- 12-17 Min Read
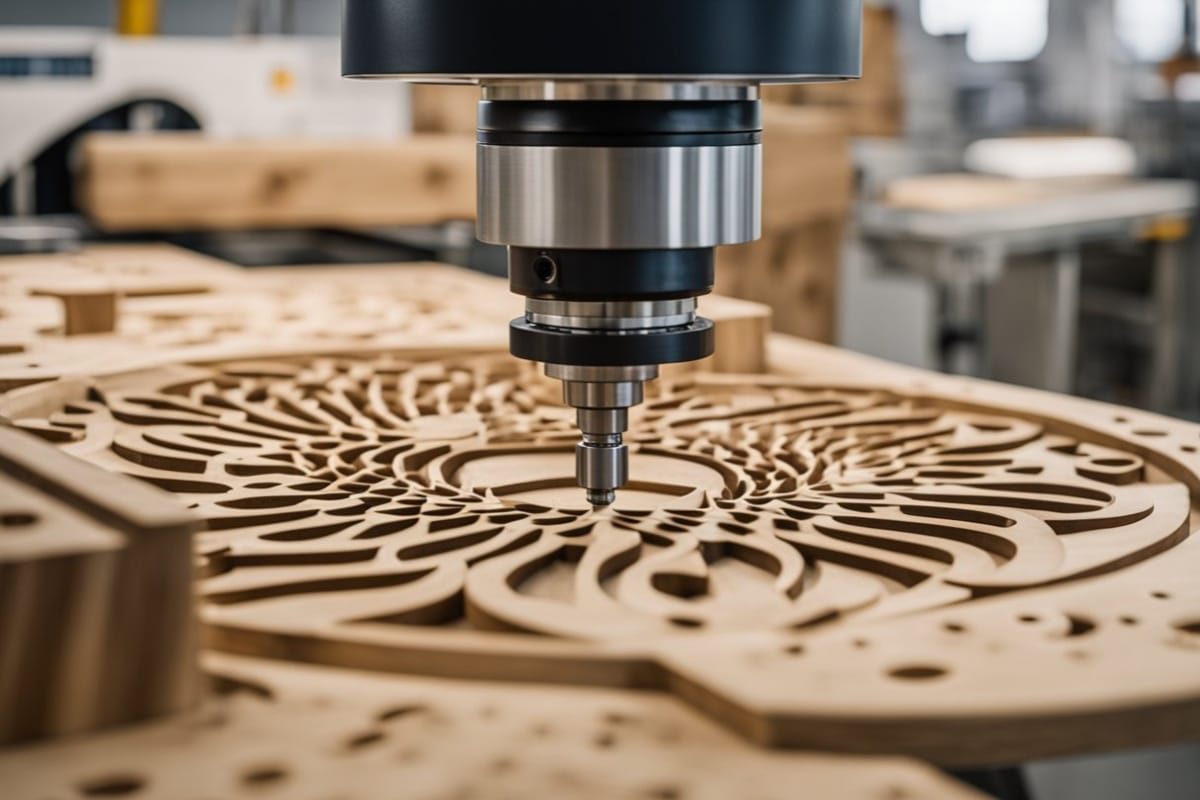
A CNC router is a powerful and precise machine used in various industries, from woodworking to metal fabrication. However, its performance and accuracy depend significantly on the proper installation of cutting tools. Loading a CNC router tool correctly ensures clean cuts, extends tool life, and prevents damage to the machine.
Improper tool loading can lead to misalignment, tool breakage, or even workpiece defects. Whether you are a beginner or an experienced operator, following the correct steps to load and secure your CNC router tool is beneficial for optimal performance. This guide will walk you through the step-by-step process, covering tool selection, collet installation, calibration, and testing to help you achieve precise and efficient CNC machining.
Understanding CNC Router Tools
CNC router tools are essential components that define the cutting, engraving, and shaping capabilities of a CNC router. These tools can be categorized into two key aspects: cutting tool types and tool holders and chucks.
