- 8-12 Min Read
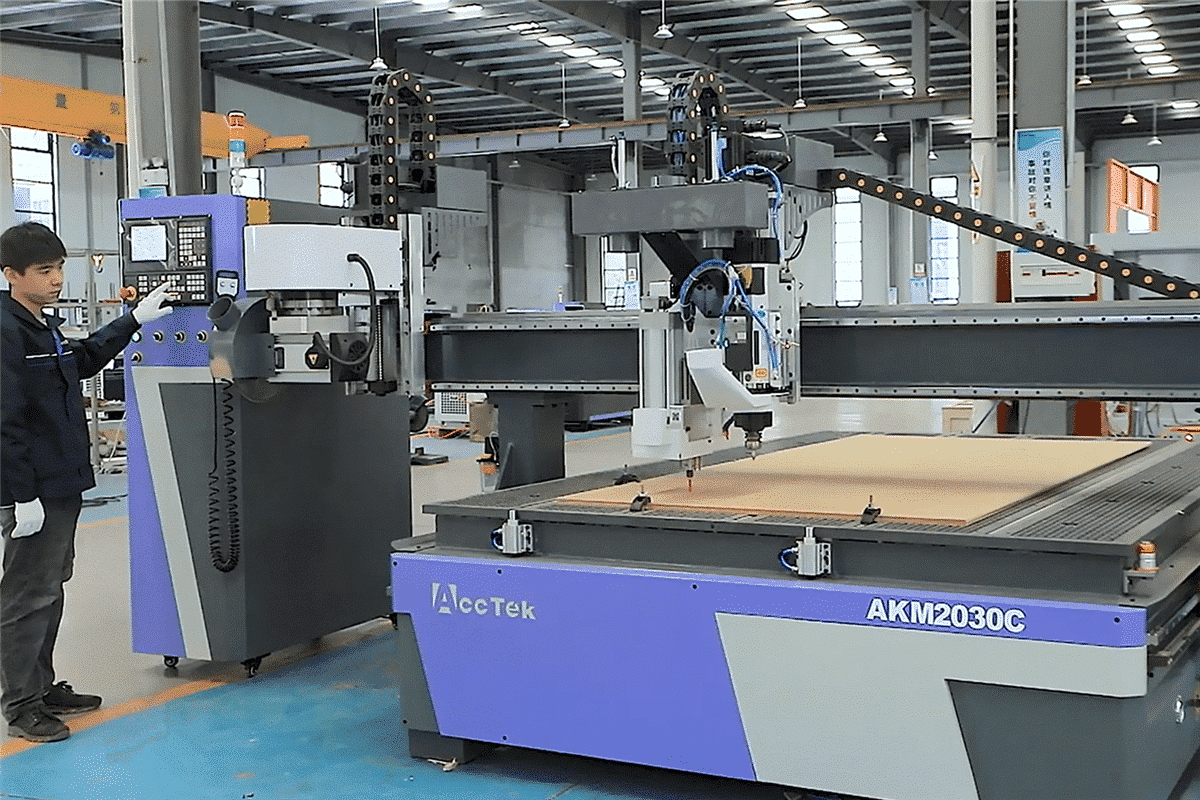
CNC routers have become a cornerstone of modern manufacturing, enabling precise, efficient, and automated production across various industries. Whether you’re an aspiring hobbyist or a professional looking to enhance your skills, understanding CNC routers can open new doors. However, many beginners wonder: Is it challenging to learn how to operate a CNC router?
The answer depends on several factors, including your technical background, familiarity with software, and the specific projects you plan to undertake. In this article, we’ll explore what it takes to learn CNC router operation, breaking down the skills involved, the learning curve, and how beginners can handle the learning challenges. By the end, you’ll have a clear idea of whether mastering CNC technology is within your reach and how you can set yourself up for success.
Understanding CNC Router
With automated cutting and the ability to replicate designs with minimal error, CNC routers save time and labor, making them ideal for both industrial use and DIY enthusiasts. Whether you’re considering investing in one or are simply curious about how they work, understanding CNC routers is the first step toward unlocking their full potential.
