- 10-14 Min Read
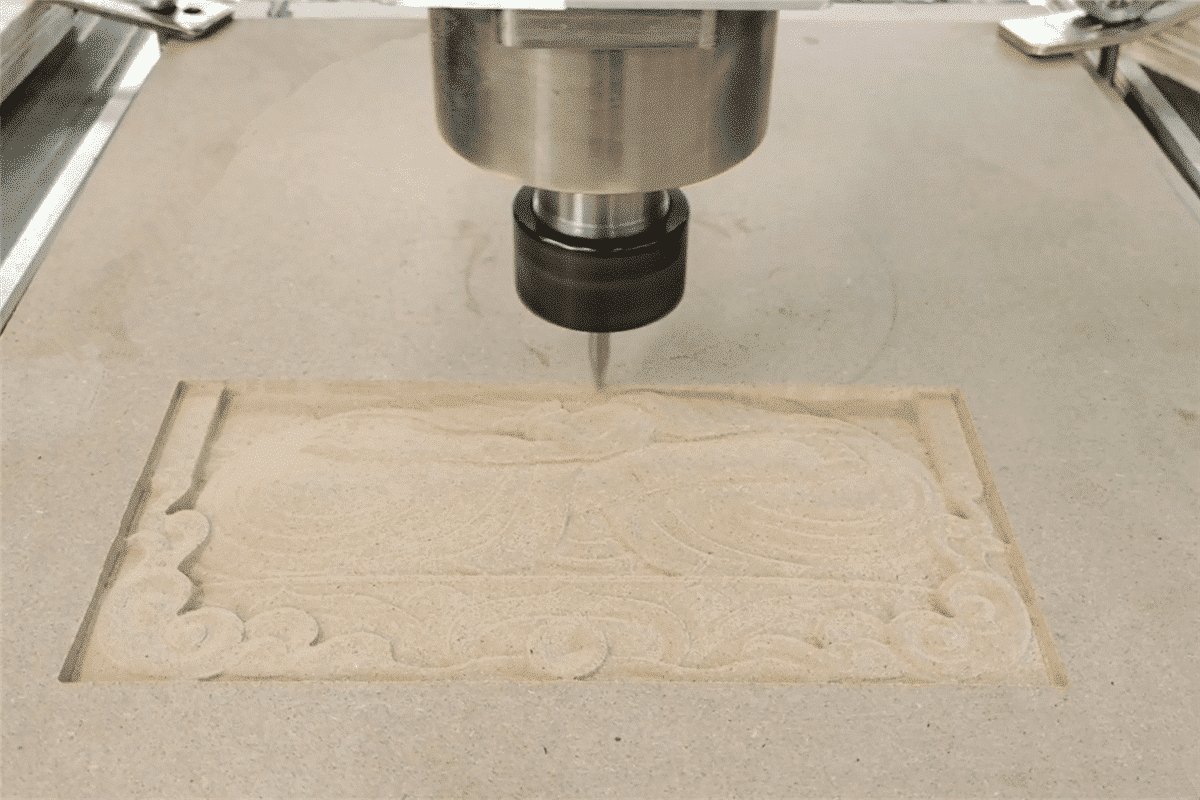
In the realm of precision manufacturing, CNC routers stand as indispensable tools, enabling the creation of intricate designs with unparalleled accuracy. However, achieving optimal results hinges not only on the machine’s inherent capabilities but also on the stability and performance of its tools. Tool deflection and vibration are common issues that can compromise the quality of the machined product, leading to inaccuracies, poor surface finish, and increased wear on both the tools and the machine. Understanding the causes of these issues and implementing effective strategies to mitigate them is beneficial for maintaining the integrity of the machining process.
In this article, we delve into the critical aspects of preventing CNC router tool deflection and vibration, exploring their detrimental effects on machining outcomes and how tool stability serves as the linchpin for achieving superior results. By understanding and addressing these factors, machinists can enhance the overall quality of their work, ensuring precise and reliable outcomes in every project. Whether you are a seasoned professional or new to CNC routing, this guide offers valuable insights to elevate your machining processes and achieve superior results.
Understanding CNC router tool deflection and vibration
Understanding tool deflection, identifying vibration, and ensuring tool stability are essential components of successful CNC machining. By exploring these areas, we aim to provide valuable insights and strategies to enhance machining accuracy and ensure high-quality results.
Defining Tool Deflection
Tool deflection refers to the deviation of the cutting tool from its intended path during the machining process. This deviation is caused by the forces exerted on the tool, which can be influenced by factors such as the tool’s material, geometry, length, and cutting parameters, including feed rate and spindle speed. When a tool deflects, it can lead to inaccuracies in the final product dimensions, uneven cuts, and poor surface finishes. Recognizing and understanding the causes of tool deflection is necessary for any machinist aiming to maintain precise and consistent machining operations.
