- 10-14 Min Read
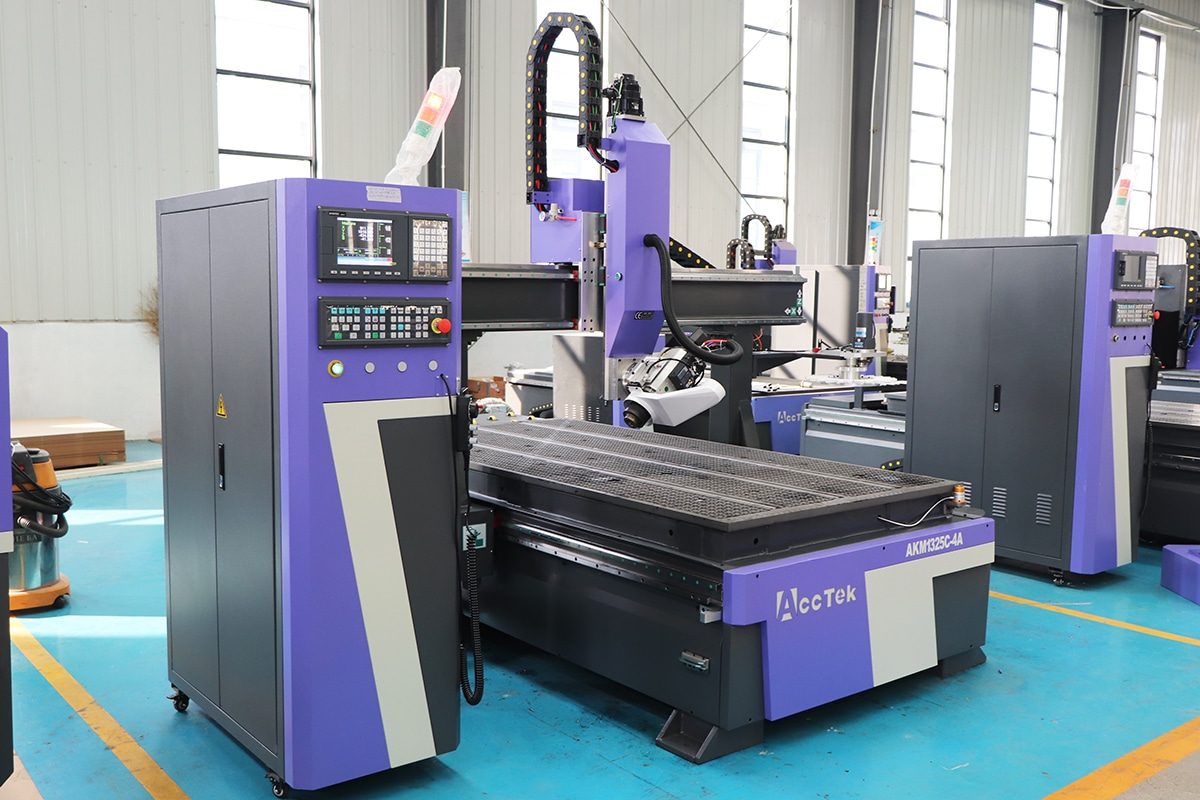
CNC routers are widely used tools in modern manufacturing, offering precision and automation for cutting, engraving, and milling various materials. Increasing CNC router speed can significantly enhance productivity, reduce machining time, and lower operational costs. However, simply pushing the machine to run faster can lead to tool wear, poor surface finish, or even mechanical failures. The key lies in understanding the factors that affect speed and applying the right strategies to boost performance safely and effectively.
This article explores the essential techniques to increase CNC router speed, from adjusting cutting parameters to upgrading components and implementing smarter machining strategies. Whether you are working with wood, plastic, or metal, these insights will help you maximize efficiency while maintaining precision and machine longevity.
Understanding CNC Router Speed
CNC router speed is a critical factor that directly impacts machining efficiency, quality, and tool longevity. Achieving the right balance between speed and precision ensures smoother operations, reduced cycle times, and longer tool life. Here, we will fully understand CNC router speed.