Introduction to CNC Router
A CNC (Computer Numerical Control) router is a computer-controlled cutting machine used for precise and automated material shaping. Unlike traditional tools, CNC routers follow pre-programmed designs to carve or engrave materials such as wood, plastic, metal, foam, and composites. They are widely employed in industries like furniture manufacturing, signage production, and prototyping, providing high precision and efficiency for complex tasks. Key components of a CNC router include:
- Control System: CNC routers are controlled by computer programs that translate designs into specific tool movements. These programs are typically created using computer-aided design (CAD) and computer-aided manufacturing (CAM) software.
- Spindle: The spindle is the motorized component that rotates the router bit. It is responsible for the actual cutting or carving of the material. Spindles can have different power ratings depending on the materials they are intended to cut.
- Worktable: The worktable is the surface on which the material to be cut is placed. It can be an aluminum flatbed or a vacuum table that holds the material securely in place during the cutting process.
- Drive System: CNC routers use various drive systems to move the cutting tool precisely along the X, Y, and Z axes. Common drive systems include ball screws, lead screws, or rack and pinion systems.
Basics of CNC Machining
CNC machining refers to the broader concept of using automated machine tools to shape and fabricate parts based on computer instructions. Understanding the basics of CNC machining is beneficial for using a CNC router effectively. Key concepts include:
- G-code: The programming language used to instruct the CNC machine on how to move, cut, and perform other operations. Learning to read or generate G-code is beneficial to operate CNC routers efficiently.
- Axis control: CNC routers typically operate on three primary axes—X (left to right), Y (front to back), and Z (up and down). Advanced models may have additional axes for more complex machining.
- Toolpaths: The path followed by the cutting tool during operation. A well-optimized toolpath ensures faster machining with minimal wear on tools.
- Material compatibility: Different settings are required for cutting various materials, such as adjusting spindle speed, feed rate, and cutting depth based on material type and thickness.
- CAM software: Computer-Aided Manufacturing (CAM) software translates designs from CAD (Computer-Aided Design) programs into G-code, automating the programming process and ensuring accuracy.
Mastering these basic concepts is the first step for you to operate CNC routers. To use CNC routers for efficient production, you still need to achieve it through practice and continuous learning.
Technical Skill Development for CNC Routers
Mastering CNC router operation involves developing skills in three critical areas: setup and calibration, tool and workholding techniques, and proficiency with CAD/CAM software. These skills ensure smooth operation, precise machining, and high-quality results.
CNC Router Setup and Calibration
Setting up and calibrating a CNC router ensures precision and smooth operation. Learning these processes ensures the CNC router performs efficiently and minimizes errors.
- Machine Setup: Begin by placing the CNC router on a stable surface and ensuring the worktable is level to minimize vibrations. Connect the control system and power supply, then test the CNC router’s movement along the X, Y, and Z axes to verify smooth motion without obstructions.
- Axis Calibration: Verify the X, Y, and Z axes are properly aligned to avoid dimensional inaccuracies. Use dial indicators or alignment tools to verify that each axis moves correctly and without deviation. If necessary, adjust the screws or linear rails to fine-tune the alignment.
- Spindle and Tool Calibration: Install the tool securely in the spindle and adjust the spindle speed according to the material’s requirements. Perform a test cut to confirm the accuracy of the toolpath before starting production and make any necessary adjustments to avoid material waste or tool wear.
Tool and Workholding Techniques
The quality of the finished product depends heavily on selecting the right tools and securing the material properly on the worktable. Developing proper tools and workholding techniques improves safety, ensures precision, and enhances productivity.
- Tool Selection: Choose cutting tools based on the material and the desired finish, such as end mills for metals, spiral router bits for wood, or V-bits for engraving. Selecting tools with appropriate coatings, like carbide or titanium, can extend tool life and improve cutting efficiency by reducing friction and wear.
- Tool Maintenance: Tools should be inspected regularly for wear, chips, or dull edges and replaced or re-sharpened as necessary. Keeping tools clean prevents performance issues. Additionally, storing tools in a dry, organized environment protects them from corrosion and accidental damage, ensuring they are ready for use when needed.
- Workholding Techniques:Use clamps, vacuum tables, or double-sided tape to secure materials firmly. Ensure that the workpiece is flat and doesn’t shift during machining to prevent errors. Sacrificial boards are often used beneath the workpiece to prevent cutting into the machine bed.
