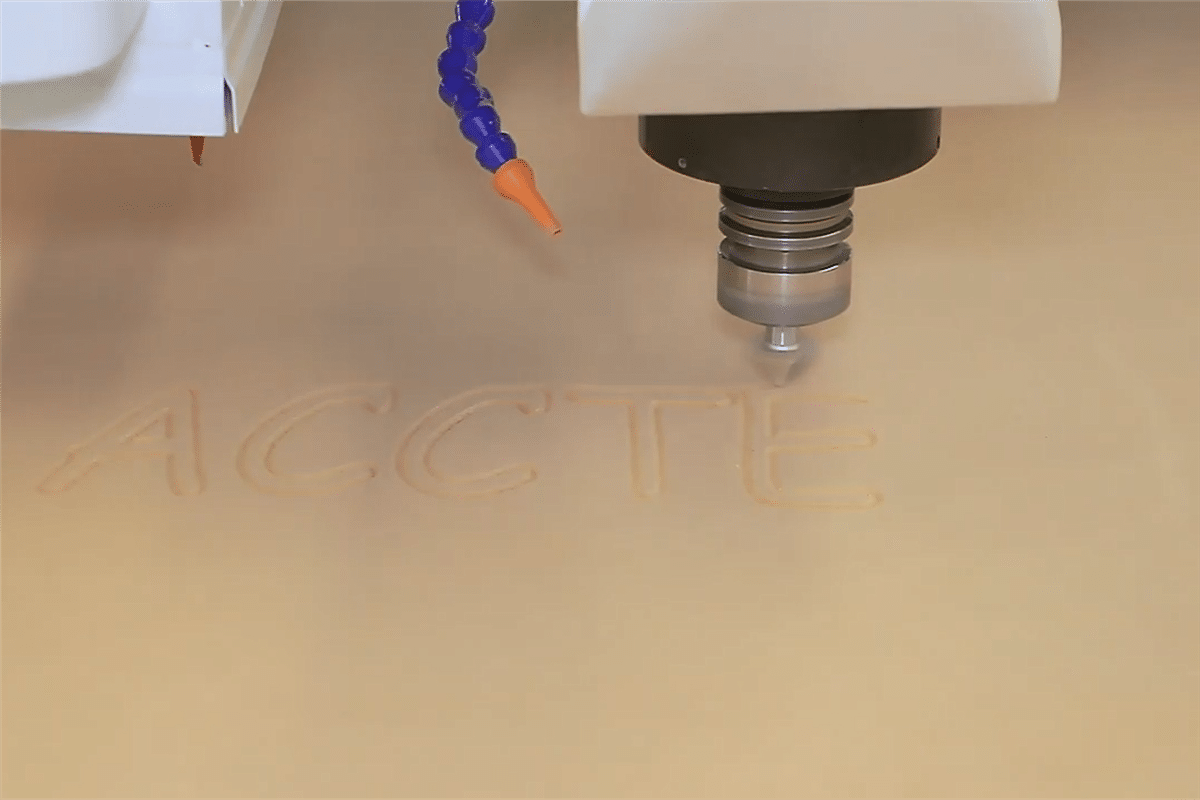
In the world of modern manufacturing, Computer Numerical Control (CNC) technology has revolutionized the way we create intricate designs and prototypes. Among the diverse array of CNC machines, the CNC router emerges as a versatile tool, capable of transforming digital designs into tangible creations with remarkable accuracy. However, amidst the intricate web of technologies that govern the manufacturing process, a common question often arises: Is the CNC router a product of Computer-Aided Design (CAD) or Computer-Aided Manufacturing (CAM)? This question serves as a gateway to understanding the intricate relationship between design and production in the world of CNC machining. In this comprehensive article, we will delve deep into the functionalities of CNC routers, elucidating how they bridge the gap between CAD and CAM processes.
What is a CNC Router?
Before delving into its association with CAD or CAM, let’s first understand what a CNC router is. Essentially, a CNC router is a computer-controlled cutting machine that utilizes a rotating cutting tool to carve out designs from various materials such as wood, plastic, metal, and composites. These machines are equipped with precision motors that move the cutting tool along multiple axes, enabling intricate and accurate cuts according to predefined specifications. CNC routers are widely used in industries such as furniture, advertisement, musical instruments, and manufacturing, offering high precision, repeatability, and automation in the cutting process. They are an essential component of modern manufacturing, allowing for the efficient production of complex shapes and designs with minimal manual intervention.