Cutting Tool Types
CNC routers use a variety of cutting tools designed for different materials and machining tasks. The most common types include:
- End Mills: Versatile tools used for general cutting, profiling, and pocketing. Available in flat, ball nose, and tapered variations.
- V-Bits: Ideal for engraving, sign-making, and decorative cutting, providing sharp and clean edges.
- Compression Bits: Designed for cutting plywood and laminates, ensuring a clean finish on both the top and bottom surfaces.
- Upcut & Downcut Bits: Upcut bits pull chips upward for efficient material removal but may cause tear-out, while downcut bits push material downward for a cleaner top surface.
- Straight Bits: Used for simple cutting, slotting, and shaping operations in wood and soft materials.
- O-Flute Bits: Specifically designed for cutting plastics and acrylics, minimizing heat buildup and preventing melting.
- Drill Bits: Used for boring holes in materials, ensuring precise hole placement.
Each cutting tool is made from materials like carbide or high-speed steel (HSS), with coatings such as titanium nitride (TiN) or diamond coatings to enhance durability and cutting efficiency.
Tool Holders and Chucks
The tool holder and chuck system secure the cutting tool in the CNC router’s spindle, ensuring stability and accuracy during machining. The key components include:
- Collet Chucks: The most common tool-holding system in CNC routers, collets grip the tool shank firmly to reduce vibration and ensure precision.
- ER Collets: A widely used collet system that provides excellent tool-holding strength and accommodates various shank diameters.
- Hydraulic Tool Holders: These use hydraulic pressure to secure the tool, offering improved vibration dampening and accuracy.
- Shrink Fit Holders: Heat-expansion-based tool holders that provide a strong, balanced grip, ideal for high-speed cutting.
- Quick-Change Tool Holders: Designed for CNC routers with automatic tool changers(ATC), allowing fast and efficient tool swaps to improve productivity.
Proper selection and maintenance of tool holders and chucks are beneficial to ensure tool stability, reduce runout, and extend tool life. Regular inspection and cleaning help prevent tool slippage and ensure consistent machining performance.
By understanding both cutting tool types and tool-holding systems, CNC router operators can optimize their machining processes for better precision, efficiency, and tool longevity.
Tool Selection Considerations
Selecting the right tool for a CNC router is beneficial for achieving precise, efficient, and high-quality machining results. Two key factors to consider are material compatibility and machining operation, as they directly impact cutting performance and tool longevity.
Material Compatibility
Different materials require specific cutting tools to ensure clean cuts, minimal wear, and maximum efficiency. Choosing the wrong tool can lead to excessive heat, poor surface finish, or tool breakage. Below are common material categories and the recommended tool types:
- Wood Recommended Tools: Straight bits, upcut/downcut end mills, compression bits. Note the use of arbide tools for durability, and downcut bits for clean top surfaces.
- Plastics and Acrylics Recommended Tools: O-flute bits, single-flute end mills. Note the prevention of melting by using high-speed tools with effective chip evacuation.
- Metals Recommended Tools: Carbide end mills, coated tools (TiN, TiAlN). Note the use of sharp tools with coolant or lubrication to reduce heat buildup.
- Composites and Laminates Recommended Tools: Diamond-coated bits, compression bits. Note the use of tools designed for abrasive materials to prevent premature wear.
- Foam and Soft Materials Recommended Tools: Ball nose bits, straight bits. Note the use of sharp tools with minimal cutting force to prevent material distortion.
Machining Operation
The type of machining operation determines the tool shape, flute design, and cutting-edge geometry. Selecting the right tool based on the machining task ensures optimal performance.
- Profiling & Contouring: End mills and straight bits work well for general shaping. Note the use of appropriate flute direction based on material tear-out concerns.
- Pocketing & Engraving: V-bits and small-diameter end mills create intricate details. Note the use of V-bits for fine details and shallow-depth cuts.
- Drilling & Boring: Drill bits are specifically designed for hole-making. Note that ensure proper feed rate and peck drilling to prevent tool breakage.