CAD/CAM Software Proficiency
CAD and CAM software are key to creating and executing designs. Proficiency in these tools allows users to generate accurate models and efficient toolpaths.
- CAD Software: Tools like AutoCAD, Fusion 360, or SolidWorks allow operators to design parts with precise dimensions, geometries, and tolerances. Mastering CAD software involves learning to create sketches, extrude shapes, and assemble components, ensuring the design meets production requirements.
- CAM Software: CAM software translates CAD models into G-code, the language used to control CNC routers. Programs like Fusion 360, VCarve, or Mastercam allow users to define toolpaths, set spindle speeds, feed rates, and cutting depths. Users also need to run simulations to detect potential issues and validate that the toolpaths will perform correctly during production.
- Design-to-Production Workflow: Understand how to transfer files between CAD, CAM, and the CNC router seamlessly. Operators must manage file formats (like DXF, STEP, or STL) and ensure compatibility between software and hardware. Adjust designs and toolpaths as needed for revisions or different materials.
Developing skills in these three areas equips CNC router users with the knowledge needed for efficient and precise operations. As these skills improve over time, operators will be better prepared to handle complex projects, troubleshoot issues, and achieve consistent, high-quality results.
Programming and Operation for CNC Routers
Programming CNC routers involves using G-code and M-code, which control the movements and operations of the machine. By mastering both G-code programming and the hands-on operation of CNC routers, users can ensure precise, efficient, and safe machining. Here are the specific steps:
G-Code Programming Points
G-code is the primary language used to control CNC routers, defining every movement and operation. Operators must understand key commands.
- Understand Coordinate Systems: Familiarize yourself with CNC router coordinate systems, including absolute (G90) and incremental (G91) modes, to control movements precisely.
- Define Toolpaths with Basic G-Codes: Use key G-codes like G00 for rapid movement, G01 for linear cuts, and G02/G03 for clockwise and counterclockwise arcs.
- Set Speeds and Feed Rates: Specify spindle speed (S command) and feed rate (F command) based on material and tool requirements to ensure optimal cutting conditions.
- Add Tool Changes and Offsets: Use T-codes for tool changes and apply tool length offsets (G43) to accommodate tool variations and ensure accuracy.
- Write M-Codes for Auxiliary Functions: Program M-codes to manage operations like turning the spindle on/off (M03/M05) or controlling coolant (M08/M09) as needed.
- Simulate the Code in CAM Software: Run simulations to detect potential issues before transferring the code to the machine for machining.
Machine Operation and Monitoring
Operating a CNC router involves loading the G-code, setting the toolpath, and positioning the material accurately on the worktable. Additionally, continuous monitoring during operation helps ensure the tool performs correctly.
- Load the G-Code and Prepare the Machine: Transfer the G-Code to the CNC router’s control system and ensure the machine is powered on and initialized.
- Set the Workpiece and Tool Properly: Secure the material using clamps or vacuum tables and install the correct tool in the spindle, ensuring it is tightly fastened.
- Perform a Dry Run: Run the program without material (dry run) to verify that the toolpath works as expected and check for any collisions or errors.
- Check Zero Points and Tool Offsets: Calibrate the machine’s X, Y, and Z axes, ensuring the tool’s starting position matches the program’s reference point.
- Monitor the Machining Process: Start the operation and monitor the CNC router to detect tool wear, overheating, or material shifting. Pause the machine if adjustments are needed.
- Ensure Safety and Efficiency: Follow safety protocols, such as wearing protective gear and keeping the area clear, to prevent accidents during operation.
- Evaluate the Output and Perform Maintenance: Inspect the finished part for quality, clean the work area, and maintain tools and machine components for future operations.
By combining precise G-code programming with efficient operation and monitoring, CNC router users can achieve high-quality results while minimizing errors and downtime.
Practical Applications and Projects of CNC Routers
CNC routers empower users to create intricate designs and functional products with speed and consistency. Whether for practical training or advanced specialization, CNC routers open doors to a wide range of applications and innovative projects, serving both beginners and professionals across different fields.