Identifying Vibration in CNC Machining
Closely related to tool deflection, vibration is another critical issue that machinists must manage. Vibration, or chatter, can occur due to the dynamic interactions between the cutting tool, workpiece, and machine. It often results from imbalances, resonances, or improper setups. Vibration can be identified through signs such as visible surface waves on the machined part, audible noise during cutting, and increased tool wear. This phenomenon not only affects the accuracy and quality of the machined parts but can also lead to potential damage to the CNC router itself. Identifying the sources and manifestations of vibration is beneficiall for implementing effective damping techniques and maintaining smooth machining operations.
The Importance of Tool Stability
Tool stability is a critical factor in achieving high-quality machining results. Stable tools are less prone to deflection and vibration, ensuring that the cutting path remains accurate and the surface finish is smooth. Achieving tool stability involves selecting the appropriate tool material and geometry, optimizing cutting parameters, and ensuring a robust setup. Stable tools reduce wear and tear, enhance the longevity of the equipment, and minimize production costs associated with rework and scrap. Therefore, prioritizing tool stability is a priority for machinists aiming to produce precise, high-quality parts consistently.
Mastering the concepts of CNC router tool deflection and vibration is necessary for any machinist aiming to achieve superior machining quality. By addressing these aspects, machinists can overcome common challenges, enhance machining accuracy, and achieve superior results in their projects.
Factors affecting tool deflection and vibration
Tool deflection and vibration are critical issues in CNC machining that can significantly impact the precision and quality of the machined parts. Understanding the factors that contribute to these phenomena is beneficiall for developing strategies to mitigate their effects. This section explores the key factors affecting tool deflection and vibration.
Material Properties
- Hardness and Toughness: The hardness and toughness of the material being machined affect the cutting forces. Harder materials generate higher cutting forces, which can increase the likelihood of tool deflection and vibration. Tougher materials may also resist cutting forces differently, affecting stability.
- Material Inhomogeneity: Variations in the material properties of the workpiece, such as inclusions or varying hardness, can lead to uneven cutting forces and increased vibration.
Tool Geometry and Selection
- Tool Geometry: The shape and size of the cutting tool, including its length, diameter, and flute design, play a significant role. Longer and thinner tools are more susceptible to deflection, while shorter and thicker tools provide greater stability.
- Tool Selection: The rigidity and strength of the tool material influence its resistance to deflection. Tools made from harder materials like carbide are less prone to deflection compared to those made from high-speed steel (HSS). The rigidity of the tool material helps maintain accuracy under high cutting forces.
Cutting Conditions
- Feed Rate and Spindle Speed: High feed rates and spindle speeds can increase the forces exerted on the tool, leading to greater deflection and vibration.
- Depth of Cut: Taking too deep a cut can overload the tool, causing deflection. Multiple passes with shallower cuts can reduce the stress on the tool.
- Tool Path and Engagement: The tool path and how the tool engages with the workpiece affect stability. Sharp changes in direction and sudden tool engagements can induce vibration.
Tool Holder and Spindle Selection
- Tool Holder: High-quality, rigid tool holders ensure that the tool is held securely, reducing the chances of deflection. Precision tool holders minimize runout, which can otherwise lead to vibrations.
- Spindle: A well-maintained spindle that runs true is beneficiall for reducing vibrations. Any misalignment or wear can introduce imbalances and deflection. Using a spindle that can operate smoothly at the required speeds for the tool and material can help maintain stability.
By considering these factors across the four key aspects, machinists can effectively reduce tool deflection and vibration, leading to improved machining accuracy and superior quality of the machined parts.
Technology to prevent tool deflection and vibration
Preventing tool deflection and vibration in CNC machining involves employing various techniques across different aspects of the machining process. Here, we explore effective strategies from optimizing cutting parameters to utilizing advanced tool damping technology.
Optimizing Cutting Parameters
- Feed Rate and Spindle Speed: Adjusting feed rates and spindle speeds to optimal levels reduces the cutting forces that cause deflection and vibration. Lowering feed rates and spindle speeds can help stabilize the cutting process. Incrementally adjusting these parameters based on real-time feedback can prevent sudden increases in cutting forces.
- Depth of Cut: Using shallower depths of cut reduces the load on the tool, minimizing deflection. Multiple shallow passes can achieve the same material removal rate as a single deep cut but with greater stability.
- Spindle Speed: Set spindle speed appropriately based on the material and tool being used. Higher speeds can sometimes reduce deflection by reducing cutting forces.
Correct Tool Path Planning
- Smooth Tool Paths: Planning tool paths with gradual changes in direction minimizes sudden force changes that can cause vibration. Ensuring the tool engages with the workpiece consistently throughout the path helps maintain stable cutting conditions.