- 3D Carving & Contouring: Ball nose end mills, tapered ball nose bits. Note the use of fine step-over settings for smooth finishes.
- Laminated & Veneered Materials: Compression bits prevent surface tear-out. These bits are cut in both directions to maintain clean edges on both sides
By considering both material compatibility and machining operation, CNC router operators can select the most suitable tool to enhance cutting precision, extend tool life, and optimize overall machining performance.
Tool Holding System
A tool holding system is a crucial component of CNC routers, ensuring that the cutting tool is securely mounted in the spindle for precision machining. This system consists of two key components: the chuck system and the tool holder. Both elements work together to provide stable and efficient tool operation during CNC machining.
Chuck System
The chuck system is responsible for gripping the tool shank and securing it in place within the spindle. The chuck type significantly affects tool stability, concentricity, and overall machining performance. Common chuck systems include:
- Collet Chucks: It is the most commonly used tool holding system in CNC routers, offering a firm and precise grip on tool shanks of various diameters. They use ER collets (e.g., ER16, ER20, ER25, ER32) to accommodate different tool sizes, ensuring high concentricity and minimal runout. Collet chucks are known for their versatility, cost-effectiveness, and ease of use, making them ideal for general machining applications.
- Hydraulic Chucks: They use hydraulic fluid pressure to clamp the tool shank evenly, providing superior vibration dampening and high precision. The uniform clamping force reduces tool runout and extends tool life, making these chucks ideal for high-speed and fine-detail machining. Hydraulic chucks are commonly used in delicate applications, such as precision milling and engraving, where minimal tool deflection is required.
- Shrink Fit Chucks: It rely on heat expansion to secure the tool shank tightly within the holder. The tool holder is heated using an induction heater, causing it to expand, and when the tool is inserted, it cools and contracts, creating a firm grip with exceptionally low runout. Shrink fit chucks require specialized heating equipment for tool changes.
- Pneumatic Chucks: They use compressed air pressure to clamp and release tools, making them highly efficient for automatic tool-changing (ATC) systems. Pneumatic chucks offer consistent clamping force, fast tool changes, and minimal setup time, improving machining productivity in industrial applications. Pneumatic chucks are widely used in high-speed production environments, such as automated woodworking and metal cutting, where rapid tool swaps are necessary.
Tool Holder
The tool holder connects the cutting tool to the chuck system and ultimately to the CNC router spindle. It ensures proper tool positioning, rigidity, and stability during machining. The selection of a tool holder impacts cutting performance, tool life, and machine efficiency.
- ER Collet Tool Holders: They are the most common tool holding system in CNC routers, work with ER collets to hold various tool shank sizes. ER collet tool holders provide high clamping force, good concentricity, and minimal runout, making them suitable for general machining applications.
- ISO and HSK Tool Holders: This is designed for industrial CNC routers with high-speed spindles, commonly found in automatic tool-changing (ATC) systems. ISO tool holders have a standard taper interface, while HSK tool holders feature a shorter, hollow taper that improves gripping force, stability, and accuracy. HSK holders excel in high-speed machining, providing superior balance and reduced vibration.
- BT and CAT Tool Holders: They are widely used in heavy-duty CNC machining centers, offering high rigidity and excellent balance for high-speed and high-torque applications. Both types provide strong tool grip, reduced vibration, and improved accuracy, making them ideal for heavy-duty cutting operations.
- Quick-Change Tool Holders: This is designed to speed up tool swaps, significantly reducing downtime in CNC machining operations. They are commonly used in automatic tool-changing (ATC) systems, allowing tools to be changed in seconds without manual intervention. These holders enhance machining efficiency, especially in high-volume production environments.
The tool holding system in a CNC router consists of the chuck system (which grips the tool) and the tool holder (which connects the tool to the spindle). Selecting the right combination ensures stable, precise, and efficient machining. Proper maintenance and the correct choice of tool holding components significantly impact machining accuracy, tool longevity, and overall CNC performance.