CAD: The Blueprint of Design
In the dynamic landscape of modern design and engineering, CAD stands as a pivotal tool, reshaping the way we conceptualize, refine, and bring ideas to fruition. From exquisite wood carving patterns to complex musical instrument structures, CAD technology empowers designers to create precise digital representations that serve as the foundation for innovation and production. In this section, we will explore CAD from three distinct perspectives:
Definition and Purpose of CAD
CAD, short for Computer-Aided Design, refers to the use of computer software to facilitate the creation, modification, analysis, or optimization of design concepts. At its core, CAD serves as a digital drafting board, allowing users to transform ideas into detailed and accurate 2D or 3D models. Whether designing architectural structures, mechanical parts, electronic circuits, or artistic creations, CAD software provides the tools necessary to visualize, iterate, and refine designs with precision.
The primary purpose of CAD is to streamline the design process, enabling designers and engineers to explore concepts, test feasibility, and communicate ideas effectively. By leveraging CAD technology, professionals can produce comprehensive digital models that serve as blueprints for manufacturing, construction, prototyping, and visualization. CAD software not only accelerates the design iteration cycle but also enhances collaboration among multidisciplinary teams, driving innovation and efficiency in various industries.
Software Options for CAD
The landscape of CAD software is vast and diverse, offering solutions tailored to the specific needs and preferences of users across different industries. From industry-leading suites with comprehensive toolsets to specialized applications focused on niche markets, the options for CAD software abound. Some of the prominent CAD software options include:
- AutoCAD: Developed by Autodesk, AutoCAD is one of the most widely used CAD programs, known for its versatility and extensive feature set. It caters to various disciplines, including architecture, engineering, and construction, offering 2D drafting and 3D modeling capabilities.
- SolidWorks: SolidWorks is a parametric CAD software designed primarily for mechanical engineering and product design. It facilitates the creation of 3D models with robust simulation and analysis tools, fostering innovation and optimization in product development.
- Fusion 360: Fusion 360 is a cloud-based CAD/CAM platform that integrates design, engineering, and manufacturing workflows. It offers collaborative tools, advanced modeling capabilities, and CAM functionality, making it suitable for startups, hobbyists, and professional designers alike.
- SketchUp: SketchUp is a user-friendly CAD software known for its intuitive interface and accessibility. It caters to architects, interior designers, and hobbyists, enabling rapid prototyping and conceptualization of architectural and spatial designs.
These are just a few examples of the diverse CAD software options available, each with its unique features, strengths, and applications.
Key CAD Functions in CNC Routing
Within the realm of CNC routing, CAD plays a key role in generating the digital models that serve as the foundation for manufacturing processes. The key functions of CAD in CNC routing include:
- Design Creation: CAD software allows users to create detailed 2D or 3D models of the desired components, parts, or products to be fabricated using CNC routers. Designers can define dimensions, shapes, geometries, and features with precision, ensuring accuracy in the final output.
- Model Modification: CAD enables designers to iterate upon and refine their designs based on feedback, requirements, or constraints. Whether adjusting dimensions, altering geometries, or adding intricate details, CAD software provides the flexibility to modify models efficiently.
- File Export: CAD software allows users to export digital models in various file formats compatible with CNC routers. Common formats include DXF (Drawing Exchange Format) and DWG (AutoCAD Drawing), which contain the necessary geometric information and instructions for CNC machining.
By leveraging these key functions of CAD, designers can create digital models optimized for CNC routing, laying the groundwork for precise and efficient manufacturing processes.
CAM: Transforming CAD into Reality
Once the design is finalized in the CAD environment, the CAM phase comes into play to translate the digital model into actionable instructions for the CNC machine. CAM software bridges the gap between design and production by generating toolpaths and machining strategies optimized for CNC operations. In this section, we will explore CAM from three distinct perspectives:
Definition and Purpose of CAM
CAM, short for Computer-Aided Manufacturing, refers to the use of computer software to generate instructions for automated manufacturing processes. It acts as the intermediary between CAD models and the machines responsible for fabricating physical objects. CAM software translates digital designs, typically created in Computer-Aided Design (CAD) software, into machine-readable instructions, such as G-code, that control the movements of CNC routers. The primary purpose of CAM is to optimize the manufacturing process by automating tasks, optimizing toolpaths, and maximizing the utilization of resources. By leveraging CAM, manufacturers can achieve higher levels of productivity, accuracy, and consistency in their production workflows, ultimately leading to cost savings and improved quality.