- Adaptive Tool Paths: Using CAM software to create adaptive tool paths that adjust in real time based on cutting conditions can prevent deflection and vibration.
- Trochoidal Milling: Implementing trochoidal milling techniques, where the tool moves in a circular pattern, reduces radial engagement and distributes cutting forces more evenly.
Tool and Tool Holder Balance
- High-Performance Tool Holders: Hydraulic and shrink-fit tool holders provide superior clamping force and concentricity compared to traditional collet chucks, reducing deflection and vibration. These tool holders offer minimal runout, ensuring that the tool remains stable during machining.
- Tool Balancing: Using pre-balanced tools, especially for high-speed applications, ensures that the tool remains stable during operation.
Reducing Overhang
- Tool Length Optimization: Minimize tool overhang from the holder to the cutting edge. Shorter tools are inherently more rigid and less prone to deflection.
- Properly Supported Tools: Ensuring that tools are properly supported by the tool holder and any necessary extensions can minimize deflection.
Tool Damping Technology
- Tuned Mass Dampers: Integrating tuned mass dampers into the tool holder or machine structure absorbs and dissipates vibrational energy, reducing the amplitude of vibrations.
- Damping Tool Holders: Using tool holders designed with damping materials or mechanisms can significantly reduce vibration during machining.
By integrating these techniques into CNC machining processes, manufacturers can effectively minimize tool deflection and vibration. This not only improves machining accuracy and surface finish but also enhances tool life and overall productivity. Continuous refinement and adaptation of these strategies based on specific machining challenges and advancements in technology will further optimize machining operations in the future.
Advanced technology for tool stability
Achieving tool stability in CNC machining helps maintain high precision and quality of manufactured parts. Advanced technologies have been developed to enhance tool stability, addressing issues related to tool deflection and vibration. Here are some cutting-edge technologies that contribute to improved tool stability:
Adaptive Machining
Adaptive machining is an advanced approach in CNC technology that dynamically adjusts the machining process in response to real-time conditions. This technique enhances tool stability and extends tool life by optimizing cutting parameters based on the current state of the tool and workpiece. Here are its key manifestations:
- Real-Time Feedback: Sensors and monitoring systems provide real-time data on tool wear, cutting forces, and material conditions.
- Automatic Adjustments: The CNC system adjusts feed rates, spindle speeds, and cutting depths to maintain optimal machining conditions.
- Predictive Analytics: Machine learning algorithms predict tool wear and potential failures, allowing for preemptive adjustments to prevent instability.
Vibration Reduction Systems
Vibration in CNC machining can lead to poor surface finishes, reduced tool life, and potential damage to the machine or workpiece. Vibration reduction systems are designed to minimize these adverse effects, ensuring a more stable and precise machining process. Here are its key manifestations:
- Damping Technologies: Implementation of passive or active damping systems to absorb and dissipate vibrational energy.
- Dynamic Balancing: Automatic balancing systems adjust the tool or spindle to counteract imbalances that cause vibrations.
- Stiffness Enhancement: Design improvements in tool holders, spindles, and machine structures to increase rigidity and reduce susceptibility to vibrations.
Tool Monitoring Systems
Tool monitoring systems are beneficiall for maintaining tool stability by continuously tracking the condition and performance of the cutting tools. These systems help in the early detection of tool wear, breakage, or other issues, enabling timely interventions. Here are its key manifestations:
- Sensor Integration: Use of various sensors (e.g., acoustic emission, force, temperature) to gather data on tool conditions.
- Data Analysis: Advanced software analyzes sensor data to assess tool wear, predict tool life, and identify any abnormalities.
- Alerts and Automation: Automated alerts and system responses to tool issues, such as reducing feed rates or stopping the machine to prevent damage.
By leveraging these advanced technologies, manufacturers can significantly enhance tool stability, reducing tool deflection and vibration. This leads to improved machining accuracy, better surface finishes, extended tool life, and increased overall productivity. As technology continues to evolve, further innovations in these areas will continue to push the boundaries of what is possible in CNC machining.
The influence of tool stability on machining quality
Tool stability is a crucial determinant of processing quality in CNC machining. It impacts various aspects of the manufacturing process, notably surface finish and dimensional accuracy, tool life and cost efficiency, and the scrap rate. Here’s an exploration of how tool stability affects machining quality:
Surface Finish and Dimensional Accuracy
- Smooth Surfaces: Stable tools reduce vibrations, which in turn minimizes the occurrence of chatter marks and surface irregularities. This results in a smoother, higher-quality surface finish.
- Finer Details: Stability ensures consistent engagement between the tool and the workpiece, promoting even material removal and a finer surface texture. It is particularly important in applications requiring high aesthetic or functional standards.
- Minimized Deflection: When tools are stable, deflection is minimized, allowing the tool to follow the programmed path precisely. This leads to parts that closely match their specified dimensions and tolerances.