Tool Loading Procedure
Properly loading a tool into a CNC router is beneficial for achieving precision, efficiency, and safety during machining operations. The process involves four key steps: preparing the CNC milling machine, installing the tool holder, inserting the cutting tool, and fixing the tool.
Preparing the CNC Router
Before loading a tool, it is essential to ensure that the machine is properly prepared to prevent misalignment, tool slippage, or damage.
- Power Off and Safety Check: Turn off the machine and wear appropriate protective gear (gloves, safety glasses).
- Clean the Spindle and Tool Holder Area: Remove any dust, debris, or previous tool residue to ensure a secure fit.
- Verify Tool and Collet Compatibility: Check that the selected tool matches the spindle collet size and machining requirements.
- Check the Tool Loader (If Applicable): For automatic tool-changing (ATC) systems, ensure the tool magazine is operational.
Installing the Tool Holder
The tool holder secures the cutting tool and connects it to the CNC router’s spindle.
- Select the Correct Tool Holder Type: Choose between ER collet holders, BT/CAT tool holders, or HSK tool holders, depending on the machine configuration.
- Inspect and Clean the Tool Holder: Remove dust or chips to prevent tool misalignment.
- Insert the Tool Holder into the Spindle: Align the holder correctly with the spindle taper or collet system.
- Secure the Tool Holder: Use the appropriate tightening mechanism, such as a drawbar or retention knob, to fix it in place.
Inserting the Cutting Tool
Once the tool holder is installed, the cutting tool must be inserted securely.
- Choose the Right Cutting Tool: Select an appropriate tool based on the material, cutting operation, and machine settings.
- Insert the Tool into the Collet or Holder: Ensure the tool shank is positioned correctly inside the collet.
- Check Tool Projection Length: The tool should extend only as much as necessary to prevent excessive deflection or vibration.
Fixing the Tool
After inserting the cutting tool, it must be securely clamped to prevent movement during operation.
- Tighten the Collet Nut or Tool Clamping Mechanism: Use a wrench, hydraulic system, or shrink fit mechanism to lock the tool in place.
- Verify Tool Concentricity: Spin the spindle manually or use a dial indicator to check for runout.
- Set the Tool Length Offset: Measure and input the tool length into the CNC controller to ensure accurate cutting depth.
- Perform a Test Run (if applicable): Run a low-speed test to confirm proper installation before full-speed operation.
Following a structured tool loading procedure ensures that the CNC router operates safely and efficiently. By carefully preparing the machine, installing the tool holder, inserting the cutting tool, and securing it properly, machinists can achieve higher accuracy, extended tool life, and improved machining performance.
Considerations for Optimizing Tool Loading
Optimizing the tool loading process in CNC routers enhances machining accuracy, efficiency, and tool longevity. Three key factors to consider are tool change speed, tool calibration and measurement, and the tool presetting system. Implementing best practices in these areas helps reduce downtime, ensure precision, and enhance overall productivity.
Tool Change Speed
Minimizing tool change time is beneficial for maintaining high production efficiency, especially in automated or high-volume CNC machining.
- Use an Automatic Tool Changer (ATC): ATC systems allow for rapid tool swapping, reducing downtime between machining processes.
- Optimize Tool Magazine Arrangement: Arrange tools in the tool changer logically to minimize travel time and unnecessary tool swaps.
- Quick-Change Tool Holders: Implementing quick-change collets or tool holders speeds up manual tool changes, improving efficiency in small-batch production.
- Check and Maintain Tool Clamping Mechanisms: Ensure that collets, retention knobs, and pneumatic or hydraulic clamping systems are in good condition to prevent delays caused by tool-loading issues.
Tool Calibration and Measurement
Accurate tool calibration and measurement are beneficial for maintaining precision in machining operations. Improper tool length or offset settings can lead to dimensional errors, poor surface finishes, and tool breakage.
- Use a Tool Length Setter: A touch probe or tool setter measures tool length automatically, ensuring correct offset input.