The Importance of Speed in CNC Machining
Speed is a critical aspect of CNC routing that affects multiple areas of production, including:
- Enhanced Productivity: Faster machining speeds lead to shorter production cycles, allowing manufacturers to complete more tasks in less time.
- Reduced Operational Costs: Optimizing speed minimizes machine runtime, reducing electricity consumption and labor costs. Efficient speed settings also lower tool wear, saving on replacement costs.
- Higher Profitability: Faster processing without compromising quality allows businesses to handle more orders, increasing revenue potential while maintaining competitive pricing.
Factors Affecting CNC Router Speed
Several factors influence how fast a CNC router can operate effectively. Key considerations include:
- Spindle Speed (RPM): The rate at which the cutting tool rotates affects cutting efficiency. Higher spindle speeds work well for softer materials, while harder materials require lower speeds to prevent tool wear and overheating.
- Feed Rate (IPM or mm/min): This determines how quickly the tool moves across the material. The right feed rate depends on the material type, tool sharpness, and spindle speed.
- Cutting Depth and Step-Over: Deeper cuts and larger step-overs remove more material per pass but require more power and rigidity. Optimizing these settings ensures a balance between speed and quality.
- Machine Rigidity and Stability: A sturdy CNC router with high-quality linear guides and a stable frame can sustain higher speeds without excessive vibration, ensuring precise cutting.
- Tool Selection: The type, material, and sharpness of the cutting tool impact speed. Using carbide or coated tools can enable higher-speed operations while maintaining durability.
- Software and Control System: Advanced CNC control systems with optimized acceleration, deceleration, and toolpath strategies can significantly enhance cutting speed while maintaining accuracy.
- Cooling and Lubrication: Proper cooling systems prevent tool overheating, allowing for continuous high-speed machining without compromising tool life.
By understanding these two aspects, CNC router operators can make informed decisions to maximize speed while maintaining precision and machine longevity.
Workpiece and Material Considerations
Optimizing CNC router speed requires careful attention to the workpiece material and its preparation. The material type, how it is prepared, and the tools used all significantly influence cutting efficiency. To maximize speed while maintaining quality, consider the following three key aspects:
Material Selection for Processing Speed
The type of material being machined directly affects the achievable speed and cutting performance. Some materials allow for faster machining, while others require lower speeds to maintain precision and prevent tool damage. Choosing the right material for the required speed can significantly enhance machining efficiency.
- High-Speed Materials: Softwoods, plastics, and foams can handle higher spindle speeds (18,000-24,000 RPM) and feed rates because they generate minimal cutting resistance.
- Moderate-Speed Materials: Aluminum, acrylics, and MDF require moderate spindle speeds (10,000-18,000 RPM) to balance speed and surface finish while minimizing melting or tearing.
- Low-Speed Materials: Hardwoods, composites, and metals such as stainless steel and brass require slower speeds (6,000-15,000 RPM) to prevent overheating, excessive tool wear, and surface defects.
Stock Material Preparation Technology
Proper preparation of the workpiece before machining ensures smoother operations, reduces tool strain, and allows for faster cutting speeds. Key preparation techniques include:
- Surface Flattening: Ensuring the material is even and properly aligned reduces tool stress and prevents irregular cuts. For wood and MDF, pre-surfacing the material enhances cutting efficiency.
- Material Stabilization: Materials with internal stresses (such as metal sheets or plywood) should be stabilized to prevent warping or shifting at high speeds. Drying wood properly prevents moisture-related issues that could affect cutting precision.
- Proper Workholding: A secure workholding method, such as vacuum tables, clamps, or jigs, ensures the material remains stable at higher speeds, reducing the risk of vibration-induced defects.
Tool Optimization for Material Compatibility
Selecting the right cutting tools and optimizing their performance is beneficial for increasing CNC router speed while maintaining quality. Considerations include:
- Tool Material: Carbide and coated tools withstand higher speeds and last longer than standard high-speed steel (HSS) tools. Diamond-coated tools are ideal for cutting abrasive materials like composites and laminates at higher speeds.