Software Options for CAM
CAM software encompasses a diverse range of applications tailored to specific industries and manufacturing processes. From simple 2D machining to complex multi-axis milling, there are numerous software options available to cater to the diverse needs of manufacturers. Here are some prominent software options for CAM:
- Mastercam: Mastercam is one of the most widely used CAM software packages, offering a comprehensive suite of tools for machining operations, including milling, turning, wire EDM, and more. It provides advanced features for toolpath creation, simulation, and optimization, making it suitable for industries such as aerospace, automotive, and mold making.
- Fusion 360 CAM: Fusion 360, developed by Autodesk, is a cloud-based CAD/CAM platform that integrates design and manufacturing workflows seamlessly. Its CAM capabilities include 2.5-axis to 5-axis machining, adaptive clearing, and simulation tools. Fusion 360 CAM is popular among startups, hobbyists, and small to medium-sized businesses due to its affordability and ease of use.
- SolidCAM: SolidCAM is a CAM software solution integrated within the SolidWorks environment, providing users with a seamless workflow from CAD to CAM. It offers a wide range of machining strategies, including milling, turning, and wire EDM, with features such as iMachining for high-speed machining and advanced simulation capabilities.
- CAMWorks: CAMWorks is an intuitive CAM software solution that operates directly within SolidWorks, providing users with a familiar interface for programming CNC machines. It offers automatic feature recognition, knowledge-based machining, and advanced simulation tools, streamlining the programming process and reducing machining times.
- BobCAD-CAM: BobCAD-CAM is a user-friendly CAM software package that caters to a wide range of industries, including manufacturing, woodworking, and 3D printing. It offers 2D and 3D machining capabilities, along with features such as nesting, engraving, and simulation, making it suitable for both beginners and experienced users.
These are just a few examples of the many CAM software options available on the market today. When choosing CAM software, it’s essential to consider factors such as the specific machining requirements, compatibility with existing CAD systems, ease of use, and support and training options provided by the software vendor.
Key CAM Functions in CNC Routing
In the context of CNC routing, CAM software plays a pivotal role in transforming digital designs into precise cutting instructions for CNC routers. Some key functions performed by CAM software in CNC routing include:
- Toolpath Generation: CAM software generates toolpaths based on the geometry of the CAD model and machining parameters specified by the user. These toolpaths define the trajectory of the cutting tool as it moves across the workpiece, ensuring optimal material removal while minimizing machining time and tool wear.
- Material Optimization: CAM software allows users to optimize material usage by nesting parts efficiently within the available stock material. By arranging parts close and minimizing waste, manufacturers can reduce material costs and maximize the yield from each raw material sheet.
- Machining Strategies: CAM software provides a range of machining strategies tailored to specific cutting tasks and material types. These strategies include contouring, pocketing, profiling, engraving, and drilling, among others. Users can achieve the desired surface finish, dimensional accuracy, and production efficiency by selecting the appropriate machining strategy and parameters.
CAD to CAM Workflow
The CAD to CAM workflow in a CNC router involves several key steps to translate a digital design into machine-readable instructions for the CNC router to follow. Let’s explore the CAD to CAM workflow in CNC routing:
CAD Design Phase
The CAD design phase is where the digital model or blueprint of the desired part or product is created using CAD software. This phase involves the following steps:
- Design Creation: Designers use CAD software to create 2D or 3D models of the product they intend to manufacture with the CNC router. They define dimensions, shapes, features, and any other relevant parameters.
- Dimensioning and Detailing: Designers add detailing, dimensions, features, and other necessary information to the CAD model to ensure clarity and accuracy in the manufacturing process.
- File Export: Once the design is finalized, designers export the CAD model in a format compatible with CAM software. Common file formats for CNC routing include DXF (Drawing Exchange Format) and DWG (AutoCAD Drawing).
CAM Programming Phase
In the CAM programming phase, the digital CAD model is translated into machine-readable instructions (G-code) for the CNC router. This phase involves the following steps:
- Importing CAD Files: CAM software imports the CAD files, allowing users to work directly with the digital model.