- Manually Verify Tool Offset (If Necessary): Operators should double-check tool height manually using a gauge block or feeler gauge when automatic measurement is unavailable.
- Monitor Tool Wear: Regularly measure and check tool wear to prevent inaccuracies caused by tool degradation over time.
- Use Software-Based Tool Compensation: Many CNC controllers allow for automatic tool wear compensation, adjusting tool offsets dynamically based on usage.
Tool Presetting System
A tool presetting system is used to measure and set tool parameters before loading them into the CNC router machine, improving accuracy and reducing setup time.
- Offline Tool Presetting: Using an external tool presenter enables operators to measure tool length and diameter before inserting the tool into the machine, reducing machine downtime.
- Integrated Tool Presetting: Some CNC routers have built-in probe-based tool presetting systems that measure tools within the machine, ensuring real-time accuracy.
- Digital Tool Libraries: Storing tool data in a CNC database allows for faster tool selection and reduces the risk of errors during tool changes.
- Automated Tool Offset Adjustment: Some high-end CNC routers can automatically update tool offsets in the control system, ensuring precise machining without manual intervention.
Implementing ATC systems, tool setters, and presetting solutions leads to higher productivity and better machining results, making CNC router operations more streamlined and cost-effective.
Tool Maintenance and Inspection in CNC Routers
Regular checks and upkeep help prevent tool failure, reduce downtime, and maintain consistent cutting quality. To keep tools in optimal condition, maintenance should focus on the following four key aspects:
Regular Inspection
Routine inspection of CNC router tools helps identify wear, misalignment, and potential failures before they impact machining quality.
- Check for Tool Wear and Damage: Examine cutting edges for chipping, dullness, or deformation, which can affect cutting performance.
- Measure Tool Length and Diameter: Use a tool presetter to verify tool dimensions and prevent inaccuracies in machining.
- Inspect for Tool Runout: Excessive runout can lead to vibration and poor surface finishes. Checking with a dial indicator ensures precision.
- Monitor Tool Holder and Collet Condition: Look for cracks, corrosion, or deformation in tool holders, collets, and retention knobs to avoid tool slippage or instability.
- Follow a Scheduled Inspection Routine: Implement daily, weekly, and monthly checks based on tool usage to maintain reliability.
Tool Cleaning
Proper cleaning removes debris, extends tool life, and maintains cutting efficiency.
- Clean Tools After Each Use: Remove dust, metal shavings, and residue to prevent tool clogging and overheating.
- Use Proper Cleaning Methods: For deeper cleaning, compressed air blows away fine particles, while ultrasonic baths remove stubborn buildup.
- Lubricate Tool Holders and Retention Knobs: Apply a light coating of lubricant to prevent rust and ensure smooth tool changes.
- Keep Spindles and Collets Clean: Regularly clean the spindle interface and collets to maintain proper tool grip and reduce runout.
Tool Replacement
Replacing worn-out or damaged tools prevents machining errors and enhances production efficiency.
- Monitor Cutting Performance: If a tool starts producing rough cuts, excessive burrs, or requires more force, it’s time for a replacement.
- Follow Manufacturer’s Recommended Tool Life: CNC tool manufacturers provide estimated tool lifespans—adhering to these helps avoid tool failure.
- Replace Worn Collets and Tool Holders: Over time, collets lose grip strength, and worn tool holders can cause tool misalignment and chatter.
- Track Tool Usage with a Management System: Many CNC routers allow digital tracking of tool wear, alerting operators when a replacement is needed.
Proper Storage and Handling
Proper tool storage prevents damage and ensures quick accessibility.
- Store Tools in a Dry, Organized Environment: Use tool racks, foam-lined cases, or preset storage systems to prevent damage.
- Label and Categorize Tools: Organizing tools by size, type, and wear level improves efficiency in tool selection and setup.
- Avoid Dropping or Mishandling Tools: Even minor impacts can cause microscopic fractures, reducing tool integrity and performance.