- Flute Count and Geometry: Fewer flutes (1-2) allow for higher chip evacuation, making them ideal for plastics, wood, and aluminum at high speeds. More flutes (3-5) provide a better surface finish but require slower speeds, suitable for metals and harder materials.
By carefully selecting the right materials, ensuring proper workpiece preparation, and using optimized tools, CNC router operators can significantly increase machining speed while maintaining precision and tool longevity. The next sections will explore practical techniques to increase CNC router speed efficiently.
Optimization Techniques for Increasing CNC Router Speed
To maximize CNC router speed without compromising accuracy, it is necessary to optimize tool paths, fine-tune feeds and speeds, and optimize software. These aspects work together to ensure efficient material removal while maintaining tool longevity and surface quality.
Optimizing Tool Paths
An efficient tool path reduces unnecessary movements, minimizes cutting resistance, and improves overall machining efficiency. Below are key strategies to optimize tool paths:
- Adjusting Cutting Strategies: Implementing advanced toolpath strategies, such as adaptive clearing and trochoidal milling, can significantly enhance machining speed. These strategies ensure a consistent chip load by dynamically adjusting tool engagement, allowing for higher feed rates and deeper cuts without excessive tool wear. High-speed machining (HSM) toolpaths, which prioritize smooth, continuous movements rather than abrupt direction changes, also help maintain momentum, reducing cycle times and preventing unnecessary machine slowdowns.
- Minimize Tool Retract and Radial Advance: To optimize toolpaths, ensure the tool remains engaged with the material as much as possible, reducing air cutting and unnecessary rapid positioning movements. Using ramped or helical entries instead of direct plunges minimizes stress on the tool and material while maintaining a continuous cutting motion. Additionally, optimizing lead-in and lead-out moves prevents abrupt deceleration, keeping the machine operating at peak efficiency.
- Implement Toolpaths Based on Chip Load: The toolpath should maintain consistent tool engagement, preventing sudden load increases that can slow down the cutting process. Using constant cutter engagement strategies like equal step-over in pocketing or constant tool engagement angles in contouring ensures steady chip formation, allowing for faster feed rates without compromising tool life or surface finish.
- Simplify Geometry and Reduce Complexity: Simplifying part geometry by reducing unnecessary details, smoothing sharp corners into arcs, and using larger radii where possible helps the CNC routermaintain higher speeds. Additionally, eliminating redundant tool motions and using efficient nesting techniques for batch production can further reduce machining time while maintaining precision and material utilization.
Fine-Tuning Feeds and Speeds
Setting the correct feed rate and spindle speed ensures smooth material removal while preventing tool wear and overheating.
- Dynamic Feed Speed Control: Instead of using a constant feed rate, the CNC router automatically slows down in high-resistance areas (such as tight corners and deep pockets) and accelerates in straight, open-cutting paths. This technique prevents excessive tool load, minimizes vibrations, and ensures consistent chip removal, allowing for faster speeds without compromising precision.
- Speed Adjustment for Specific Materials: Soft materials like wood, plastics, and foam can withstand higher spindle speeds (18,000–24,000 RPM) and faster feed rates, while harder materials like aluminum, steel, and composites need lower spindle speeds (6,000–15,000 RPM) and carefully controlled feed rates to prevent tool overheating and excessive wear.
- Adaptive Feed Speed Control Algorithm: Modern CNC controllers and CAM software use adaptive feed speed control algorithms that dynamically adjust cutting speeds based on real-time monitoring of tool load, material resistance, and spindle torque. These algorithms slow down the feed rate when encountering denser material sections or sudden tool engagement and speed it up when cutting in low-resistance areas.
- Using Feed and Speed Calculators and Software: Feed and speed calculators help CNC router operators determine optimal cutting parameters by considering tool type, material hardness, chip load, and machine capabilities. This eliminates guesswork and ensures that feed rate, spindle speed, and depth of cut are precisely tuned for maximum efficiency and tool life.
Software Optimization
Optimizing CNC router speed is not limited to hardware improvements, advanced CNC software can also have a significant impact on speed and performance.