- Toolpath Generation: CAM software generates toolpaths based on the CAD model and machining parameters defined by the user. Toolpaths define the precise movements of the cutting tool (router bit) as it traverses the material to carve out the desired shapes.
- Setting Machining Parameters: Machining parameters such as cutting speeds, feed rates, tool selection, and depth of cut are specified based on material properties and desired outcomes.
- Simulation and Verification: Before proceeding to the actual machining process, CAM software allows users to simulate and verify the toolpaths to ensure they are free from errors, collisions, and other issues. Simulation helps optimize machining strategies and minimize the risk of scrap or rework.
- Post-Processing: Once the toolpaths are finalized, CAM software generates the G-code, which contains the instructions for the CNC router. This G-code is specific to the machine configuration and controller used and may require post-processing to ensure compatibility and optimization.
CNC Machining Phase
With the CAM programming completed, the G-code is transferred to the CNC router, and the machining process begins. This phase involves the following steps:
- Loading G-code: The generated G-code is transferred to the CNC router’s controller, either directly or via a USB drive or network connection.
- Workpiece Setup: Operators set up the workpiece on the CNC router’s bed, securing it in place using clamps, vises, or vacuum fixtures.
- Tool Setup: The appropriate cutting tool is installed in the CNC router’s spindle, and tool offsets are set to ensure accurate machining.
- Executing Machining Operations: The CNC router executes the programmed toolpaths, precisely moving the cutting tool along the designated paths to cut, carve, or engrave the workpiece according to the CAD design.
- Monitoring and Quality Control: Operators monitor the machining process to ensure proper operation, adjust settings as needed, and inspect the quality of machined parts.
Finishing and Post-Processing
- Surface Finishing: After machining, additional finishing operations such as sanding, polishing, or painting may be performed to achieve the desired surface finish.
- Deburring: Sharp edges or burrs resulting from machining operations are removed to ensure a clean and smooth final product.
- Assembly (if applicable): Machined parts may be assembled with other components to complete the final product.
Throughout the CAD to CAM workflow in a CNC router, attention to detail, precision, and quality control help ensure the accurate translation of digital designs into physical objects. Manufacturers can optimize efficiency, minimize errors, and achieve superior results in CNC routing operations by following a systematic approach and leveraging advanced CAD and CAM software tools.
Operator Involvement in CAD and CAM
CNC router operators play a multifaceted role in CAD and CAM processes. By leveraging their knowledge, skills, and expertise, operators ensure the efficient and accurate execution of machining operations, translating digital designs into high-quality finished products. Here are three key aspects describing the CNC router operator’s involvement in CAD and CAM:
CNC Operator Role
- Understanding of CAD Designs: While CNC operators may not always be directly involved in CAD design, they must have a fundamental understanding of CAD models and blueprints. This understanding allows operators to interpret design specifications, dimensions, and tolerances, ensuring accurate translation of digital designs into physical parts.
- Interpretation of CAM Instructions: CNC operators are responsible for interpreting CAM instructions generated from CAD models. They must understand the toolpaths, machining parameters, and G-code instructions provided by CAM software to effectively program and operate the CNC router.
- Quality Control and Inspection: Operators are tasked with inspecting machined parts to ensure they meet design specifications and quality standards. This involves verifying dimensions, surface finishes, and geometric tolerances, as well as identifying and addressing any discrepancies or defects in the finished parts.
Programming and Setup Responsibilities
- CAM Programming: CNC operators are often responsible for CAM programming, which involves setting up machining parameters, selecting cutting tools, and generating toolpaths using CAM software. This requires a deep understanding of machining processes, material properties, and tooling requirements to optimize efficiency and quality.
- Toolpath Optimization: Operators must optimize toolpaths generated by CAM software to minimize machining time, reduce tool wear, and maximize material utilization. This involves selecting appropriate cutting strategies, specifying feed rates and spindle speeds, and optimizing tool engagement to achieve optimal machining performance.
- Machine Setup and Calibration: Operators are responsible for setting up and calibrating the CNC router before machining operations. This includes installing cutting tools, setting tool offsets, zeroing reference points, and verifying machine alignments to ensure accurate and reliable operation.
Understanding Tool Requirements
- Tool Selection: CNC operators must have a thorough understanding of cutting tool requirements based on material type, geometry, and machining operations. This involves selecting appropriate tool types, sizes, and coatings to achieve desired surface finishes, dimensional accuracy, and tool life.