Practical Training and Practice
Practical training with CNC routers involves hands-on experience to build foundational skills. Beginners typically start with small projects, such as creating personalized nameplates, cutting basic furniture components, or engraving simple designs. These initial tasks develop familiarity with setting up machines, selecting tools, and managing software.
Educational institutions and training centers often use CNC routers to teach students about machining principles through projects like crafting cutting boards, signs, or prototypes. As learners progress, they gain confidence in handling more complex materials and operations, preparing them for real-world applications in manufacturing, woodworking, and fabrication.
Advanced Technology and Specialization
Advanced CNC router applications involve using specialized tools and technology for high-precision and customized projects. In specialized fields, 5-axis CNC routers allow for complex 3D sculpting, while advanced toolpaths maximize precision and efficiency.
Customized CAM software is also used to handle unique production challenges, such as micro-machining or large-format fabrication. Projects in this realm include producing complex furniture, creating molds for industrial use, and developing prototypes for consumer products. Mastery of these advanced tools and methods enables professionals to push the limits of CNC technology for innovation and industrial excellence.
The versatility of CNC routers makes them invaluable tools in both learning environments and specialized industries. Through hands-on practice, users can build essential skills, while advanced technologies enable professionals to explore new creative and manufacturing possibilities. Whether crafting simple wooden signs or developing complex industrial prototypes, CNC routers provide a platform for continuous learning and innovation.
Overcoming Challenges and Pitfalls in CNC Router Operation
While CNC routers offer immense versatility and precision, mastering their use comes with a unique set of challenges. Identifying and overcoming these challenges is beneficial to ensure smooth operations, minimize downtime, and improve production efficiency.
Common Barriers to Learning CNC
Learning to operate CNC routers can feel overwhelming due to the technical nature of programming, machine setup, and tool selection. Beginners often struggle with understanding G-code, mastering CAD/CAM software, and troubleshooting machine errors. To overcome these barriers, it’s essential to start with small, manageable projects and gradually increase the complexity as confidence grows.
Hands-on practice reinforces theoretical knowledge, and beginners should embrace trial and error as part of the learning curve. Breaking tasks into steps, such as focusing first on machine setup, and then progressing to programming, makes the process more approachable.
Learning Resources
Having access to the right learning resources can help overcome challenges when operating a CNC router. Many online platforms offer tutorials, video courses, and forums dedicated to CNC routers, such as YouTube channels, Udemy courses, or specific CAD/CAM software communities.
Manufacturer-provided manuals and training sessions are also invaluable for understanding the nuances of the machine and software. Additionally, using simulation tools within CAM software allows users to practice programming without the risk of damaging equipment or wasting materials, speeding up the learning process.
Support Networks
Building a support network helps maintain continuous improvement and complete troubleshooting. Joining online forums, local maker spaces, or CNC user groups provides a community where users can share experiences, ask questions, and receive advice. Mentorship from experienced operators can accelerate learning by offering practical insights and personalized guidance.
Many CNC router manufacturers also provide technical support and online communities, where professionals troubleshoot issues collaboratively. Having access to these networks ensures that users don’t have to face challenges alone and fosters continuous learning and innovation.
Overcoming the challenges of CNC router operation requires a combination of technical knowledge and continuous learning. With the right approach, both beginners and professionals can effectively overcome the challenges of CNC router operation and grow their skills over time.
Summarize
While learning to operate a CNC router may seem challenging at first, with the right mindset, resources, and practice, it becomes an achievable goal. Breaking the process into manageable steps makes the learning curve smoother. Access to online tutorials, practice projects, and support networks can further accelerate progress. Though it requires patience and dedication, mastering CNC router skills opens the door to endless creative and professional opportunities, making the learning journey well worth the effort. Continue reading “Use a CNC Router: Comprehensive Guide” and you will get more information on how to operate the machine properly.
As a well-known CNC router manufacturer in China, AccTek offers a wide models range of machines suitable for both beginners and professionals. We provide not only high-quality machines but also comprehensive support, including training resources and technical assistance to help users overcome the initial challenges of learning CNC. For anyone looking to invest in a CNC router, AccTek CNC delivers both the tools and the support to make the learning process smooth and rewarding.