- CAM Software Efficiency: CAM software significantly influences CNC router speed by generating optimized toolpaths, minimizing unnecessary movements, and improving cutting strategies. Meanwhile, post-processor customization tailors the CAM-generated G-code to the specific CNC machine’s capabilities, optimizing motion commands, acceleration settings, and machine-specific cycles.
- CNC Controller Software: Advanced controllers support real-time acceleration and deceleration adjustments, look-ahead processing, and adaptive feed rate control to ensure continuous and efficient cutting. By fine-tuning acceleration settings, spindle speed ramping, and motion smoothing algorithms, CNC routers can achieve higher speeds without sudden stops or unnecessary slowdowns.
- Simulation and Virtual Machining: Virtual machining software allows operators to detect tool collisions, inefficient toolpaths, and excessive non-cutting movements, which can be adjusted before execution. By using real-time machine kinematics and physics-based simulations, manufacturers can test different speeds and feed settings, ensuring that the CNC router runs at maximum efficiency without compromising accuracy or safety.
By implementing these optimization techniques, CNC router operators can significantly increase speed while maintaining quality, extending tool life, and reducing overall machining time. In the next section we will explore some upgrades and maintenance practices that can be used to increase the speed of your CNC router.
Upgrades and Maintenance for Higher Speed
To maximize the speed of your CNC router, hardware upgrades and routine maintenance are further practices to be performed. Investing in the right upgrades enhances performance, while regular maintenance prevents slowdowns caused by wear and tear. Below are key aspects to consider.
Upgrade equipment and components
- Upgrading Motors and Drives: The motion system significantly impacts cutting speed. Upgrading from stepper motors to servo motors provides higher acceleration, better torque control, and improved positioning accuracy, allowing the machine to run at higher feed rates without losing precision. Additionally, switching to high-performance drives and controllers ensures smoother, faster movements with minimal vibrations.
- Enhancing Linear Motion Components: High-speed operation requires a rigid, low-friction movement system. Upgrading to precision linear guides and ball screws or rack-and-pinion systems can improve speed while maintaining stability. Lubricated, wear-resistant rails reduce friction and allow for smoother, more consistent tool movement, ultimately increasing machining speed without sacrificing accuracy.
- Optimizing Spindle Performance: A higher-power spindle motor enables faster cutting speeds, especially for dense materials like metals and composites. Upgrading to a variable-frequency drive (VFD) controlled spindle allows for more precise speed adjustments, optimizing performance based on material type and cutting conditions.
- Lightweight and Sturdy Frame: A rigid yet lightweight CNC router frame enhances speed by reducing vibrations and supporting faster acceleration and deceleration. Frames made from aluminum extrusions or reinforced steel structures provide the necessary stability while keeping weight manageable.
- Efficient Cooling and Chip Removal System: Options such as mist cooling, air blowers, or liquid cooling systems help maintain optimal temperatures, extending tool life. Additionally, a strong chip removal system, including dust extractors or vacuum systems, ensures that debris does not obstruct cutting paths, enabling uninterrupted high-speed machining.
Advanced Processing Technology
- High-Speed Cutting Strategy: These strategies minimize cutting forces by ensuring a consistent chip load, which enables higher feed rates without excessive tool deflection. Additionally, using optimized toolpaths with smooth transitions prevents abrupt speed changes, enhancing overall machining efficiency.
- High-Speed Drilling and Hole Processing: High-speed drilling techniques, such as rigid tapping and through-spindle coolant, help maintain accuracy and prevent heat buildup in deep-hole drilling applications. Advanced CNC controllers allow for rapid positioning and synchronized feed rates, ensuring faster and more precise hole drilling in materials like wood, plastics, and metals.
- High-Speed Engraving and Surface Finishing: For detailed engraving and fine surface finishing, high-speed machining (HSM) techniques, such as raster engraving and constant velocity motion, enable rapid processing while maintaining intricate details. Using high-RPM spindles and fine-tip cutting tools improves engraving resolution and minimizes tool marks.