By focusing on the above maintenance strategies, CNC router operators can maximize tool efficiency, reduce machining errors, and extend the lifespan of tools and tool holders. A proactive maintenance routine ensures consistent cutting quality, improved safety, and reduced downtime in CNC operations.
Troubleshooting Tips
Proper troubleshooting ensures smooth CNC operations by addressing tool-related issues before they affect machining quality. Below are key troubleshooting tips for common CNC router tool problems.
Tool Runout
Tool runout occurs when the cutting tool wobbles instead of rotating perfectly within the spindle, leading to inaccurate cuts and poor surface finishes. Here are techniques to fix it:
- Check and Clean the Tool Holder and Collet: Remove dust, chips, or debris that may be causing misalignment.
- Use a High-Precision Tool Holder: Switch to shrink-fit, hydraulic, or HSK tool holders for better concentricity.
- Inspect the Tool Shank and Collet Condition: Replace worn-out collets or damaged tool shanks that may be contributing to runout.
- Verify Proper Tool Installation: Ensure the tool is fully seated and correctly tightened in the collet.
- Measure Runout with a Dial Indicator: Identify and correct excessive runout before machining to ensure better accuracy.
Tool Chatter
Tool chatter refers to excessive vibration during cutting, resulting in poor surface finish, loud noise, and reduced tool life. Here are techniques to fix it:
- Reduce Spindle Speed and Adjust Feed Rate: Slowing down the spindle or increasing the feed rate can help reduce vibration.
- Use a More Rigid Tool Holder: Opt for shorter tool holders or hydraulic tool clamping systems to minimize tool flexing.
- Check Tool Overhang: Reduce tool overhang by minimizing the projection length of the tool from the collet.
- Use a Tool with a Different Helix Angle: A variable-helix tool helps distribute cutting forces more evenly, reducing vibration.
- Improve Machine Rigidity: Ensure the CNC routerbed is properly leveled and check for loose components in the spindle assembly.
Tool Breakage
Tool breakage occurs when the cutting tool snaps due to excessive force, improper feed rate, or incorrect tool selection. Here are techniques to fix it:
- Check and Adjust Cutting Parameters: Reduce the depth of cut, feed rate, or spindle speed to decrease stress on the tool.
- Use the Correct Tool Type: Choose a tool with the appropriate flute count, coating, and material (carbide for metals, high-speed steel for wood and plastics).
- Ensure Proper Chip Evacuation: Use upcut tools or compressed air to clear chips and prevent recutting, which can overload the tool.
- Inspect for Tool Overhang Issues: Keep tool overhang to a minimum to prevent excessive leverage forces that lead to breakage.
- Monitor Tool Wear and Replace When Necessary: Regularly check tools for dull edges or chipping, replacing them before failure occurs.
By applying these troubleshooting techniques, CNC operators can effectively reduce tool runout, minimize chatter, and prevent tool breakage, ensuring higher machining accuracy, better surface finishes, and longer tool life. Regular maintenance, proper tool selection, and optimized cutting parameters are key to avoiding these common CNC router tool issues.
Summarize
Loading CNC router tools correctly is a fundamental skill that directly impacts machining accuracy, efficiency, and tool longevity. By following a structured approach, operators can ensure optimal performance and reduce the risk of errors or equipment damage. Whether you’re working with a manual tool-changing setup or an advanced automatic tool changer (ATC), consistent best practices will lead to smoother operations, reduced downtime, and extended tool life. As CNC technology continues to evolve, mastering these essential procedures will help operators achieve long-term success in machining.
When it comes to precision, efficiency, and reliability in CNC machining, AccTek CNC stands out as a professional CNC router manufacturer offering high-quality solutions tailored to various industries. Our machines feature high-precision tool holders, powerful spindles, and intuitive control systems, making tool setup quick, accurate, and hassle-free. Committed to quality workmanship, innovative technology and exceptional customer support, AccTek CNC is the preferred choice for professionals looking to optimize their CNC operations.