- Accurate Cutting Forces: Stable tools maintain consistent cutting forces, which is beneficial for producing parts with precise dimensions and maintaining geometric accuracy throughout the machining process.
Tool Life and Cost Efficiency
- Wear Reduction: Stable tools experience less fluctuation in cutting forces, which reduces the stress and wear on the cutting edges. This leads to longer tool life and reduces the frequency of tool changes.
- Uniform Wear Patterns: Consistent tool stability results in uniform wear patterns on the tool, helping to maintain sharpness and cutting efficiency over a longer period.
- Reduced Tool Replacement Costs: Prolonged tool life translates to fewer tool replacements, directly reducing the costs associated with purchasing new tools.
- Decreased Downtime: With fewer tool changes and less need for maintenance due to premature wear, machine downtime is minimized, leading to more productive machining operations and better utilization of equipment.
Reducing Scrap Rate
- Fewer Reworks and Scraps: Tool stability ensures that each machined part meets quality standards, reducing the likelihood of defects that would necessitate rework or lead to scrapping. This results in cost savings and more efficient use of materials.
- Improved First-Pass Yield: The likelihood of achieving the desired quality on the first pass is increased with stable tools, reducing the need for corrective actions and the associated material waste.
Tool stability is fundamental to achieving high machining quality. Ensuring tool stability through advanced technologies and optimized machining practices can lead to smoother surface finishes, precise dimensional accuracy, extended tool life, enhanced cost efficiency, and reduced scrap rates. These improvements collectively contribute to more efficient, reliable, and cost-effective manufacturing processes, ultimately enhancing overall productivity and product quality.
Tool stability maintenance practices
We have learned the importance of maintaining tool stability in CNC machining to ensure high-quality production, extend tool life and maximize efficiency, so it is time to focus on tool stability maintenance. Effective maintenance practices can significantly reduce tool deflection and vibration, thereby improving machining results. Here are some key practices for maintaining tool stability:
Regular Machine Maintenance
- Routine Calibration: Periodically calibrate the CNC machine to ensure it operates within specified tolerances. Regular calibration helps maintain tool stability by ensuring accurate and precise movements.
- Alignment Checks: Conduct regular alignment checks for the spindle, tool holders, and other critical machine components. Misalignments can cause excessive vibrations and tool deflection, negatively impacting machining quality.
- Scheduled Lubrication: Follow a consistent lubrication schedule for all moving parts, including the spindle, linear guides, and ball screws. Proper lubrication reduces friction and wear, contributing to smoother operation and improved stability.
- Wear and Tear Monitoring: Regularly inspect machine components such as bearings, belts, and drive systems for signs of wear and tear. Early detection of worn components allows for timely replacements, preventing potential stability issues.
- Cleaning and Debris Removal: Keep the machine clean and free from debris. Accumulated dirt and chips can interfere with machine movements and cause inaccuracies.
Toolholder and Spindle Maintenance
- Regular Cleaning: Clean tool holders frequently to remove any debris, dust, or residues that could affect the tool’s grip and stability. A clean tool holder ensures a secure fit for the cutting tool, reducing runout and vibration.
- Proper Balancing: Ensure tool holders are balanced correctly. Imbalanced tool holders can introduce vibrations that compromise machining quality. Use balancing equipment if necessary.
- Secure Clamping: Verify that the tool is securely clamped in the holder. A strong and uniform clamping force minimizes movement and vibration during machining.
- Spindle Inspection: Inspect the spindle for any signs of wear or damage. Ensure the spindle bearings are in good condition and properly lubricated to prevent vibrations.
Maintaining tool stability requires a comprehensive approach that encompasses regular machine maintenance, toolholder and spindle maintenance. By implementing these practices, manufacturers can achieve improved machining quality, extended tool life, and increased cost efficiency. Regular maintenance ensures that the machining process remains stable and reliable, ultimately leading to higher productivity and better product quality.
Summarize
Preventing CNC router tool deflection or vibration is beneficiall for maintaining the precision and quality of machining operations. Tool stability plays a key role in achieving this, as even minor deflections or vibrations can significantly impact the final product’s dimensions and surface finish. Focusing on tool stability enhances machining accuracy, reduces waste, and extends the lifespan of both tools and machinery, leading to more efficient and cost-effective production processes. Through diligent attention to these factors, CNC operators can achieve superior machining outcomes and maintain a competitive edge in the industry.
If you are in search of a reliable and innovative CNC router manufacturer, look no further than AccTek CNC. Whether you are a small business or a large industrial operation, AccTek CNC has the expertise and products to meet your machining needs with precision and reliability. Choose AccTek CNC for a partner you can rely on to elevate your manufacturing capabilities and ensure the highest standards of quality and performance.