- Multi-Tasking and Simultaneous Processing Operations: Modern CNC routers equipped with multi-axis capabilities (double-head and 3-spindle machining) enable simultaneous cutting, drilling, and engraving operations. Multi-tasking functionality allows the CNC router to perform multiple tool movements simultaneously, reducing idle time and increasing productivity.
Maintenance and Optimization
- Regular Machine Maintenance: This includes lubricating linear guides, ball screws, and bearings to reduce friction and prevent premature wear. Cleaning dust, chips, and debris from the work area and machine components ensures smooth operation and prevents overheating. Additionally, checking for loose bolts, electrical connections, and worn-out cables helps maintain machine stability, reducing unexpected slowdowns or breakdowns.
- Calibration and Alignment Inspection: Regular calibration of the spindle, tool holder, and motion system ensures proper positioning and minimizes cutting errors. Inspecting gantry squareness, table flatness, and tool offsets helps maintain precision at high speeds.
- Tooling Maintenance and Replacement: Regular inspection and replacement of cutting tools, collets, and tool holders ensures sharp edges and proper tool engagement. Using high-quality carbide or coated tools extends tool life and allows for higher feed rates.
- Performance Monitoring and Data Analysis: Analyzing feed rates, spindle loads, and tool wear trends allows operators to make data-driven adjustments for better performance. CNC software with diagnostic tools and predictive maintenance features can detect potential issues before they cause downtime, ensuring consistent high-speed operation.
By integrating hardware upgrades, advanced machining techniques, and diligent maintenance routines, CNC router operators can achieve higher processing speeds, improved precision, and longer machine lifespan, ultimately increasing productivity and reducing operational costs.
Training and Skills Development
Enhancing CNC router speed is not solely dependent on hardware and software upgrades, it also requires operator expertise and continuous skills development. Proper training ensures that operators can fully leverage the machine’s capabilities, optimize toolpaths, and troubleshoot issues efficiently. Below are key areas of training and skills development that contribute to faster and more precise CNC routing.
- Operator Efficiency Training: Well-trained operators can set up, adjust, and operate the CNC router more efficiently, reducing setup time and machining errors. Training should focus on machine operation fundamentals, tool changes, material handling, and troubleshooting to ensure smooth workflow and minimal downtime. Operators should also learn to interpret machining errors and adjust feed rates, spindle speeds, and cutting depths accordingly to maintain optimal speed without tool breakage or surface defects.
- Programming Skills Improvement: Advanced CNC programming and CAM software training allow operators to create optimized toolpaths that enhance cutting speed and efficiency. Understanding G-code modifications, adaptive toolpath strategies, and high-speed machining techniques (such as trochoidal milling and climb milling) help operators reduce cycle times and improve machining accuracy. Additionally, learning how to use simulation tools ensures that programs are fully optimized before running on the machine, preventing unnecessary slowdowns.
- Continuous Learning and Industry Updates: CNC technology is constantly evolving, and operators need to stay updated with the latest advancements in software, hardware, and machining techniques. Regular participation in industry workshops, online courses, and manufacturer training programs keeps operators informed about new high-speed machining strategies, updated control system features, and automation enhancements. Staying ahead of industry trends enables businesses to implement the latest best practices for faster and more efficient CNC routing.
By investing in operator training and skills development, CNC router users can maximize speed, improve machining efficiency, and reduce errors, leading to higher productivity and better overall machine performance.
Summarize
Increasing CNC router speed requires a balanced approach integrating hardware upgrades, software optimizations, advanced machining strategies, and skilled operation. Simply pushing the machine to run faster can lead to tool wear, poor surface finish, and mechanical failures. Instead, operators can achieve higher efficiency by carefully optimizing toolpaths, feed rates, and spindle speeds without compromising accuracy or machine longevity.
If you’re looking to increase CNC router speed, improve productivity, and maintain top-notch machining quality, AccTek CNC is the ideal partner. With a strong commitment to performance, reliability, and innovation, AccTek CNC provides high-speed, high-precision CNC routers designed to enhance productivity in various industries. Our high-performance machines, intelligent software, and expert support provide a complete solution for high-speed CNC routing, making them a trusted choice for businesses looking to boost efficiency and stay competitive in the industry.