- Tool Maintenance: Operators are responsible for maintaining cutting tools in optimal condition to ensure consistent performance and longevity. This includes routine maintenance tasks such as tool sharpening, tool changing, and tool inspection to detect signs of wear or damage.
- Tool Life Monitoring: Operators monitor tool life during machining operations and replace worn or damaged tools as needed to maintain machining efficiency and quality. This involves tracking tool wear, tool breakage, and chip load conditions to optimize tool life and minimize production downtime.
Integration Challenges and Solutions
In the realm of CNC routing, the integration of CAD and CAM processes is key for ensuring seamless translation of digital designs into physical objects. However, this integration often presents challenges that must be addressed to optimize workflow efficiency and quality. In this section, we explore the integration challenges faced by manufacturers in CAD and CAM processes for CNC routers, along with innovative solutions to overcome them.
Data Transmission Issues
- Challenge: One of the primary challenges in CAD-CAM integration is the seamless transmission of design data between CAD and CAM software. Incompatibilities in file formats, version disparities, and data loss during transfer can lead to errors and inconsistencies in machining instructions.
- Solution: Implementing standardized file formats such as STEP or IGES facilitates smooth data exchange between CAD and CAM environments. Additionally, utilizing integrated CAD/CAM software suites or establishing robust data management protocols ensures data integrity and accuracy throughout the workflow.
Consistency from CAD to CAM
- Challenge: Maintaining consistency and accuracy in design specifications from CAD to CAM poses another significant challenge. Discrepancies in geometric dimensions, material properties, or machining parameters between CAD models and CAM instructions can result in deviations from the intended design and compromise the quality of machined parts.
- Solution: Adopting parametric modeling techniques and feature-based CAD/CAM software enables the creation of associative relationships between design elements and machining operations. This ensures that any changes made to the CAD model are automatically propagated to the CAM environment, maintaining consistency and synchronization between the two domains. Additionally, conducting thorough validation and verification checks at each stage of the workflow helps identify and rectify discrepancies early on, minimizing errors and rework downstream.
Seamless Workflow Integration
- Challenge: Effective utilization of integrated CAD/CAM systems in CNC routers requires proficient training and expertise among operators. Lack of familiarity with CAD/CAM software functionalities, insufficient training resources, and resistance to adopting new technologies can hinder the seamless integration of CAD and CAM processes.
- Solution: Implementing collaborative design platforms that facilitate real-time communication and collaboration between CAD designers and CAM programmers streamlines workflow integration. Cross-training operators in CAD and CAM functionalities enhances their understanding of the entire manufacturing process, enabling them to troubleshoot issues and optimize machining operations effectively. Additionally, promoting a culture of continuous learning and providing ongoing support and resources for skill development empower operators to harness the full potential of integrated CAD/CAM systems, driving productivity and innovation in CNC routing operations.
In the ever-evolving landscape of CNC routing, addressing integration challenges and implementing effective solutions for CAD and CAM processes can improve efficiency and accuracy. By overcoming data transmission issues, ensuring consistency from CAD to CAM, and providing seamless integration training for operators, manufacturers can unlock the full potential of integrated CAD/CAM systems in CNC routers, driving innovation and competitiveness in CNC routing operations.
Summarize
The debate over whether a CNC router is primarily a CAD or CAM product reveals the intricate relationship between design and production in modern manufacturing processes. It is evident that both CAD and CAM are integral components of the CNC machining workflow, working in tandem to bring digital designs to life in physical form. Rather than viewing CNC routers strictly through the lens of CAD or CAM, it is more accurate to recognize them as a convergence of both disciplines, each contributing essential elements to the overall manufacturing process. As technology continues to advance, the synergy between CAD and CAM will only strengthen, further blurring the distinction between the two and emphasizing the importance of an integrated approach in modern manufacturing.
As a professional CNC router manufacturer and seller, AccTek CNC is committed to providing our customers with not only high-quality machines but also valuable knowledge-sharing resources. Therefore, we highly recommend that you bookmark our official website: www.acctekcnc.com. By doing so, you will have convenient access to our latest news, updates, and insights at any time. Thank you for choosing AccTek CNC as your trusted partner in CNC machining. We look forward to serving you and supporting your manufacturing needs now and in the future.